The Digital Construction Awards attracted 165 entries this year, 84 of which have been shortlisted. Here, we detail the shortlisted entries for Digital Innovation in Productivity.
Digital Innovation in Productivity rewards the consultancy that has demonstrated excellence and helped their client(s) transform their businesses or projects through the adoption of digital processes and technologies.
Seven entries have made the shortlist.
Buildots
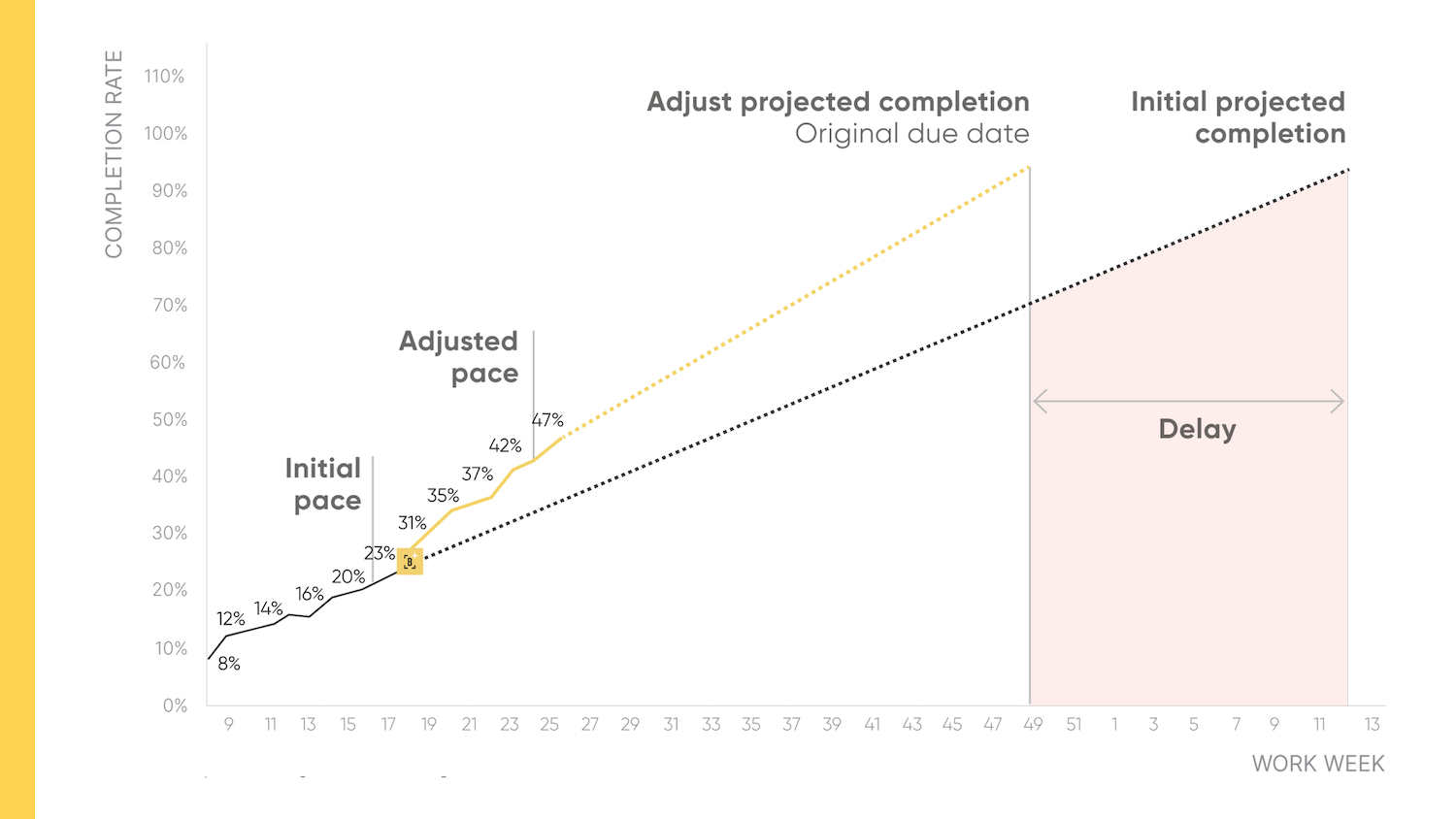
Using a combination of 360-degree helmet-mounted cameras and AI, Buildots is helping contractors to make data-driven, proactive decisions.
Perhaps the key productivity gain enabled by Buildots is predictive risk management: contractors can use the delay-forecasting capabilities to accurately plan and monitor activities each week to ensure deadlines are met.
Contractors can also use the Loose End tool, which flags all missed work on a weekly basis to prevent bottlenecks and delays. Buildots also produces accurate progress reports with predictive early warnings, which can be used to review past performance and plan upcoming activities.
Predictive risk management was a key factor for Integrated Health Projects (IHP), the joint venture between Sir Robert McAlpine and Vinci, which deployed Buildots to minimise preventable schedule overruns through proactive management.
IHP used Buildots to measure the pace of all active subcontractors on a weekly basis and compared this with the required pace for matching the planned schedule.
IHP found that the HVAC and plumbing subcontractors were behind schedule due to inefficient distribution of labour across floors, impacting critical paths in certain areas.
Looking at the underlying causes of the delays, IHP decided to shift the affected subcontractors to a different area and adjust sequencing. With these changes, IHP was able to increase its production pace to the required rate and safeguard the critical path.
Geospatial Commission/AtkinsRéalis | The National Underground Asset Register
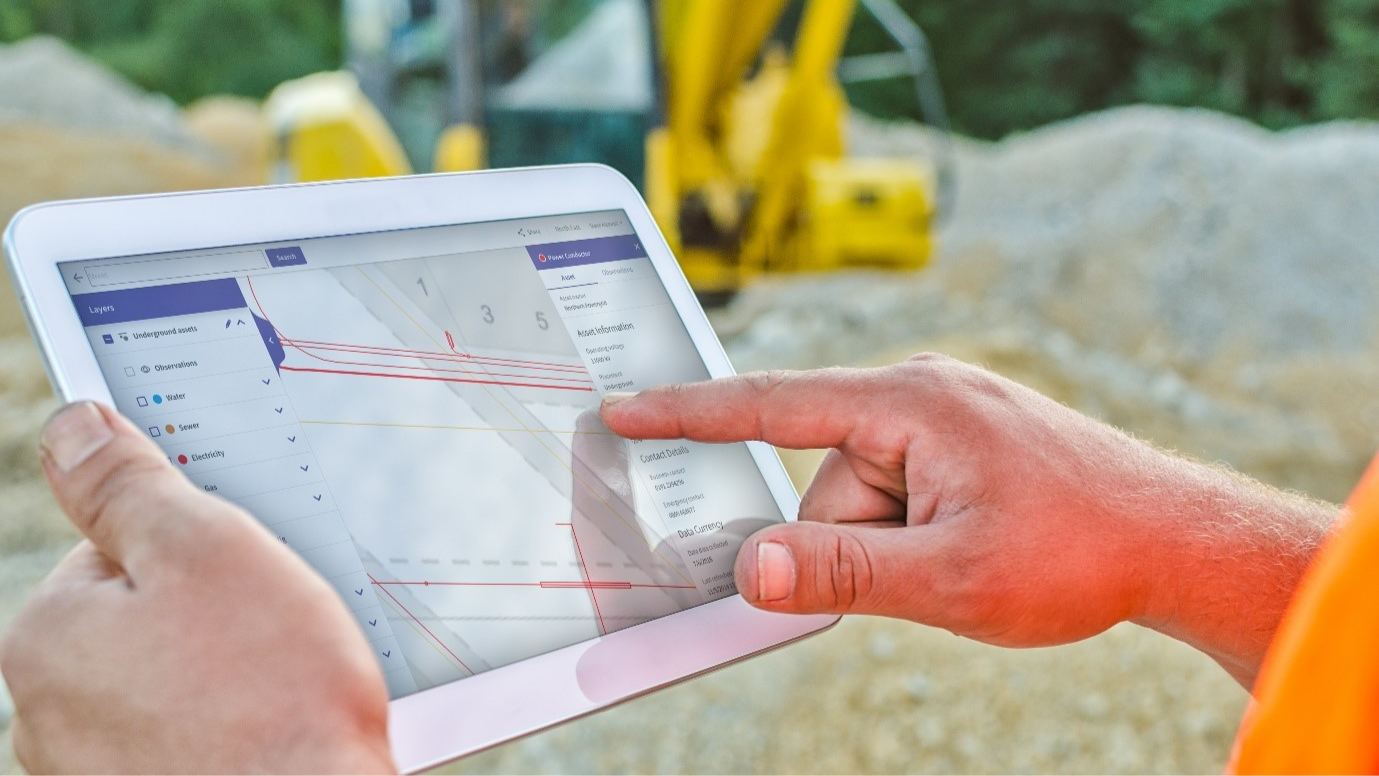
The Geospatial Commission and AtkinsRéalis are building the National Underground Asset Register (NUAR) – an interactive digital map of underground pipes and cables that will improve safe digging and end accidental strikes.
There are an estimated four million kilometres of underground pipes and cables across the UK, and a hole is dug every seven seconds to install, fix and maintain them. Each of the more than 700 owners of these assets is legally required to share data for ‘safe digging’. However, there is currently no standardised method for this, with multiple organisations having to be contacted for each dig, providing information in varied formats and to different timelines.
This results in an estimated 60,000 accidental strikes on these pipes and cables every year, putting workers’ safety and lives at risk, in addition to community disruption which costs the UK economy £2.4bn annually.
NUAR gives planners and excavators standardised, secure, instant access to the data they need, when they need it, to carry out work effectively and safely. It also reduces the time it takes to get location data from 6.1 days to 60 seconds.
An initial version of NUAR is now available across England, Wales and Northern Ireland. It already includes data from major energy, water and telecommunication companies, transport organisations and local authorities.
NUAR is expected to be fully operational by the end of 2025, when it is estimated it will deliver £490m of economic growth annually through reduced accidental damage, increased efficiency, and reduced community disruption.
JCB | LiveLink: Support Case Management
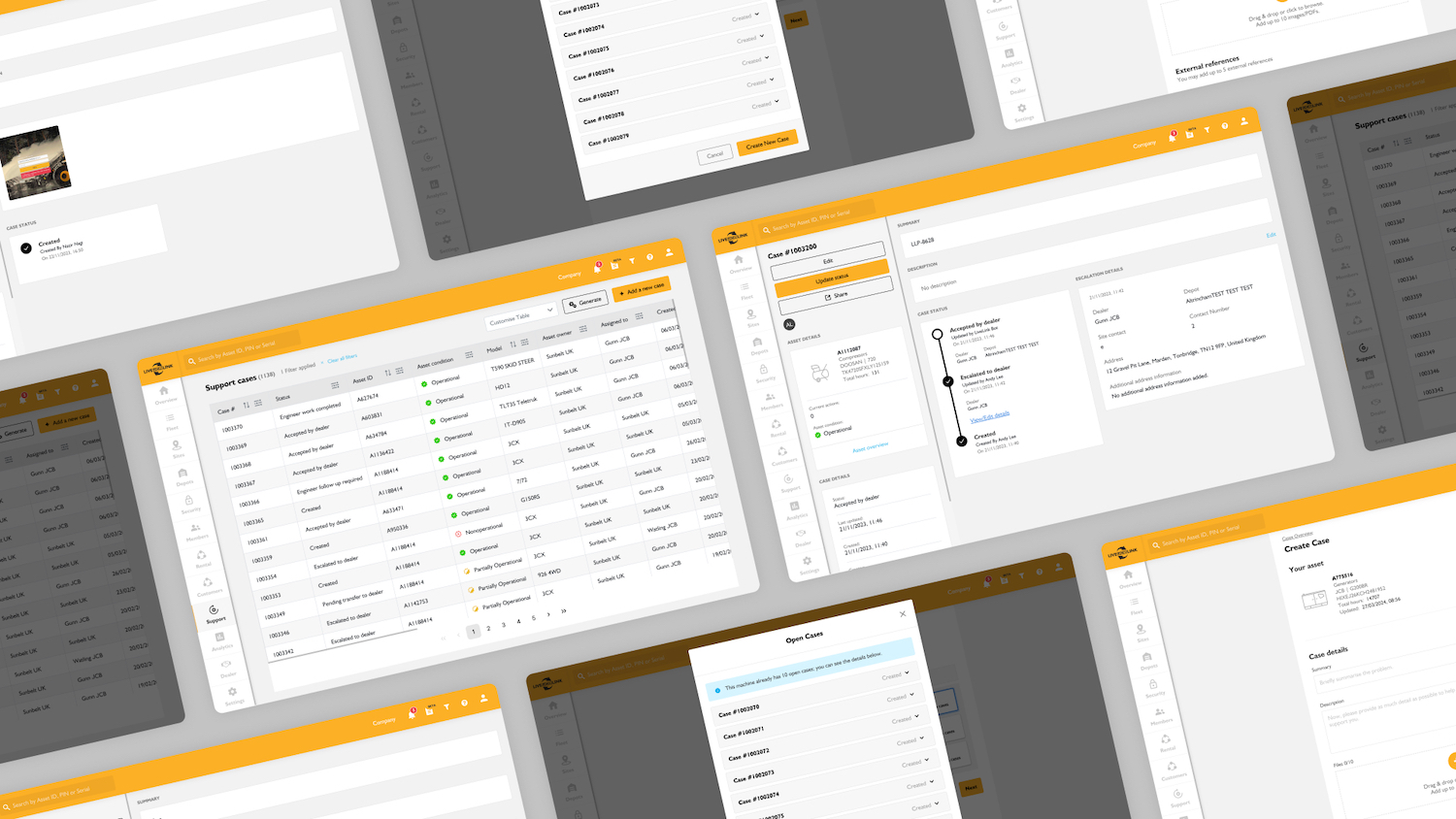
Machine downtime remains one of the biggest operational challenges facing the construction industry, costing UK operators over £1bn annually in lost productivity, repair costs, rental fees for replacements and penalties for delays, according to JCB.
Historically, the reporting and resolving of plant issues on site has been a manual and verbal process, with a high risk of human error: miscommunication of an issue can lead to an engineer arriving without the proper tools to fix the issue, for example.
JCB (alongside its digital partner Atomic Multimedia Consultants) developed JCB LiveLink, a telematic solution that allows customers to keep track of their entire fleet in one place. From monitoring live locations, receiving proactive health alerts, and setting security geofences to integrating mixed fleets, LiveLink equips users with actionable insights to help reduce costs, improve efficiency, and provide full peace of mind.
The system is delivered through a new web platform, and two mobile device apps, JCB LiveLink App and JCB Operator App.
Most importantly, LiveLink Support Case Management helps to ensure a more accurate reporting of plant-related issues – preventative maintenance, a routine inspection, or extra support – with traceability, enabling JCB to deliver the specific response the customer needs in a timely fashion.
LiveLink is designed to enable operators to easily and reliably report issues to achieve fast resolution, and to ensure that JCB dealer engineers receive high-quality and reliable information for quick and accurate remote diagnosis of machine issues.
And, like parcel-delivery apps, it keeps all parties involved informed with timely updates.
JCB estimates that more than 5,000 days of downtime have been averted since launch.
John Sisk & Son | Concrete Roads Framework
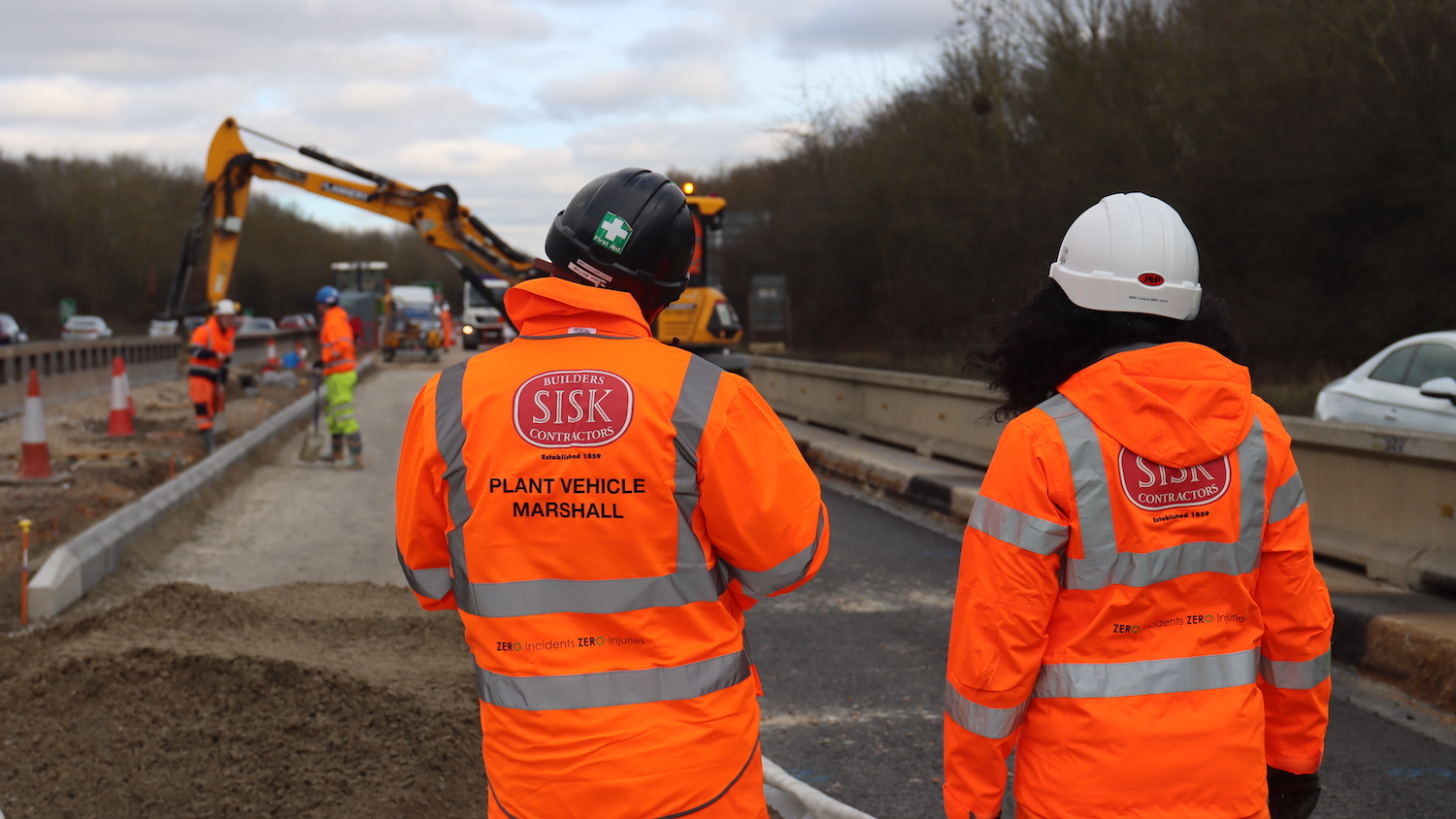
John Sisk & Son is leading the end-to-end digital (E2ED) strategy for National Highways on the £400m Concrete Roads Framework. The framework is meant to improve the quality of 400 miles of existing concrete roads, by either repairing or replacing the concrete surface of several motorways and major A roads.
The E2ED strategy introduces new methods of working and technologies, and involves 13 stakeholders across National Highways and its delivery partners for concrete roads reconstruction, lifecycle extension and design.
Work to date has involved creation of bespoke systems to support E2ED protocols with data managed through a supporting portal, covering the whole project lifecycle with surveys, design, construction and handover being managed digitally.
Sisk started with the end in mind – collaborating with the client and primary asset owners to understand future asset management requirements. Sisk’s leadership of the E2ED working group focused on providing guidance to stakeholders in delivering their commitments and assisting with improving productivity and problem-solving through technology advances.
Sisk drew up the Exchange Information Requirements (EIR) that inform the delivery of an asset information model. The EIR provided the fundamental step-change for all stakeholders to adopt digital processes that allow the reuse of the populated values in design and construction within K-Portal (the geospatial asset data collation portal) and inform the primary asset owners’ systems.
This relationship between Sisk’s combined model with the client’s K-Portal delivered the greatest benefit, enabling early engagement with stakeholders who would traditionally not get involved in the early process. There was a more thorough review process that also served as mitigation against future cost increases.
Laing O’Rourke/AtkinsRéalis/VolkerRail | Geographical Information System on East West Rail
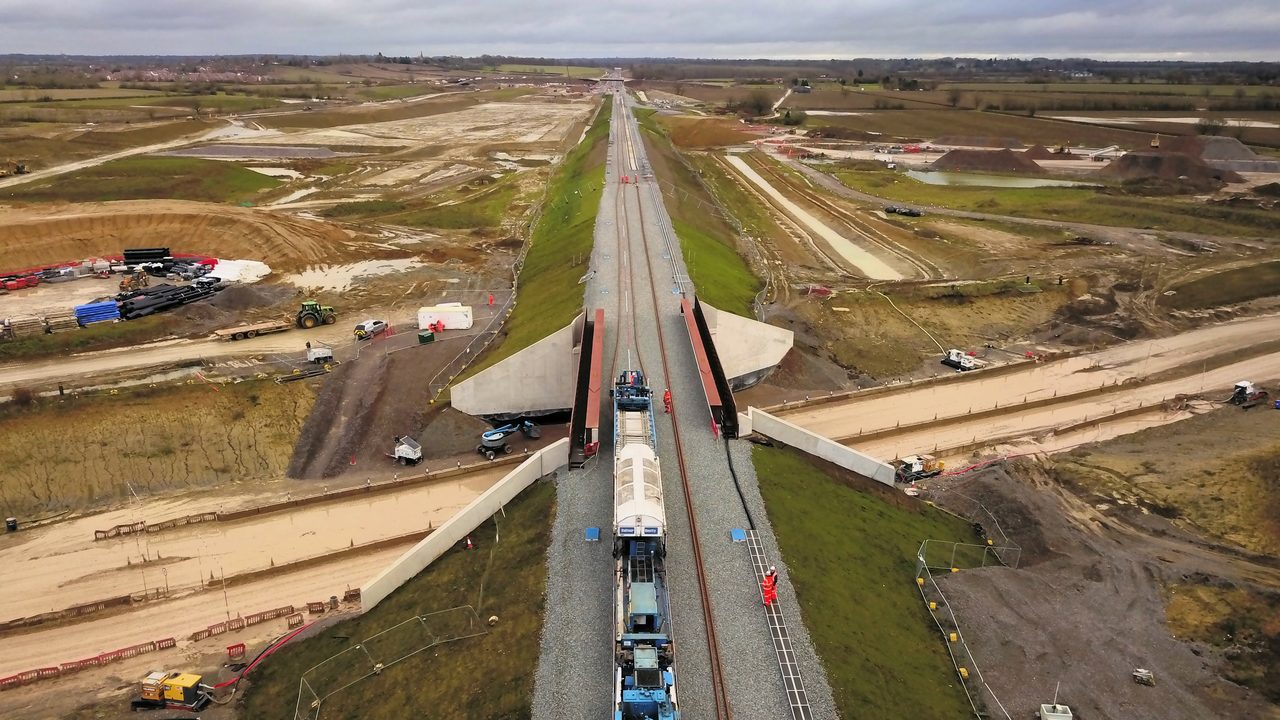
Using a geographical information system (GIS), Laing O’Rourke has taken an onerous week-long boundary surveying task along 40km of the site and reduced it to a day of work. The subsequent efficiency gains have catalysed a new methodology in the delivery of large-scale infrastructure projects, which the contractor believes is set to become standard practice in the industry.
At the East West Rail (EWR) Alliance, GIS served as a comprehensive repository for project data, becoming crucial for handling as-built details, particularly fencing, as the project approached completion.
Ensuring all fencing remained within the legally defined Transport Works Order Boundary was vital. Traditionally, the installation verification by the supply chain required manual checks by Laing O’Rourke’s surveying team – a process that could extend to a week, depending on the fencing volume that had been installed. To streamline this, the contractor proposed leveraging GIS to add buffers to the boundary, allowing for a focused review of fencing potentially outside the legal limits.
By querying for installations 5m or 10m beyond the boundary, the team’s workload was significantly reduced to only exceptions. Further enhancing efficiency, Laing O’Rourke developed a Python script within GIS to automate the update and review process, delivering swift feedback to the surveying team. This innovation not only accelerated verification, but also ensured compliance with legal boundaries, illustrating the transformative impact of integrating technology into traditional surveying practices.
The effectiveness of this method was so pronounced that it was rapidly adopted across all phases of the EWR project within a month.
Subsequently, the Python script and mapping technique were further applied to the HS2 enabling works project.
Laing O’Rourke is now actively incorporating the script and mapping method into bids for more rail infrastructure projects.
L Lynch | The Operator App and the Customer App
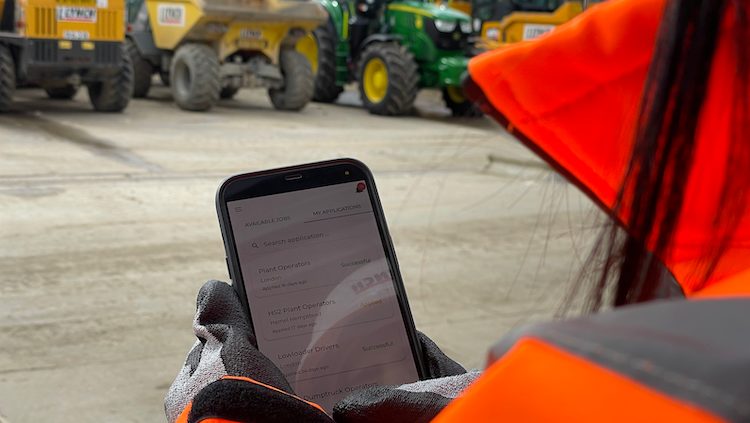
As a leading provider of operated plant hire, L Lynch engages with thousands of operators throughout various touchpoints, from onboarding to compliance, scheduling, and timesheet management.
Traditionally, Lynch’s processes were cumbersome, relying on a plethora of phone calls, WhatsApp messages, online forms, and emails. Recognising the importance of efficiency and clarity, Lynch endeavoured to modernise its recruitment and onboarding processes. Additionally, transitioning from paper-based timesheet recording to a digital platform was essential to mitigate delays and errors, ensuring prompt and accurate payments and satisfied operators.
Such a new system had to be digital, automated and, most importantly, user-friendly and accessible for the operator, customer and internal stakeholders.
The Operator App streamlines processes related to operators, automating tasks such as onboarding, compliance, scheduling, and timesheet recording. By consolidating timesheets and daily defect reporting into a user-friendly interface, Lynch claims it has created a “frictionless experience tailored to site workers, regardless of their technical proficiency”.
Similarly, the Customer App is designed with the customer in mind, facilitating task management on smartphones. With modern interfaces and search functions, it integrates essential data in one location. Telematics functionality provides live tracking and insights, empowering customers to make informed decisions and improve project efficiency.
Lynch has reduced depot call times by up to two hours per week and streamlined operator onboarding, saving approximately 30 minutes per operator.
Additionally, invoice accuracy has improved from 97% to 99.4%, and payment accuracy from 96% to 99.7% with the app.
Teknobuilt | Accelerating data centre construction delivery
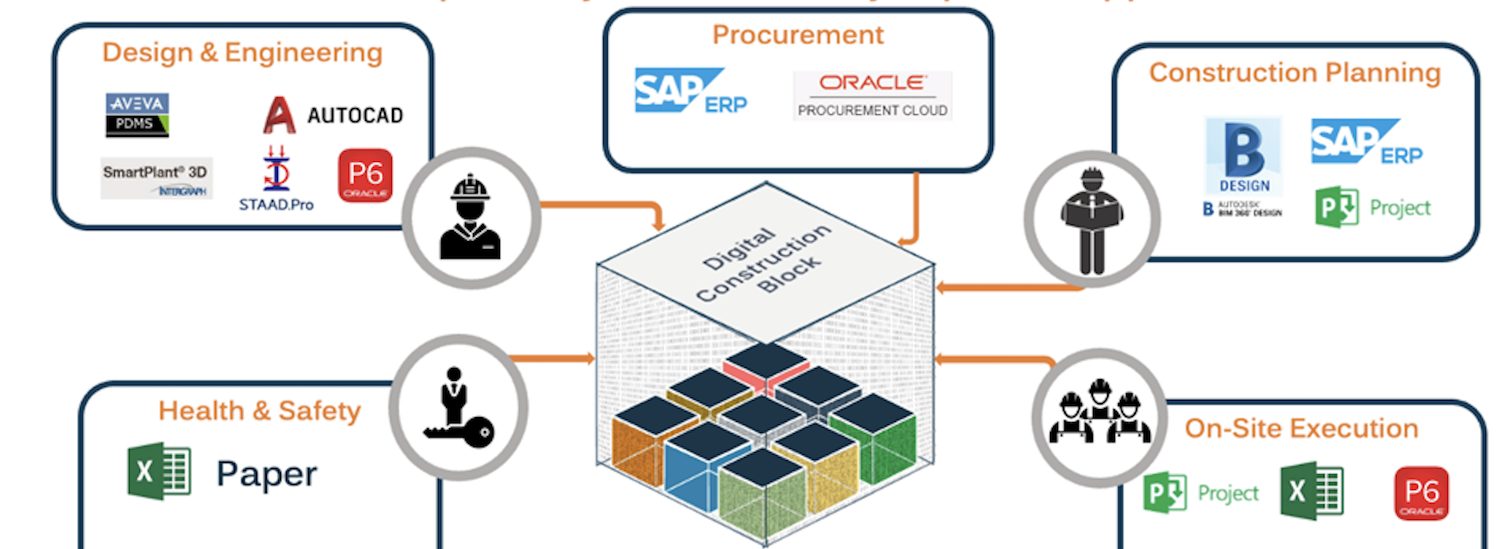
Teknobuilt claims it is “revolutionising the way data centre projects are delivered”. It has reduced the average design-to-build time for data centres from 22 months to just 15.
Its data centre client faced numerous challenges that led to massive delays. The challenges were significant, including constant schedule overruns, missed milestones, poor visibility during project execution, inability to accommodate changes during construction, and inefficient planning of the construction sequence.
To overcome these challenges, the project aimed to optimise the timeline for constructing and delivering data centres, improve project schedule predictability, increase owner’s assurance, provide visibility and certainty of contractors’ deliveries, and offer early visibility of potential hindrances and delays.
Teknobuilt’s subject matter experts analysed the current work processes, met with key internal and external stakeholders, and identified various ways to improve efficiency and foster collaboration. The Teknobuilt team created a scalable and repeatable blueprint to improve work breakdown and accelerate project delivery. By using its digital solutions, Teknobuilt has significantly increased efficiency, automated manual processes and unlocked valuable insights and intelligence to help identify issues early.
Teknobuilt combines the AWP (advanced work packaging) methodology from oil and gas construction with Lean thinking. While AWP methodology provides a structured approach to project management, integrating Lean principles can further improve efficiency, reduce waste, foster collaboration, drive continuous improvement, and ultimately improve project outcomes across various dimensions including cost, schedule, quality, and safety, according to Teknobuilt.
This approach is combined with Teknobuilt’s platform, which uses what it calls digital construction blocks that allow real-time collaboration and document management, optimisation of project scheduling, and the collection and consumption of data through machine learning models.
Celebrate with the best
The winners of the Digital Innovation in Productivity category, alongside the victors of the other 12 categories, will be revealed at the awards dinner on 2 July at the Brewery in London.
You can join them by booking your places at the awards.
The Digital Construction Awards celebrate best practice and reward innovation in the application of information management and digital technology in the built environment sector.
The awards are run by Digital Construction Week, the Chartered Institute of Building (CIOB), and Construction Management and BIMplus.
Awards sponsors include Bluebeam, Procore, Revizto and the CIOB.
Don’t miss out on BIM and digital construction news: sign up to receive the BIMplus newsletter.