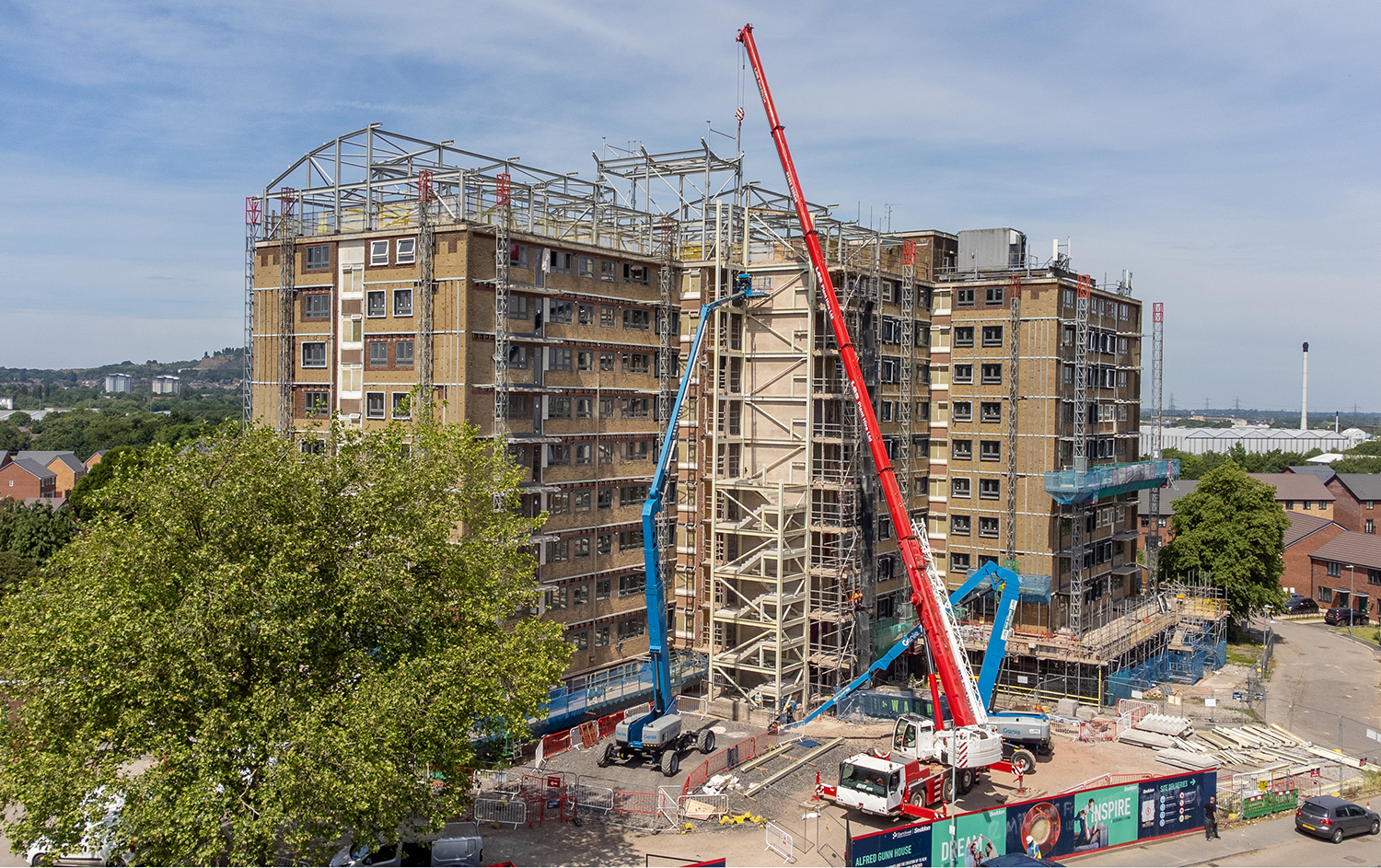
The Building Safety Act and the Grenfell fire have put high-rise residential jobs in an uncomfortable spotlight. Kristina Smith meets the Seddon team refurbishing and recladding three residential towers in the West Midlands.
Recladding residential tower blocks is challenging for any contractor in the current climate. Tough new laws on fire safety and the Grenfell legacy mean such projects attract forensic levels of scrutiny. And with the legislative landscape still changing, construction teams must think on their feet.
This was the context for Seddon on the recladding and refurbishment of Alfred Gunn House in Oldbury for Sandwell Metropolitan Borough Council in the West Midlands. And on top of the fire safety issues, there was the technical challenge of adding an external staircase to one of the three tower blocks and demolishing the corner to do so.
A key aspect was getting the risk allocation right, says Seddon regional director Rob Moore. “It is not only the project that’s the challenge, so too is getting the contractual details agreed and the risk management right from the start, at the pre-tender stage,” he explains.

Project details: Alfred Gunn House
Client: Sandwell MBC
Main contractor: Seddon
Designer: Sandwell MBC
Sub-designer (M&E): Ridge
Start: March 2020
Forecast finish: Summer 2023
Cost (forecast): £21m
Form of contract: JCT with quantities and partial contractor design
Subcontractors
Cladding and roofing works: H&H Fabrications
Steelwork: Reynolds & Litchfield
M&E: Staffordshire Plumbing and Heating
Part of Seddon’s detailed risk assessment and negotiation process involved looking at who had design responsibilities for what. The contractor says it always considers the competency of the client in relation to the complexity of a project. “We have turned down similar schemes with organisations we did not think were ready for it,” says Moore.
An evolving scope
When Seddon started work on the project in early 2020, it comprised installation of cladding to the three 1960s tower blocks. This included enclosing balconies, the addition of 10 flats on the roof, creating new flats in the basement and the construction of 16 new homes, half of them two-bedroom and the other half four-bedroom.
Over the course of the project, the scope has evolved, as it became apparent that the buildings needed attention internally too; a BBC news story about residents living in damp conditions may have contributed to that decision.
Seddon’s contract now includes replastering, new electrics, new kitchens and bathrooms and new soil and ventilation pipes. The contract sum has risen from £14m to an estimated £21m.
The tenants would not have been in the blocks at all during the works, had all gone to plan. But, one week after Seddon started on site in March 2020, Covid-19 struck. Not only did this limit what could be done on the tower blocks, it meant the decant of tenants was halted; some were only moved out this summer.
Work on the new homes, built around the tower in former car parking and unused space, could continue. Seddon completed these and handed them over in August 2021 – all are now occupied.
Demolition works begin
Work on the tower blocks began again in early 2021. Demolition and strip-out works took place on the roofs to make way for the lightweight steel structure for the 10 additional homes. In the basement, which is three-quarters underground, plant and bin storage facilities were removed.
Seddon also carried out significant repairs to the external concrete of the building which had not been included in the original scope.
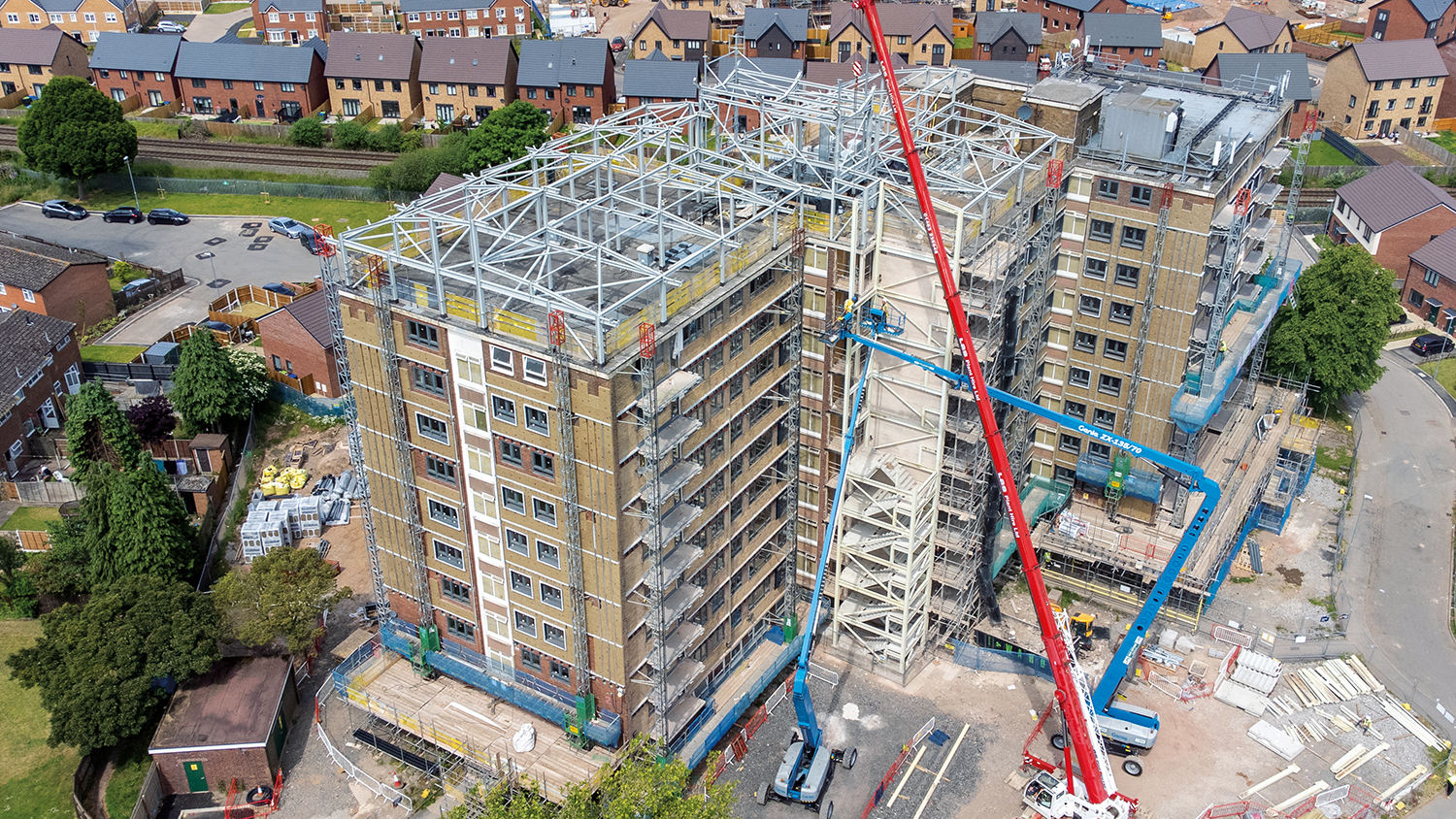
The demolition of the central tower corner to make way for the new external staircase demanded extensive temporary works and structural works. Working from the top down, Seddon propped and braced each floor before removing external walls using remote-controlled Brokk demolition robots and installing the new blockwork as they went.
Seddon regional operations manager Jim Reidy has over 40 years’ experience in construction but has never done works quite like this before. “It’s an interesting thing to do,” he says. “Not only technically, but due to the fact we were working on a live block. You have to protect people and you are taking a chunk off the corner.”
The extensive pre-planning has paid off, says Moore. Seddon lifted the steel stairs, which will be clad in the same material as the rest of the building, into place in July 2022.
Significant fire safety work
The fire safety works on the project are significant. They include fire stopping, fire doors, sprinkler systems, new water mains, removal of gas from the flats, fire breaks and fire protection to the replacement vertical drainage system. Sandwell MBC, as well as being the client, is the designer.
The council took design liability for all the fire work and the cladding, all structural elements, plus the M&E, the design of which it subcontracted out to Ridge.
Seddon is installing a variety of insulation and cladding types. From the first to the ninth floor, accounting for 80% of the cladding, a natural cement finish 8mm compressed fibre cement Ceramapanel sits over 100mm of rock mineral wool slab insulation, Rocksilk RainScreen Slab.
The top floors will be clad in 8mm fibre cement panel, Boothbay Blue HardiePlank with 150mm of glass mineral wool, Earthwool OmniFit.
Meanwhile the ground floor and basement is clad in Staffordshire blue Corium slip bricks over 100mm mineral wool OmniFit insulation.
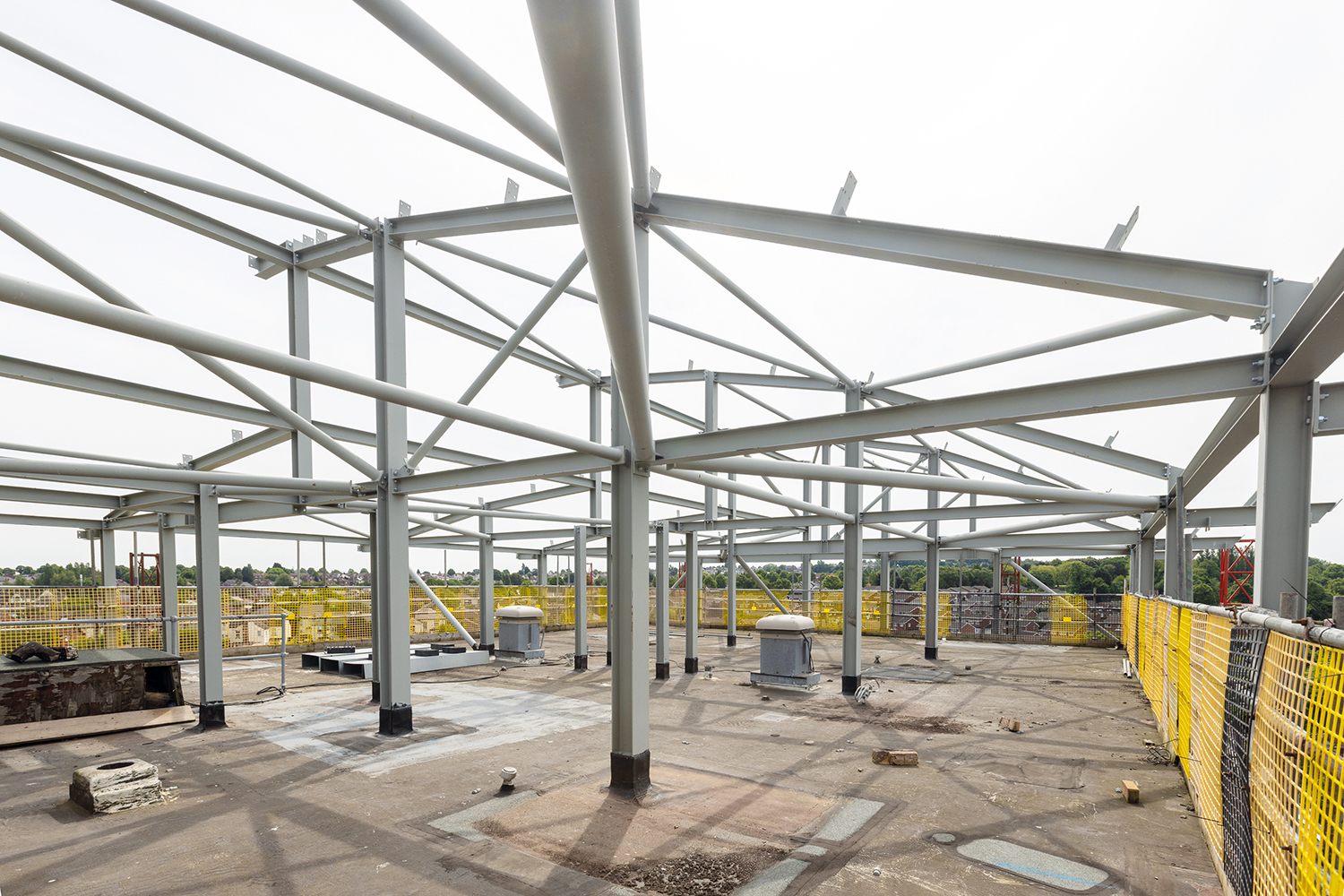
With changes to the Building Safety Bill happening right up to it coming into force in April 2022, the project’s goal posts were changing as the work progressed. This was also the case with the ‘golden thread’ – how information is recorded throughout a project and made available to those who need it – which has still not officially been defined.
“The fire protection measures have not changed in the main. It is more around the design intricacies that have been enhanced with respect to testing, certificates and QA processes,” says Moore.
Part of Seddon’s contract with the council saw it signing up to a design management process which included testing and inspection. Seddon has been able to work with the council to improve that process further, says Moore.
Seddon has divided the building up via a grid system, with every element of work inspected, photographed and signed off by supervisors, the client and a third party if necessary.
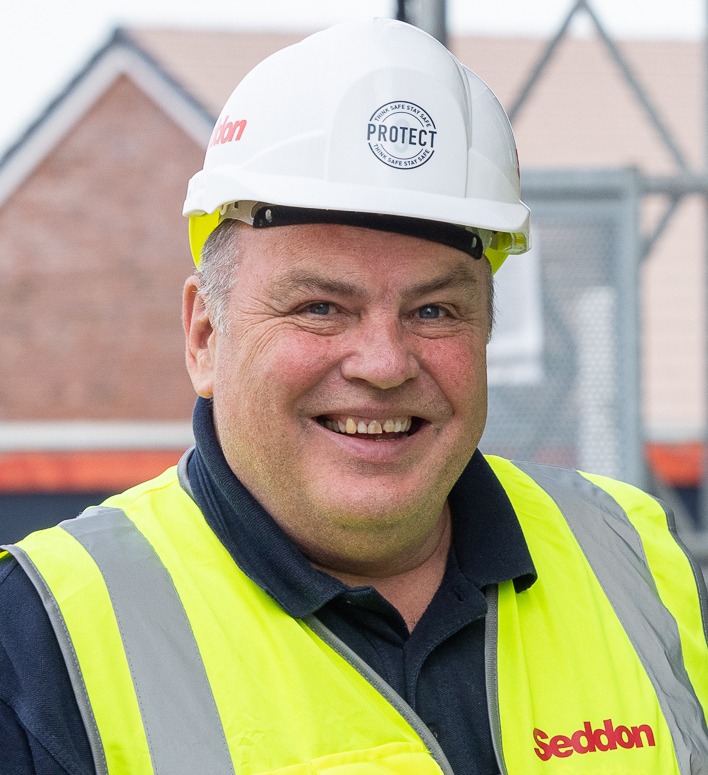
CV: Jim Reidy, regional operations manager, Seddon
Jim Reidy started his construction career as an apprentice carpenter in 1977 for contractor Thomas Elvin in Birmingham.
Reidy has worked in construction and in private housing, for the likes of Bovis and Bellway, and in social housing as well. He has been construction director at Kingfisher Building and more recently worked for British Gas’s construction arm, carrying out energy efficiency retrofit projects.
Now approaching retirement, he is helping bring on the next generation through Seddon’s apprentice and trainee programme.
“The testing would always have happened,” says Moore. “Where it is better and stronger is that we are able to evidence every single element of the work that has been done: who installed it, when it was installed, when it was signed off and who approved it. This was above and beyond Sandwell’s original process.”
This has required investment on Seddon’s part. “As well as investing in software such as SnagR, we have invested in additional site management resources and extra project administration on the scheme,” Moore says. “It’s about us having the security and the comfort for the future.”
Seddon has also trained its subcontractors. “We are bringing the supply chain along with us and hopefully these practices will transfer in terms of good quality for future projects,” says Moore.
One more year
The original project schedule, which had completion in summer 2021, has been pushed back a whole year. It was not until summer 2022 that the final group of tenants were moved out, by which point Seddon was installing rails for the cladding.
There have also been delays to the works on the roof. To install the lightweight steel framing for the additional homes on the roof, mobile phone antennae have to be moved. However, the design was not agreed with the company responsible for the antennae in time for the programme to progress as planned. This again is the council’s risk, something Seddon was careful to tie down at the contract stage.
“This is a specialist project that incorporates lots of different elements of works,” says Moore. “It is attractive to us because we are not taking the design liability in key areas. What we can bring to the table is our experience and knowledge, our technical support and guidance and our delivery expertise.”