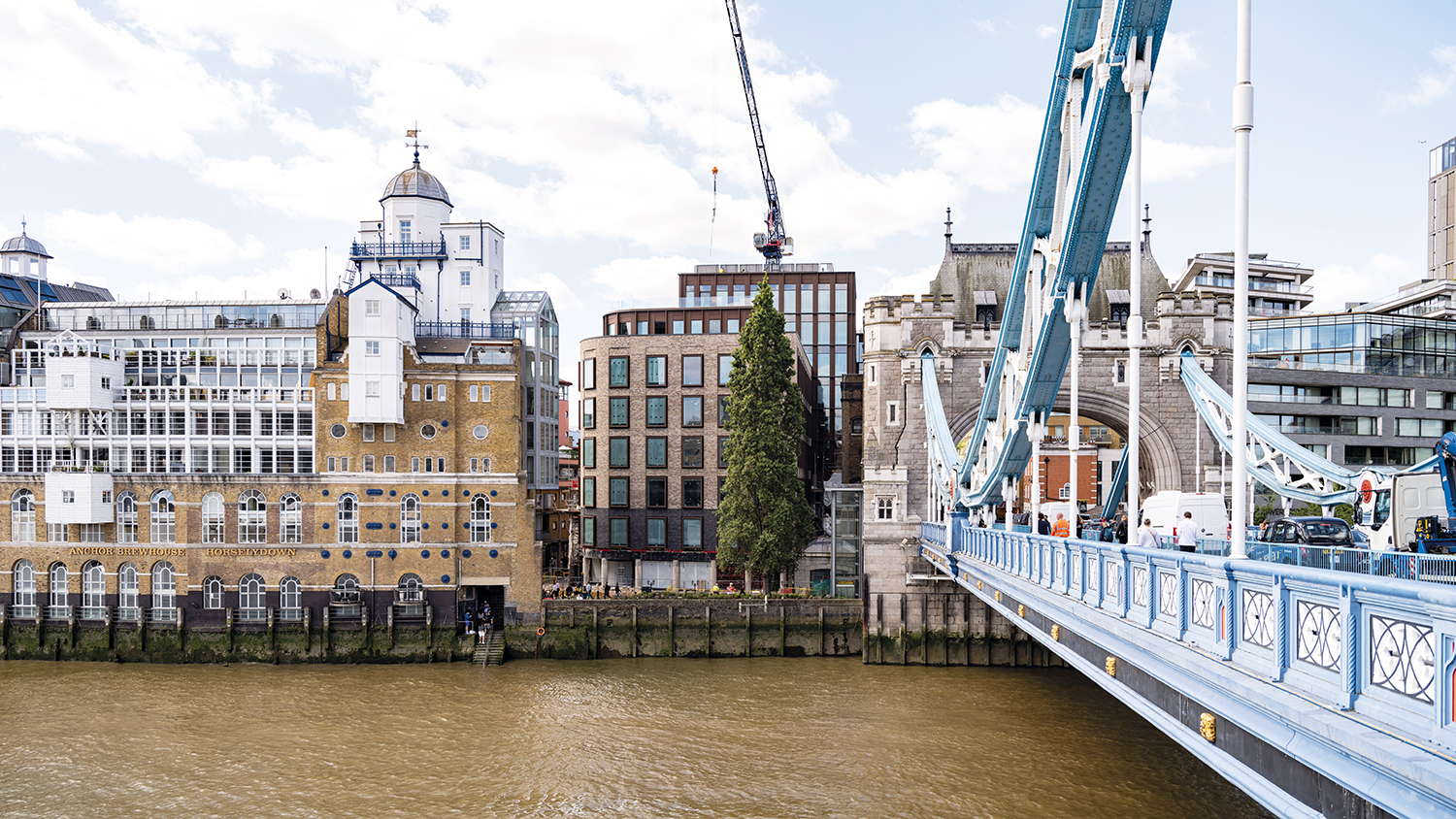
Willmott Dixon’s latest project, next to London’s Tower Bridge, has incorporated 1930s steel beams in a building designed to make an impact on sustainable construction. Cristina Lago reports.
TBC.London might soon become one of the most photographed office buildings in the world. Located on the south bank of the River Thames, it sits in a unique spot overlooking Tower Bridge and within the Shad Thames conservation area, famous for its 19th-century warehouses and cobbled streets.
TBC.London
Value: £56m
Client: Fore Partnership
Main contractor: Willmott Dixon
Architect: ECE and Stiff + Trevillion
Structural engineer: Webb Yates Engineers
Form of contract: Bespoke contract based on JCT
Timeline of the project: 95 weeks contract programme extended to 101 weeks
Completion date: October 2024
Building dimensions
Building height: 36m (measured from average ground floor level to top of level 09 parapet)
Building dimensions: 25m (w) x 83m (l) (measurement taken at level 01 at the widest and longest point of building)
Floor space: 13,660 sq m
Size of site: c2,150 sq m
But aside from being at the steps of an iconic landmark, Willmott Dixon’s project has strong sustainability credentials: it has been designed to be net zero in operation, becoming one of the first workspaces in the capital to be run solely by electricity.
It is also a poster child for the retrofit-first approach: instead of demolishing the former 1990s office block, sustainable real estate developer Fore Partnership – Willmott Dixon’s client – was adamant that the project should reuse the old foundations and make the most of the circular economy. So much so that it decided to reclaim 16 tonnes of prewar steel beams from the old House of Fraser store in the West End and incorporate them into the building’s frame – believed to be a UK first.
The original building, Tower Bridge Court, was first put on the market by Savills in 2018. Erected in 1990, it had a gross internal area of 10,300 sq m, comprising six floors and a basement including 20 car parking spaces. It was built with a concrete frame construction and external cavity walls with an outer skin of clay-facing brickwork.
Demolition agreed
Southwark Council agreed during a pre-application meeting in September 2017 that the building could be demolished as long as the replacement made a better contribution to the character and appearance of the conservation area. One of the proposals considered was to demolish the block and rebuild it as a 14-storey hotel.
“I think it effectively scared people off because any smart hotel person would have thought there’s no way that they’re going to get planning approval for a knockdown rebuild for a 14-storey class building next to Tower Bridge,” says Basil Demeroutis, an aeronautical engineer and Fore’s managing partner.
In the end, Fore was one of three bidders that put an offer and successfully bought it for £51m, £6m less than the asking price.
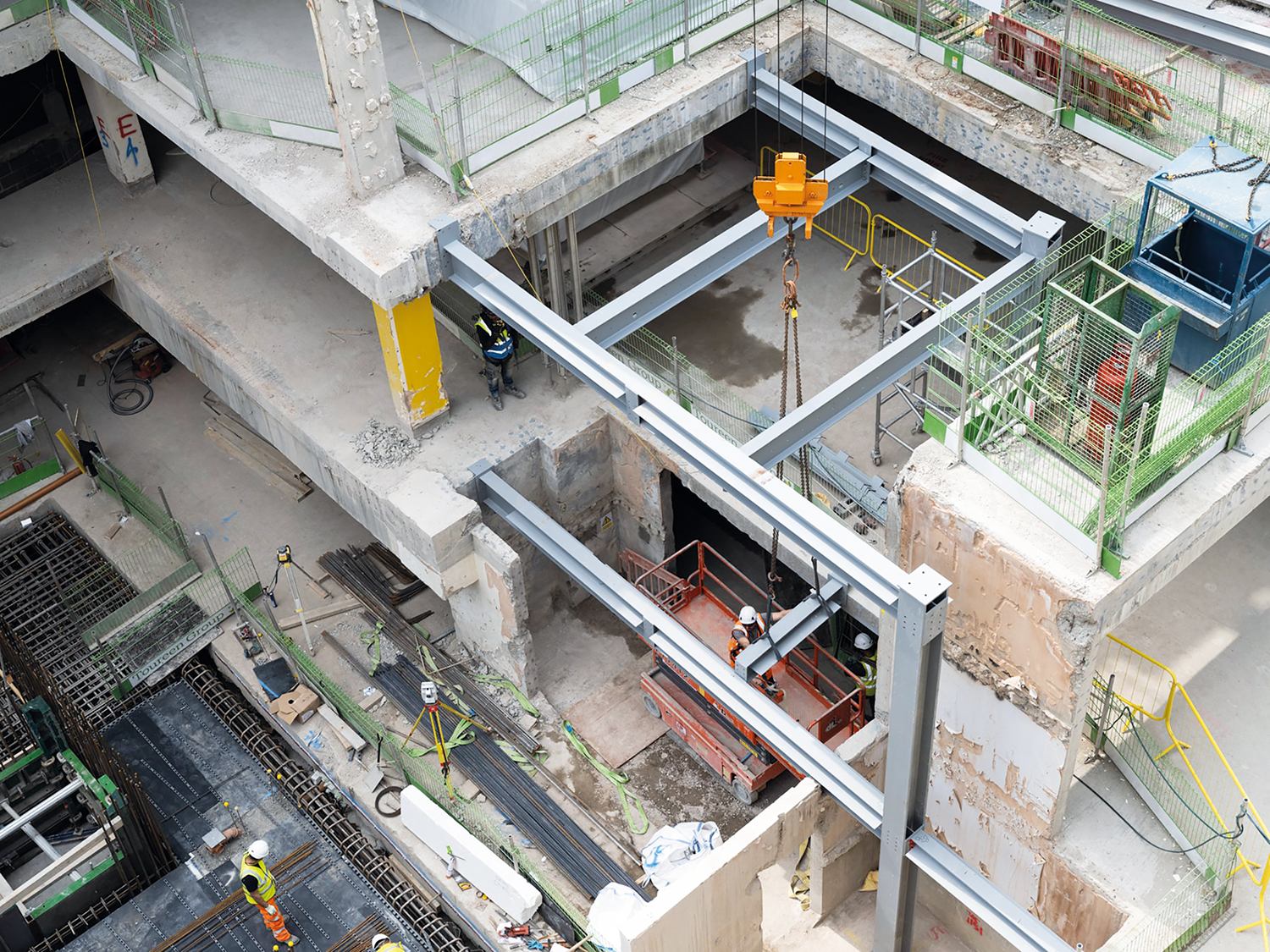
“We bought it as a sale-leaseback from the West of England insurance company, which was the owner-occupier of the building,” Demeroutis continues. “They stayed in for a year and during that time we got our act together in terms of what we wanted, which we finally decided in February 2020.”
Demeroutis laughs at the “perfect timing” of the resolution: one month later, Fore had to put everything on hold as a result of the covid pandemic.
“But our strategy was from the beginning not knocking down the building,” he emphasises. “As part of our company ethos [Fore’s motto is ‘Do well by doing right!’], we are committed to no new construction and therefore it was important to us to work with the existing building. Carbon was embedded into our thinking and strategy from day one.”
Getting Willmott Dixon on board
To realise Fore’s vision, which included working with a contractor committed to overcoming the challenges of implementing sustainable methods of construction, they needed to team up with the right people.
They initially signed a preconstruction services agreement with McLaren but the process eventually ended as a single-stage tender after Demeroutis met with Chris Tredget, then managing director of Willmott Dixon’s construction team for London and the east of England, at a UKGBC event, where Demeroutis sits on the board.
From that point, Fore and the contractor worked bilaterally to develop and negotiate the cost plan. The pandemic and lockdowns meant that work had to be paused for six months but both companies ultimately signed a bespoke JCT contract in August 2022, with works starting on site the following month.
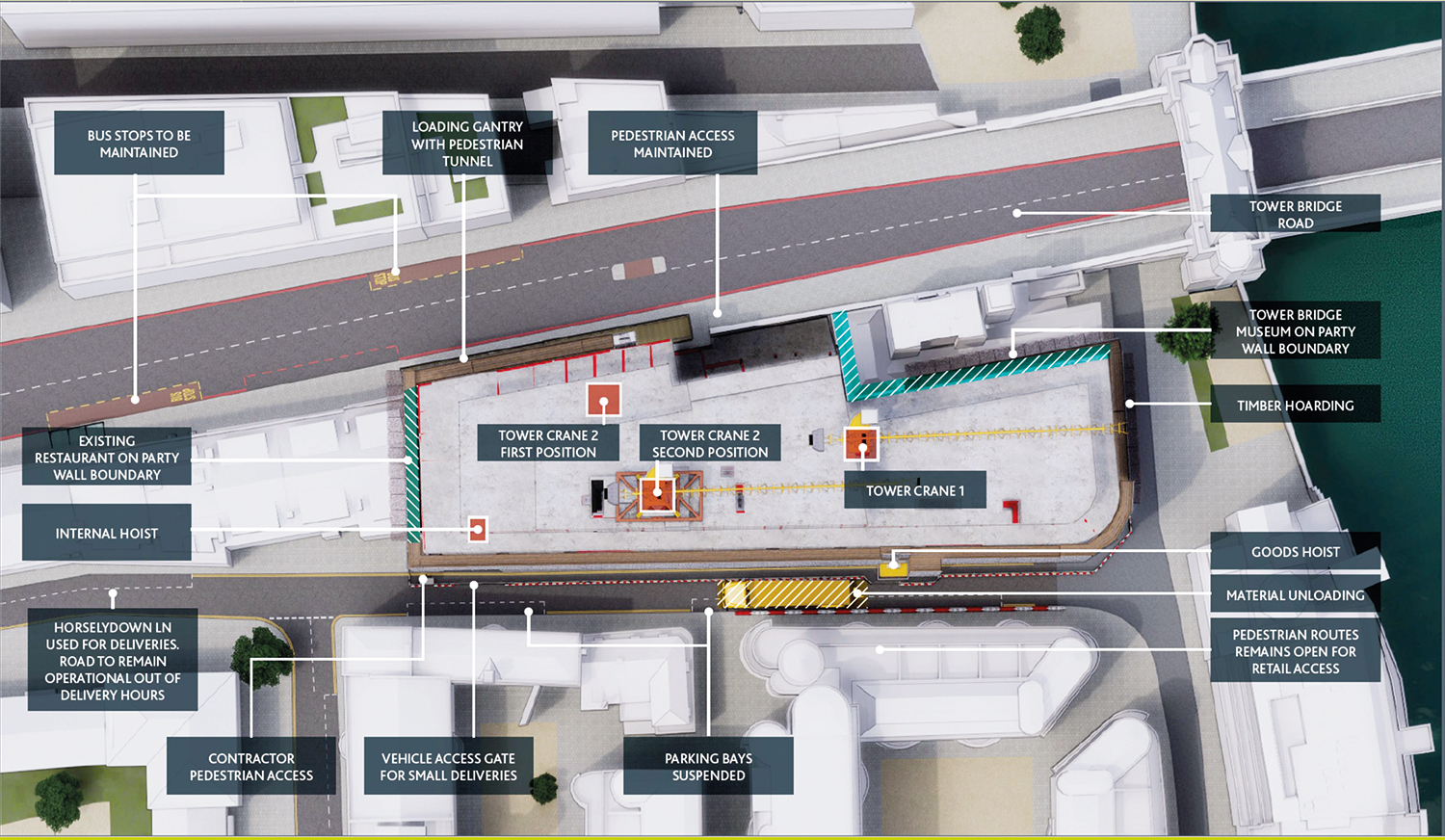
Demeroutis adds that while Willmott Dixon was ready, willing and able to join Fore’s journey – the hardest part was to convince its funding partners to come aboard.
“There was a financing component that unlocked the ability to start on site, which only unlocked once the pandemic officially ended in the summer of 2022,” says Demeroutis. “It’s hard to remind ourselves what it was like back then but, from a company’s standpoint, it was uncertain times.
“However, we knew that at some point we would come out of it and we knew that it was the right product, the right building and that we had the right story.”
Reimagining Tower Bridge Court
Constructing TBC.London involved the implementation of innovative and sustainable materials and technologies – but it also came with important challenges associated with the building’s tight location in a densely populated heritage area with minimal storage access, explains Matt Adams MCIOB, senior operations manager at Willmott Dixon.
The scheme required cutting and carving the existing building while retaining some of the structure, including the concrete frame, to add three floors and turn it into an eight-storey plus basement building. It was expanded from a 6,300 sq m net internal area to almost 10,200 sq m, which had to be done sensitively, due to the location’s significance.
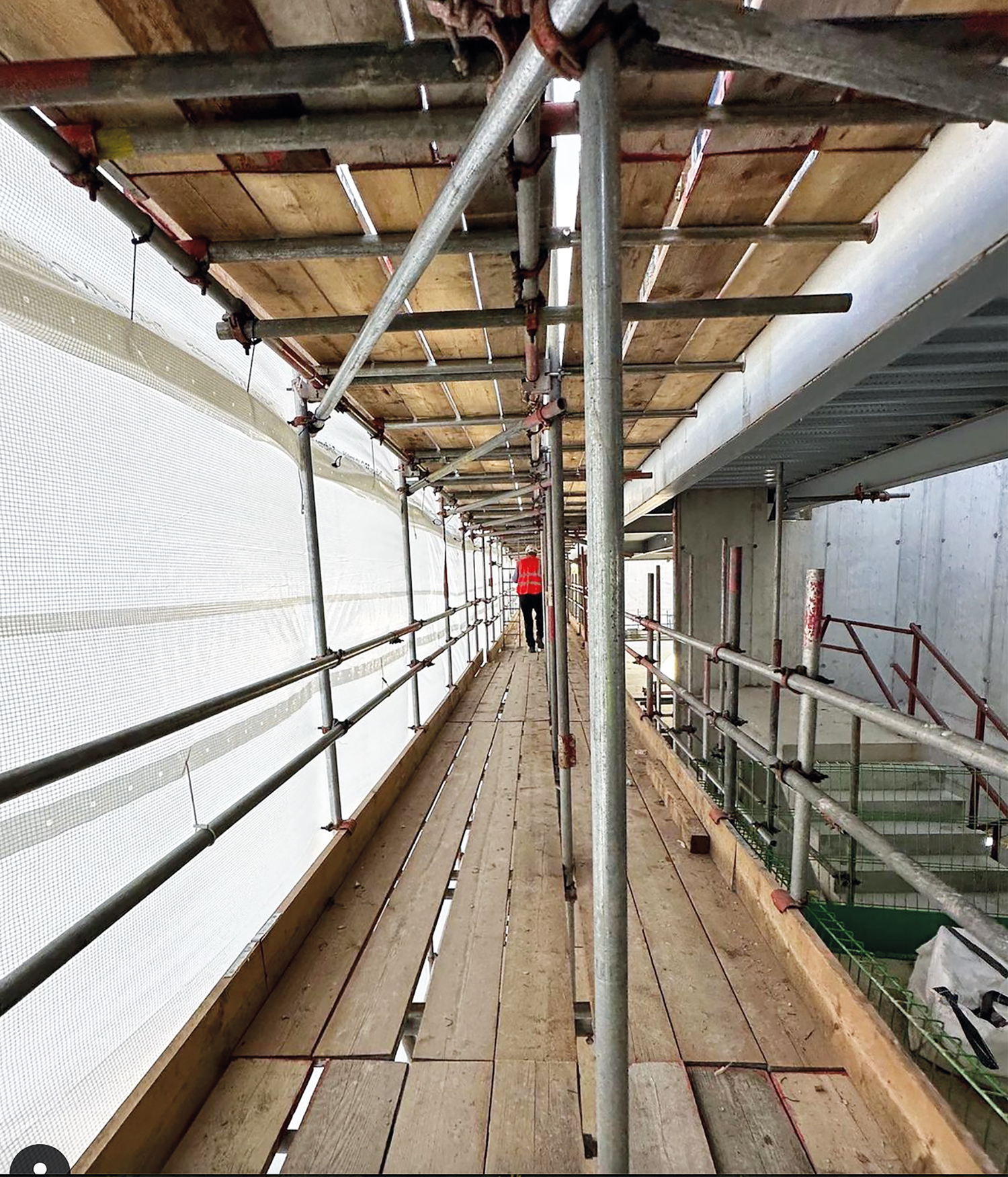
“Essentially, what we’ve constructed is the removal of the middle of the building, replaced it with a new core, added three additional floors and then knitted the existing frames together,” says Adams.
Reconfigured basement
A big financial decision early on, adds Demeroutis, was deciding where to move the core, which in the old structure was on the west side, facing Tower Bridge Road.
“We reconfigured the whole basement, which was a big challenge because it meant that all the space down there – including car facilities, sprinkler tanks, attenuation tanks – had to be shifted around and ductwork locations moved around inside the building,” Adams tells CM.
“Originally, on Tower Bridge Road, there was a glassed-type facade atrium area which was using up a lot of space and we removed it and extended the floor plates.”
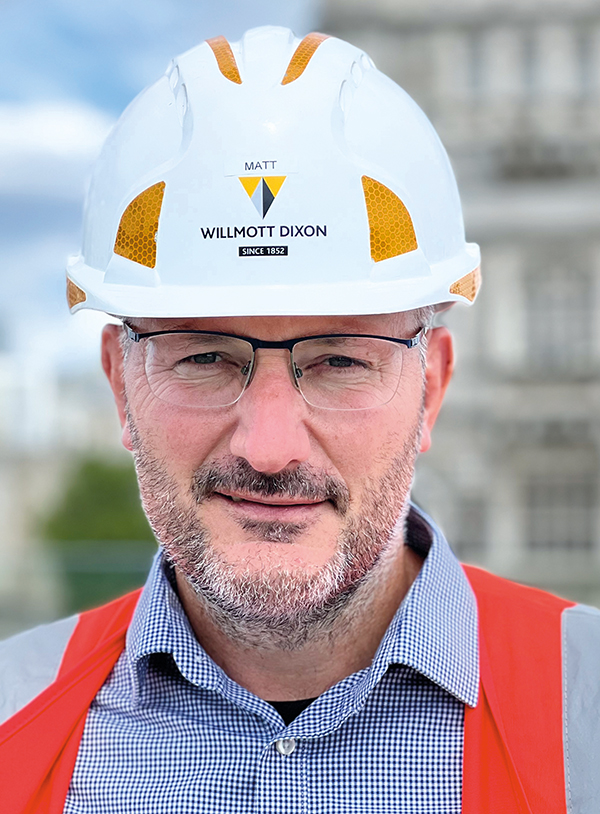
CV: Matt Adams MCIOB, senior operations manager, Willmott Dixon
My career in construction began in surveying, working for a very small PQS firm based in Watford. Since then I have worked as a senior surveyor for Kier and have been with Wilmott Dixon for 12 years now.
Approximately six years ago, I was asked to lead a challenging project in Hampstead as a senior operations manager – just before the pandemic hit, which brought a whole new unknown set of challenges.
TBC.London is the most sustainable project I have ever built and its complexity and the location being next to a national treasure are the type of challenges I thrive off.
You live and breathe a project and become emotionally attached to it as it goes through its twists and turns – and the end result will be a fantastic legacy.
Demeroutis adds: “It was a £2.7m-£2.8m decision to move the lift course to the back of the building, which is what we did in the end. That created a 12m clear span from the edge of the left corner to the windows – up from the previous 6m in the old building between the core and the windows facing the river and the City – and, instead of the doughnut-shaped floorplates, we designed it as a c-shape.”
A positive of the new entrance forecourt is that it gives breathing space to the adjacent accumulator tower and chimney stack, a Grade II-listed building next to Tower Bridge. Its purpose was to store high-pressure water for use in hydraulic machinery. To avoid obstructing its view, the north side of TBC.London was designed to be lower than its middle, and even the brick colours match those of the historic structure.
“The relationship between the accumulator tower and ours started to inform how we wedding-cake the building with the surrounding landscape,” Demeroutis says.
“We were able to reuse the existing piles and only had to introduce new ones underneath the new staircores,” says Adams.
Made of steel
TBC.London led a breakthrough in ‘urban mining’ by reusing 16 tonnes of 1930s steel beams salvaged from the former House of Fraser building in London’s West End.
“The idea came from Basil while he was going on a bike ride with Gareth Atkinson, a director of Civic Engineers, who was working on the House of Fraser refurbishment project. He told him that he had some steel beams there, so Basil came to us and said, can we use them in our building?” explains Adams, who laughs when retelling how taken aback he was by the suggestion. “I said: what, really? But we did it.”
The use of reclaimed steel was a core sustainability initiative for the project, but it required significant coordination and problem-solving to successfully implement it. Willmott Dixon had to pause its original steel order, and work with the suppliers to cancel a portion of it, to instead use the House of Fraser steel. The original plan was to reuse many more beams from the old department store but challenges around supply and demand and testing constrained it.
For this, Adams’s team worked with Cleveland Steel, a company specialising in sourcing and storing reclaimed steel. “You send them your steel fabrication drawings and ask them to match them with what they’ve got available,” Adams says.
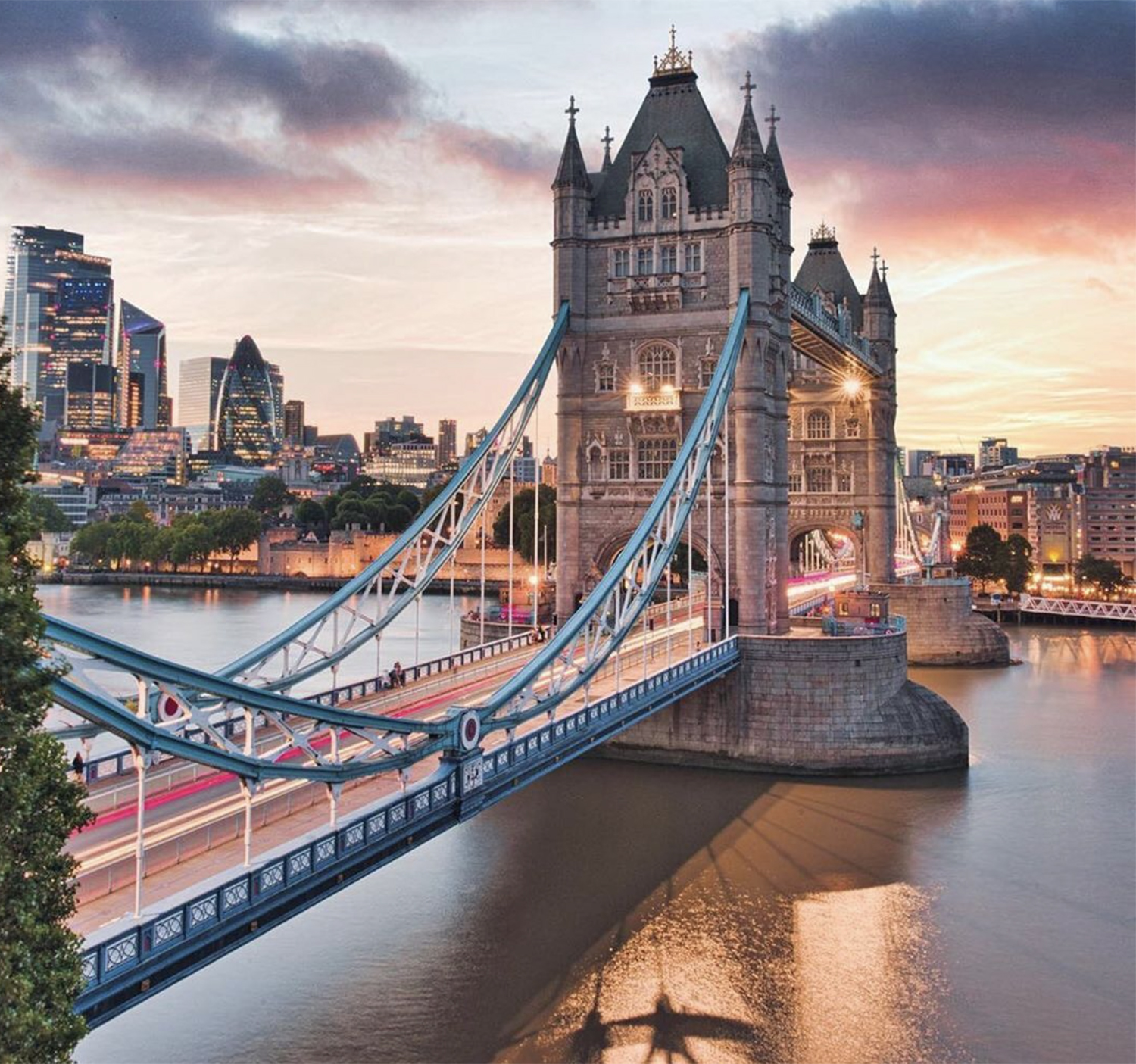
“It’s very economical and an important step towards the circular economy. I would have loved to use many more [recycled steel beams] but we engaged with Cleveland a bit later in the programme and it is all dependent on what is available at the time. Next time we’ll do more.”
Mechanical and chemical properties
Because the beams dated from the 1930s, they had to be thoroughly tested to establish the mechanical and chemical properties of the steel, which added another layer of extra time and complexity.
The independent Steel Construction Institute’s protocol for reusing reclaimed steel excludes any produced before 1970, and guidance in this area is still underway. There are some limitations to the applications of this older stock. For example, it cannot be used in structures that are subject to fatigue, plastic analysis or seismic loading. It should also be stripped of paint and finishes and hardness tested to determine its yield and ultimate strength.
In addition to the House of Fraser beams, TBC.London incorporated a further 40 tonnes of reclaimed steel from sites across south-east England, and all reinforcement within the structure’s concrete comes from 98% recycled steel.
“It’s a powerful story that shows you can change things in the industry,” Adams adds. “You are working with your competitors and new people you’ve never met before to achieve something that’s very positive which also offers an end cost-neutral position. But the carbon saving is invaluable.”