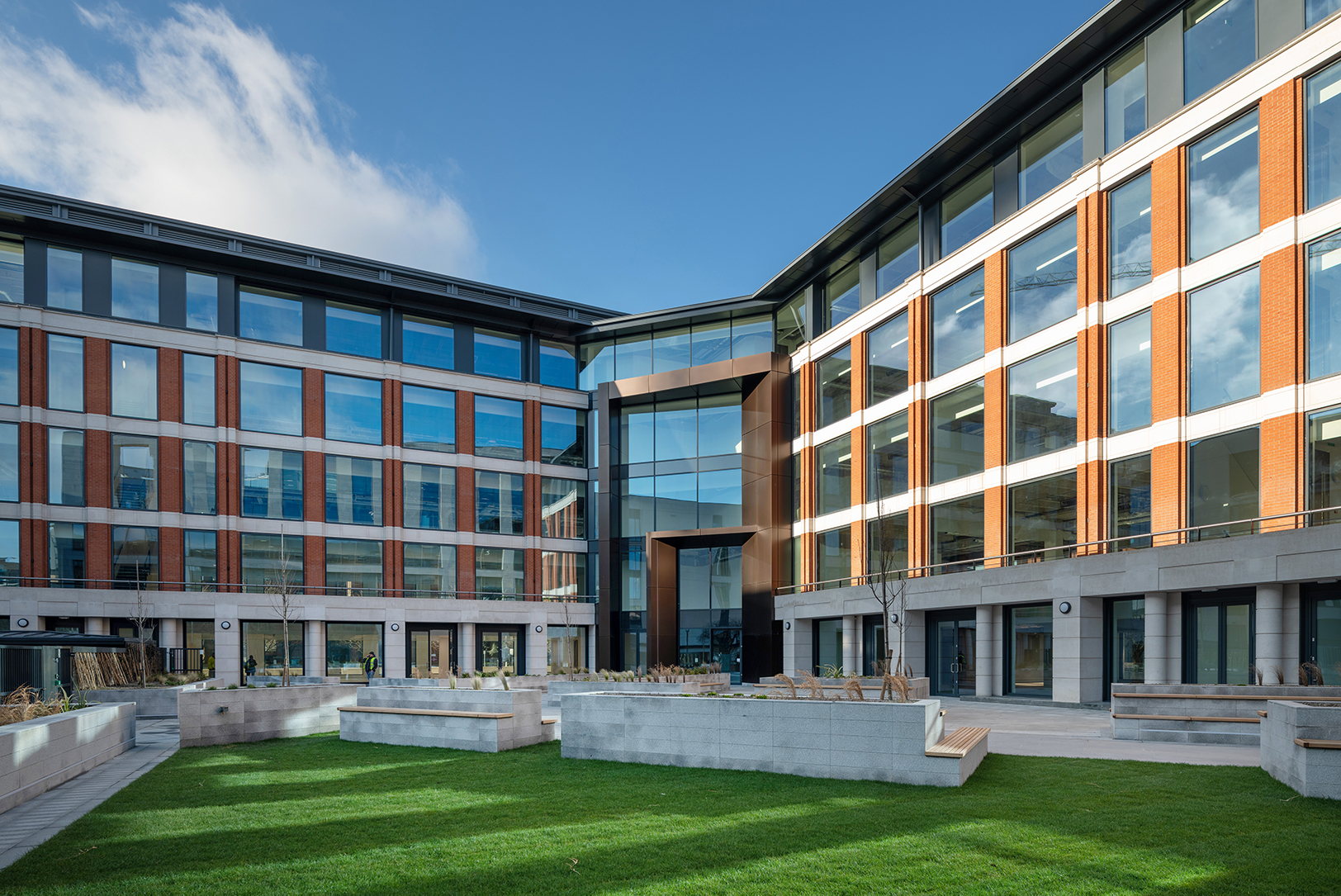
Curing is the final step in concrete construction, often utilising surface-applied curing compounds to retain moisture and promote proper hydration. However, these compounds can interfere with the adhesion of hot melt waterproofing systems, potentially compromising the bond needed for a waterproof, monolithic layer across the deck.
When cement mixes with water, it undergoes hydration, which hardens, strengthens and stabilises the concrete. Without adequate moisture retention during its drying process, the concrete may not achieve its intended strength. After pouring, surface-applied curing compounds can be used to help prevent premature water loss, supporting the hydration process and ensuring a successful finish.
Surface-applied curing compounds are popular due to their ease of use and cost-effectiveness, though they may pose compatibility issues with hot melt systems or bitumen air and vapour control layers (AVCLs). Their necessity can depend on environmental conditions, as warm or windy weather often accelerates drying. British Standards (BS EN 13670:2009) specify that curing compounds should not be used on surfaces where bonding of other materials is required unless proven harmless or fully removed beforehand.
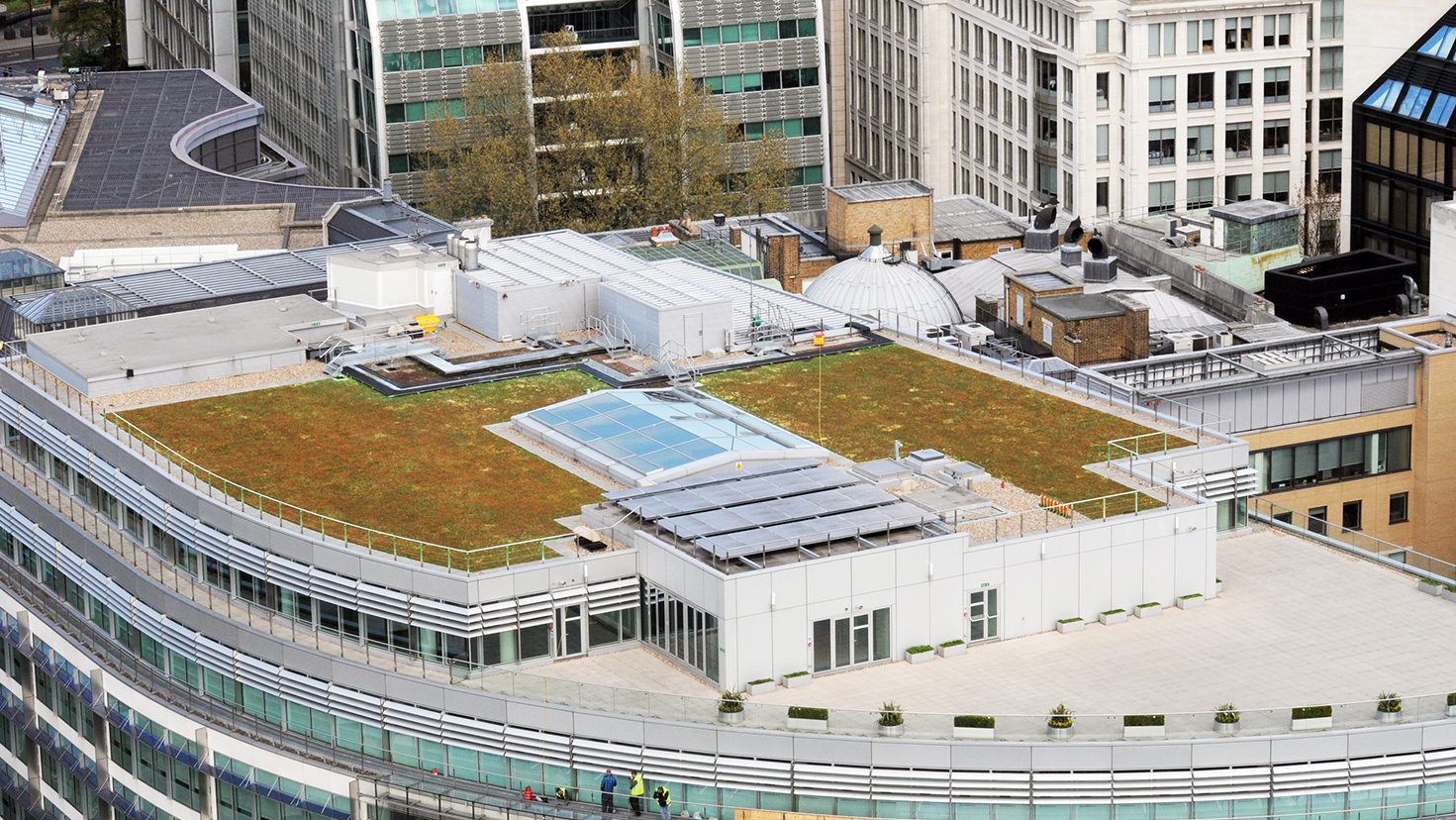
Compatability considerations
Compatibility with hot melt waterproofing is generally better with pure sodium silicate-based surface-applied curing compounds. However, other types including resin-based, wax-based, wax/resin-based, acrylic and chlorinated rubber-based surface-applied curing compounds may impair bonding, posing risks to the waterproofing integrity.
Consideration in using these incompatible compounds requires consultation with the manufacturer’s technical team for removal methods to avoid creating a barrier between the cured concrete and the waterproofing.
It should be remembered that the feature of any hot melt waterproofing system is that it can be bonded adequately to the fully cured in situ concrete deck. A properly bonded hot melt system results in a monolithic waterproof skin, preventing water ingress, which is critical when covering the roof with insulation or landscaping.
If incompatible curing compounds go unreported, the waterproofing system’s bond to the concrete could be compromised, leading to potential water-tracking issues and failed adhesion tests.
Curing compounds create challenges for roofing contractors, as they can be hard to detect. Smooth surfaces or failed peeled bond tests may indicate their use. Bauder advises open communication between contractors and waterproofing manufacturers whenever curing compounds are employed to prevent unforeseen costs and complications. If curing compounds are added last-minute, it’s cost-effective to remove them post-curing, before waterproofing begins.
To avoid complications, specifiers and contractors should consult waterproofing manufacturers during the planning stage to evaluate potential effects of curing compounds.
Bauder supports its contractors through guidance and training on these matters. For more information, visit bauder.co.uk or call 01473 257671.
This article has been produced in partnership between Construction Management and Bauder.