The retrofit of our existing buildings means overcoming some major technical challenges, says Sir Robert McAlpine’s Mike O’Donnell, which is where construction’s problem-solving capability comes in.
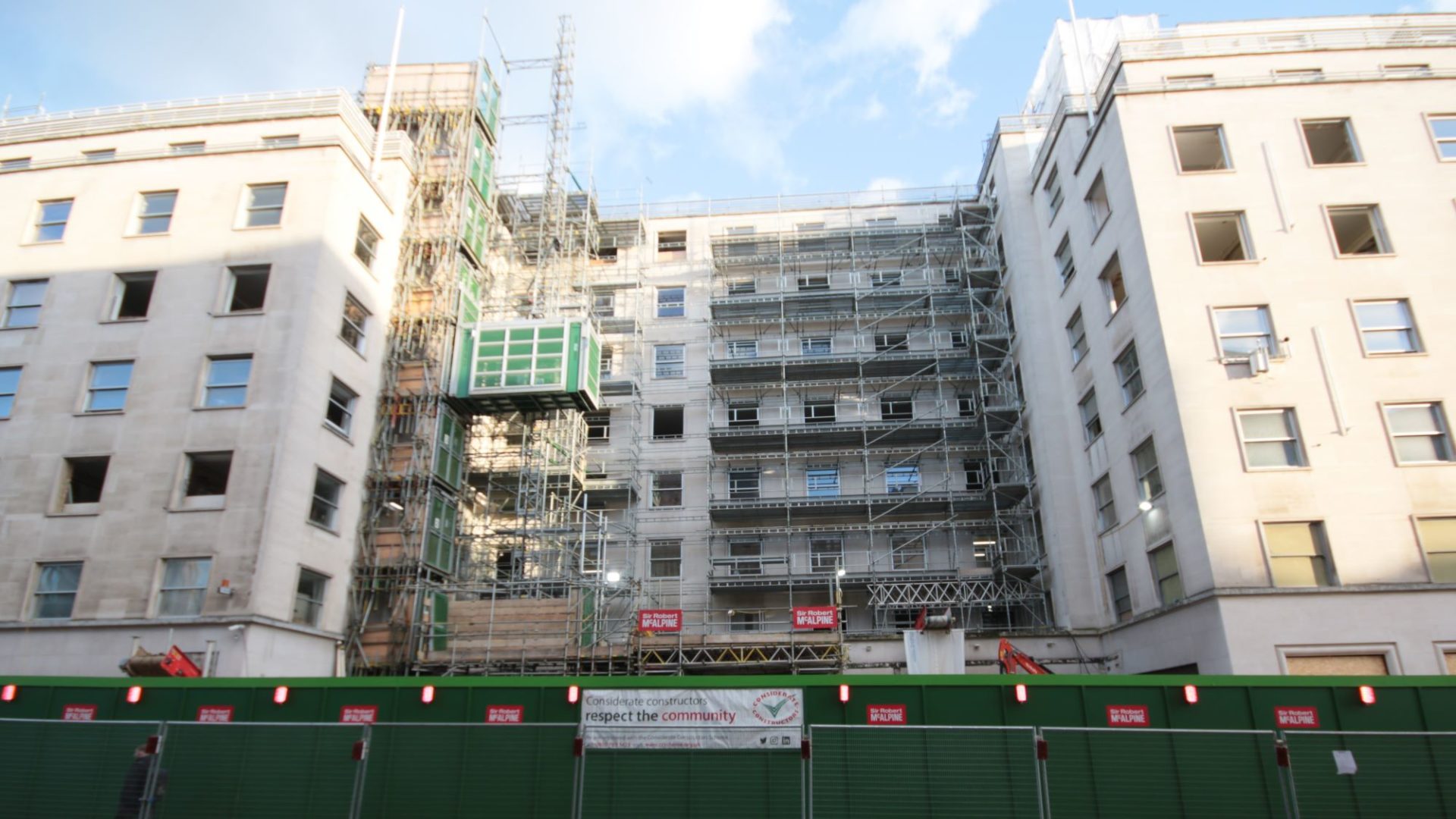
The UK is pledged to a legally binding net-zero 2050 target, which cannot be reached without the support of the private sector. As 42% of the UK’s greenhouse gas emissions (GHG) are influenced by the built environment, the construction industry has a responsibility to ensure it is making its own net-zero commitments to the same, or even shorter timeframe.
Whilst net-zero building techniques have emerged over the last decade, new buildings are only part of the carbon emissions equation. We are not working from a clean slate: by 2050, 80% of the buildings that exist today will still be in use.
It is also estimated that globally improving energy efficiency could achieve more than 40% of the energy-related emission cuts needed to reach climate goals. Decarbonising existing building stock is one of the key means by which UK construction can reduce energy consumption and its carbon footprint.
This is no longer just an environmental case, it’s a business case too. With the government introducing increasingly rigorous regulations on the energy efficiency of buildings, there will be 30 million sq ft of unlettable space in London alone by 2030.
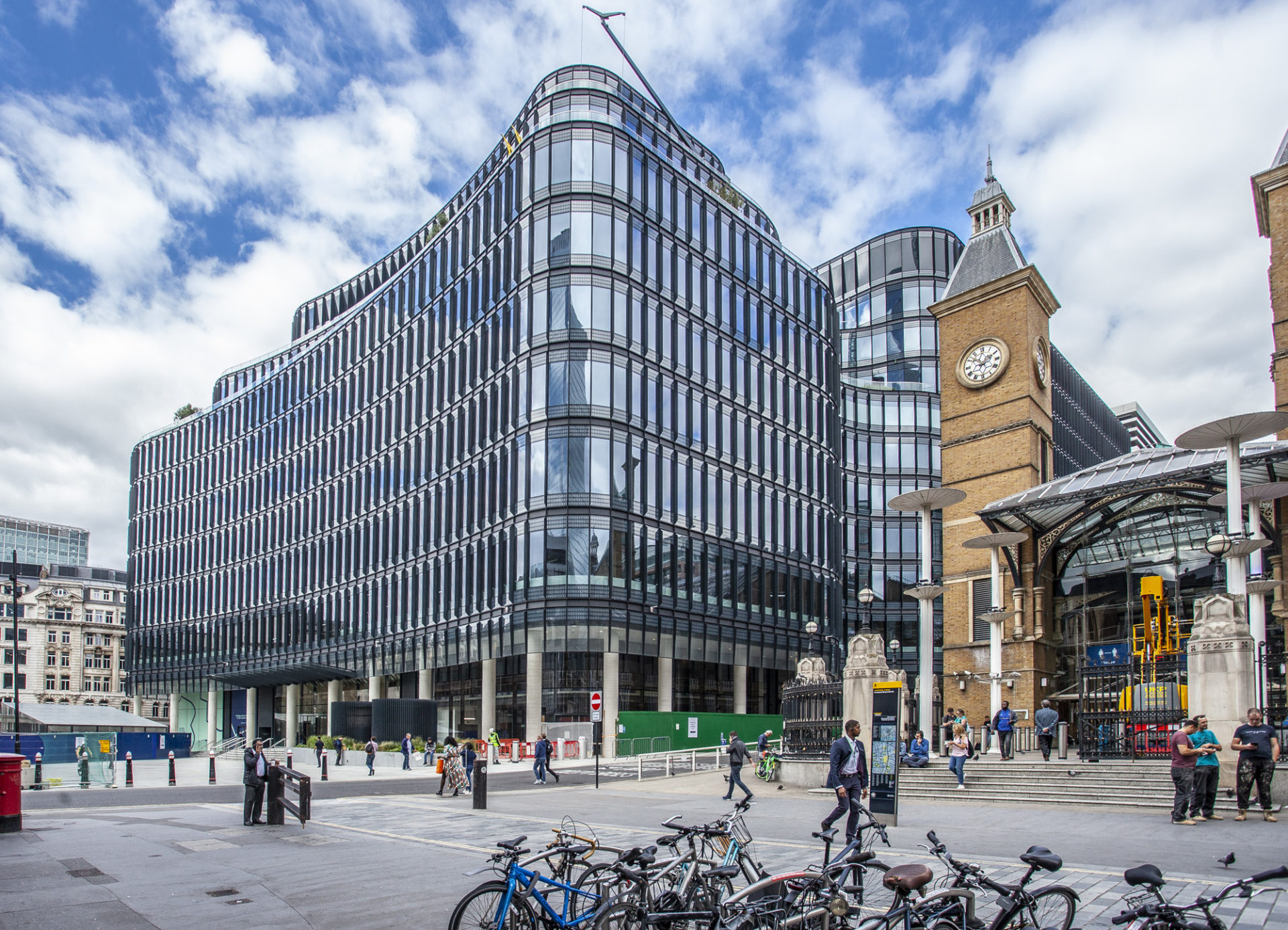
Yet, a blanket commitment to retaining and retrofitting existing buildings is no small feat. Given the age and varying standards of the UK’s existing building stock, significant works will be required to retrofit buildings to modern performance standards and there can be hidden carbon costs in these projects.
Retrofitting means technical challenges
On 100 Liverpool Street – the first net-zero British Land building and a project where Sir Robert McAlpine provided design, construction and digital construction services – approximately half of the existing building was retained and incorporated into the new building: 32% of the steel frame, saving 3,435 tonnes of carbon; and 49% of the concrete foundations and slabs, saving a further 4,086 tonnes of carbon.
However, the temporary works necessary for retrofitting projects can have a significant impact on embodied carbon.
Sir Robert McAlpine retrofitted The Westbury Hotel in Mayfair, London – a project that saved more than 2,000 tonnes of demolition waste and 3,700 tonnes of carbon emissions. But jacking up the eight-storey concrete frame required substantial temporary works using mini piles that have a higher cement content, increasing embodied carbon costs. Refurbishment projects also typically require significant amounts of steel and, in the UK, reclaimed steel is still yet to be standard practice.
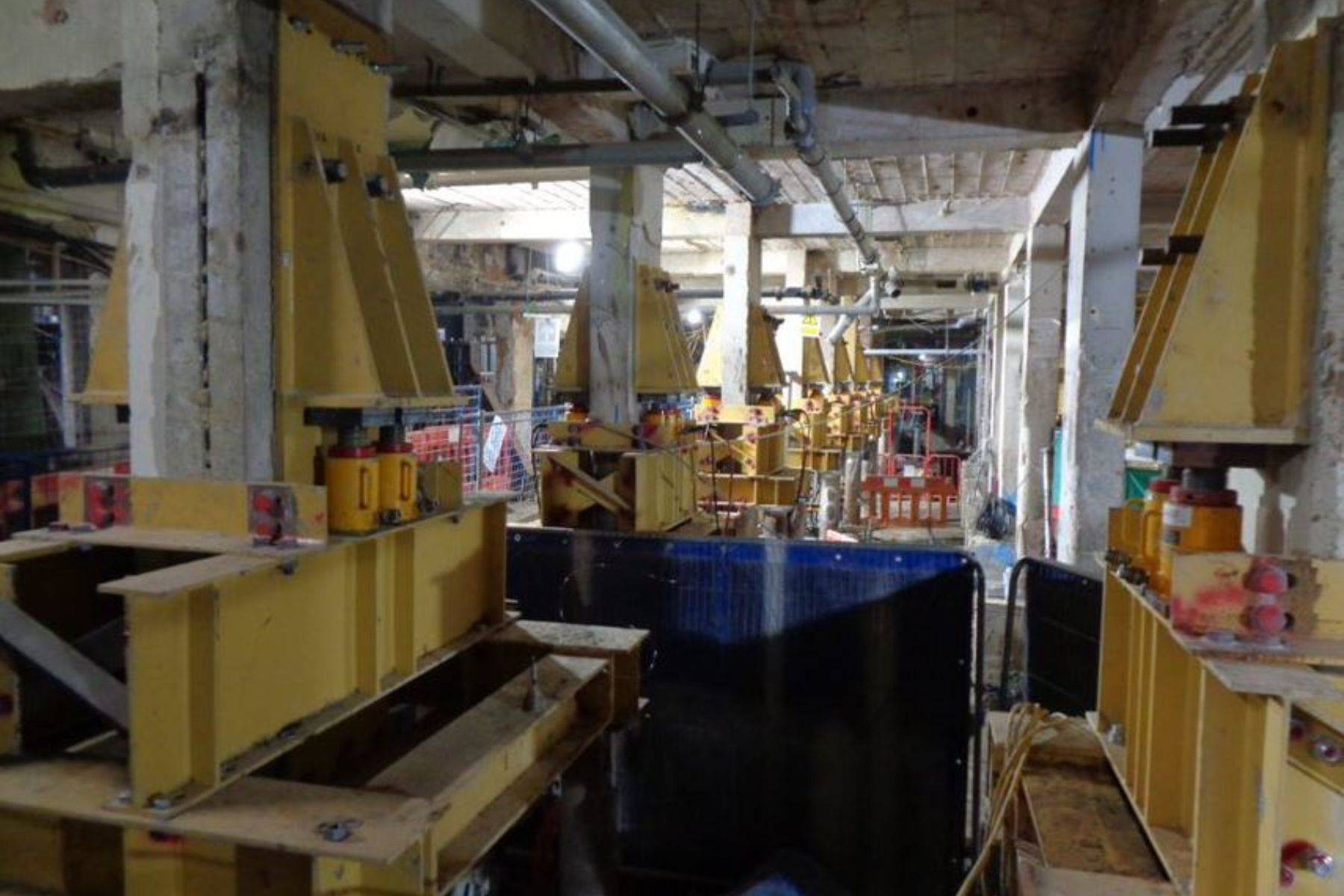
These carbon costs can be quantified and accounted for, but refurbishing existing buildings will throw up unexpected additions to carbon budgets. The difficulty of older buildings is often not knowing what a project team will find until the renovation process begins. Effective planning is therefore essential to ensure leeway in carbon budgets and that projects are keeping their carbon emissions as low as possible.
Contractors need to engage stakeholders
As contractors, it is important to bring wider stakeholders, clients and supply chain partners along with the retrofitting journey.
Engaging with projects’ embodied and operational carbon is a conversation that should be had throughout the lifecycle of a building, and we can help advise stakeholders on their responsibility for carbon reduction, sharing best practice across the industry and, in turn, improving the supply and demand of refurbishment projects.
Clients can support by engaging contractors early – we can then ensure that any risks associated with retrofitting are addressed, and that the project is delivered on time and to budget whilst hitting sustainability goals.
The challenge of the UK’s existing building stock isn’t going away.
Action is urgently needed to ensure the UK is not left with millions of pounds of stranded assets in the built environment. As an industry, construction must also ensure our offering to clients can meet the demands of this challenge to play our part in reaching net zero.
We will need to look at some areas of construction differently, but, reassuringly, we are an industry of problem solvers, powered by engineering excellence. If we apply our best minds to the net-zero arena and remain open to new ways of working and innovating, we will succeed.
Mike O’Donnell is managing director, commercial, at Sir Robert McAlpine.
Comments
Comments are closed.
Interesting article. One issue that might add value is to consider how you would approach the insurance market on these types of project. In particular the latent defects market. You referenced use of recycled steel for instance and wonder if we can get stats or papers that could tell a story on how this would work in practice?