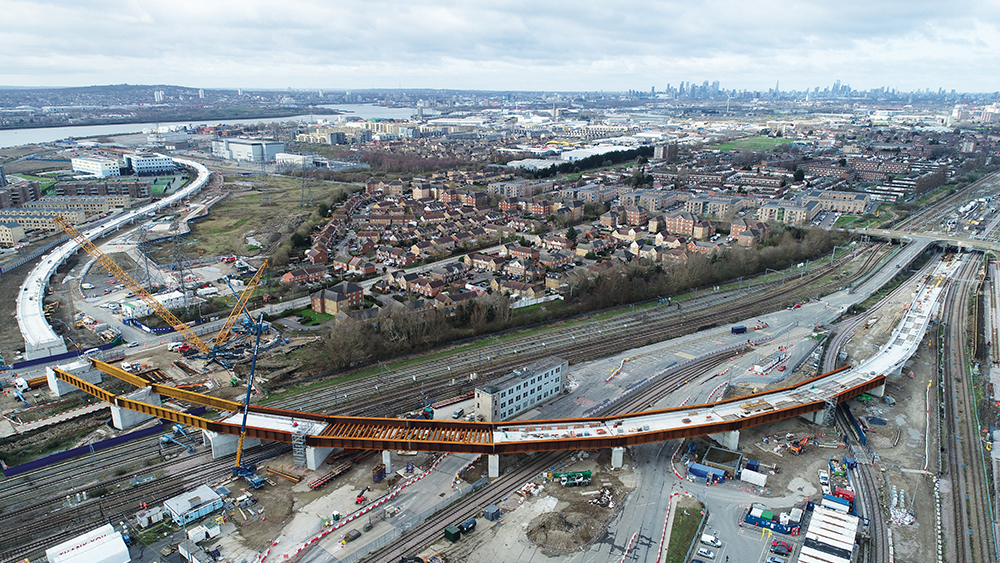
Connecting a new riverside development meant traversing a number of significant infrastructure assets including rail lines, a freight yard, HS1 tunnels, roads and a waterway. The solution is a 1.5km-long viaduct using steel to minimise disruption to these assets. Martin Cooper reports.
With planning permission for up to 10,800 new homes, along with numerous healthcare, shopping, community and leisure facilities, Barking Riverside is currently east London’s largest housing-led mixed-use development.
Located on the site of a former coal-fired power station that closed in 1981, the former brownfield area is not best served by public transport and in order for the new development to realise its full potential a dedicated railway extension and station are being built.
The extension will add 4.5km to the London Overground network, extending the Gospel Oak line from Barking to a new elevated Barking Riverside terminus, which will be situated in the main square of the development. On completion, it will be capable of operating four trains per hour and provide residents with a vital transport link to the rest of the capital and beyond.
Project team – Barking Riverside Viaduct
Architect: Weston Williamson
Client: Transport for London (TfL)
Main contractor: MSVF (Morgan Sindall/VolkerFitzpatrick JV)
Structural engineer: Arcadis
Steelwork contractor: Severfield
Better public transport links go hand in hand with the development’s sustainability goals. The new railway, along with planned river transport, will mean there will be less reliance on residents having to drive. Other green credentials at Barking Riverside include over 41% of the site being dedicated to open space, including a new ecology park with all green areas linked by parkland, cycle routes and footpaths.
A key element of the extension is a 1.5km-long viaduct that carries the final part of the new twin railway line over a number of infrastructure assets, such as the existing London to Tilbury rail lines, a DB Cargo freight yard, High Speed One tunnels, roads and a waterway.
Being able to span these obstacles is the main reason why this part of the new branch line has been built on a viaduct, although a high water table is also a major factor. Meanwhile, the elevated railway and its terminus will create a focal point in the heart of the new town square as well as providing commercial and retail opportunities in the bays under the raised station.
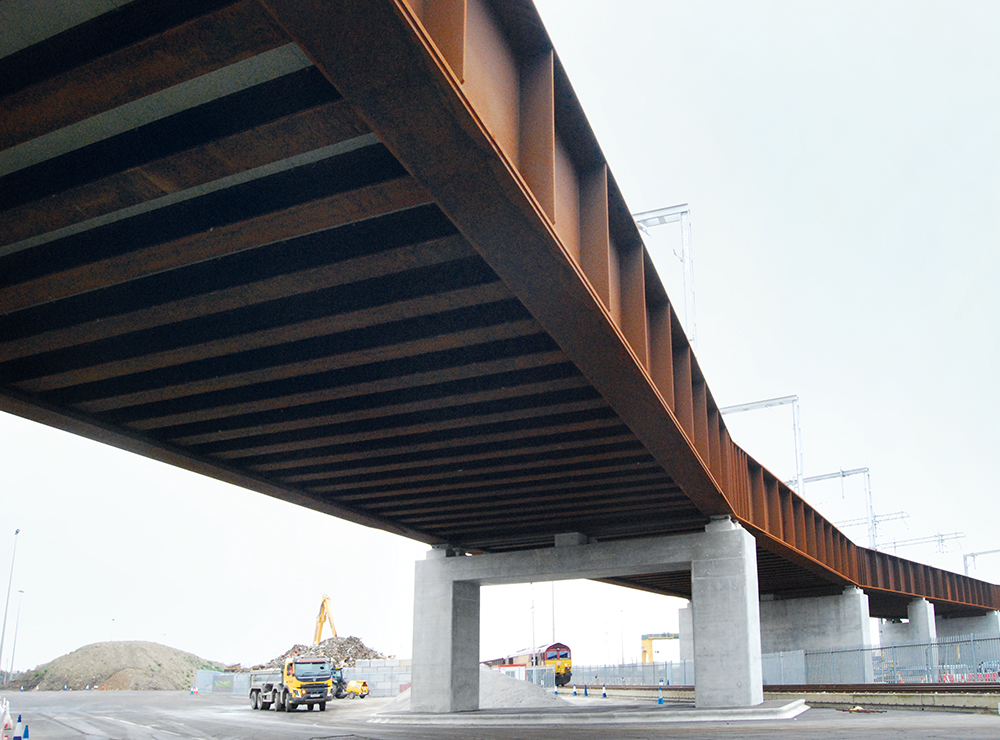
The viaduct can be divided into two parts: a concrete structure with precast beams and piers supporting a cast in-situ deck; and a steel viaduct also supported on concrete piers.
The former creates the longest part of the viaduct and ends at the Barking Riverside terminus, while the latter is approximately 400m long and consists of nine spans at the northern end, with some 3,500 tonnes of steel used in total.
Explaining the reason for choosing two different construction designs, Transport for London’s (TfL) head of programme James Barrows says: “Steelwork was chosen for the northern end of the viaduct as it was the only material that could efficiently create the longer spans, up to 42m long, needed to pass over rail, road and river obstacles.”
“We have built 57 concrete piers to support the deck along the entire route of the viaduct, each one supported on piled foundations which are up to 45m deep.”
As well as creating the required long spans, the use of steel has allowed the project team to minimise disruption to these infrastructure assets. Less time and equipment was needed to erect the steel part of the viaduct, as prefabricated girders were brought to site, ready to be erected during a series of weekend possessions.
All of the sections used are fabricated from weathering steel, which was specified because the material is durable and requires no future maintenance or painting. This is an important consideration, as any work on the viaduct in the future could cause major disruption to the operational railway assets below.
Working on behalf of TfL, construction of the viaduct was begun by Morgan Sindall/VolkerFitzpatrick joint venture (MSVF) in 2019. As well as the interfaces with existing transport infrastructure, the site is also home to a myriad of underground services, all of which had to be located and then worked around when MSVF started the piling programme.
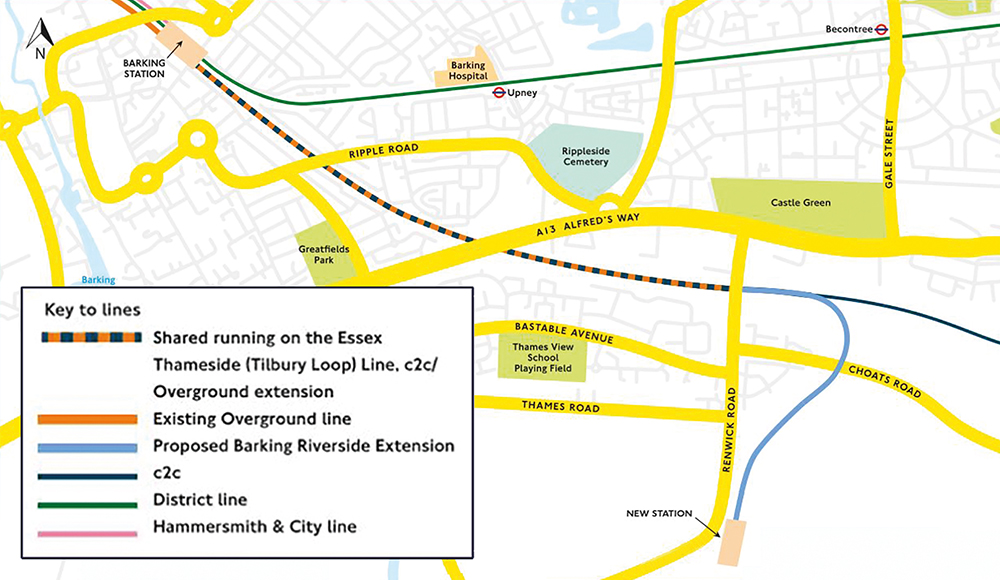
There are also some services above ground, namely a series of high-tension overhead cables crossing the route of the concrete part of the viaduct. In this location, the structure has actually been designed to dip down and then up again to ensure suitable electrical clearance is achieved for the railway’s overhead power system.
“We have built 57 concrete piers to support the deck along the entire route of the viaduct, each one supported on piled foundations which are up to 45m deep,” says MSVF project director Steve Balliston.
The construction of the piers was followed by the installation of the viaduct’s deck. For the steelwork element, this work started with the most northerly steel girders for span five. Beyond this, spans one to four form the ramp of the viaduct that bring the structure up to its regular 12m height.
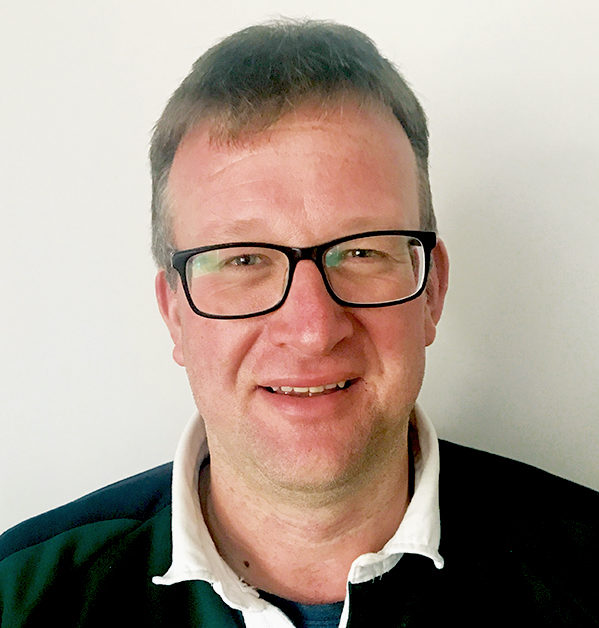
Construction career: James Barrows, head of programme, Transport for London
James Barrows arrived at Transport for London in 2007, after 10 years with Balfour Beatty, which he joined after graduating from London South Bank University with a civil engineering degree.
He worked as a project engineer and project manager with London Underground before moving on to the Barking Riverside Extension project in late 2016, when the design was being completed. Barrows then led the project through the detailed design and contract award phases, appointment of the Morgan Sindall/VolkerFitzpatrick joint venture, and commencement of site works in early 2019.
In January 2020, he was appointed head of programme of the Barking Riverside Extension.
Span five goes over a DB Cargo siding that forms part of its Ripple Lane depot. Requiring weekend possessions and close coordination with the rail freight provider, steelwork contractor Severfield and its lifting partner, Sarens, installed the span’s two main plate girders, each weighing more than 100 tonnes and measuring 35m long x 3m deep.
Each of the steel spans has up to 22 cross beam members, all 12m long (corresponding with the width of the viaduct). Four cross beams were also installed during the span five weekend possession, with the remainder lifted into place during the following week. This initial steelwork, and most of the subsequent lifts, were done using a Sarens 1,000 tonne capacity mobile crane.
The next four spans also go over the Ripple Lane depot and include one span supported by smaller, slender columns designed to allow easier vehicle movements around Ripple Lane.
“The viaduct piers are mostly large solid structures, and would be intrusive within the depot and impede vehicle movements,” explains Barrows. “For one span, we have installed two slender columns instead of a pier as they allow vehicles to easily pass, while the adjacent pier has been designed with a large opening in the middle for vehicular access.”
Largest steel sections
A challenging rail interface occurs adjacent to the goods yard where the viaduct spans the Tilbury to Fenchurch Street lines. Beneath these tracks are the High Speed One tunnels that accommodate Eurostar and domestic trains from London St Pancras station. Pile locations were consequently limited and they had to be installed around these subterranean assets.
One of the final steel spans to be installed was also the longest and because of site constraints, required the use of one of the UK’s biggest mobile cranes, with a lifting capacity of 1,200 tonnes.
Two steel girders, measuring 42m long x 3m deep and each weighing 120 tonnes, represented some of the largest sections ever fabricated by Severfield at its Lostock facility near Bolton.
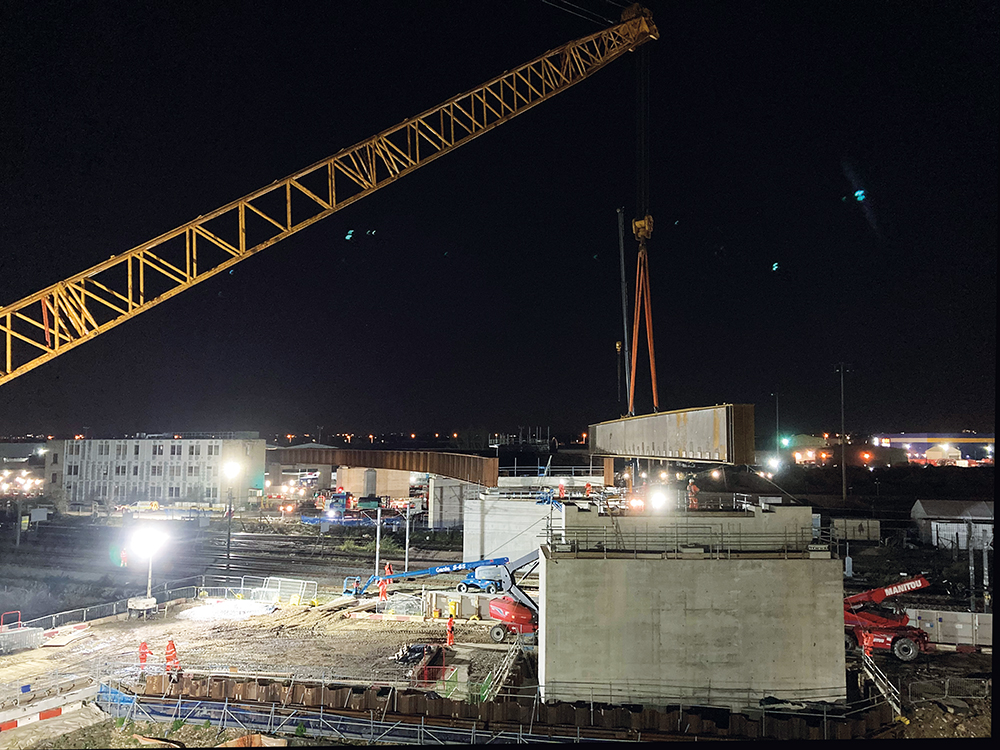
Moving these large steel sections around the yard and onto delivery trucks was a significant challenge, as Severfield assistant project manager Gethin Williams explains: “Our overhead cranes at Lostock have a lifting capacity of 100 tonnes, which is not enough to lift these items.
“The solution was to fabricate each girder on temporary trestles. Once the sections were ready to leave the factory, self-propelled modular transporters (SPMTs), each with a maximum lifting capacity of 140 tonnes, were reversed under the temporary trestles and jacked up towards the steel beams to allow for safe loading on to delivery trucks.”
Transporting the girders to east London was also challenging. Severfield had to liaise with local councils and police to temporarily remove traffic lights and other street furniture that would otherwise obstruct their movement – both near the factory and Barking.
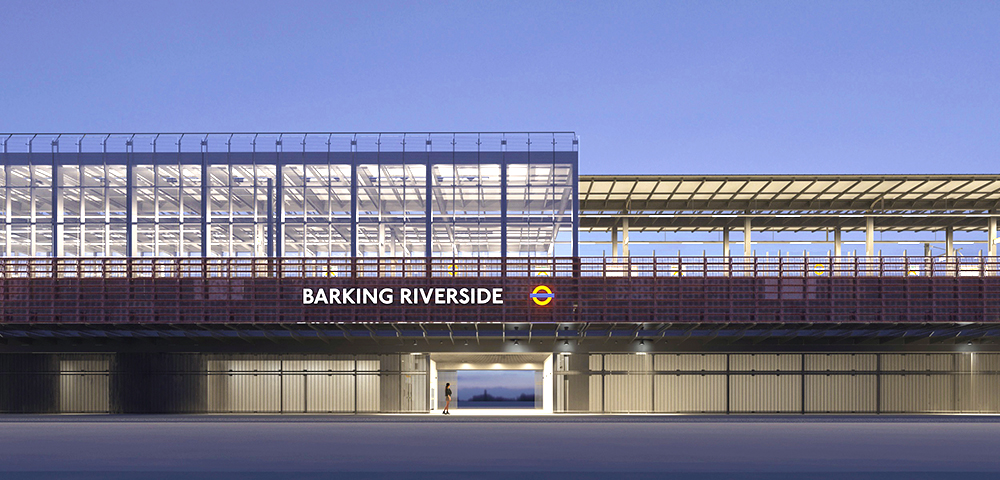
Once delivered to site, the girders were installed using a Sarens Gottwald 1,200-tonne capacity mobile crane lifting the 120-tonne girders at a 65m radius, with a 71m main boom, and requiring 350 tonnes of lift ballast.
The installation of this vital span, which crosses the Ship and Shovel waterway, allowed the team to lift the final steel girders into place last April, allowing the follow-on trades installing the deck and tracks to begin their work. Barking Riverside train services are scheduled to start during autumn 2022.