To reduce embodied carbon in construction, you need carbon calculators – and three high-profile tools have recently been launched. CM reports
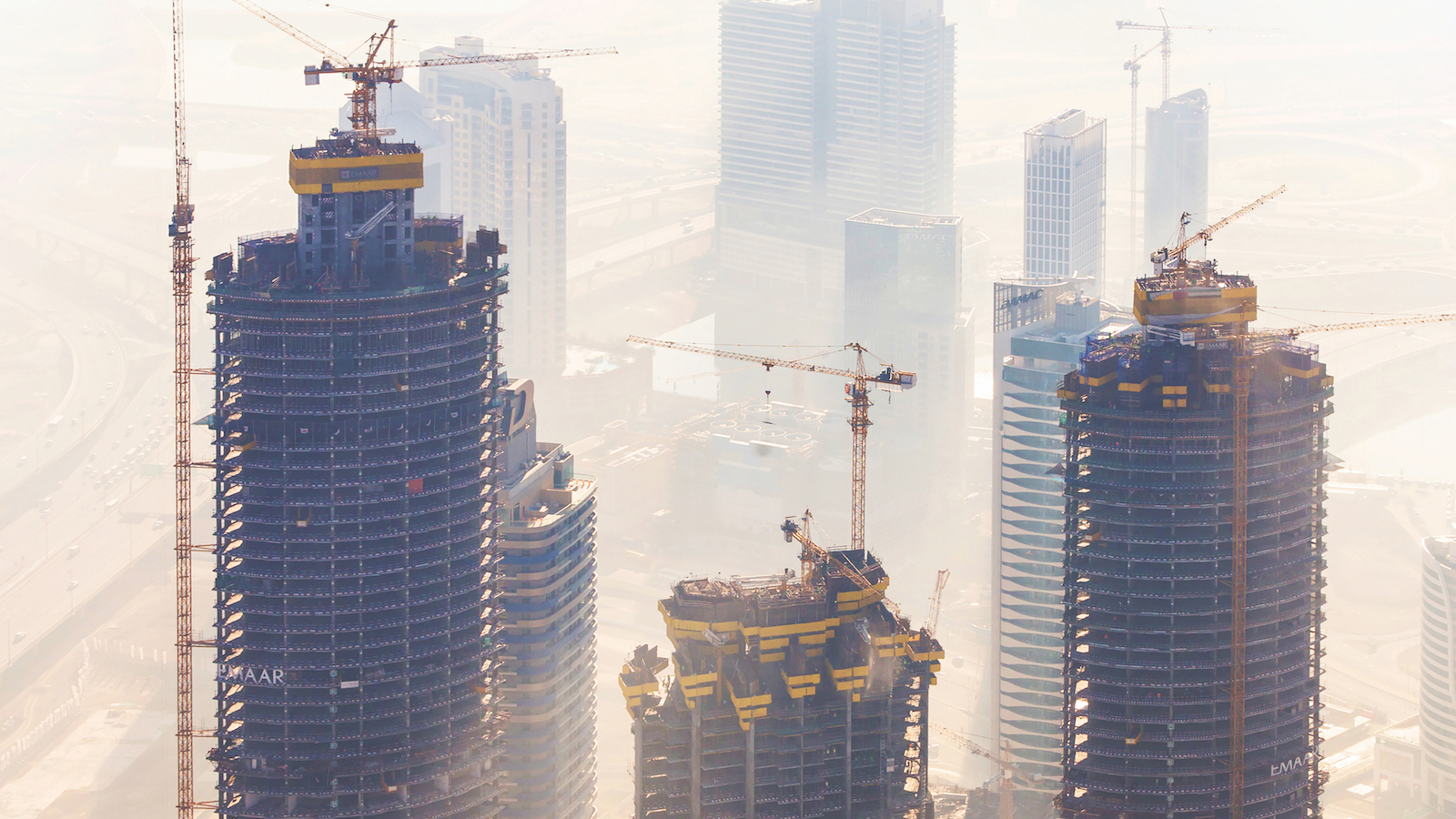
Carbon reduction targets are scary: to avoid the catastrophic effects of a 1.5 deg C of global warming, the UN’s Intergovernmental Panel on Climate Change suggests that humanity must curb its carbon emissions by 49% by 2030 and achieve carbon neutrality by 2050.
To cut carbon, we must first measure it wherever we can find it – and there’s a lot of carbon to be found in the built environment (see UK Green Building Council definition, below).
In recent months, three high-profile carbon calculators have been revealed: Balfour Beatty’s AutoBIM Carbon Calculator and the Costain/Winvic tool are both in testing (see boxes), while the Structural Carbon Tool from Elliott Wood and the Institution of Structural Engineers (IStructE) was launched a month ago and is already in the hands of more than 1,400 people.
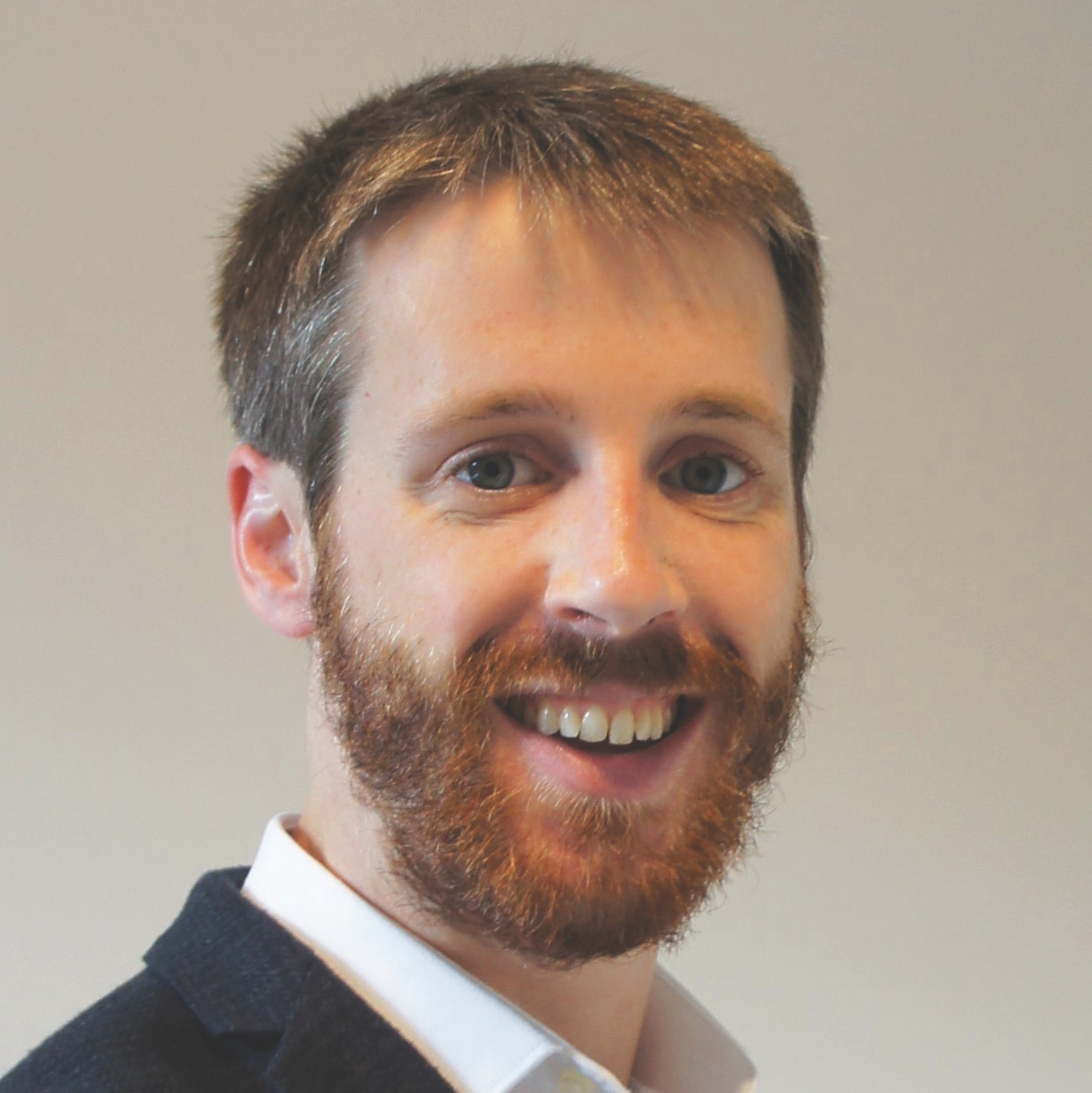
“If you’ve never done a carbon calculation in your life, within two minutes of using the tool you can work out the carbon footprint of a beam or column”
The Structural Carbon Tool is free to everyone: you don’t have to be an IStructE member to download it. It’s an Excel-based tool, aligned with BS EN 15978, BS EN 15804, and is based on Elliott Wood’s in-house carbon calculation tool, reconfigured to interpret IStructE’s How To Calculate Embodied Carbon document.
Will Arnold, head of climate action at IStructE, says: “It’s designed to be universally applicable to any size of project, to any size consultancy anywhere in the world. The idea is that if you’ve never done a carbon calculation in your life, within two minutes of using the tool you can work out the carbon footprint of a beam or column. And within half an hour, you can measure a basic structure if you’ve got the quantities to hand.”
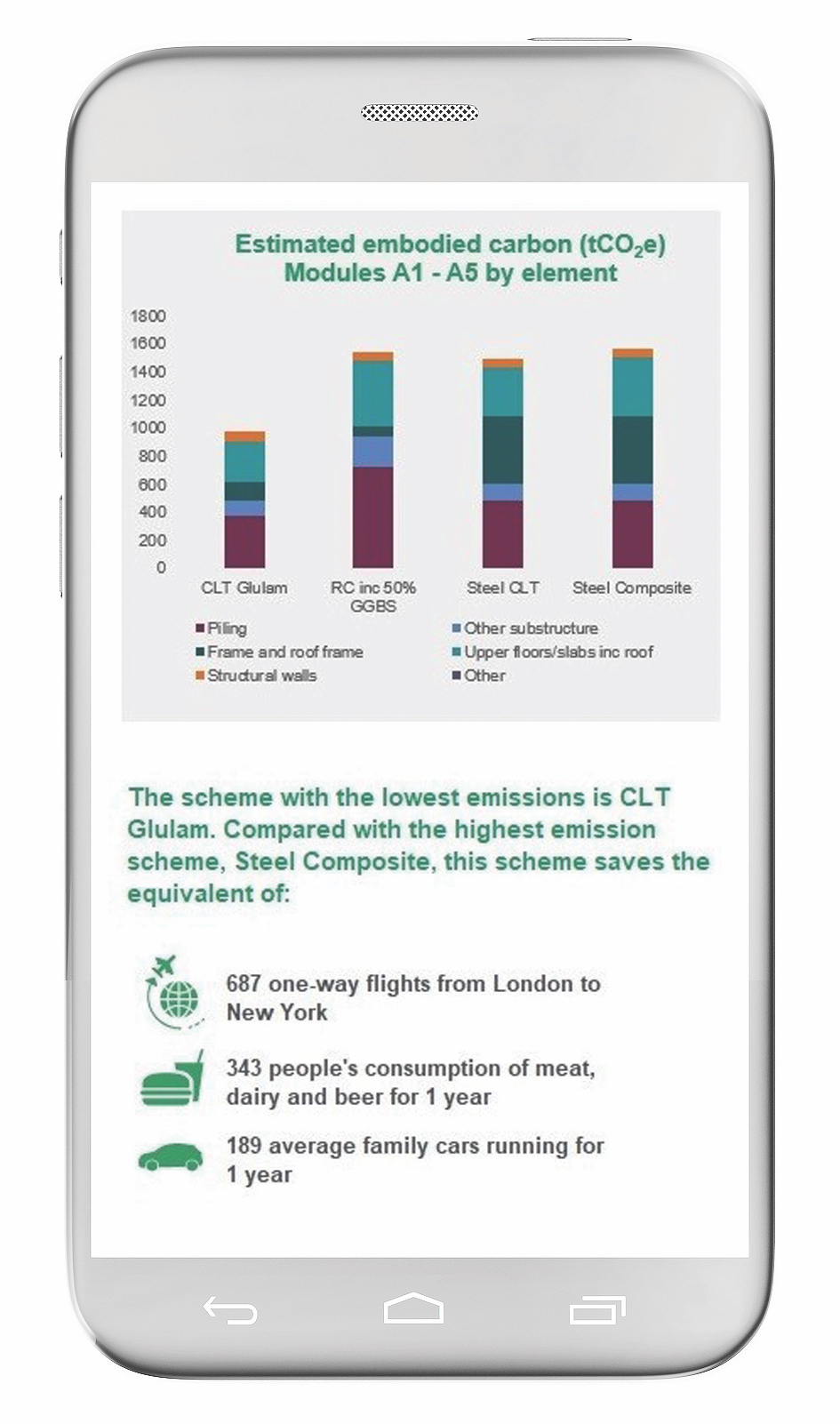
The IStructE calculator estimates embodied carbon for structural elements by material type and provides a real-world comparison of the savings
The user keys in the material specifications and the quantities; the tool then multiplies the quantities by the relevant carbon factors and outputs a raft of information designed for the user to understand where carbon hotspots are in a project and target those hotspots for alternative approaches either in design or material specification to help reduce the carbon. This includes the Structural Carbon Rating Scheme (SCORS).
The tool’s output includes an ‘equivalence’ function that generates a simple real-world comparison for how much carbon is embodied in a project – for example, its carbon could be equivalent to 1,400 one-way flights from London to New York.
Arnold says: “It’s quite important that we try to retain an aspect to this tool that enables the engineer to speak to the client in terms that they understand.
Defining embodied carbon in construction
The UK Green Building Council defines embodied carbon thus: “Embodied carbon is the total greenhouse gas emissions (often simplified to ‘carbon’) generated to produce a built asset. This includes emissions caused by extraction, manufacture/processing, transportation and assembly of every product and element. In some cases (depending on the boundary of an assessment), it may also include the maintenance, replacement, deconstruction, disposal and end-of-life aspects of the materials and systems that make up the asset. It excludes operational emissions of the asset.”
“It’s always worth bringing it home and highlighting to the client that if they pick option A instead of option B, it’s the equivalent emissions of 1,000 cars being driven around the UK for a year or whatever.”
Arnold notes that the UN-affiliated Global Status Report For Buildings And Construction reported the manufacturing, transport and installation of structural materials accounted for 10% of energy-related CO2 emissions in 2019. In a call to the wider industry, he adds: “The industry lacks data on the carbon emissions from site activities, such as the use of plant and equipment. We would love to hear from contractors who are collecting such data on site.”
Balfour’s 14% saving
Balfour Beatty is set to roll out a carbon calculator after initial tests showed potential embodied carbon savings of up to 14% achieved through better-informed design choices.
Currently in its beta testing phase on four Balfour sites, the AutoBIM Carbon Calculator automatically links BIM data to embodied carbon data from the Inventory of Carbon and Energy database, an online source that provides energy and embodied carbon information for construction materials.
In addition, the calculator also allows users to input information from environmental product declarations sheets, verified and registered documents that provide transparent and comparable data about the environmental impact throughout the life cycle of a product or material.
Following a phased rollout across Balfour Beatty’s projects over the next four months, the AutoBIM Carbon Calculator will be available to the wider industry within the next 12 months, with plans to expand the remit of the calculator to measure the energy performance of products and materials post completion.
The calculator was developed by Balfour in collaboration with Innovate UK, Leeds Beckett University, Hertfordshire University and White Frog Publishing.
Costain and Winvic learn from the past
Costain and Winvic are helping the University of the West of England (UWE Bristol) to develop artificial intelligence (AI) and machine learning technology to combat embodied carbon.
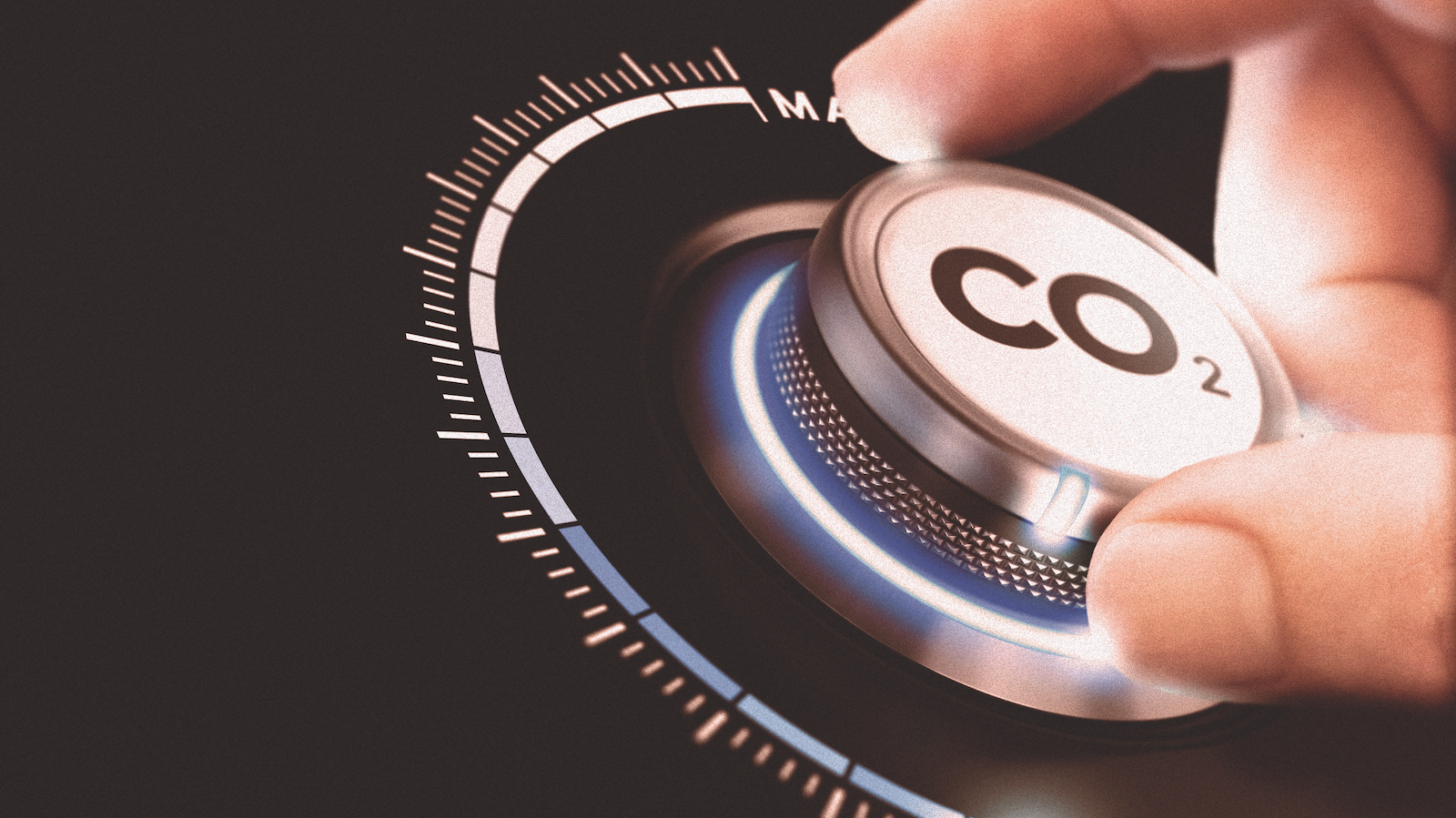
UWE Bristol’s Big Data Laboratory is leading the two-year, £800,000 project with funding from Innovate UK. The project team is completed by Edgetrix, which specialises in cloud and AI solutions. Determining which low-carbon materials to use on a project can be time-consuming: the new software will use machine learning to make that calculation and save time, UWE Bristol claims.
Dr Lukman Akanbi at UWE Bristol, who is leading the project, which started late last year, says: “We are going to collect embodied carbon data from previous projects, and machine learning models will be developed to learn the patterns from this data. The system will then be able to come up with alternative materials quicker.
“For a large-scale project for example, instead of taking five to 10 hours to work out alternatives, it could initially take only one to two hours, and further down the road, once more data is gathered, just a few minutes.”