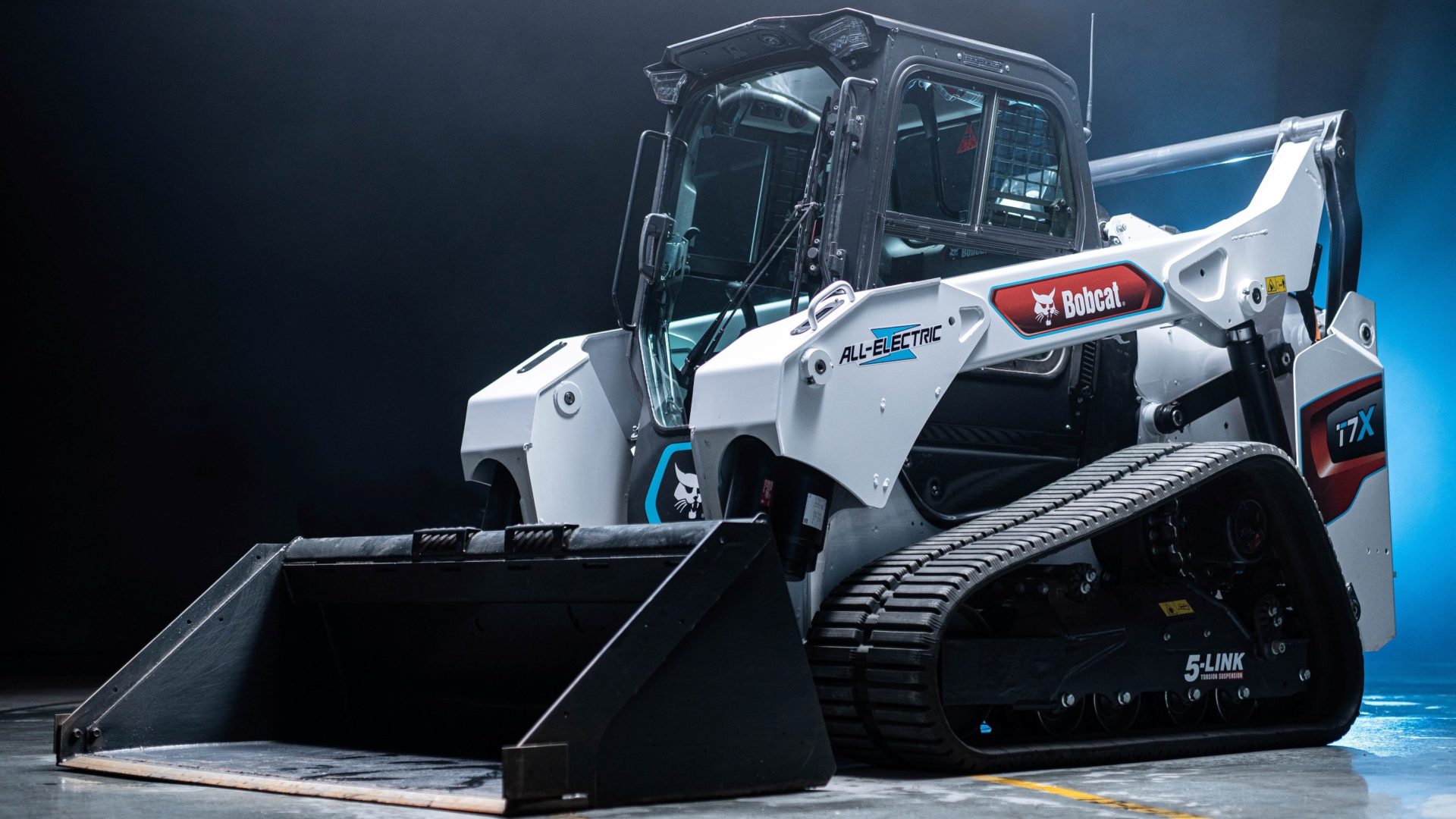
Just as electric vehicles are starting to take to the roads, more electric construction plant and equipment is being launched into the market. But when will we reach a point when all plant is electric? It could take longer than you think, explains Kevin Minton.
Hardly a day goes by without the launch of a battery powered item of plant or news of a company adding electric equipment to their fleets.
In the first half of January alone came news of what is claimed to be the world’s first electric compact tracked loader, and of a contractor converting an asphalt spreader from diesel to battery power. And machines like mini excavators, compact dumpers and scissor lifts are already available in battery versions.
Certainly, the COP26 environmental summit in Glasgow last year highlighted the urgent need to reduce emissions. More organisations have net zero carbon targets in place and are looking for greener ways of working.
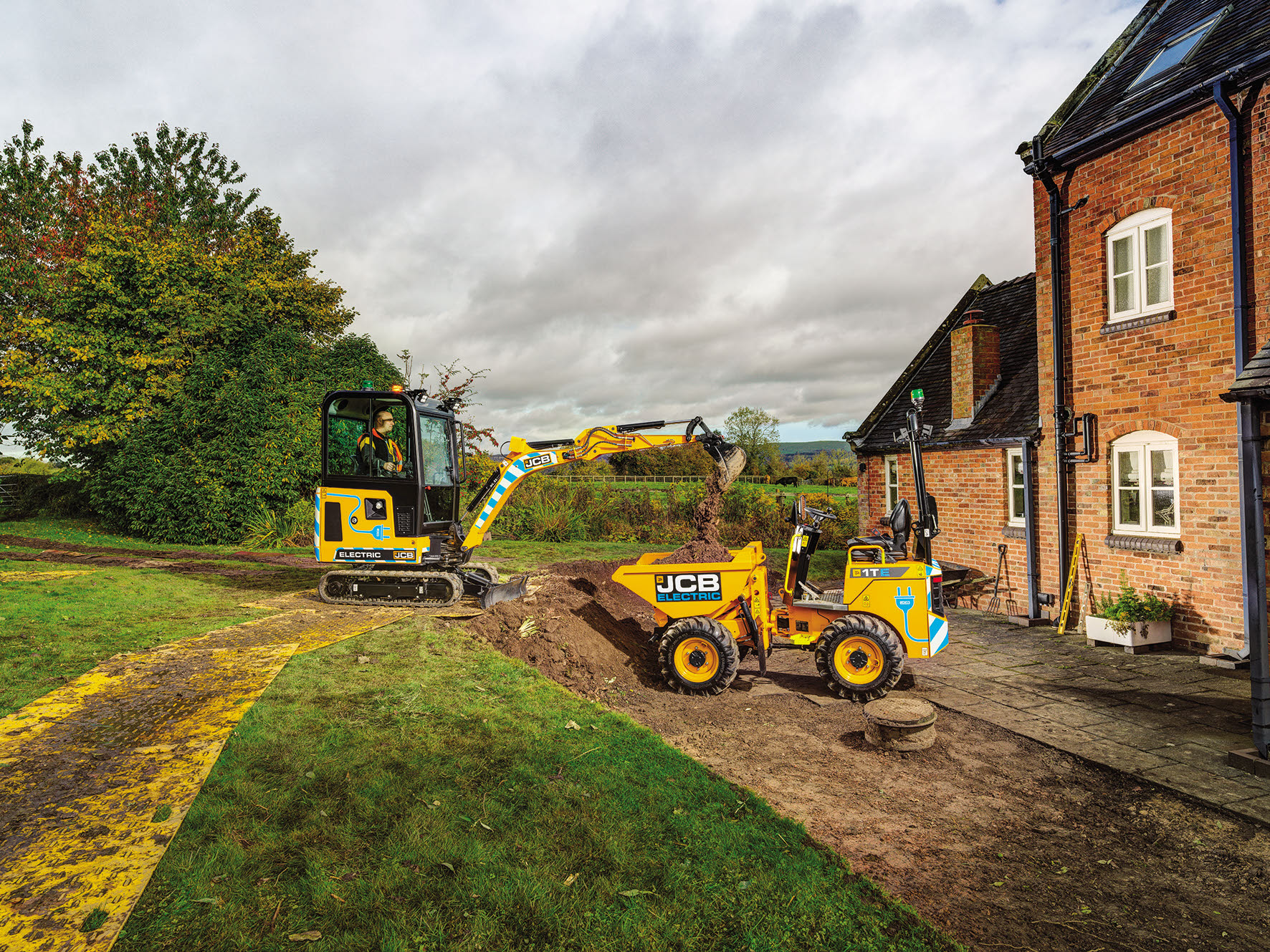
So you may ask: how long before all plant goes electric? The probable answer is, however: longer than you might think. This is because the technology has not yet reached a stage where it can power all machine types.
Most battery versions are smaller, compact models in the lower weight classes and offer sufficient power for perhaps four-to-six hours of operation, in the case of something like a mini excavator, before recharging is needed.
One manufacturer has said that to power a 20-tonne excavator using current technology would require a lithium-ion battery itself weighing 8 tonnes.
For the appropriate applications, however, battery machines are a practical choice to avoid the use of fossil fuels. And they offer other benefits such as reduced noise and the possibility of indoor working, in turn increasing operational flexibility and efficiency.
As with electric road vehicles, the battery technology carries a higher price tag that reflects considerable R&D investment. Manufacturers, however, point out that factors like eliminating fuel costs and the much-reduced maintenance requirements can make battery powered plant more cost-effective to own and operate in the long run.
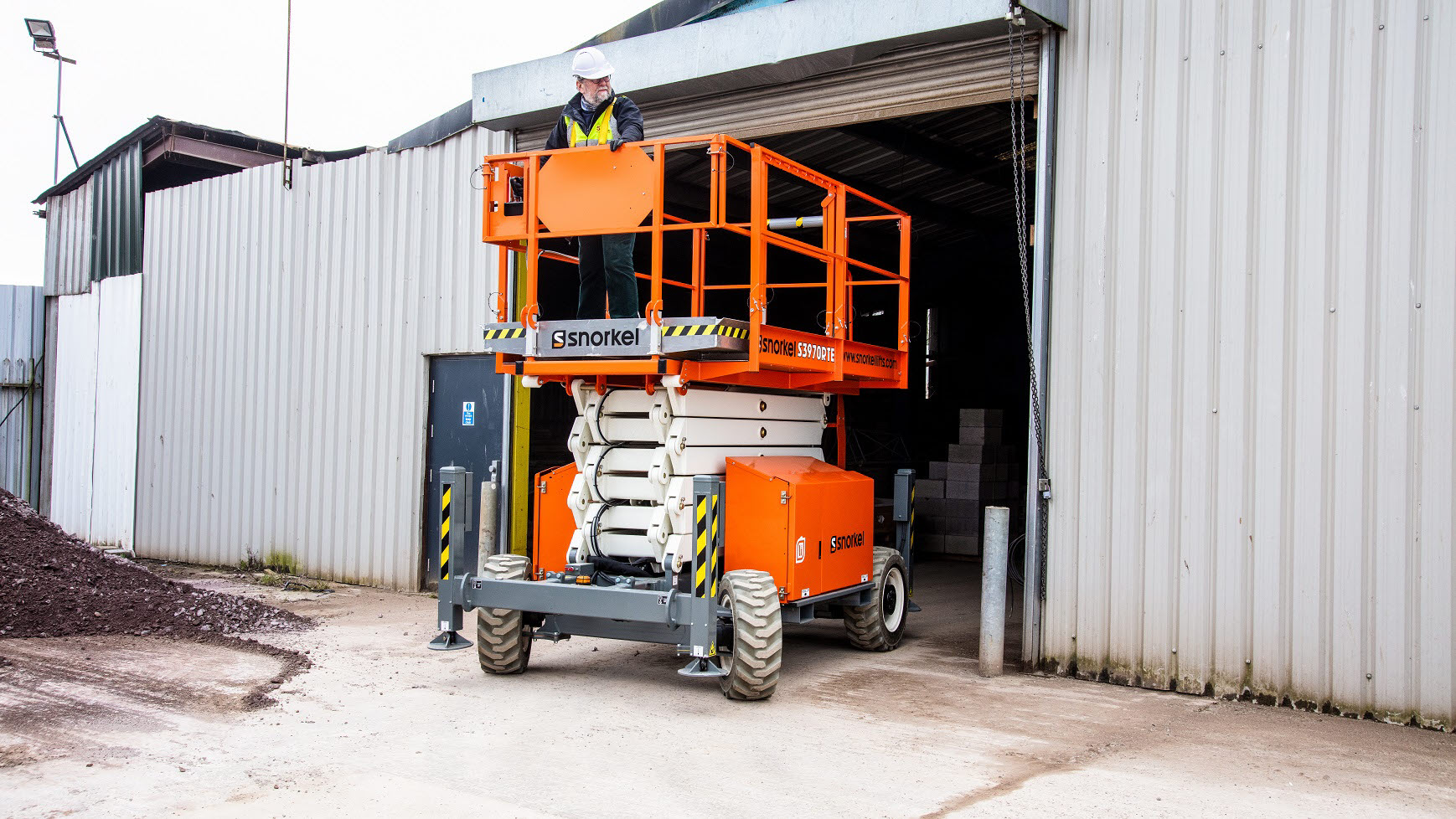
Nevertheless, construction sites must have a recharging infrastructure in place. How and where will machines connect to the power supply, and will the electricity be generated from environmentally friendly sources?
Certainly, hybrid generators with high-capacity batteries topped up by solar panels or wind turbines might form part of the solution to provide power at times other than demand peaks. But such considerations need to be factored into a site set-up.
Again there are similarities here with electric road vehicles. For users with a convenient charging system in place and with appropriate mileage demands they are a viable, green solution. However, for long-distance driving, clean diesel may be more practical. And it’s similar for heavy earth-moving requirements.
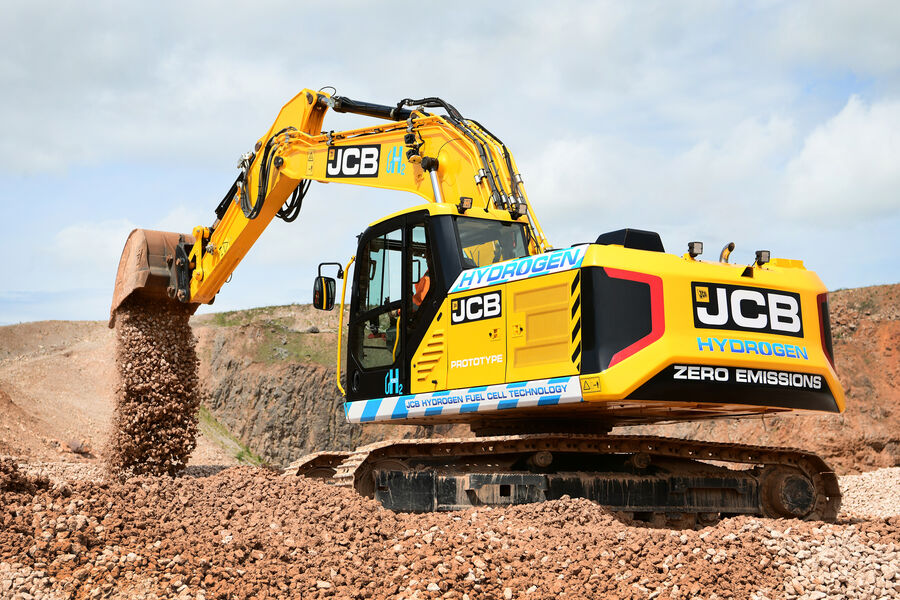
Manufacturers also face challenges in switching to producing battery variants while phasing out conventionally powered counterparts. And if all users wanted to replace their diesel machines with electric models, supply at current levels would not be able to keep pace. Change will be inevitable, but gradual.
Therefore, a range of power sources will likely be needed to achieve net zero targets. Indeed, many people see hydrogen fuel playing a key role, particularly for high-power requirements.
The removal of the red diesel tax rebate this April will make operators look more closely at other fuel sources – which is the government’s intention. Certainly, more construction professionals are using battery-powered plant in their fleets and lowering their carbon footprints in the process.
Nevertheless, many hirers and users have relatively young diesel machines in their fleets and will not want to replace them soon. That’s one reason for such strong interest in HVO (hydro-treated vegetable oil) as a direct drop-in replacement for diesel that can reduce greenhouse gas emissions by 90%.
All power options will be needed in the short-to-medium term if we are to achieve net zero cost effectively and practically.
The Construction Plant-hire Association’s 2021 Conference focused on environmental solutions using various power sources and it will likely be a theme again this year. There will doubtless be plenty to discuss there, and in the pages of Construction Management as new developments unfold.
Kevin Minton is chief executive of Construction Plant-hire Association (CPA).