The Digital Construction Awards attracted 170-plus entries this year, 85 of which have been shortlisted. Here, we detail the finalists for the Design Innovation award.
This category recognises the best use of digital technology and data to enhance the practical aspects of building and project design for successful delivery. This category is not focused on design aesthetics.
Six entries made the shortlist.
Bridgwater Tidal Barrier | AtkinsRéalis/Environment Agency
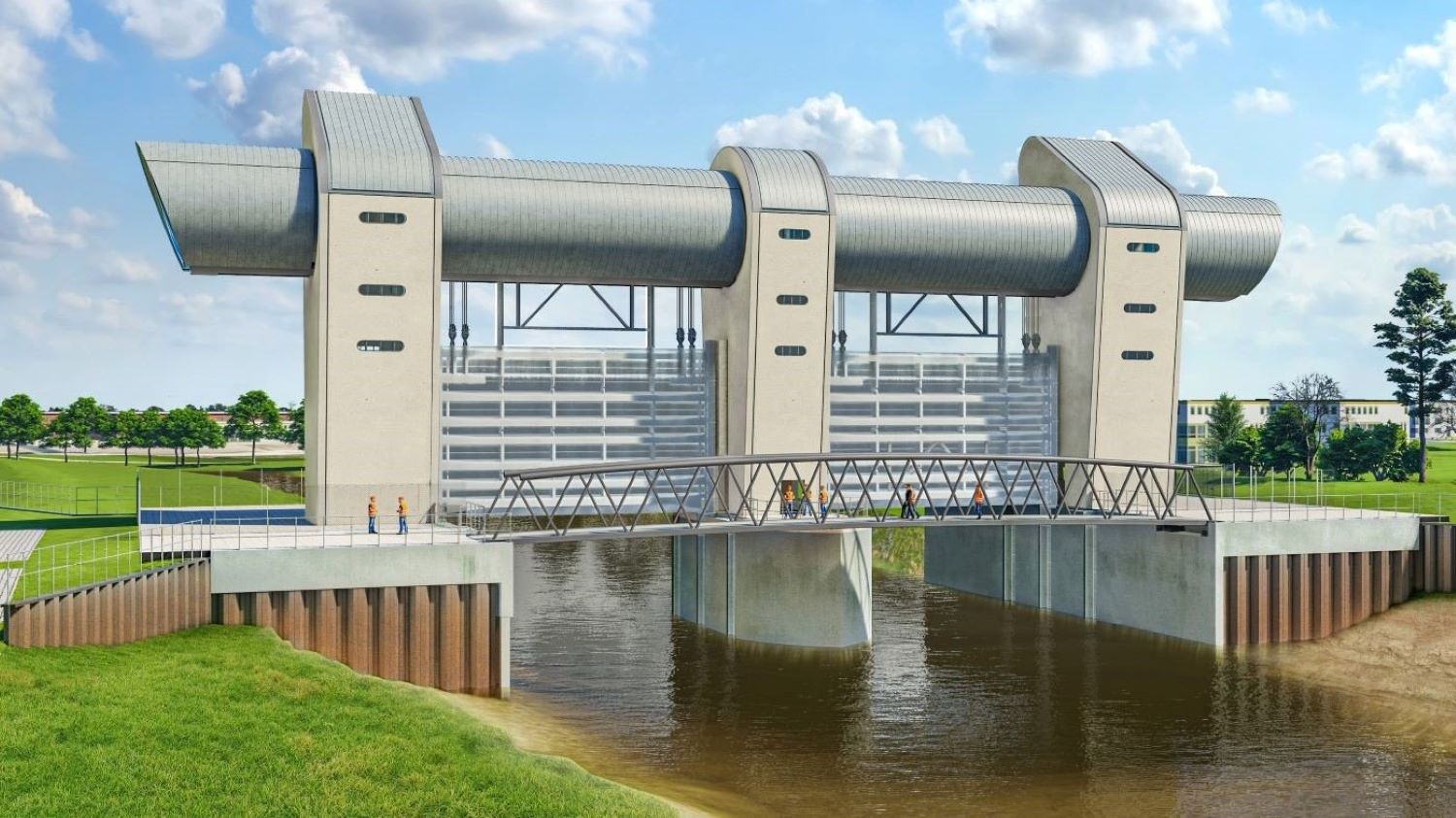
AtkinsRéalis has delivered a 53% reduction in embodied carbon on the Bridgwater Tidal Barrier, using a bespoke digital tool that tracks carbon in real-time during design. Commissioned by the Environment Agency, the scheme protects more than 11,300 homes and 1,500 businesses from flooding until 2125. But its sustainable design also sets a new precedent for carbon-conscious infrastructure.
A key challenge in infrastructure is the limited visibility of embodied carbon during design. Traditional calculators are time-intensive and typically used after critical decisions are locked in, limiting their influence. Funded by the Environment Agency’s Net Zero Innovation Pathway, AtkinsRéalis integrated the EA’s ERIC carbon calculator into its ‘BIM Analytics – Carbon’ platform, enabling live carbon analysis directly from the BIM model.
This digital tool generates a carbon dashboard and heatmap, pinpointing high-impact design elements. Designers could iteratively refine their choices, with immediate feedback on carbon consequences. One major change involved switching from steel-cased reinforced concrete piles to driven steel tubes for the barrier foundations, reducing carbon by more than 25% in that element alone. Other optimisations included a pre-cast solution for the barrier towers and a revised reinforced concrete apron slab.
Overall, the team were able to reduce embodied carbon for the tidal barrier by 53% against the baseline, with a 70% reduction in the impact of carbon critical elements. The tool is now being rolled out on other EA projects.
This approach not only achieved substantial emissions reductions during early-stage design, but also offers a scalable digital solution for future low-carbon infrastructure projects across the UK.
Complex Data Centre Campus | McLaren Construction/Solibri
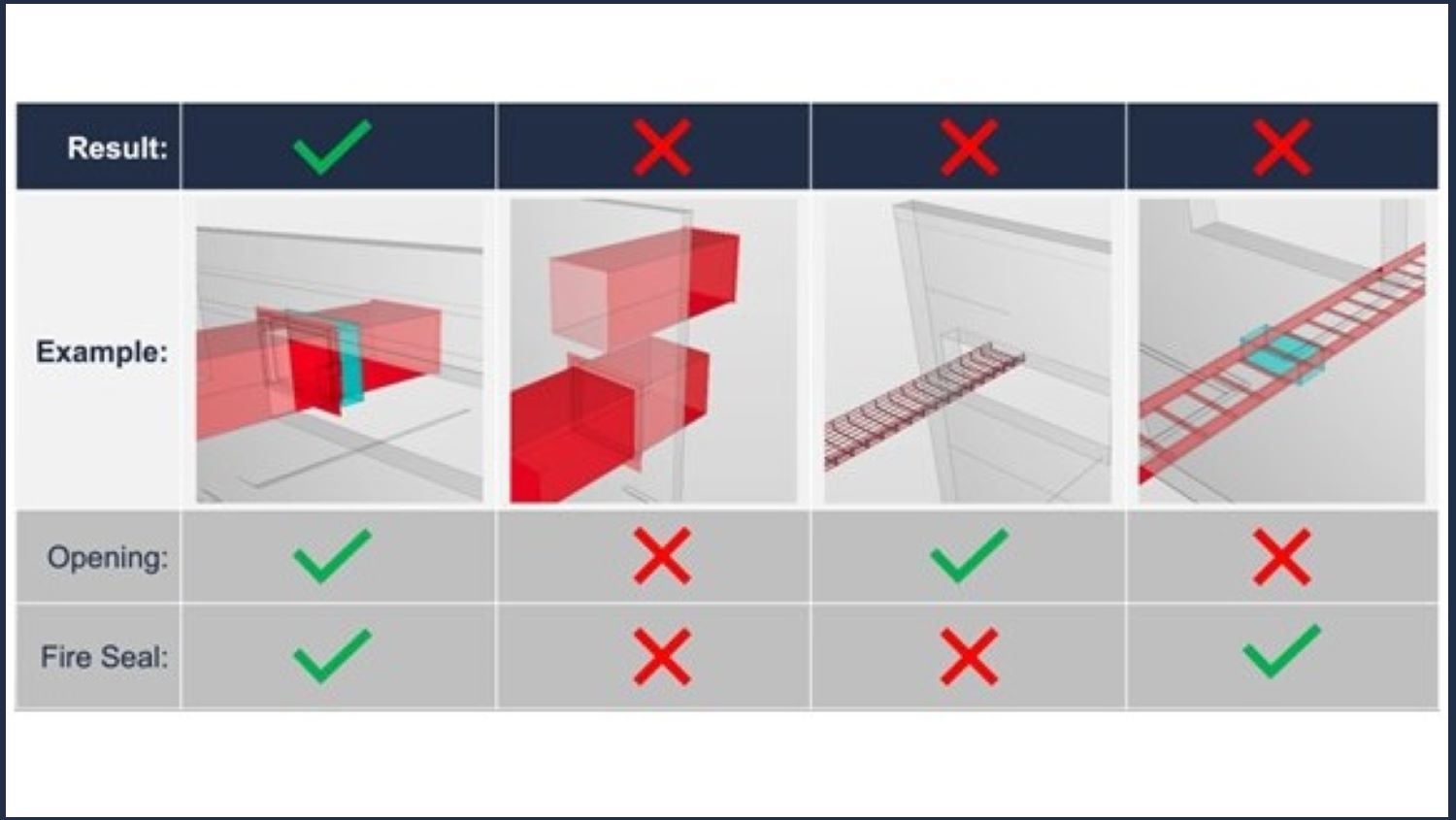
Faced with the complexity of coordinating design across disciplines for its largest project to date – a data centre campus under a pre-construction services agreement (PCSA) – McLaren sought to overhaul its inefficient and manual design processes. Challenges included managing more than 600 individually maintained clash rules, lack of digital support for firestopping compliance, subcontractor scope gaps (notably drylining), and reliance on 2D drawings for design updates.
To address these, McLaren expanded its use of Solibri, because the software supports openBIM standards and offers customisable rulesets. Key innovations included deploying Solibri’s new Design Coordination Matrix rule, which replaced hundreds of discrete clash rules with a flexible matrix structure. This improved clarity, reduced manual work, and made tolerances easier to adjust. Fortnightly technical sessions with Solibri’s development team helped resolve early adoption issues and led to customised software builds.
To enhance design compliance, McLaren implemented the BIM Coordination+ extension, specifically introducing 3D firestopping checks – an area previously managed manually in 2D. Custom rules identified issues such as missing fire seals and service clashes. For drylining gaps, a stud opening clash rule simulated stud mass and position, enabling early detection of conflicts. Model comparison rules also improved the accuracy and speed of tracking design changes.
The outcome is a streamlined, template-based coordination process that has reshaped McLaren’s workflows. Enhanced fire safety coordination supports compliance with the Building Safety Act. The federated Solibri model, improved internal communication, and early stakeholder reporting have exceeded client expectations and now inform McLaren’s digital strategy across future projects, with industry-wide benefits from continued collaboration with Solibri.
Enhancing Facade Design with GRETA: A Parametric Approach to Daily Challenges | WSP
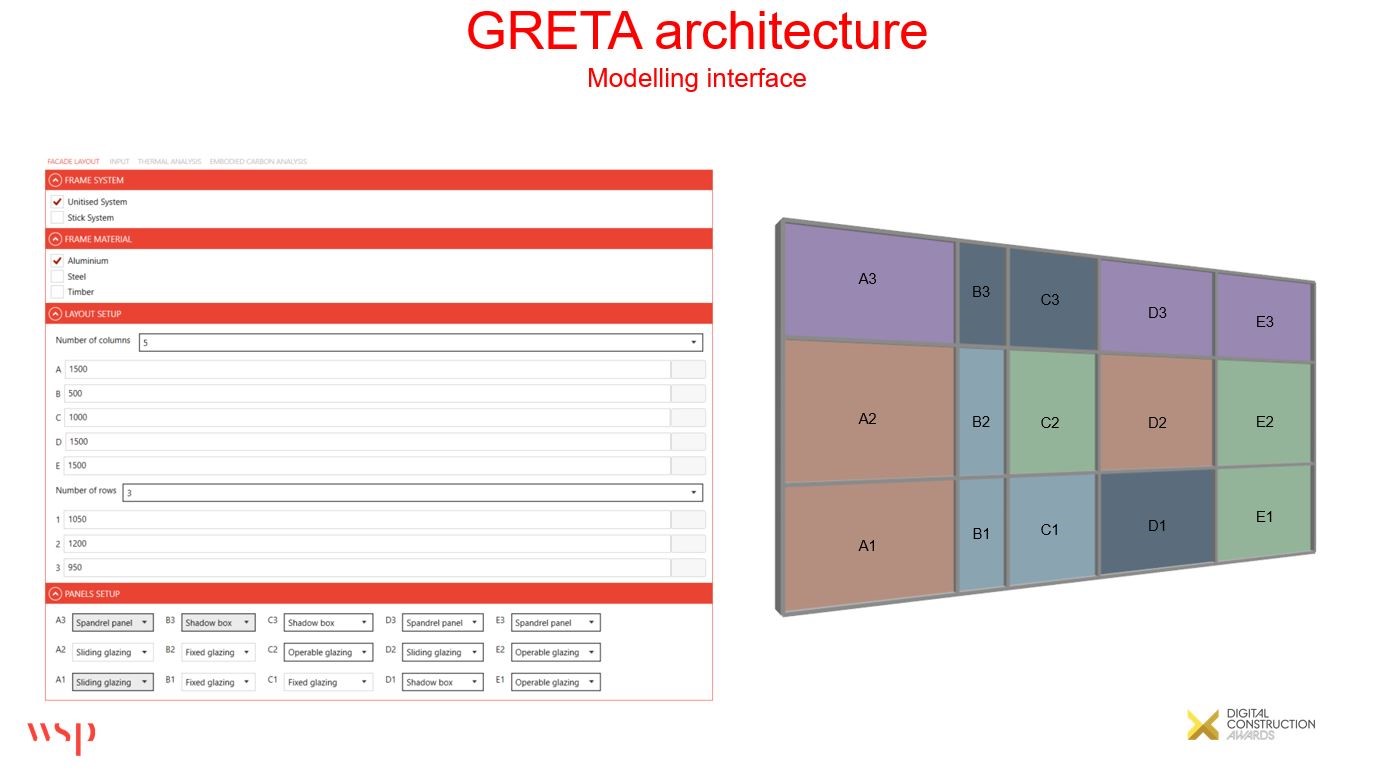
As facade systems become more architecturally ambitious, their complexity introduces technical, performance and coordination challenges. Early-stage analysis is essential to avoid premature design choices that restrict procurement and design flexibility. But existing tools, often spreadsheet-based, are labour-intensive, error-prone and not scalable.
After extensive market and literature research, WSP developed GRETA in-house to address the gap: a parametric, independent facade design tool that enables flexible optioneering without tying decisions to suppliers too early.
Built in Grasshopper and integrated with Rhino, GRETA automates facade analysis using a scalable database of validated performance archetypes. Unlike conventional workflows, it dynamically models facade geometries and discretises bays, even across complex designs. Its HumanUI interface allows non-parametric users to perform real-time assessments without advanced training.
GRETA unifies multiple simulations – including thermal performance, embodied carbon and structural analysis – within a single platform, avoiding time-consuming tool switching and manual recalculations.
GRETA’s impact has been significant for WSP. Across recent central London projects, it reduced the time required for thermal analysis of typical facade bays by up to 85% against traditional methods, freeing up resources for more in-depth analysis. The system’s flexibility also de-risks procurement, enabling decisions based on performance rather than manufacturer constraints. It has streamlined workflows, enhanced design quality, and fostered parametric engagement across wider teams.
GRETA’s scalable, product-agnostic approach has reshaped the facade design process for WSP – boosting precision, creativity and sustainability – while setting a new standard for digital innovation in early-stage design.
Prefabricated partitions on high-rise residential projects | KOPE AI/Saint-Gobain Intewall
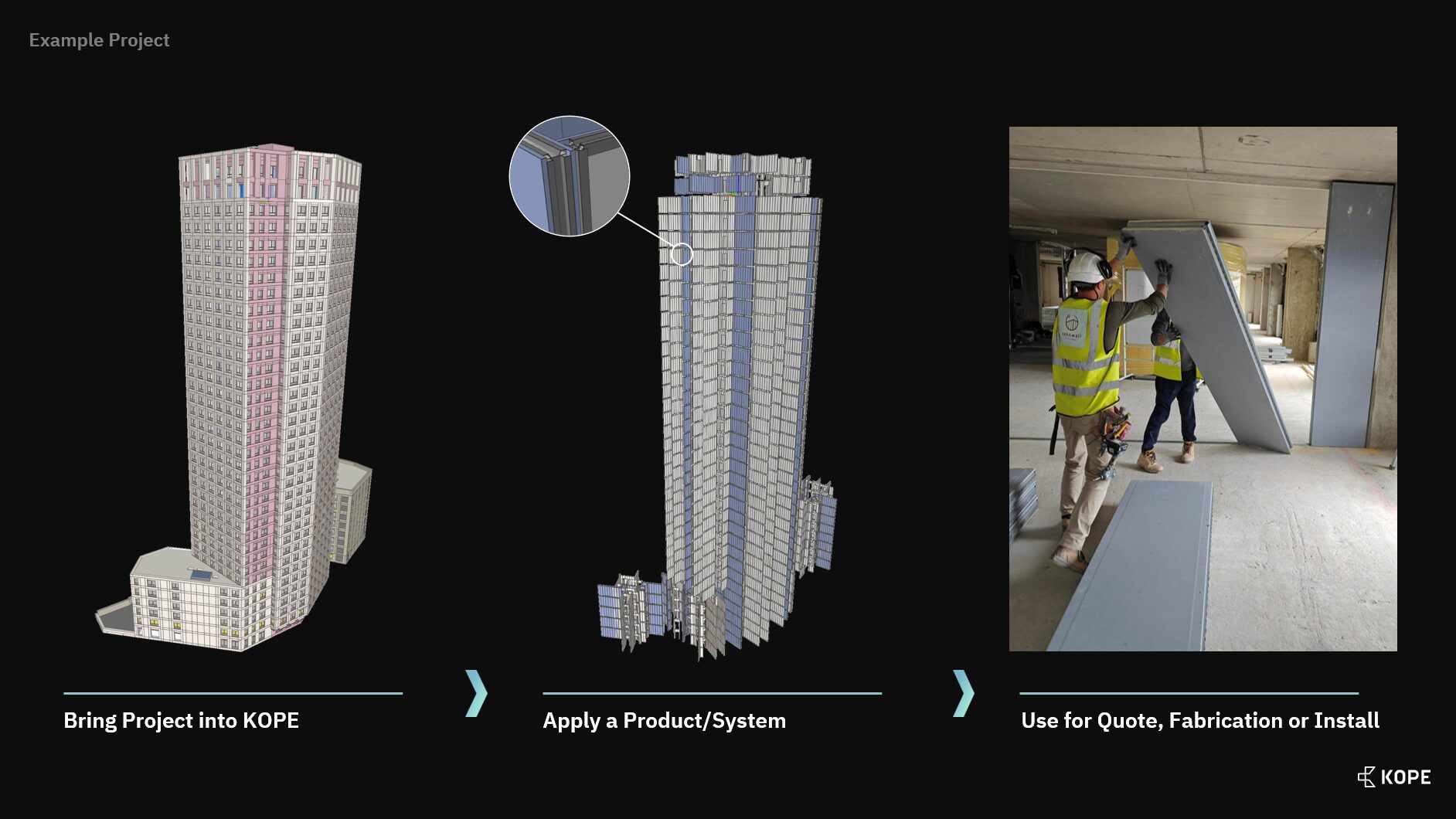
Saint-Gobain and KOPE partnered to tackle a longstanding inefficiency in adopting prefabricated partition systems in construction. Traditional feasibility assessments for systems like Saint-Gobain’s InteWall were slow, resource-heavy and required days of manual work per floor. As a result, prefabricated options were often sidelined during later-stage design phases, leading to higher costs, bespoke manufacturing, and increased project risk.
To address this, KOPE developed a cloud-based product configuration platform that digitally encodes InteWall’s manufacturing constraints, installation rules and tolerances. Integrated with BIM design files, the platform allows rapid, automated placement of prefabricated panels. On a 50-storey residential scheme, KOPE’s tool configured more than 30,000 panels in four minutes – work that would traditionally span weeks.
The innovation lies in KOPE’s AI-powered optimisation engine, which simulates thousands of panel permutations. It recommends subtle adjustments, such as shifting door and service penetrations by ±25mm, boosting standardisation by 36%. This digital feedback loop ensures real-world manufacturability, enabling offsite solutions without major redesigns.
The solution delivered transformative outcomes. Assessment times fell from days to minutes. Standardisation improvements reduced bespoke components, cutting production costs and onsite waste by up to 92%. Faster, clearer decision-making also improved collaboration between stakeholders.
This scalable digital innovation sets a new precedent for prefabrication in mainstream construction. By integrating design with manufacturing logic, KOPE and Saint-Gobain have unlocked significant sustainability gains and productivity improvements, redefining how partition systems are evaluated and deployed.
RESTOR: Reuse of structural steel in construction | Chetwoods Architects/University of Cambridge/University of Birmingham
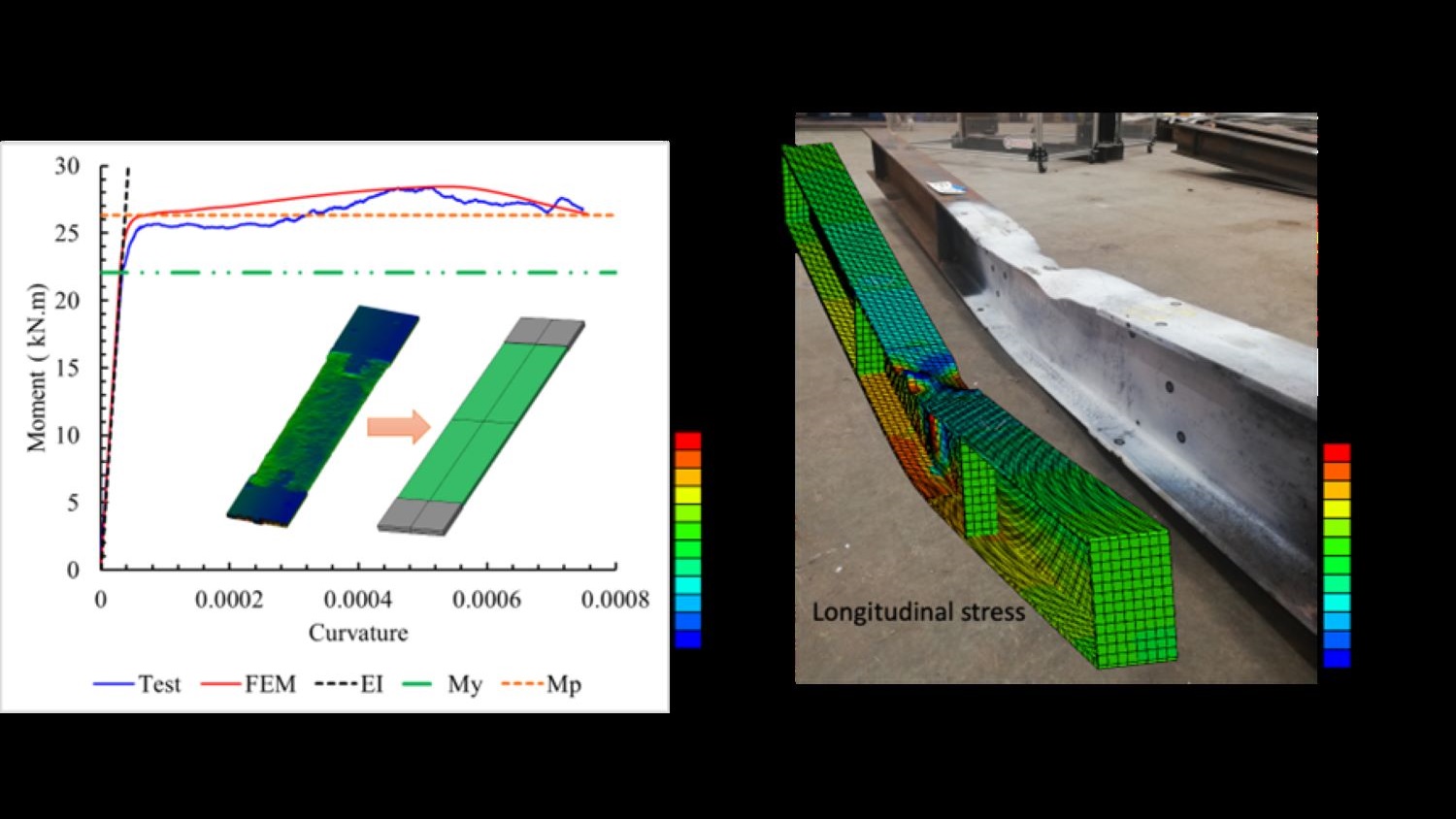
Only 15% of the UK’s structural steel is currently reused, with the remainder recycled at high energy cost – contributing to steel’s position as one of the largest industrial carbon emitters. The RESTOR project, led by the University of Birmingham and the University of Cambridge, with Chetwoods Architects acting as sector adviser, set out to embed circular economy principles into the construction industry by addressing barriers to largescale steel reuse.
RESTOR integrates non-destructive testing (NDT), machine learning and BIM into a web-based generative design tool. This tool enables engineers to assess used steel members, predict their performance, and embed them into new projects from the outset. Scanning and 3D modelling generate digital twins of steel elements, allowing precise structural evaluations and configuration into new building designs.
The parametric interface serves as a dynamic warehouse, linking existing steel members to viable structural roles in new designs. The tool’s machine learning engine streamlines this matchmaking process by optimising reuse scenarios based on steel properties, geometry and project requirements.
Used on live projects with architects Chetwoods and supplier Cleveland Steel, RESTOR has demonstrated the ability to raise steel reuse from 15% to a projected 50%. The approach cuts embodied carbon, trims procurement costs, and aligns with UK net-zero targets.
RESTOR’s generative design tool brings together contractors, designers and suppliers in real-time, embedding reuse into the design process and proving that circular construction can be both scalable and economically viable.
Transpennine Route Upgrade East | Systra/Network Rail/TRU East Alliance
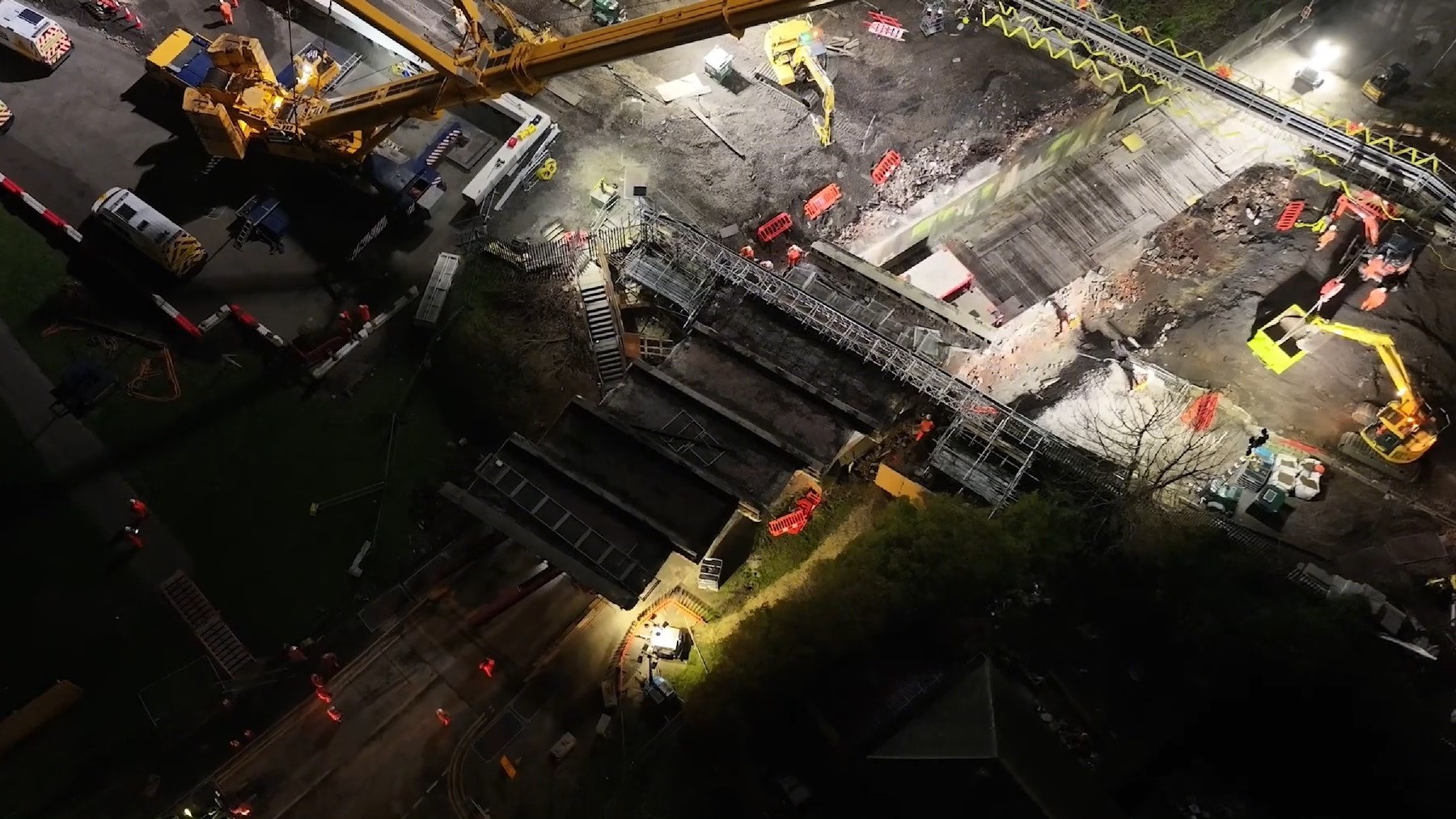
The Osmondthorpe Lane bridge reconstruction project set out to transform safety and wellbeing standards in complex construction environments. With multiple stakeholders, tight deadlines, and extensive public interface, the TRU East Alliance (Network Rail, J Murphy & Sons, Siemens, Systra and Volker Rail) identified a need for a proactive, digitally-enabled approach to health and safety. Traditional static risk assessments were insufficient for managing the dynamic risks posed by largescale infrastructure projects.
The team adopted Bentley Systems‘ 4D Synchro platform, integrating real-time scheduling with 3D models to simulate construction sequences and identify safety hazards in advance. This 4D visualisation tool enabled the team to foresee risks – including machinery clashes, ergonomics issues and pedestrian interfaces – and plan accordingly, improving workflows and reducing physical strain on workers.
Crucially, virtual site walk-throughs empowered both digitally literate and non-specialist stakeholders to explore the model, identify risks and adjust plans in real-time. Challenges around usability and data accuracy were addressed through iterative design and validation with safety experts, digital engineers and site teams. The result was a user-friendly, high-fidelity simulation environment tailored for practical decision-making.
The benefits were clear and measurable: a notable reduction in RIDDOR-reportable incidents compared with similar projects, improved worker engagement and communication, and enhanced onsite efficiency. The digital-first approach also accelerated delivery, ensuring the bridge was completed ahead of programme and within budget.
By embedding 4D modelling into safety planning, the project set a new benchmark for integrating health, safety, and wellbeing into digital construction.
Celebrate with the best
The winners will be revealed at the gala dinner on 1 July at the Brewery in London.
You can join the shortlisted entrants by booking your seats at the awards.
The Digital Construction Awards are organised by Digital Construction Week, Construction Management and the Chartered Institute of Building. The first sponsor to be announced is Bluebeam.
To find out more about the Awards, visit digitalconstructionawards.co.uk.
Generative artificial intelligence was used to help with the creation of this article. All content in the article was sourced, checked and verified by our editorial team before publication.