
There’s a global trend for more high-rise timber buildings but why are we not seeing a similar story in the UK, asks David Hopkins.
As sustainable construction moves high on the priority list globally, timber as a material has also grown in popularity, and in height. We see taller and taller timber buildings being constructed around the world using engineered timber, with the new record now standing at 86m, for a 25-storey tower in Milwaukee, USA, called Ascent.
This surge in record-breaking high-rise projects around the world is largely driven by two factors: the maturing of engineered timber technology and the drive to decarbonise the built environment.
Engineered timbers have had their properties modified to give the timber added strength, allowing them to be used in place of more energy-intensive materials like steel. These products can then be engineered to precise performance specifications, and often will be cut to measure offsite before being transported and erected at great speed.
Some engineered woods, such as cross-laminated timber (CLT), are pound-for-pound stronger than steel, with the same carbon-saving advantages as standard timber. This has opened the door for ambitious timber projects like those seen internationally.
Risk-averse UK
Given the progress made elsewhere and the obvious environmental benefits, why are we not seeing high-rise timber buildings appearing in the UK?
At present, we have a unique set of circumstances driven by a focus on building safety following the Grenfell tragedy and tough economic conditions driven partly by austerity, Brexit and other global factors.
Structural timber became a victim of these circumstances and was caught up in a blanket ban on combustible material allowed for buildings over 18m in height, before the government admitted a more nuanced approach was needed and allowed it for use provided appropriate fire tests are met. However, a ban still remains for residential buildings above 18m.
The uncertainty this situation caused has created confusion among many – and made investors even more risk-averse. Meanwhile, the development of more ambitious taller timber buildings has stalled.
Perhaps the biggest hurdle in the UK to overcome is education. Understanding of timber – how to build with it, its properties and how it relates to existing building regulations – is a real problem at all stages of construction, along with many green construction skills. It also makes insuring timber buildings more difficult.
This is a problem we are trying to address at Timber Development UK (TDUK) through our knowledge database and industry partnerships. But the huge gap in green construction skills in the UK will need to be closed if we are to see more large-scale sustainable projects.
Size isn’t everything
However, size isn’t everything. The UK was an early leader in constructing timber towers, with architect Waugh Thistleton and Hackney Council completing a 29m, nine-storey apartment building in Murray Grove in 2009. This has become a world-renowned example of timber construction.
In January, the Black & White Building, from Waugh Thistleton and The Office Group, became London’s tallest engineered-timber office building. Standing 17.8m tall, the six-storey building is an ingenious example of timber construction. It contains no concrete above the ground-floor slab; its frame uses timber to provide all the strength and adaptability of steel.
Meanwhile, the 2022 Wood Awards winner, Homerton College Dining Hall by Feilden Fowles, was built using sweet chestnut glulam for the frame and internally lined with ash. The 2022 RIBA Stirling Prize winner Magdalene College Library in Cambridge showcased engineered timber elements to a global audience.
Volume solutions
So, the expertise does exist in the UK to tackle ambitious timber projects. There is also potential to increase use of panelised timber-frame houses. Volume solutions will help ensure the supply chain is ready to reach new heights when the time is right.
One thing that we know is that timber will take centre stage as 2050 looms, whether that is above or below 18m. Though we are going through tough economic times, construction businesses should be encouraging staff to undertake CPD on timber and other green building methods. You don’t want to be left on the ground when others start building higher with timber.
David Hopkins is CEO of Timber Development UK.
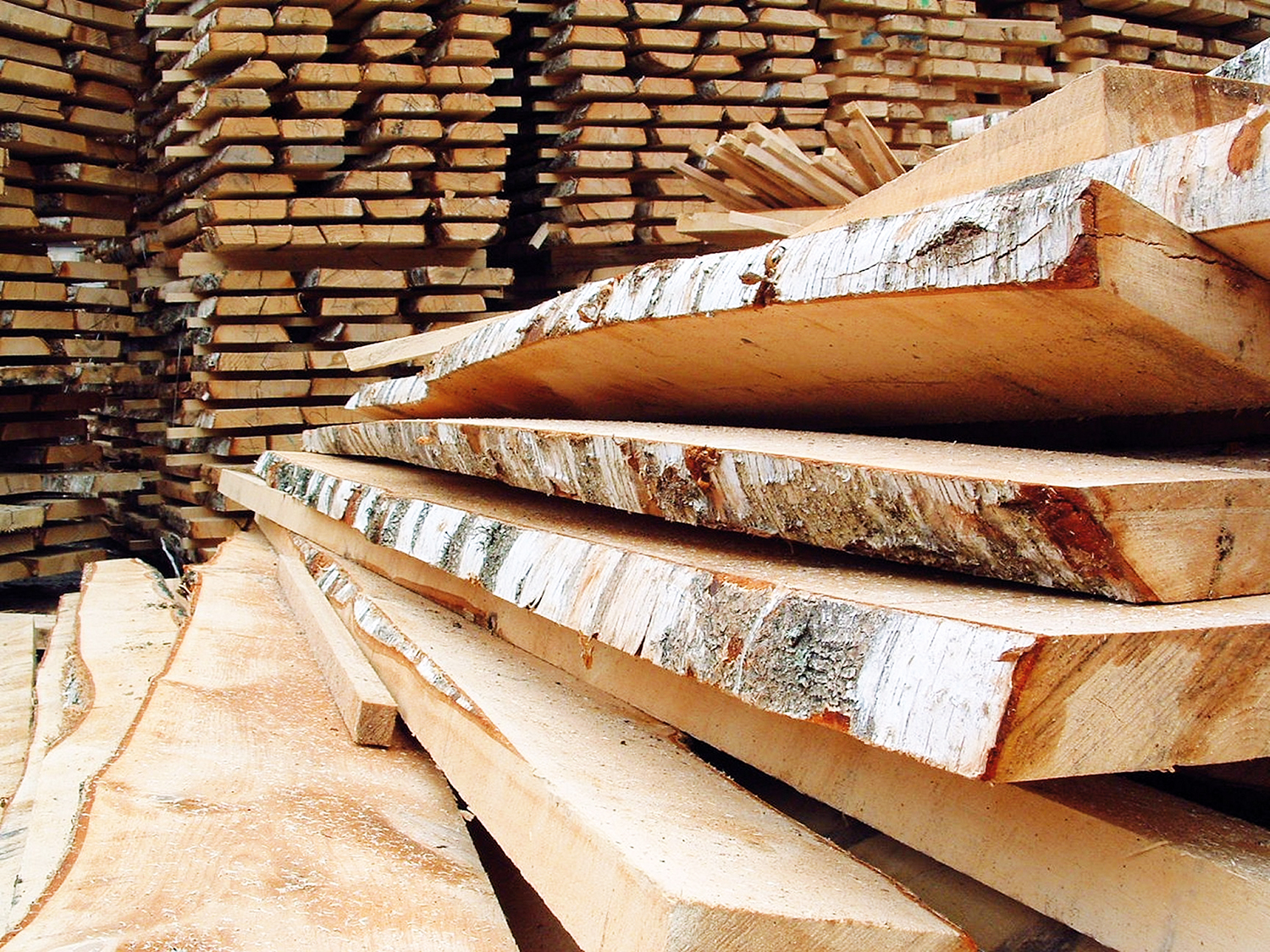
Gearing up the timber industry
Timber is a £10bn supply chain employing 350,000 people in the UK.
As part of the UK’s England Trees Action Plan, the UK government is working on a policy roadmap to encourage the use of homegrown wood in construction.
A key element of this is to increase tree planting rates across the UK to 30,000ha by the end of this parliament. However, the government is far from fulfilling that pledge.
As demand for timber construction increases, the UK needs to secure supply from trading nations on a short-term basis – and in the long term gear up for growth.
This includes increasing the amount of sustainable, productive forests in the UK, investment in sawmill capacity, panel product manufacture and wood fibre insulation manufacture. This will not only allow us to rely less on imported wood, but also create jobs for growth.
A strong, connected supply chain at home will help provide the backbone needed for more ambitious timber projects in the future.