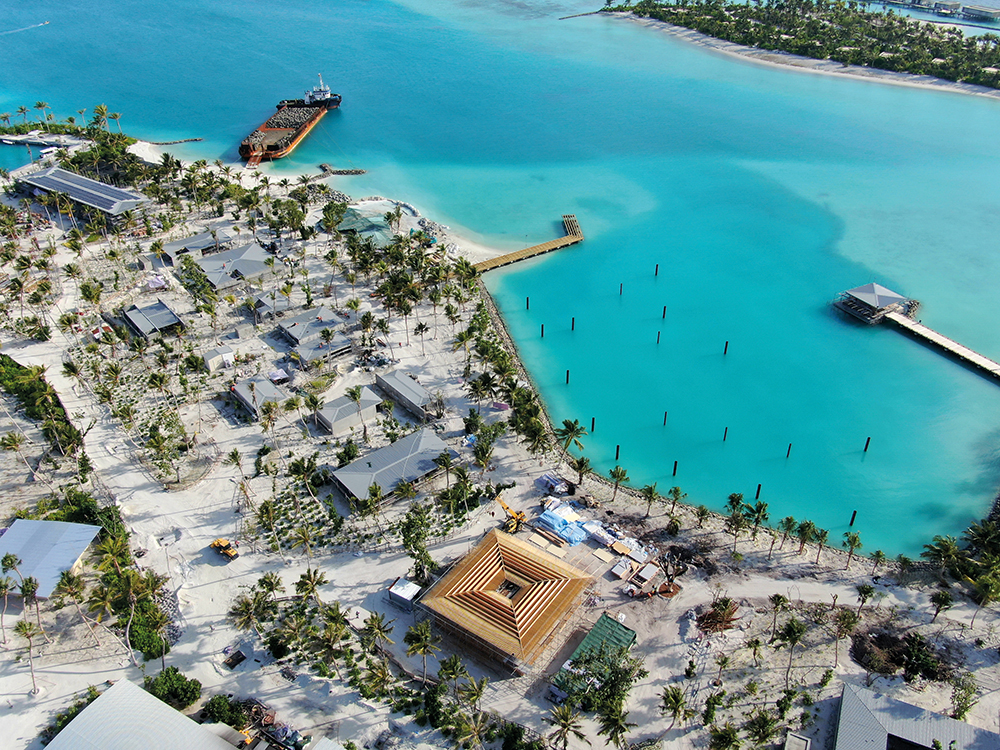
A new luxury hotel development in the Indian Ocean islands features an iconic art installation, the Skyspace. Timber engineering specialist and project team member Kevin Hill explains how the artist’s vision became reality.
It was the developer’s vision to include iconic art pieces within the Fari Islands development, comprising a Ritz-Carlton and Patina Hotel – the largest luxury hospitality development undertaken so far in the Maldives.
US artist James Turrell, known for his installations giving experiences of light and space, was commissioned to create his iconic ‘Skyspace’. The developer, Pontiac Land, also wanted to use the latest engineered timber technology for the first installation of this kind in Asia, to make it carbon negative.
Brazilian architect Marcio Kogan, who leads Studio MK27, was engaged to bring Turrell’s vision to life, and Venturer was appointed early in the design process to find the right delivery solution.
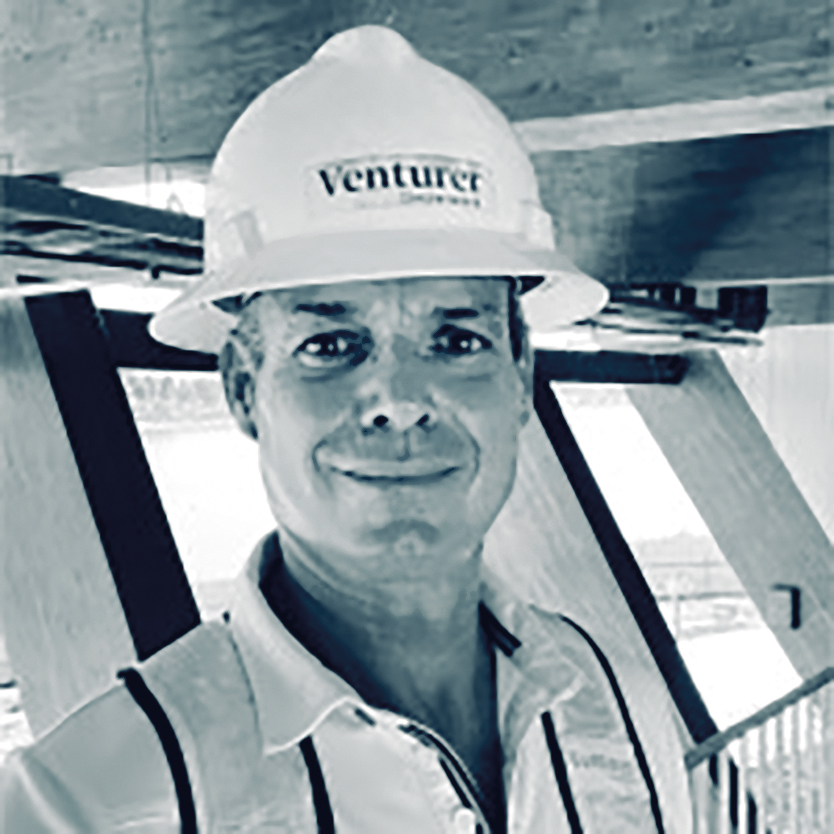
Kevin Hill CV
Since 1995: Founder and MD, Venturer Timberwork, Singapore
1992-95: Project manager, Four Seas Construction, Singapore
1989-91: Site engineer, Britannia Construction, Cheltenham
1988-89: Site engineer, Rush and Tompkins, Bristol
1985-88: Management trainee, John Laing Construction, Bristol
The design called for a 400 sq m free-span roof with razor-sharp soffits and a 16 sq m hole in its middle. Although we work with some of the best timber engineers in the business, we doubted it could be done.
That’s because when you remove the centre of a free-span roof it needs to defy gravity. If you think of iconic floating roofs such as that adorning Apple’s Apple Park campus in Cupertino, California – the biggest carbon-fibre composite roof in the world – they tend to have complex structures in the centre that radiate outward. But the design brief called for no visible beams or independent columns, inner supports or exposed connections.
Over certain spans, engineered timber’s strength-to-weight advantage diminishes so, with the owner’s blessing, we evaluated a variety of different approaches.
Other Skyspaces had relied extensively on steel sections, but steel in the corrosive marine environment of the Maldives is not ideal and site welding is typically not allowed.
Taking inspiration from Apple, we contacted a professor at MIT and commissioned a feasibility study on using composite technology. The centre opening was the biggest challenge, but the composite solution seemed to favour more support at the hips and less along the continuous edge of the facade trellis that was critical to the aesthetic.
Code compliance was another restricting factor. It was hard to find recognised design codes we could rely on in order to maintain the professional engineer’s endorsement required across the project.
Another restricting factor was uplift. The roof forms a 400 sq m wing and the lightness of composite was a drawback. Last, the proposed install methodology was based on large volumetric sectional components that were deemed hugely complex to ship and forward to site. Clearly, a flat-pack solution was the most logical approach.
Ultimately, we went back to engineered timber. A leading European timber engineer together with our manufacturing partners in Germany worked with us to conceive a solution.
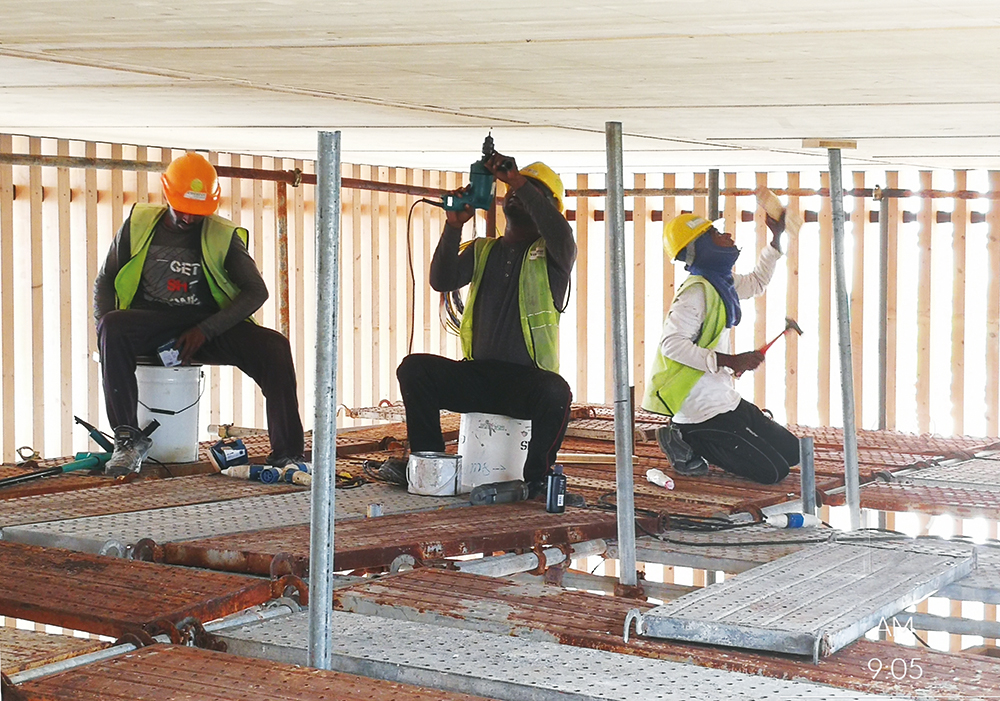
We settled on an approach where each trellis member was assigned a corresponding roof member, the trellis was reinforced with a longitudinal timber edge beam and continuous longitudinal wedge. Several continuous laminated veneer lumber (LVL) beams within the roof structure, along with the LVL roof surface, acted as a diaphragm.
The resulting solution, designed within Eurocode 5, was more efficient than composite or steel in terms of structural performance, visual aesthetic and the client’s budget.
Working with Studio MK27, we designed all components for manufacture and assembly, allowing a kit of very complicated components to be put together on site.
A key challenge of the trellis was the need to tie all the members together for it to act as a shear wall, and simplify installation by allowing the panelisation of wall elements.
“The design brief called for no visible beams or independent columns, inner supports or exposed connections.”
At the horizontal tie or connection between independent trellis components, we adopted a horizontal wedge comprised of 1mm-tolerance machined Borneo ironwood selected from an Indonesian forest certified by SVLK, the country’s timber legality assurance system. We believe this is the first time hardwood from the east has been used with engineered softwood from the west in an integrated structural solution.
The roof structure was complex because hundreds of ribs are connected by half-housed lap-and-dowel joints to each corresponding column. These elements are then tied together with five varying-sized beams, again all half-housed with a main central beam at the ridge.
Thousands of notches were precision machined by CNC machines at the factory, as were the steel drift pin holes. Finally, the diaphragm sheathing was screw-fixed to both outer surfaces, in effect constructing a profile similar to an airplane wing of old.
We calculate that the Skyspace, after production, shipping and assembly, has offset or sequestered around 100 tonnes of carbon, equivalent to taking 20 cars off the
road for a year. If built with steel and concrete, the carbon produced would likely be around 300 tonnes.
Kevin Hill MCIOB is MD of Singapore-based engineered timber specialist Venturer.