A King’s Cross mixed-use development was the first project management role for BAM’s Emily Hoggins. Live rail tunnels, a unique roof design and a pandemic ensured it posed plenty of challenges
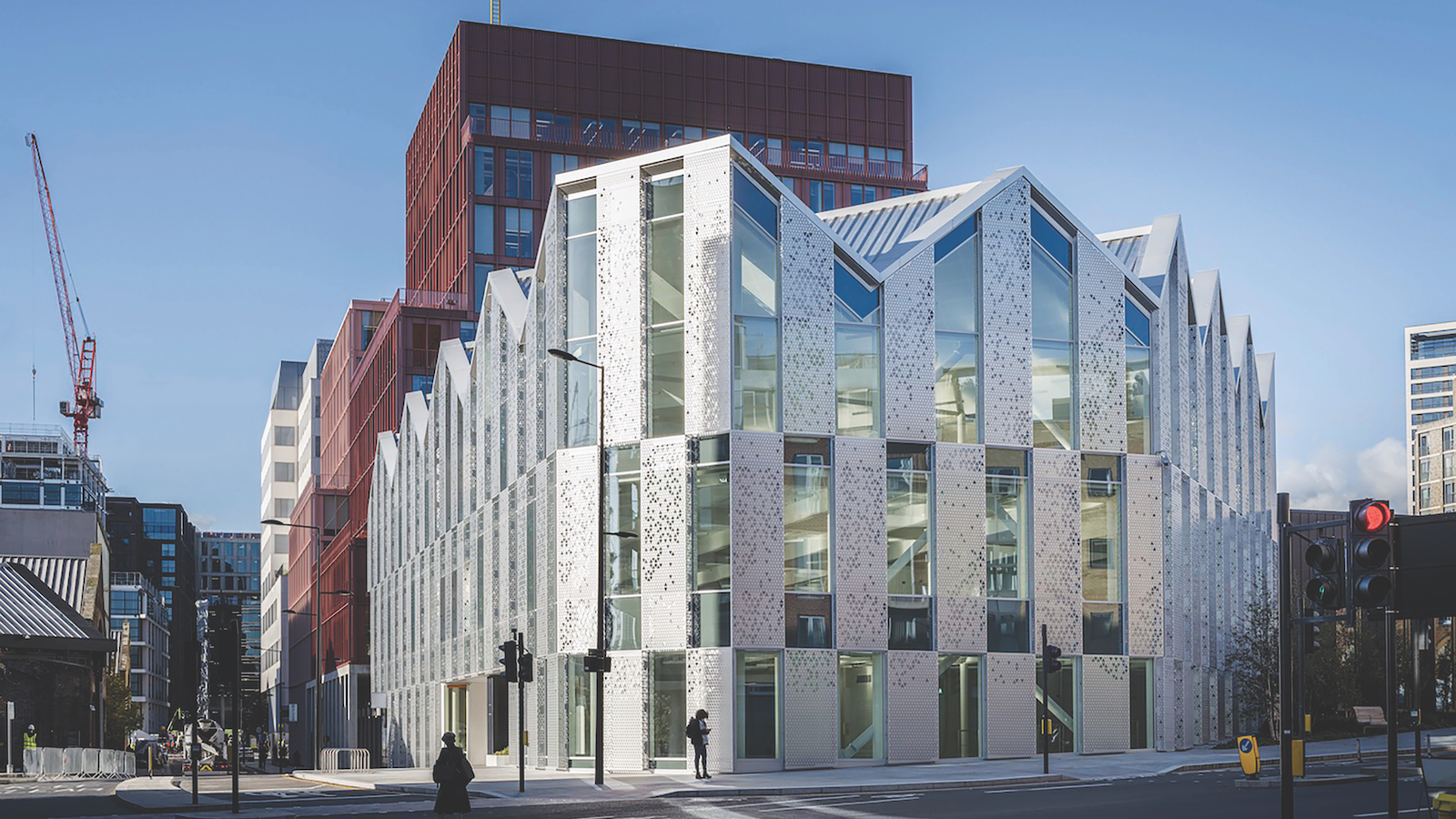
N1C, the brand new postcode for the regenerated King’s Cross, is welcoming its latest addition in the form of mixed-use development Q1 at 22 Handyside Street.
This build is one of 50 new and refurbished buildings that make up the biggest mixed-use development in single ownership in central London for over 150 years. Residents include Google and Universal Music – and Facebook is soon to move in.
Built by BAM, Q1 offers 36,000 sq ft of office space with retail units on the ground floor. The commercial building sits above Network Rail’s three Gasworks Tunnels, which run 1m beneath it, on the corner of York Way and Handyside Street.
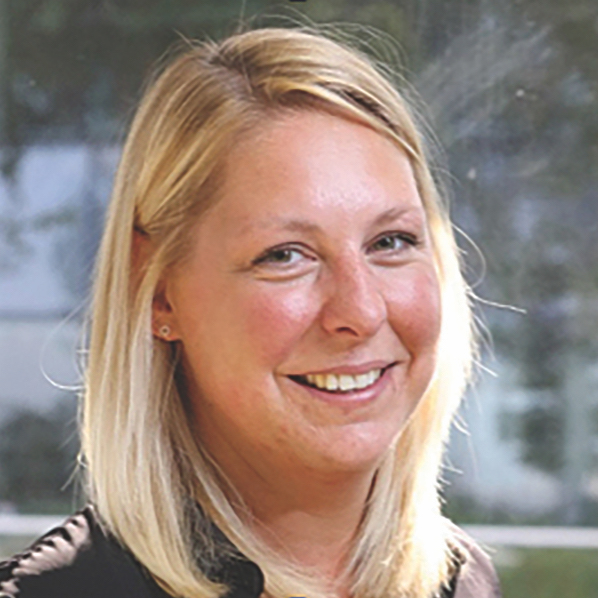
Construction manager CV: Emily Hoggins
Emily has worked in construction for 12 years with BAM since joining on a university placement. She has worked on King’s Cross projects for 10 years, including the University of the Arts, the £145m Western Transit Shed and the £49m Aga Khan Centre, before taking on her first project management role on King’s Cross Q1.
Coffey Architects’ building design captures light cleverly but its shape was born out of the constraints of the tunnels. The building’s form is determined by three factors: the position of the sun, the site perimeter and the site’s structural grid. Sitting above Grade II-listed railway tunnels, it needed to be super lightweight. Responding to these elements, Coffey Architects shifted the three-storey building diagonally. This helped balance the weight of the building while improving the orientation for heat gain, directional flow and outward views.
But what this design and the position over tunnels also did was present technical challenges for BAM and Emily Hoggins, who oversaw the build in her first role as project manager.
“It was built over three Network Rail tunnels – two of which were live – so we needed a specific construction methodology. The tunnels are Victorian brick built, so any product over them had to be lightweight,” she explains.
22 Handyside Street is built of lightweight concrete and steel. The steel frame was designed by Arup, which also helped devise a construction methodology working in 7m sections to avoid too much heave on the ground, with the lowest point 800mm from the crown of the tunnels. BAM built 750mm-deep strip foundations with a bespoke lightweight concrete with stringent QA procedures, and Jablite infills.
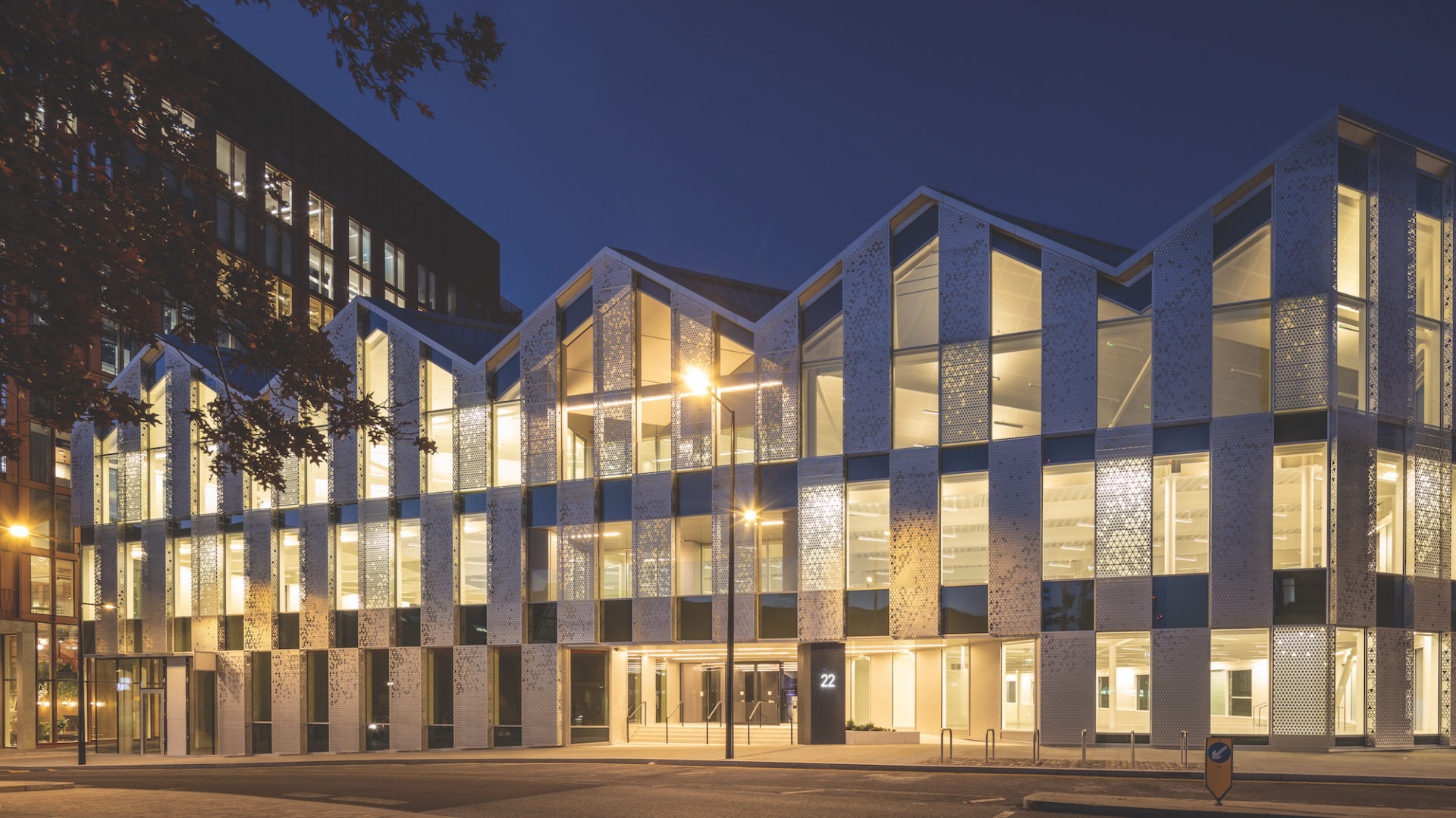
The bespoke concrete was essential to meet the weight restrictions – to ensure it was light but strong.
“We used Socotec and had it weighed and quality checked. As we were so very close to the tunnels, we had it constantly monitored with readings every 15 minutes and designed to send out alerts 24 hours a day – even at 2am on a Saturday night,” says Hoggins.
“It was my first project as project manager and it was a big step up. I had to look at every element from design and planning to build”
It took over a year to develop the strategy and methodology for this challenge, which had a nine-week programme. Hoggins says BAM worked closely with the project partners – Network Rail, the King’s Cross Estate, Arup and Argent (which has managed the regeneration of King’s Cross since creating the masterplan in 2001).
The unique roof design – a pitched roof form with a diagonal emphasis following the lines of the tunnels – was also tricky. “The complicated standing-seam pitched roof had eight valleys at a 45-degree pitch – all angles and twisted roof steel,” Hoggins explains.
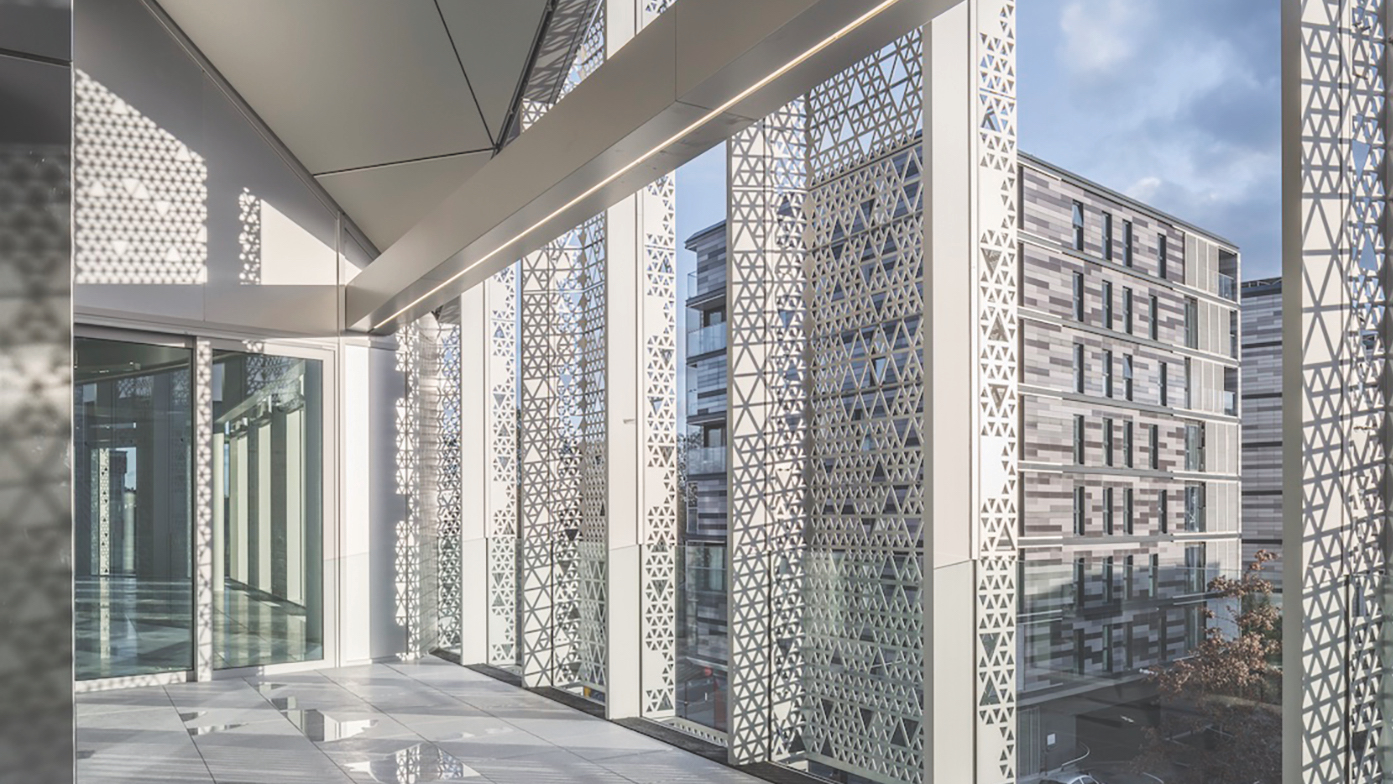
“The installation was difficult – even getting a handrail there was a challenge with the geometry. Ensuring it was safely installed was tricky. The copings were a challenge too due to the pitch of the roof, so had to be modelled, individually laser cut, bent and then dipped.”
The building boasts a facade composed of glazed curtain walling and embossed and perforated anodised aluminium panels and is on target for BREEAM Outstanding.
Testing times
As if the build couldn’t present enough challenges, along came covid. Inevitably it delayed progress – Q1 was at fit-out stage when lockdown happened in March, with completion due on 20 July.
Project team
Client: King’s Cross Central Limited Partnership
Principal contractor: BAM
Structural engineer: Arup
Architect: Coffey Architects
Subcontractors:
Facade and roof: Fleetwood Architectural Aluminium
Steel frame: B&K
Raised access floor: Kingspan
Drylining: Wallrite
Valchromat: Calanpoint
MEPH: Michael J Lonsdale
Carpentry: Atlantic Contracts
Lifts: KONE
Glazed screens: OAG
“We stopped for a week and then put into place safety, welfare and hygiene measures, which included one-way walkways and raising RAMs (risk assessment method statements),” says Hoggins. “We got back to 40% productivity and adapted as the guidance changed until we got back to maximum productivity. We completed, with only a 12-week delay, on 19 October.”
She attributes riding out this challenge to good understanding between parties. Having worked on King’s Cross projects since 2010, Hoggins already had a relationship with Argent – “I knew their way of working,” but adds “I really appreciated the relationships with partners, especially when covid hit. We relied on our subcontractors hugely but we all pulled together and made it move forward safely. There were different operating procedures and details but working in a close-knit team made the difference.”
Throughout, Hoggins says her biggest task was quality management – a new demand as project manager, having previously worked at senior site manager level, but one she has clearly met successfully. The build received critical praise and is now fully let.
“It was a big thing for us and as project manager I had to ensure quality standards were adhered to. It was my first project as project manager and it was a big step up. I had to look at every element from design and planning to build. I was in at the deep end.”