Retrofitting steel-framed buildings with intumescent coatings must follow strict standards. CM reports
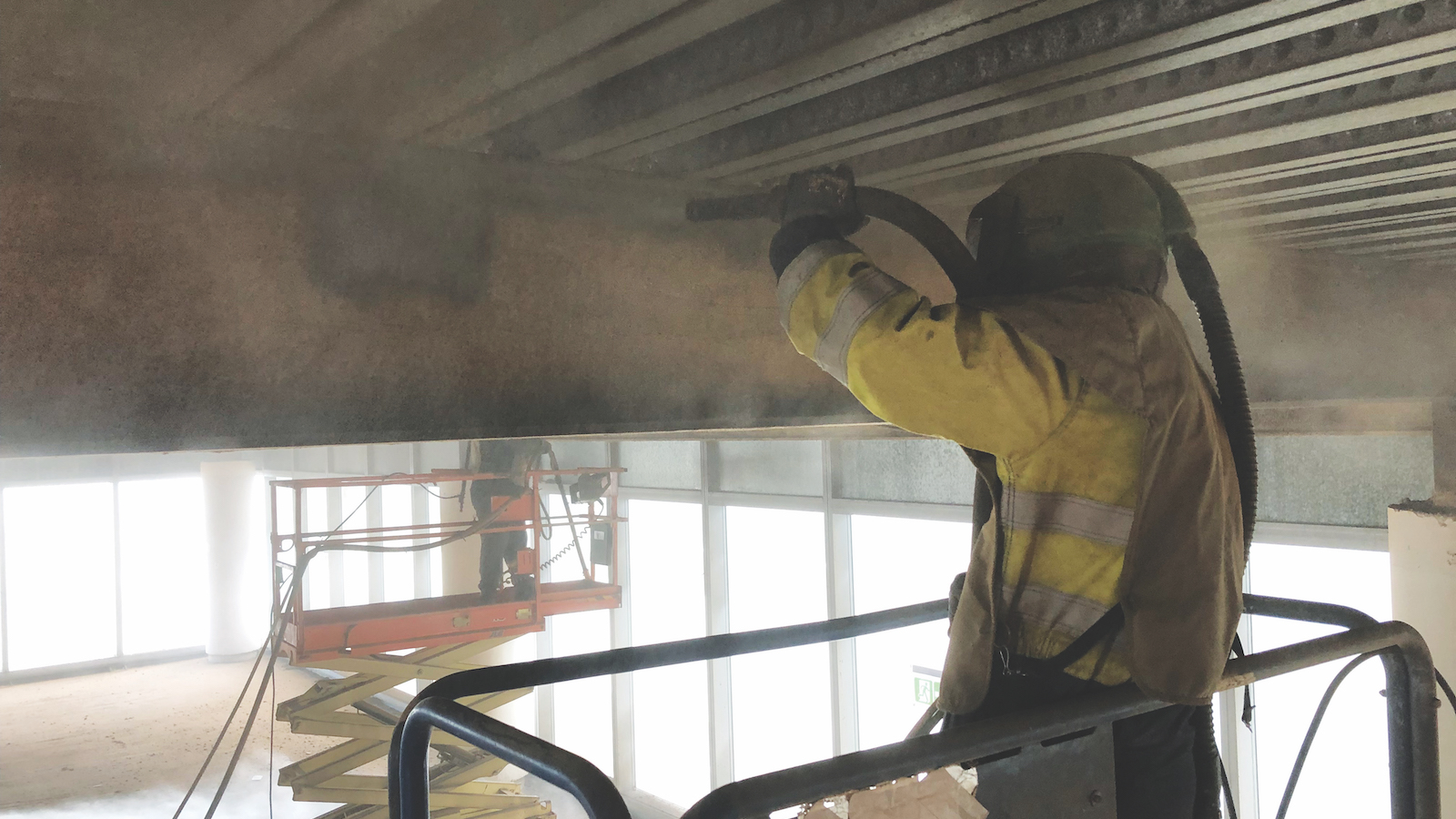
25 North Colonnade is a commercial office in London’s Docklands, built in 1991. In 2018, ISG was awarded the £70m contract to refurbish the 15-storey building. Its makeover features exposed soffits and internal steel columns and beams for a 21st century minimalist interior.
The challenge for LDD Construction, the contractor responsible for the fire protection package, was to make sure the exposed steel structures would be adequately fireproofed.
Exposed steel has to be protected with intumescent paint and must be thoroughly prepared beforehand. There are no shortcuts; if the steel surfaces are not prepared to the required Sa2.5 level (under ISO 8501-1:1988 – Preparation of steel substrates before application of paints and related products) the paint manufacturers will not guarantee the performance of their product.
“At 25 North Colonnade, we needed 80 tonnes of grit, which arrived on pallets at basement level, then had to be transported through the building to the blast floor”
LDD brought in blast-cleaning specialist VariBlast to remove cementitious coating remnants and mill scale from the steel structures, blast-cleaning 21,000 sq m of internal structural steelwork to a surface preparation level of Sa2.5.
“Our first thought is the logistics: moving specialist equipment, materials and waste safely, possibly in a building that was partly occupied,” explains VariBlast managing director Warren Farrow. “At 25 North Colonnade, we needed 80 tonnes of grit, which arrived on pallets at basement level, then had be transported through the building to the blast floor. Once used, the grit had to be swept up, and then collected and removed from site in skips.”
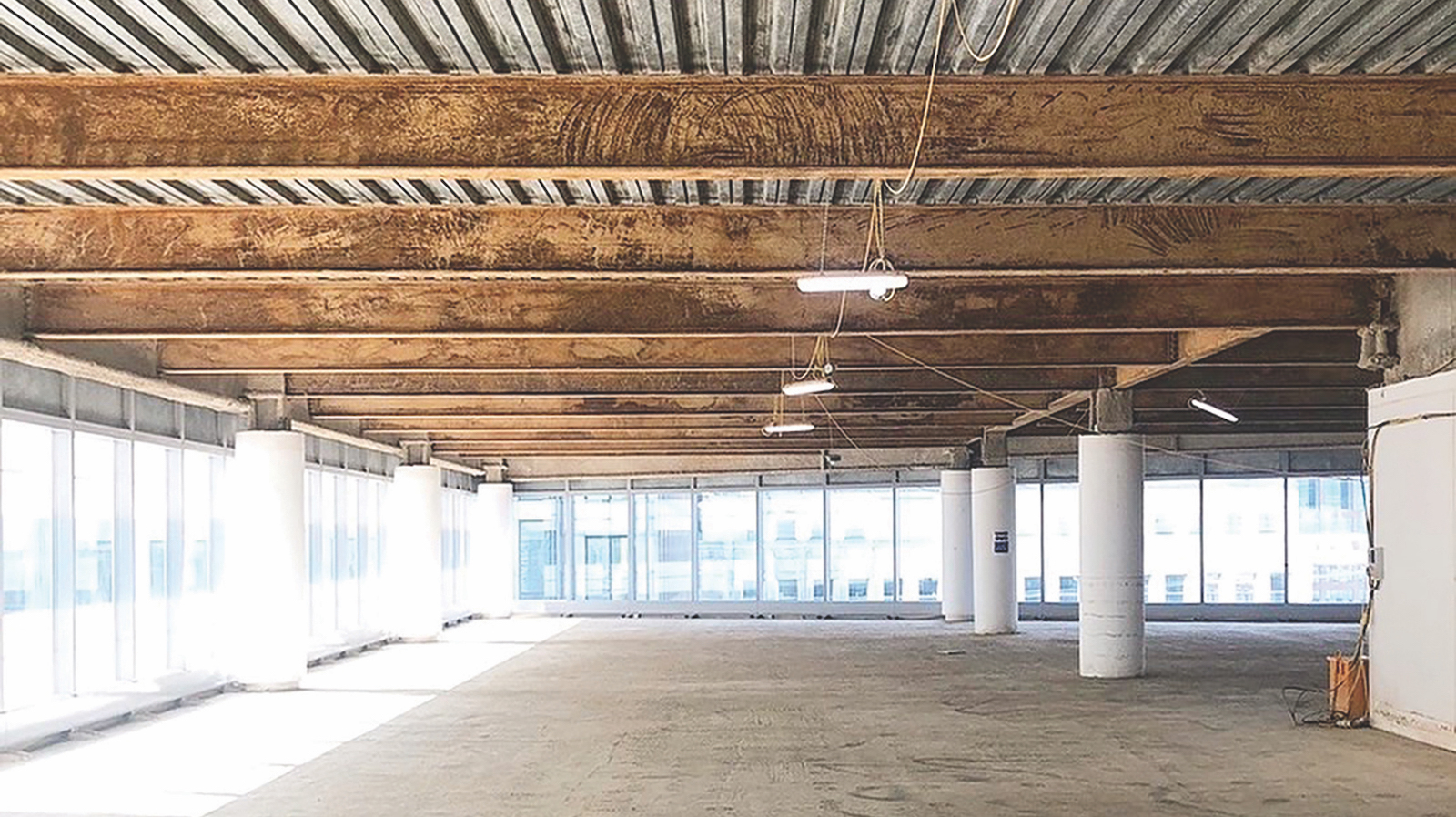
Containing and controlling dust is a necessary part of the work.
“Operatives are protected by supplying filtered air directly into their blast helmets, maintaining positive air pressure to ensure that dust cannot get through,” says Farrow. “This, together with disposable FFP3 masks, ensures even the finest particles are captured.
“We also have to protect others in the building. The area where we are working must be completely contained, which is best achieved by working solely on one floor of a building and denying access to other trades until our works are complete.”
Compressors tend to be noisy and as big as a medium-sized van, so they have to be sited on the ground floor or basement levels.
“Then, one-inch airlines are installed through dry risers to the floor we are working upon,” explains Farrow. “Usually, the compressors operate at 600 cfm, 170 psi – anything smaller would not be powerful enough when working throughout a multi-storey building.”
The timeframe for completion varies, depending how the steel was previously treated.
“If it is bare steel (typically found in older buildings), a single operative can blast-clean around 100 to 150 sq m a day to an Sa2.5 standard, when removing a coating of oxidisation caused by exposure to humidity over time,” Farrow says. “But if the steel is coated with a primer and topcoat or even a previous ‘out of specification’ fire protective coating, that slows the timeframe down to 40 or 50 sq m per blasting operative.”
Variblast finished its work in late 2019, with coatings applied shortly after. Final decoration and the general fit out are still ongoing.