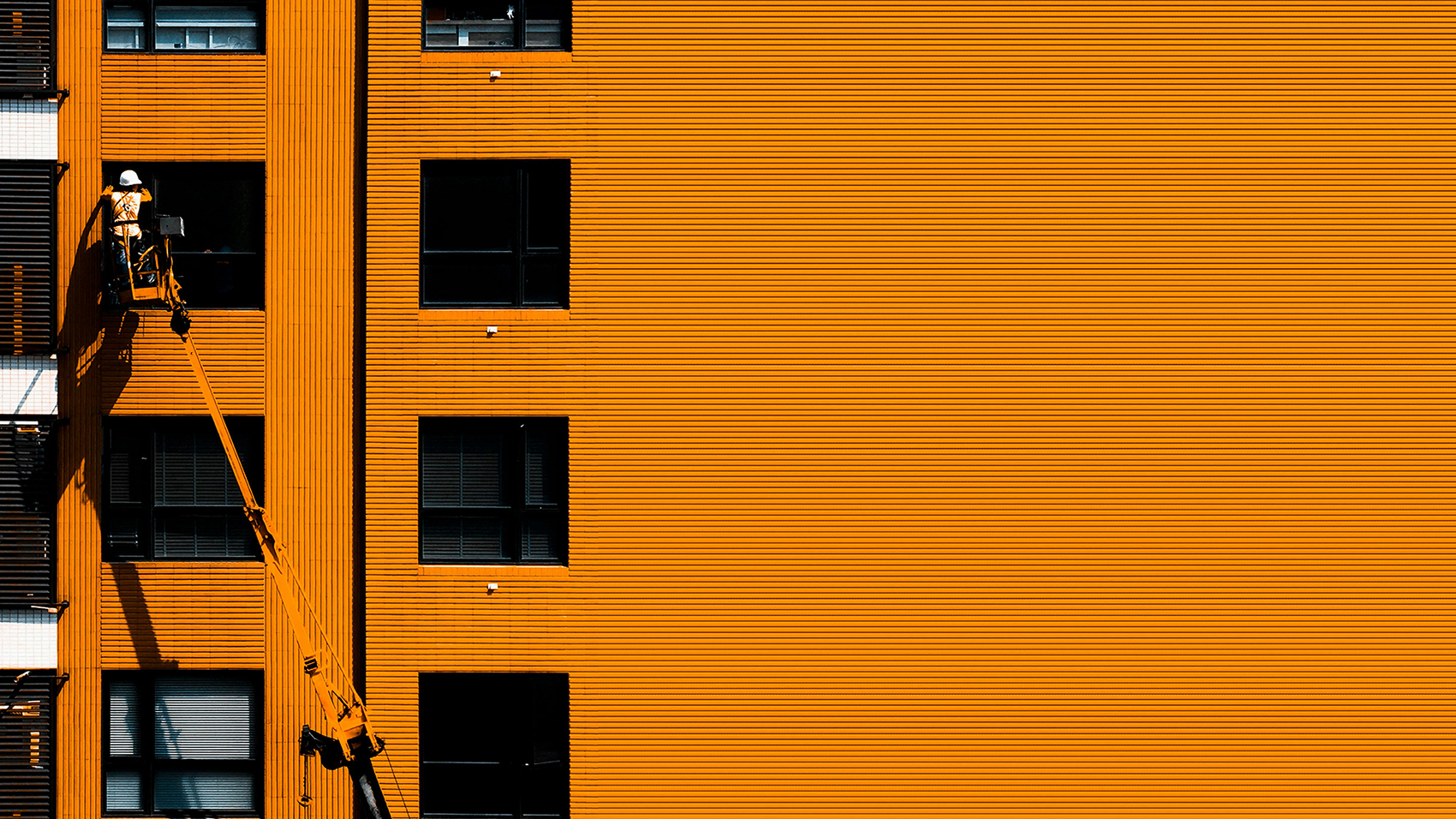
In this CPD, Anthony Walker provides an overview of the key aspects of lifecycle surveys for the assessment of a building’s condition.
“When we build, let us think that we build forever. Let it not be for present delight nor for present use alone.” John Ruskin, The Seven Lamps of Architecture, 1849
This quote from John Ruskin, a prominent 19th-century English art critic and architectural thinker, underscores the enduring nature of buildings and our responsibility to maintain them for future generations.
This philosophy is central to planned preventative maintenance (PPM) building surveys, which aim to safeguard our built environment for years to come.
What are PPM building surveys?
PPM building surveys, also known as lifecycle surveys, involve comprehensive assessments of a building’s condition, encompassing both the fabric and mechanical and electrical (M&E) elements.
These surveys are designed to identify potential issues before they escalate, enabling proactive maintenance and repairs that maximise the asset’s lifespan. Additionally, they assist in formulating investment strategies that outline necessary works, indicative costs and timing for repairs or replacements.
PPM building surveys serve three primary purposes:
- Budgeting and cost management By identifying maintenance needs in advance, property owners and managers can allocate budgets effectively, preventing unexpected financial burdens from sudden repairs. This proactive approach can lead to significant cost savings over the building’s lifecycle.
- Operational efficiency Regular maintenance ensures that building facilities remain functional, minimising disruptions that could affect business operations. This is particularly critical for commercial properties, where downtime can result in substantial financial losses.
- Asset longevity PPM surveys extend the lifespan of building components by addressing wear and tear before significant failures occur. This not only preserves property value but also promotes sustainability by reducing the need for premature replacements.
Frequency and timeframes
PPM building surveys are typically conducted every five years (quinquennially), although the optimal frequency may vary based on several factors, including:
- Building age Older buildings may necessitate more frequent surveys due to ageing infrastructure and materials.
- Building type Different types of buildings (e.g. schools, hospitals and warehouses) have varying maintenance needs.
- Usage intensity Buildings with high foot traffic or intensive use may require more frequent assessments.
- Environmental conditions Structures in harsh climates or polluted areas may need more regular inspections.
- Construction method Certain building types, such as those with 1950s-1970s prefabricated concrete panels, and reinforced autoclaved aerated concrete (RAAC) may deteriorate more quickly and require more frequent surveys.
Best practice suggests that PPM building surveys should typically cover a five-year timeframe to enable owners and managers to plan maintenance activities and budgets accordingly. In some instances, the timeframe may extend to 30 years, particularly for private finance initiative (PFI) buildings, up until the end of the contract period.
Case study: Mander Shopping Centre
In 2017, a pedestrian was struck and killed by a wooden panel outside a shopping centre in Wolverhampton during Storm Doris. At the inquest, it was highlighted that the plant room on the building’s roof may not have been maintained for nearly two decades.
Cushman and Wakefield Debenham Tie Leung Limited was responsible for managing it for the five years leading up to 2017 and were fined £1.3m in 2019 for health and safety breaches and also fined by RICS for bringing the profession into disrepute.
The case prompted RICS to review its guidance on PPM building surveys.
It is important to note that predictions beyond five years become increasingly challenging due to variations in building usage and maintenance.
Data recording
The structure of the PPM survey data can vary depending on the building surveyed and its use. However, some common elements include:
Data structure
The high-level common building data structure would include:
- Roofs
- Structure
- Facades
- Internal
- External areas
- Building Services
Many PPM surveys adopt the data structure set out in the RICS new rules of measurement (NRM3), which provides a standard for cost estimating and planning for building maintenance works and contains a group element, element, sub elemental and component structure.
NRM 3 is the preferred structure for surveys carried out on PFI buildings and will be required for buildings handed back at the expiry of the contract. It includes the following items:
Condition rating
A 4-grade structure is typically used when carrying out PPM building surveys to record the condition of construction elements, sub-elements, components and services. Each grade typically has an expression and description (see table below).
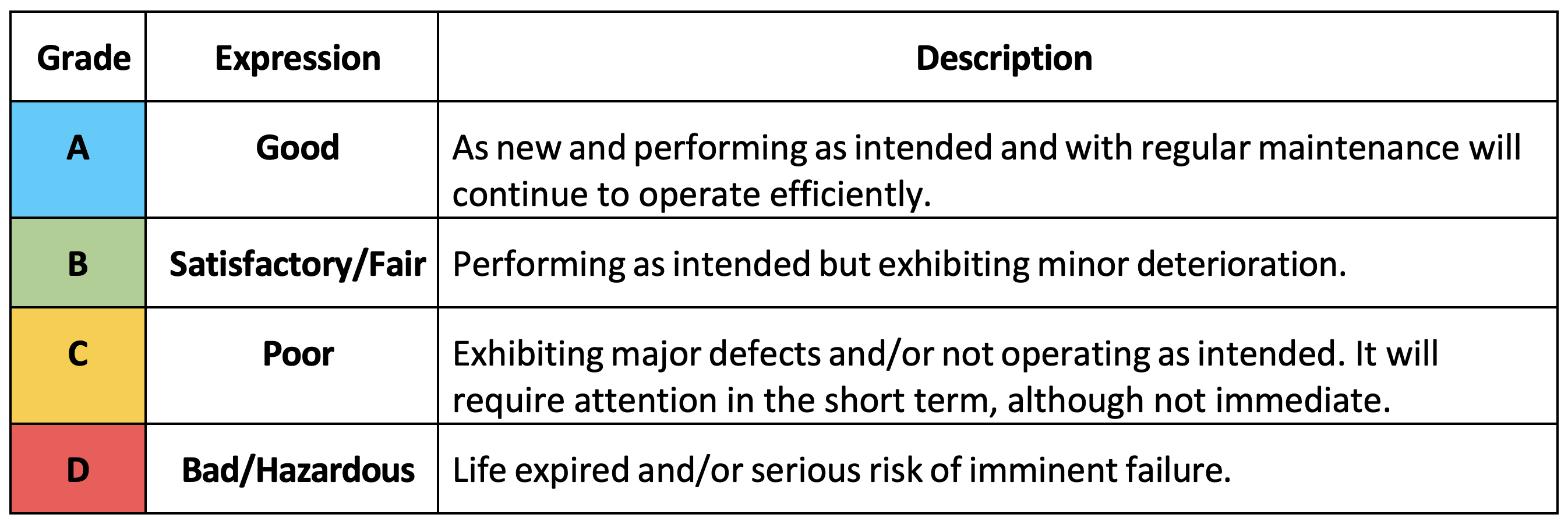
A variant of the above condition rating is the NHS Estate Code, which is A to Dx, breaking the condition down in more detail with three additional grades:
- B(C)+ – currently as B but will fall below B within five years
- CX and DX – X is added as supplementary to C or D to indicate that it is impossible to improve without replacement
The decision to use A to D, or A to Dx is made by the client. PFI building surveys typically – but not always, require A to Dx.
Case study: The Wildfowl and Wetlands Trust
In early 2022, a new Head of Property was appointed at conservation charity Wildfowl and Wetlands Trust (WWT), who promptly began developing a property strategy to ensure the effective management and maintenance of all WWT buildings.
The strategy aimed to maximise the impact of future investments. WWT engaged multi-disciplinary surveying consultancy Sircle to conduct five-year PPM surveys across their entire property portfolio.
The survey results, delivered through PDF reports, Excel spreadsheets and Power BI dashboards, enabled WWT to make evidence-based decisions on cost-effective repairs, replacements, and maintenance strategies for the future.
Residual life
This indicates the estimated remaining lifespan of a building element, sub-element, component, or the services before they need replacing based upon a visual observation while on site. For example, if carpet tiles were life expired, the residual life would be 0 years. If recently installed, it might be 15 years, depending on the carpet tile. The actual life is linked to various factors including use and maintenance, so any figures stated are purely estimates.
Component lifecycle
This indicates the full life of a component from new. For instance, a new carpet tile might have a 15-year lifecycle. As with residual life, the actual life is linked to various factors, especially intensity of use.
Indicative costs
These are typically based on repairing or replacing and uplifting to a condition grade A and calculated using a cost database such as the Building Cost Information Service or Spons. They are also exclusive of routine maintenance and servicing costs and of any further investigation or specialist tests
Collectively, the above generates a planned preventative maintenance schedule, typically provided as an Excel spreadsheet.
The survey process
The PPM building survey process involves the following steps:
- Pre-survey planning Reviewing existing documentation like previous survey reports, maintenance records, and building plans.
- Site survey Conducting a thorough inspection of the building’s interior and exterior to capture building condition data, pictures, and measurements. Any immediate health and safety issues are reported to the client on-site.
- Post-survey quality assurance Cross-checking the survey data to review its quality.
- Reporting Finalising survey outputs, including reports in PDF format, Excel spreadsheets and potentially Power BI dashboards.
- Issue survey outputs Delivering final reports to the client.
Common challenges
Some of the main challenges to PPM building surveys and their solutions include:
- Access and safety concerns: Surveying certain areas, such as rooftops, plant rooms, or confined spaces can be difficult and hazardous.
Solution: Attempts to access all areas must be requested and made. If access is not gained, this must be communicated to the property owner/manager and set out in the report.
- Data management: Analysing the vast amounts of data generated by PPM surveys can be overwhelming, particularly for large or complex buildings.
Solution: Utilise data visualisation tools such as Microsoft Power BI to provide valuable data insights quickly and efficiently. Its advanced analytics capabilities, customisable dashboards and collaboration features allow for more informed decision-making on improved maintenance strategies and future investment. Power BI’s scalability and ability to automate data processing significantly reduces the time and resources required for handling large volumes of survey data, making it an effective tool for organisations dealing with building portfolios.
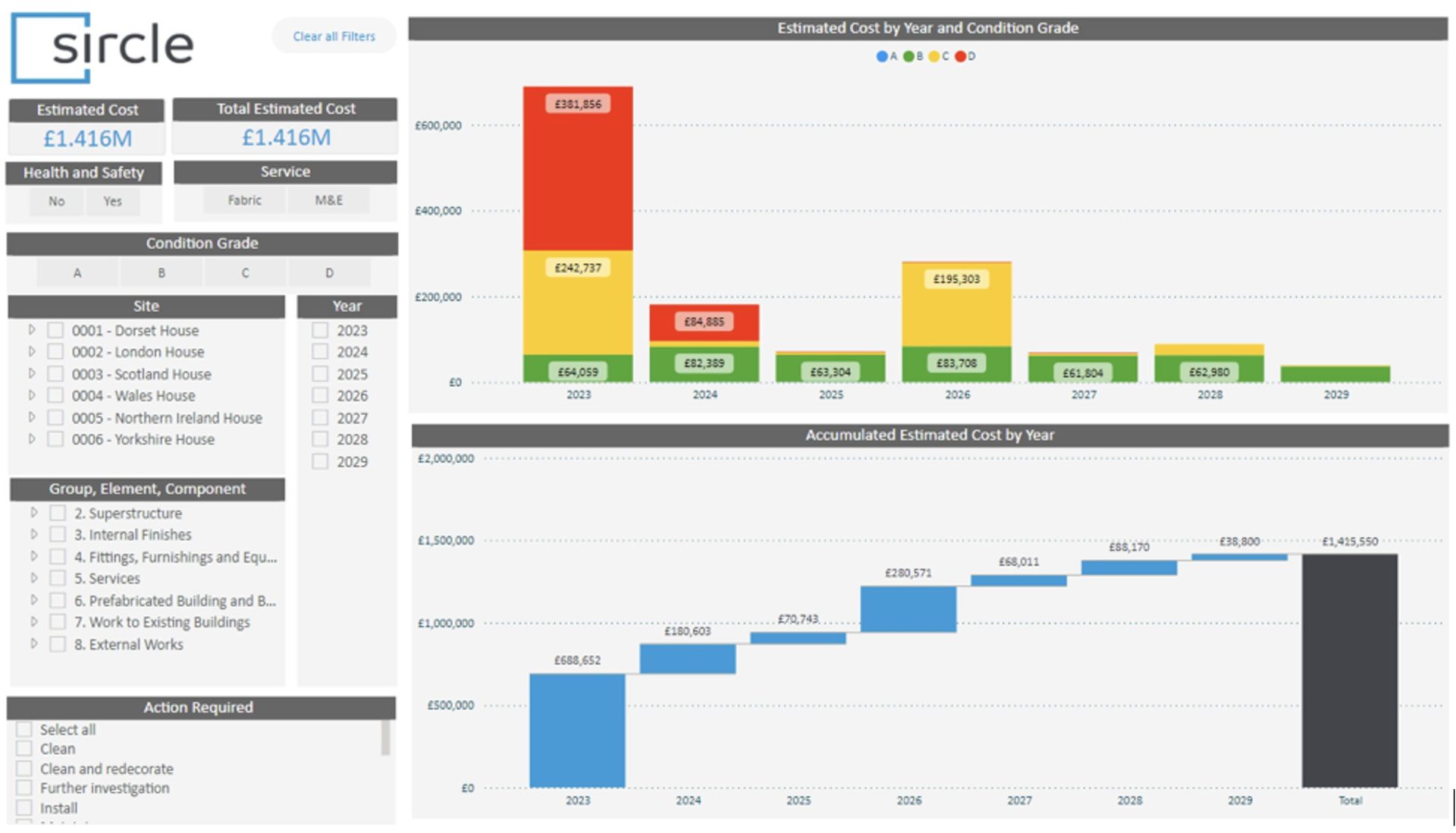
- Cost constraints: The cost of a detailed PPM survey can be a barrier for some, especially in times of tight budgets.
Solution: While a detailed PPM survey may seem like an expense, it’s actually an investment. It empowers property managers and owners to make informed decisions, avoid costly surprises, and ultimately maximize the property’s value. The insights gained can generate savings that far exceed the survey’s cost.
Conclusion
PPM building surveys play a crucial role in preserving our built environment. By proactively identifying and addressing maintenance issues, these surveys contribute to the longevity, efficiency and sustainability of buildings and support property owners and managers in ensuring that their buildings remain well-maintained and valuable assets for generations to come, echoing the sentiments of John Ruskin’s timeless words.
Legislation and standards on PPM
There are several key pieces of legislation and guidance pertaining to building maintenance in the UK, including:
- RICS professional standard, planned preventative maintenance: effective from April 2022. It sets out requirements for RICS members and regulated firms about how they provide services or the outcomes of their actions. RICS members must comply with an RICS professional standard.
- BS 8210:2020 facilities maintenance management: Provides recommendations on how to manage facilities.
- CIBSE top tips: An information sheet to help property operators, facilities managers and designers understand their responsibilities for maintenance of the workplace, equipment, devices and systems. It includes links to wider references SFG20 standard maintenance specification for building services: Addresses a wide range of building systems see.
Anthony Walker FRICS MIFireE is a chartered surveyor specialising in building surveying, fire safety and asset management. He is also a director at Sircle, a multi-disciplinary surveying consultancy.
Note: This CPD provides a general overview of planned preventative maintenance building surveys. It is recommended to consult with a suitably qualified individual for specific advice on maintenance strategies.