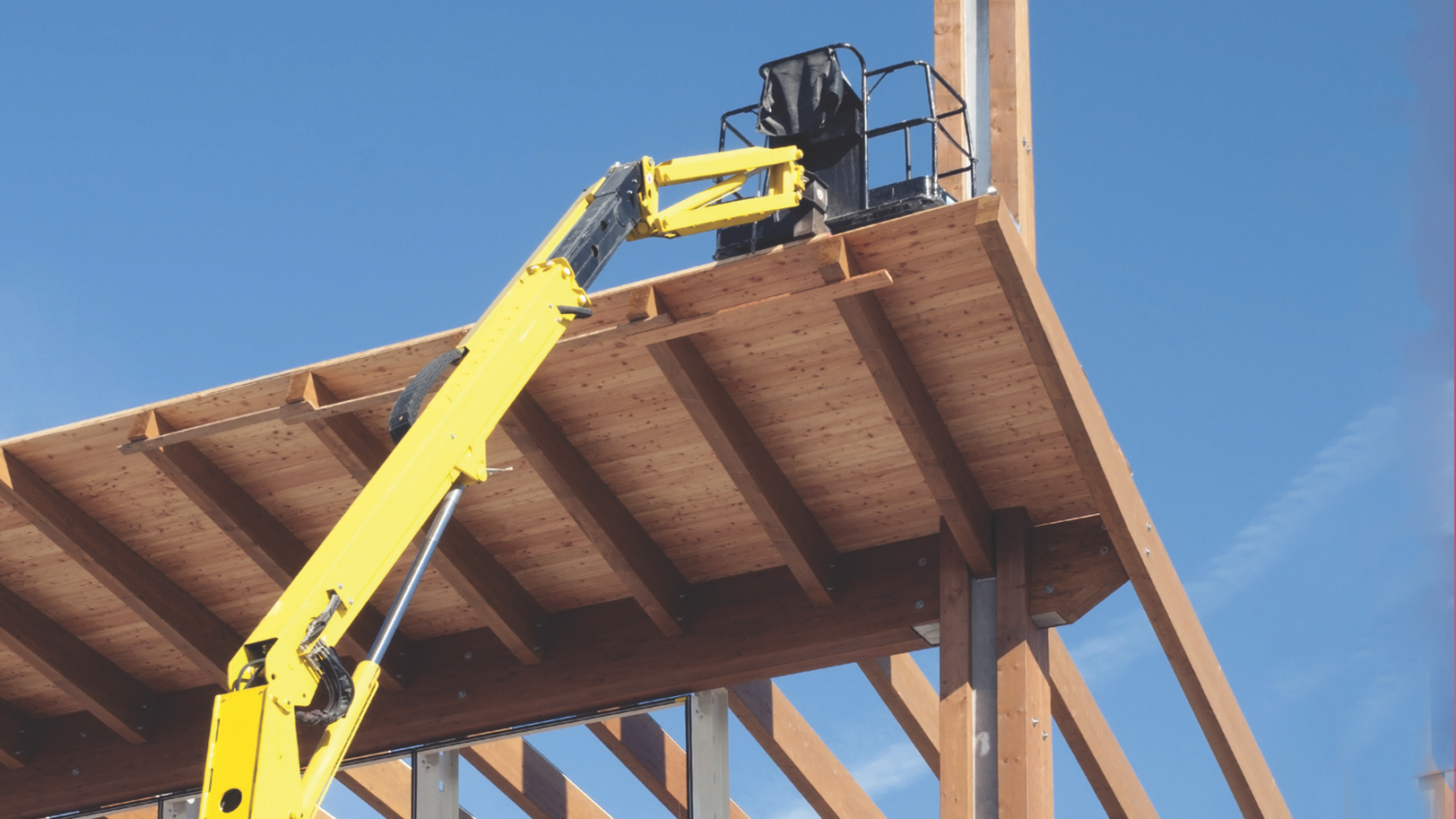
As timber construction becomes more popular as the UK tries to reach its net zero targets, how can construction with the material overcome its insurance challenges, asks Jim Glockling?
An inevitable consequence of the net zero ambition will be the increased use of wood as a structural building component of large buildings. Those in the construction industry need to understand the insurance challenges of massive timber construction to ensure they are designing and constructing buildings that are both sustainable and insurable.
Massive, or mass timber construction, uses load-bearing timber products such as cross-laminated timber (CLT panels), laminated veneer lumber (LVL), glulam and other engineered wood products.
For the insurer this presents a number of challenges: the ways they are assembled, and the additional insured perils that come in to play, especially when tall wood building are considered. These changes impact the very heart of established insurance principles for assessment and risk measurement, and to the uninformed the level of insurer concern could be mistaken for a knee-jerk reaction to the unknown.
“Insurers are particularly worried about water damage as leaks occur more frequently than fire and timber is more susceptible to water damage.”
Compliance with regulations might no longer be enough to ensure a building is buildable. No one would design a car that was uninsurable or excessively expensive to insure. The same considerations are becoming true for some buildings now that we are using materials more susceptible to fire and water. Insurers need to be able to conclude that the likely scale of loss in the event of a fire would be less than 100%, and this needs to be considered in the building design. This is not natively assured by compliance with regulations which, in the UK, are devoid of property protection measures.
Fire safety challenges, water exposure and the combination of combustible materials and voids are several key areas of concern for timber constructions. The escape of water alone is the greatest category of loss in the domestic and residential sector, greater than fire and security combined.
Insurers are particularly worried about water damage as leaks occur more frequently than fire and timber is more susceptible to water damage. Concerns focus on the risk of engineered timber products decontaminating and the risk of structural deterioration from long term, hidden water seepage.
A possible solution to insurance challenges lies in the hybridisation of traditional and modern building methods and materials. To reduce flood and fire risk, ideally at least half of the structure of multi-storey buildings should be non-combustible. The building of the first floor of a mass timber building should be in concrete with concrete floors that alternate with timber floors thereafter. All plant, electrical intake, bathrooms and kitchens should be located in the concrete core and the building should utilise a CLT panel waterproofing membrane which reduces the potential for water damage during delivery and construction before waterproofing.
“To reduce flood and fire risk, ideally at least half of the structure of multi-storey buildings should be non-combustible.”
The presence of combustible voids in cavities and roof spaces which allow the unseen spread of fires are perceived as some of the greatest challenges in building safety for insurers. A possible solution here is for all timber to be encapsulated and protected from fire exposure by gypsum or other materials to resist fire and prevent its spread and any combustible voids should be either lined, sprinkler protected or filled.
These are just a few examples which demonstrate that progress can be made to achieve the best route forward to satisfying both property insurers and all stakeholders involved in timber construction projects.
While every insurer has their own preferences, methods, and risk appetite, by succinctly positioning the insurer viewpoint, designers, architects and insurers can collaborate better to address these concerns from a common platform.
Already industry is responding with innovative solutions (often hybridisation of new and old building methods and materials) to curtail the risks posed by fire, escape of water, and flood events, but there is no doubt that government could do a great deal more by reviewing Building Regulations to include property protection to assist all.
RISCAuthority’s whitepaper provides a definitive description of the insurance challenges of timber construction methods based on insights from 24 major UK insurers. To learn more about how buildings can be designed and constructed so that they are both sustainable and insurable, download the whitepaper here.
Jim Glockling is technical director of the Fire Protection Association and RISCAuthority.
Comments
Comments are closed.
I appreciate this article is written from the perspective of a fire consultant and is reviewing the insurance issues associated with mass timber. Therein lies the problem! The construction industry needs to collaborate on effective building solutions in order to meet climate emergency targets, reduce carbon emissions, reduce risks and provide healthy, functional, affordable buildings.
This article highlights that a majority of insurance claims stem from water leaks, yet the prevention of water leaks and containment (the root cause) appear to be ignored, with the focus being on the material construction and its components. Whilst timber per se is a combustible material, in mass timber form its properties are substantive and considerably healthier, both from the occupants and material source perspective. It also seems strange that a hybrid construction proposal is being mooted without definitive technical guidance or experience to support this.
It would make sense for the CIOB and every other representative body to make a definitive step to meeting future building needs by getting together and providing workable solutions immediately. For those who don’t understand the concerns raised in the most recent IPCC report, the planet doesn’t have much time left for mankind to put matters right, yet the opportunity exists and if we don’t take it quickly it will all be too late. We in the construction industry have a lot to answer for but are moving at snails pace to address the problems we create.