Since July 2019, at a historic residential building overlooking London’s Hyde Park, CIOB chartered company member and heritage specialist Rosewood has been working on a complex facade restoration project. CM reports.
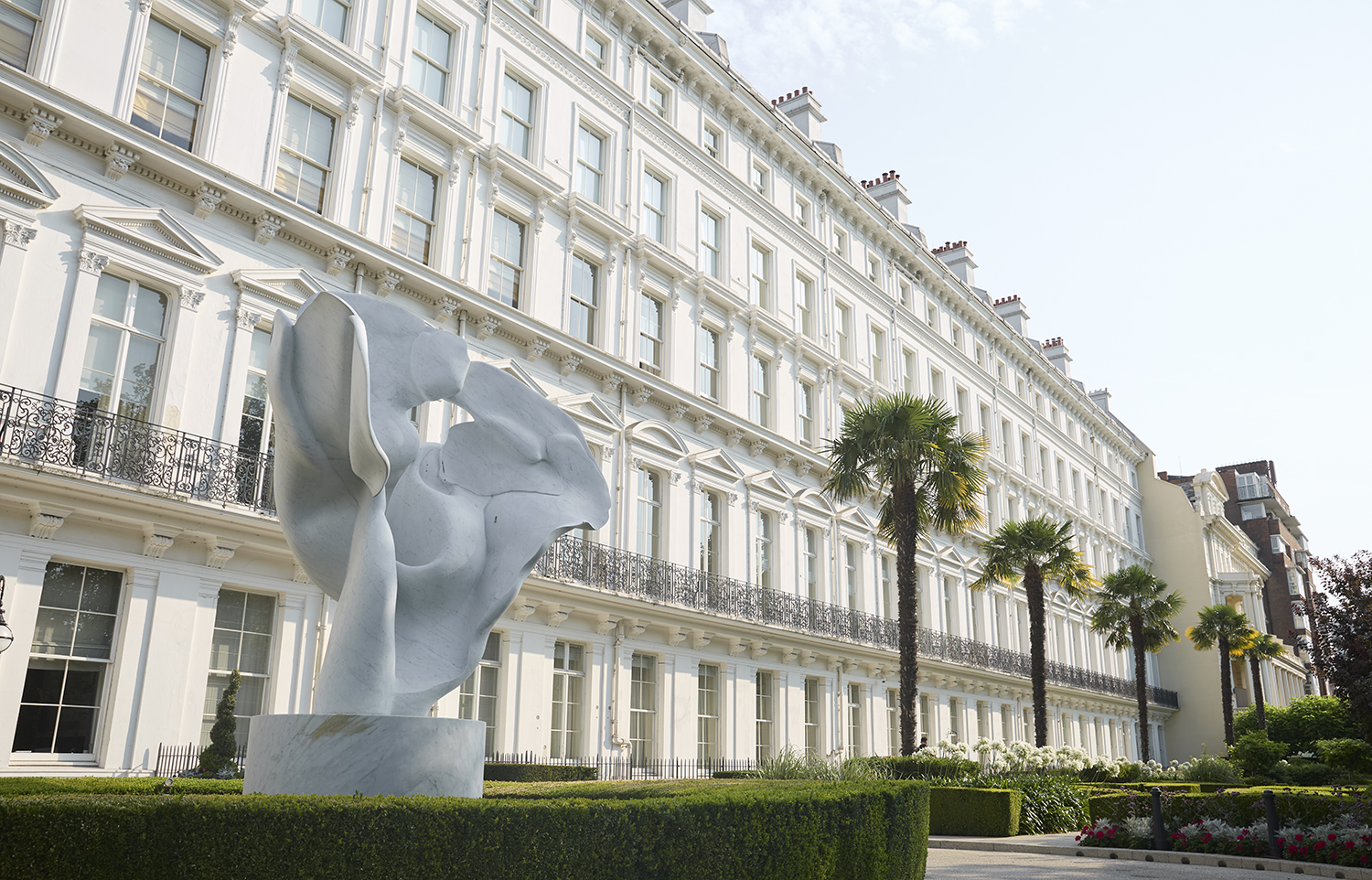
The Lancasters sits in one of London’s most exclusive postcodes. Grade II-listed and built between 1856 and 1865, this French neoclassical style terrace of 15 ambassadorial residences in W2 has spectacular views across Hyde Park, with elevations on Lancaster Gate, Leinster Terrace and the Bayswater Road.
The terrace underwent significant redevelopment over a decade ago, with the internal floors and walls demolished and a new concrete-framed replacement structure built in their place, but the French neoclassical facade was retained.
More recently, heritage specialist and CIOB chartered company member Rosewood has been working on what is the largest stucco facade restoration project on a single residential block in the UK.
“It demonstrates our ability to work on large-scale, complex heritage projects,” says Nick Austen-Smith MCIOB, contracts director at Rosewood.
The project began in 2019, just before the Covid-19 pandemic. The scheme includes stripping of the lead-based paint, structural brickwork and the replacement of failed structural ties, stucco restoration to the entire fabric of the buildings, joinery and decoration. The programme was due to be completed within two years, but this was extended due to the volume of works uncovered.
The Lancasters, Hyde Park: project overview
Principal contractor: Rosewood
Restorer and stone fixer: Rosewood
Joinery: Rosewood
Decorations: Rosewood
Structural engineer: Hockley & Dawson
Specialist fixing engineer: Harrison Goldman
Contract administrator: EBW Consultants
Project manager: Arambol
“We have a collaborative and open-book working policy, involving Rosewood, the client, project team and stakeholders, and as issues of the past emerged the programme was extended to a fifth year on site,” says Austen-Smith. “We are seeking to complete by August 2024.”
Removal of lead paint
Rosewood commenced with the removal of the lead-based paint on the facade, using specialist water and media-based cleaning methodology. This is a complex process which requires careful disposal of the lead paint. In 2018, the contractor created 12 cleaning samples for the Westminster Council conservation officer and the client to demonstrate that only the paint would be removed and the stucco facade remain in its original detail.
“The different encapsulation methods ensured that no paint escaped the confines of the scaffold,” explains Austen-Smith. “These included a shrink wrap to the scaffold, negative internal air pressures so the fabric was not affected and vacuum systems on the scaffold to draw all debris into waste units ready for collection.”
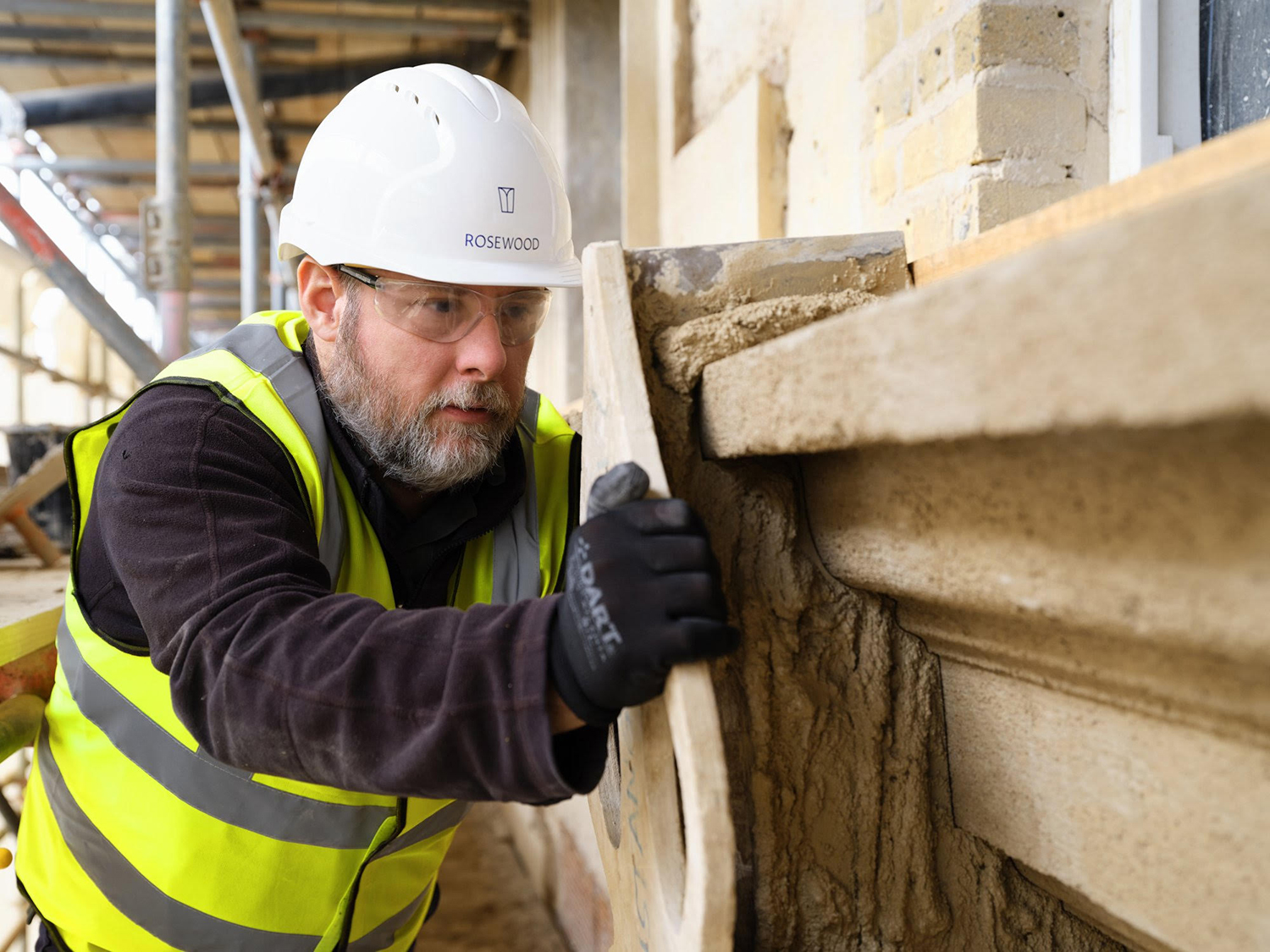
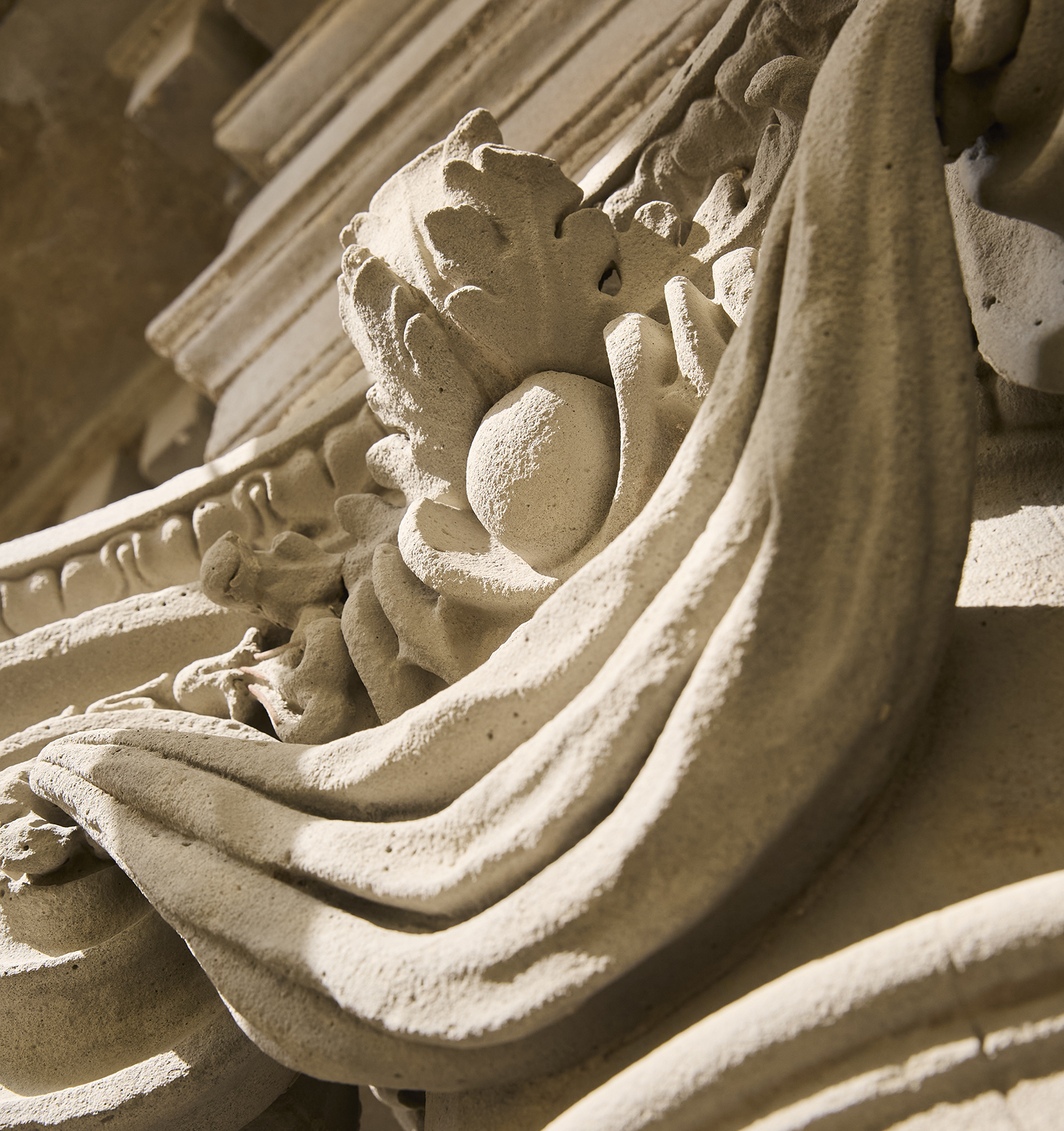
On completion of the paint removal, Rosewood carried out a survey to all the stucco – with any failed stucco removed – followed by surveys of the inner structural brickwork, once exposed.
“These surveys allowed us to map out each and every repair to the structure of the building and its highly decorative facade,” says Austen-Smith.
“The like-for-like repairs and replacement work involved classical methodology, including the use of horse moulds to re-run the cornices and window surrounds, the removal of modern concrete lintels to be replaced with classical London stock brick arches as per the original design,” Austen-Smith says. “This allows the building to move as it was intended to.
“We also fitted new detailing where there was complete failure of the capitals, window pediments and arches and the decorative lion heads.”
1,500 stainless steel ties
In tandem with the stucco works, Rosewood’s team structurally rebuilt much of the inner brickwork skin of the structure, while installing over 1,500 stainless steel ties to maintain the connection between the original facade and the modern concrete frame behind.
“We then hand-restored and re-ran, in lime render, the entire stucco facade to match the original Victorian build,” says Austen-Smith.
“Finally, we completed the restoration with a mineral-based paint, spray-applied for the finest of finishes.”
The workforce on the project has ranged from 35 up to 125 on site each day. Rosewood has overseen a stringent quality assurance scheme, says Austen-Smith.
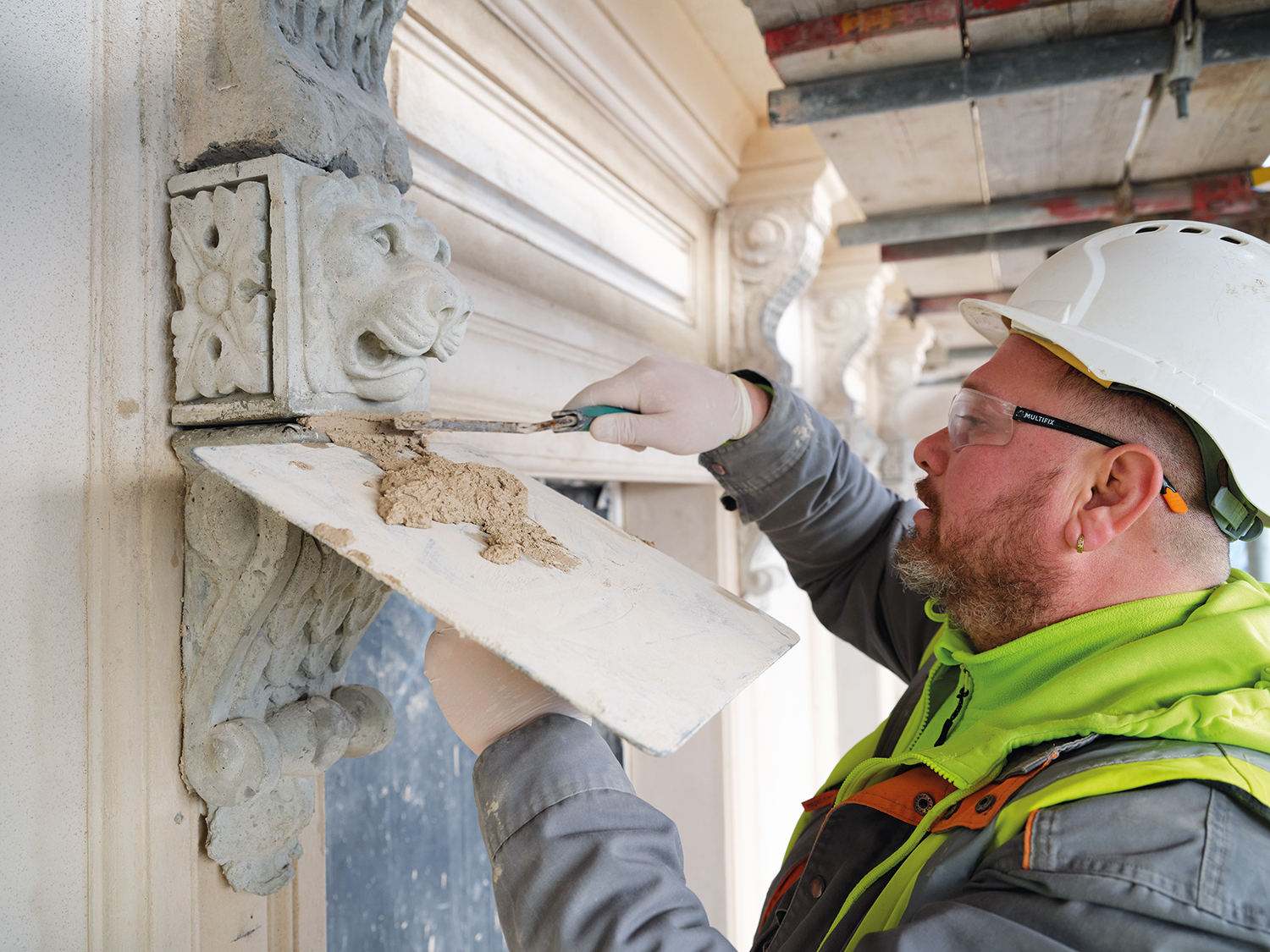
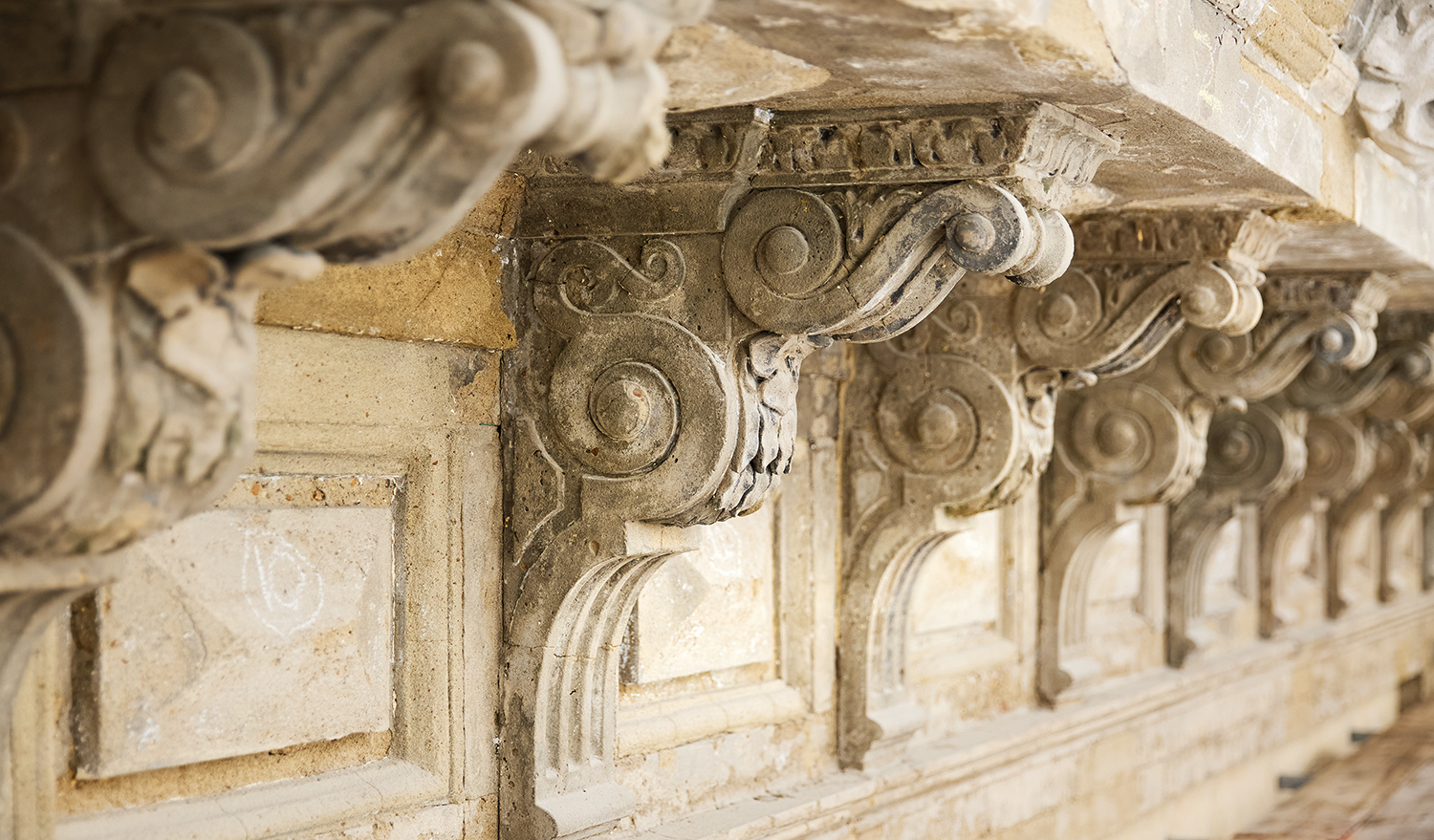
“Each trade has their respective foreperson to oversee the quality assurance which feeds up to the project manager and senior management team prior to handing over to the client,” he explains. “At Rosewood we have an in-house clerk of works, which is a little old-fashioned but ensures quality is always at the forefront of what we do as a principal contractor.”
Heritage apprenticeships
However, the greatest challenge for Rosewood on the project has been sourcing skilled labour.
“So that we can continue our strong heritage of apprenticeships, we have been training throughout our four-and-a-half years on site and will continue to do so,” Austen-Smith explains.
Eddie McFadden, Rosewood logistics director, has headed up the apprenticeship scheme. He notes: “During the project, eight restoration apprenticeships have been completed plus two NVQ7 management qualifications, which is testament to our investment in the future of Rosewood and the heritage sector.”
The ongoing training of skilled labour is “paramount” to Rosewood, adds McFadden and, as the works on The Lancasters come to a close, all of the team will move on to other projects in the company’s portfolio.
Rosewood managing director John O’Sullivan adds: “I could not be prouder of the company’s effort throughout this project. It is testament to all involved and the quality of the works produced demonstrates our expertise as a principal contractor.”
As the project developed, the complexity and diverse challenges allowed the Rosewood team to showcase the works, organising 12 walking tours of The Lancasters for surveyors and engineers, which will help Rosewood build on current and future relationships within the heritage market.