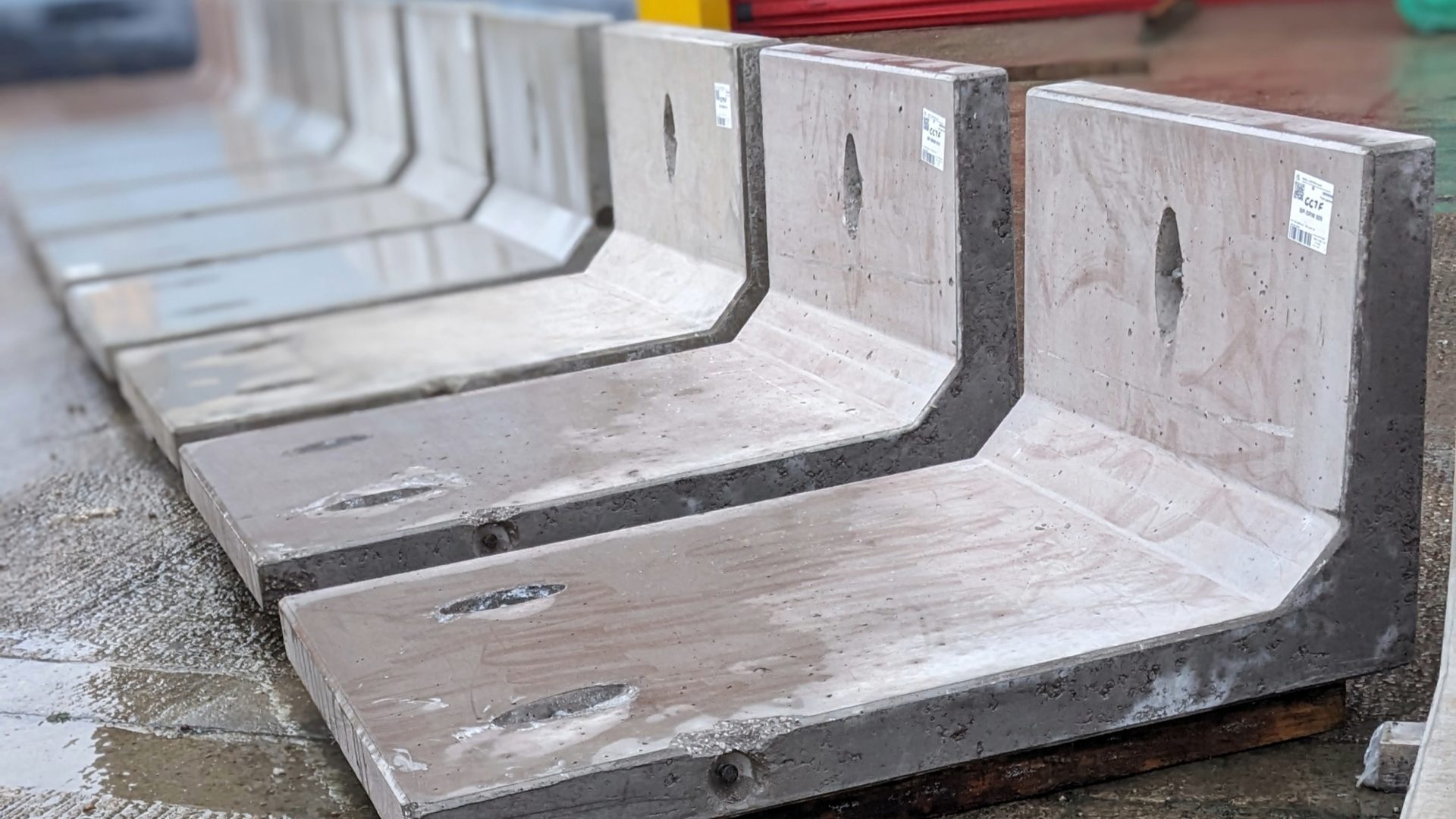
Using waste clay and brick in concrete production could reduce the material’s embodied carbon by up to 30%.
The finding is the result of a two-year study led by the Mineral Products Association (MPA), backed by Tarmac. It shows that UK reclaimed clays and finely ground brick powder can be used as calcined clays in cement and concrete manufacturing to deliver lower emissions compared with the market-leading CEM I cement.
The research also confirmed that calcined clays from these sources have the potential to divert 1.4m tonnes of material from potential waste streams if they were adopted by the UK construction industry.
Two heating methods were trialled to prepare the clay for use in cement and concrete: commonly used rotary kilns, and the more innovative ‘flash heating’. Both methods have been shown to produce high-quality calcined clays with no significant difference between techniques.
Potential for a whole new market
Clay is naturally abundant in the UK and can offer an alternative to industrial by-products such as ground granulated blast-furnace slag and fly ash, which have been traditionally used to lower the embodied carbon of cement.
The ongoing decarbonisation of the UK power and steel industries is resulting in a reduction in the production of both of those materials.
In other parts of the world, calcined clays are used as a secondary cementitious material, but until now they have not been officially tested in the UK.
Dr Diana Casey, executive director of energy and climate change at the MPA, said: “Using brick waste and reclaimed clays will not only lower carbon and reduce waste, but has the potential to create a whole new market if these clays become widely used in the construction industry, helping to retain economic value in the UK, secure jobs and attract investment.”
The study has been supported by Heidelberg Materials UK, Tarmac, Imerys Minerals Ltd, Forterra, University College London and the University of Dundee, with funding from the government’s research body Innovate UK.