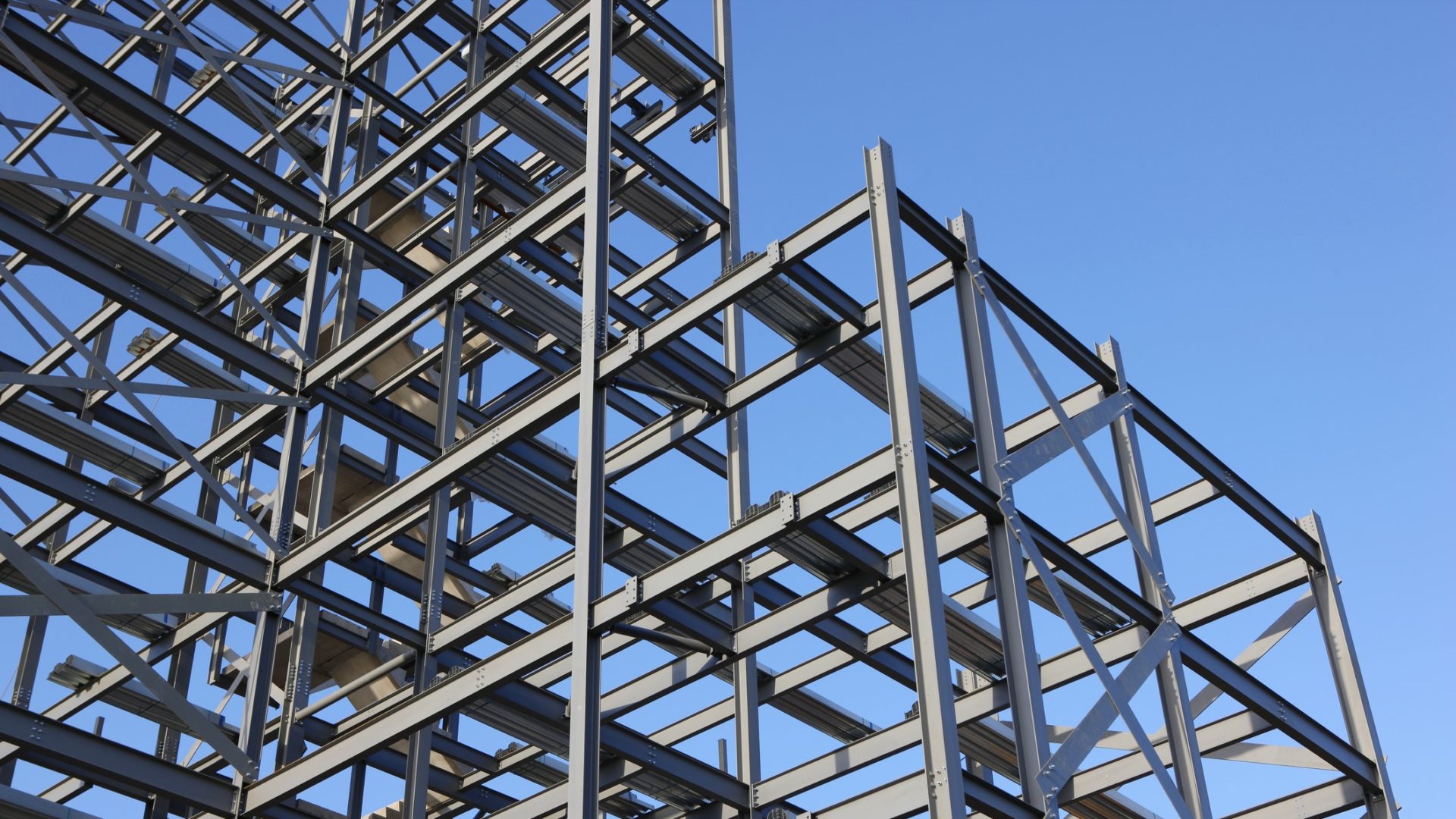
Construction products and materials including timber, steel, insulation, and roofing are becoming harder to obtain and rising in price, a joint statement from the Construction Products Association and Builders Merchants Federation has warned.
The two groups, which together co-chair the Construction Leadership Council’s Product Availability Group, have produced a summary of the status of a series of products used by the construction sector.
Timber
They said there was an imbalance between global demand and supply of timber “that is not likely to be resolved in the near future”. They warned the UK must be prepared for higher prices to continue. European production was “far lower” in 2020 compared to 2019, while UK imports of softwood during the first nine months of 2020 were also down, by 20% in volume. There has been “extremely high” demand from the USA, which is expected to continue through 2021. The Chinese market is also importing softwood at its highest-ever level. They said: “Both the US and China are prepared to pay far more for timber. In the US, the price of a benchmark 4×2 softwood product rose by 149% last year. European mills are back at full capacity, but the increased demand means that customers are on allocation, and the situation is likely to get worse in Q3 following holiday shutdowns in July and August.”
Steel
Strong global demand has driven shortages and there are order backlogs and increased prices for most timber products, including coiled sheet, stainless steel and reinforced bar. China became a net importer for the first time in 11 years in Q3 2020. Supply and demand is expected to rebalance “within the next few months”. There is also a short-term issue at UK borders, with the requirement for covid-19 tests causing delays and resulting in European hauliers being reluctant to come to the UK. Steel safeguards relating to Brexit are not restricting supply.
PIR and PUR (polyurethane and polyisocyanurate) products
PIR/PUR producers are experiencing “historically high prices” for several raw materials which is hitting short-term availability, although conditions are expected to improve by Q3 2021. High international demand for raw materials and finished goods, together with increased challenges as a result of covid-19 have also affected the cost of materials, resulting in price increases for the UK market.
Roofing
High domestic demand and reduced production stemming from the impact of covid-19 coupled with high domestic demand has led to extended lead times on most concrete tiles – averaging 19-20 weeks, with 36 weeks as a worst-case scenario. Some customers have switched to clay tiles, giving rise to lead times of 4-8 weeks on certain clay products. The situation is likely to improve in Q2 if current production levels are maintained as supply tends to outstrip demand between December and March and stocks can be built up. Lead times for BS timber battens are up to 12 weeks.
Container imports
The covid-19 crisis put “immense pressure” on the global logistics industry, the joint statement warned. This has hit the movement of freight and led to a surge in costs of building products shipped in containers especially from the Far East, including screws and fixings, tools, plumbing items and sanitaryware. Carriers have reduced routes into the UK by up to 30%, and have increased freight rates, with prices per container rising by more than 650%, without space guarantee. Containers that cost $2,100 (£1,529) at this time last year are now costing from $15,000 (£10,919) to $30,000 (£21,839). Industry analysts expect pressures to continue into 2021, despite importers looking at alternative supply chain planning.
Comments
Comments are closed.
They said there was an imbalance between global demand and supply of timber “that is not likely to be resolved in the near future”.
So can we PLEASE stop going on about building higher rise construction with TIMBER! All this green business is a joke if the industry continues to use timber at the current rates.
The same goes for sand.