The timber industry has set out its plan to meet the 2050 net zero challenge, with transport and more local sourcing a key focus, writes Charlie Law.
The timber industry has long advocated the use of timber to reduce the embodied carbon impact of construction. However, until now, there was very little information available to show the wider impacts of the timber supply chain.
Timber Development UK (TDUK), in collaboration with other key UK timber trade associations and other like-minded organisations, has launched the Timber Industry Net Zero Roadmap. This sets out the emissions within the timber supply chain and proposes steps the industry could take to reduce these, and what the journey to net zero by 2050 could look like.
The timber-related industries in the UK are responsible for 1,575,356 tonnes CO2e territorial emissions, which equates to 0.35% of UK emissions. This is very low compared to other UK manufacturing industries such as steel (12 million tonnes, 2.7% of UK emissions) and concrete (7.3 million tonnes, 1.5% of UK emissions).
Timber is also responsible for 3,655,715 tonnes CO2e of imported embodied emissions from the processing and transportation of wood products overseas.
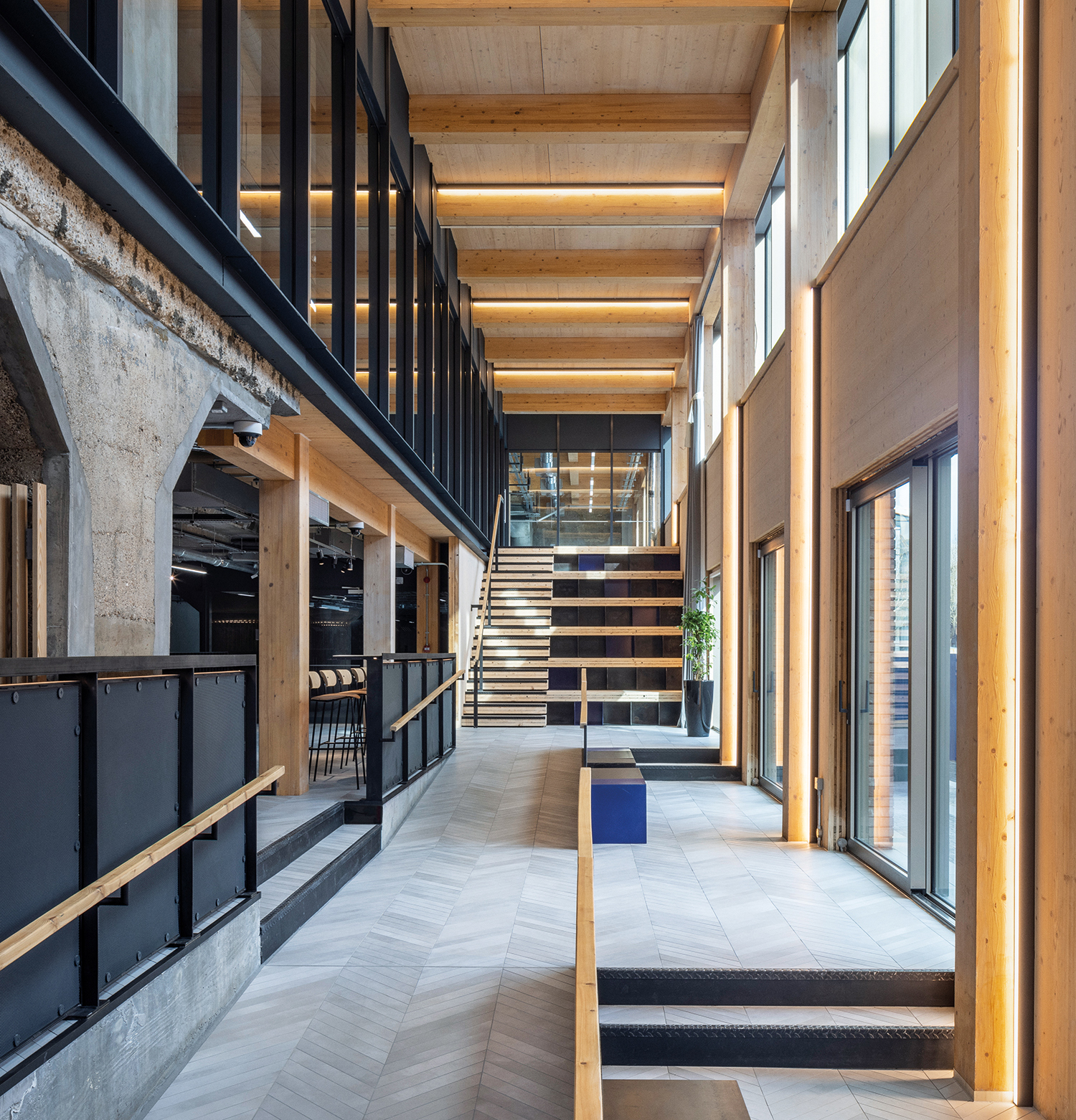
All figures in the roadmap exclude sequestered (stored) carbon within the timber product, as the document is focused on reducing the industrial emissions from timber processing and transportation. In fact, the amount of carbon absorbed and stored by timber products is greater than that emitted via industrial processes.
Reducing embodied emissions
Specifying timber in place of steel or concrete wherever practicable will therefore reduce the whole-life embodied carbon emissions of construction, and store CO2 out of the atmosphere for the life of the asset (and longer if the timber products are reused or recycled).
One example of this is The Gramophone Works in west London, the former headquarters of Sanderson Fabrics and subsequently Saga Records, which is now a commercial office scheme comprising a mix of refurbished and extended office space.
The scheme reuses the existing structure to reduce the embodied carbon, and by using glulam and cross-laminated timber (CLT) for the extended areas, the embodied carbon within the building was reduced even further, with upfront emissions kept to 1,259 tonnes CO2e, with 1,292 tonnes CO2 being stored in the timber elements for the life of the project.
With almost half of all emissions being from the transportation of timber products, this will need to be a key area of focus for reduction. Efficiencies in the use of transport and the vehicles themselves (aerodynamics) can significantly reduce emissions now, and zero-emissions trucks are likely to be widely adopted by the end of the decade.
However, construction professionals can help reduce transport miles by specifying more ‘locally sourced’ timber – for example UK-produced OSB and particleboard, or spruce plywood from Scandinavia, rather than plywood produced in the Far East or South America. In many cases this will also reduce the embodied production emissions – the second biggest source of emissions – as UK and European manufacturing is decarbonising faster than some other parts of the world.
Sources of industry emissions
Of the remaining emissions, UK production facilities, including sawmills and panel mills, are the largest source. This will require action from the UK government to ensure the electricity grid decarbonises sufficiently by 2050, as well as action from the UK timber industry.
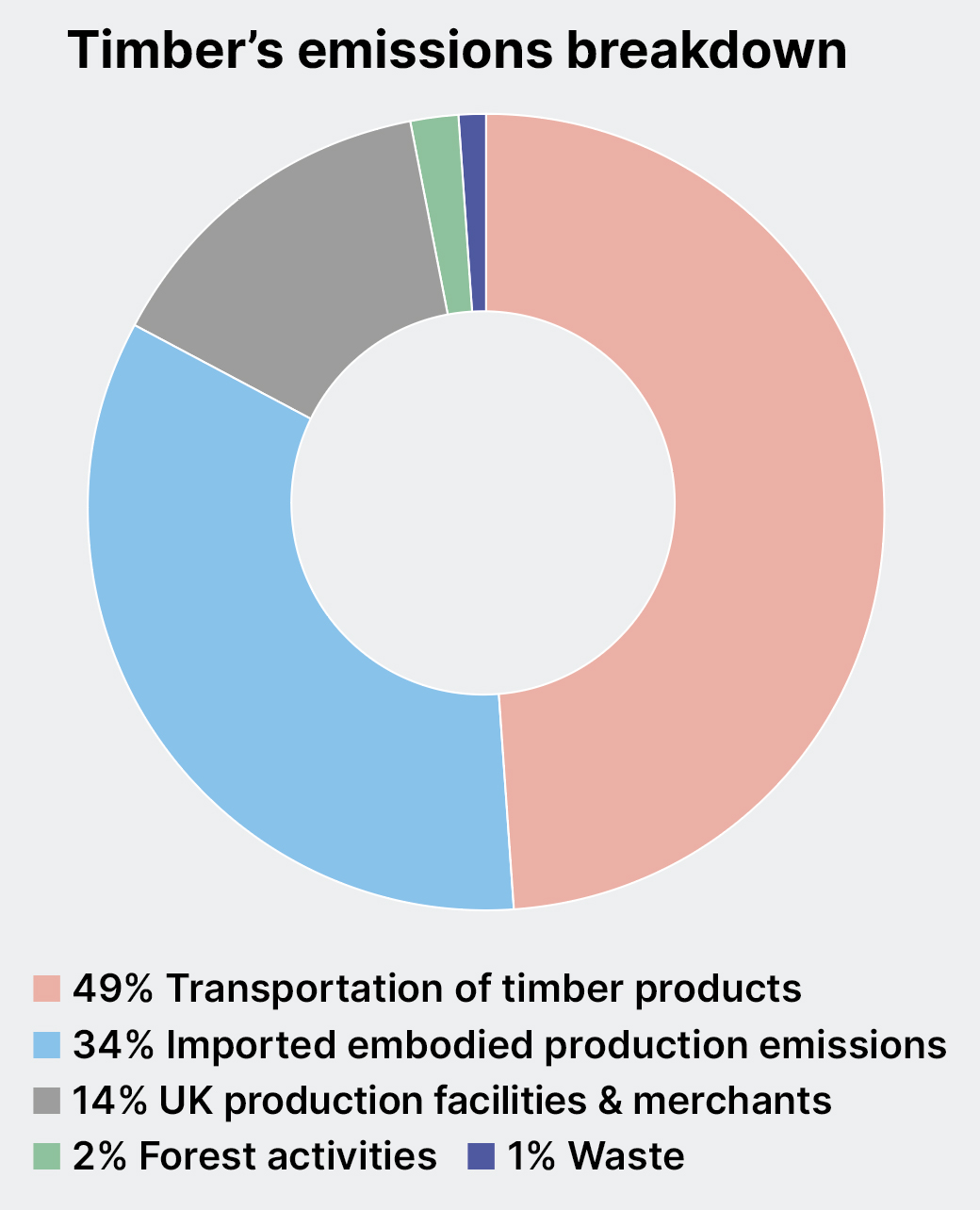
The key use of energy in production is heat, to dry out timber products for use. Where natural gas is currently used, the use of waste timber to produce energy via combined heat and power (CHP) plant is the most cost-effective and carbon-efficient option in the short term.
Emissions from forestry processes, such as felling and forwarding to the roadside, are relatively low-carbon activities, with hybrid plant already being used to reduce emissions further. This process will require new technology, in the form of green hydrogen-fuelled plant, to fully decarbonise over the long term.
Processing waste is the last key emission source. Seventy percent of emissions from waste are from the transport and initial processing of waste from construction sites, so the key action here is for the wider construction industry to reduce waste production, through offsite prefabrication where possible, and good material management on site.
By working together, the timber industry, along with the wider construction sector, can help reduce embodied carbon within the built environment, and in doing so help meet the UK government’s net
zero by 2050 targets.
Charlie Law is sustainability director at Timber Development UK.