The Thame Valley Viaduct on HS2 is being built from giant precast blocks weighing up to 90 tonnes. Hamish Champ watches as this offsite manufacturing marvel is slotted together.
A couple of miles north west of the Buckinghamshire town of Aylesbury, the UK’s longest – and the country’s first – factory-made railway viaduct is slowly taking shape, like a giant Lego set.
Comprising 72 precast concrete beams, each 25m long and weighing 90 tonnes, arrayed across 36 spans and supported by 68 factory-manufactured piers each weighing 42 tonnes, the Thame Valley Viaduct is being slotted together with millimetre precision.
When it’s finished, the 880m-long structure will carry a stretch of HS2’s London to Birmingham route across the flood plain of the Thame Valley.
HS2 North Chilterns to Aylesbury section: key projects
24km of high speed line
18 overbridges
Five underpasses
Three viaducts (including the Thame Valley Viaduct)
Five major road realignments
One Network Rail realignment
Earthworks: 6.6 million cu m excavation/8.3 million cu m fill
The viaduct forms part of a section of the high-speed railway line – technically labelled the C2/3 Programme – currently being constructed between the Chiltern Tunnel and Long Itchington Wood in three distinct lengths: North Chilterns to Aylesbury, Twyford to Greatworth, and Greatworth to Southam.
At 80km long, the C2/3 project can reel off some impressive statistics: 81 bridges, 15 viaducts, 7km of green tunnels, 22km of road diversions, 330ha of landscape planting and a whopping 30 million cu m of excavated earth.
The government may have controversially pulled the communication cord on the section of the line from Birmingham to Manchester, but contractors and engineers remain extremely busy with – and committed to – the rest of the HS2 project.
Around 6,500 people are working on the C2/3 programme, and 60 are employed on the Thame Valley viaduct, which is being built along the North Chilterns to Aylesbury section.
The viaduct was designed by HS2 Ltd’s main contractor, EKFB – a team made up of Eiffage, Kier, Ferrovial and BAM Nuttall – along with a joint venture featuring Arcadis, Setec and Cowi. Onsite assembly of the precast sections is the responsibility of Ferrovial subsidiary FC Civils Solutions.
Near to the ground
Crossing an extensive flood plain to the north and west of Aylesbury, parallel with the A41, one might have expected the viaduct’s design to be “a sexy tall one, maybe 25 or 30m in height”, says Ignacio Chicharro, EKFB’s project director for the HS2 Aylesbury Area.
Instead, the end result will appear to skim just above the surface of the waterlogged fields to blend in with the landscape. The underside of the finished viaduct will be a mere 3m above the ground, supported by piers which sit atop 45m-deep piles.
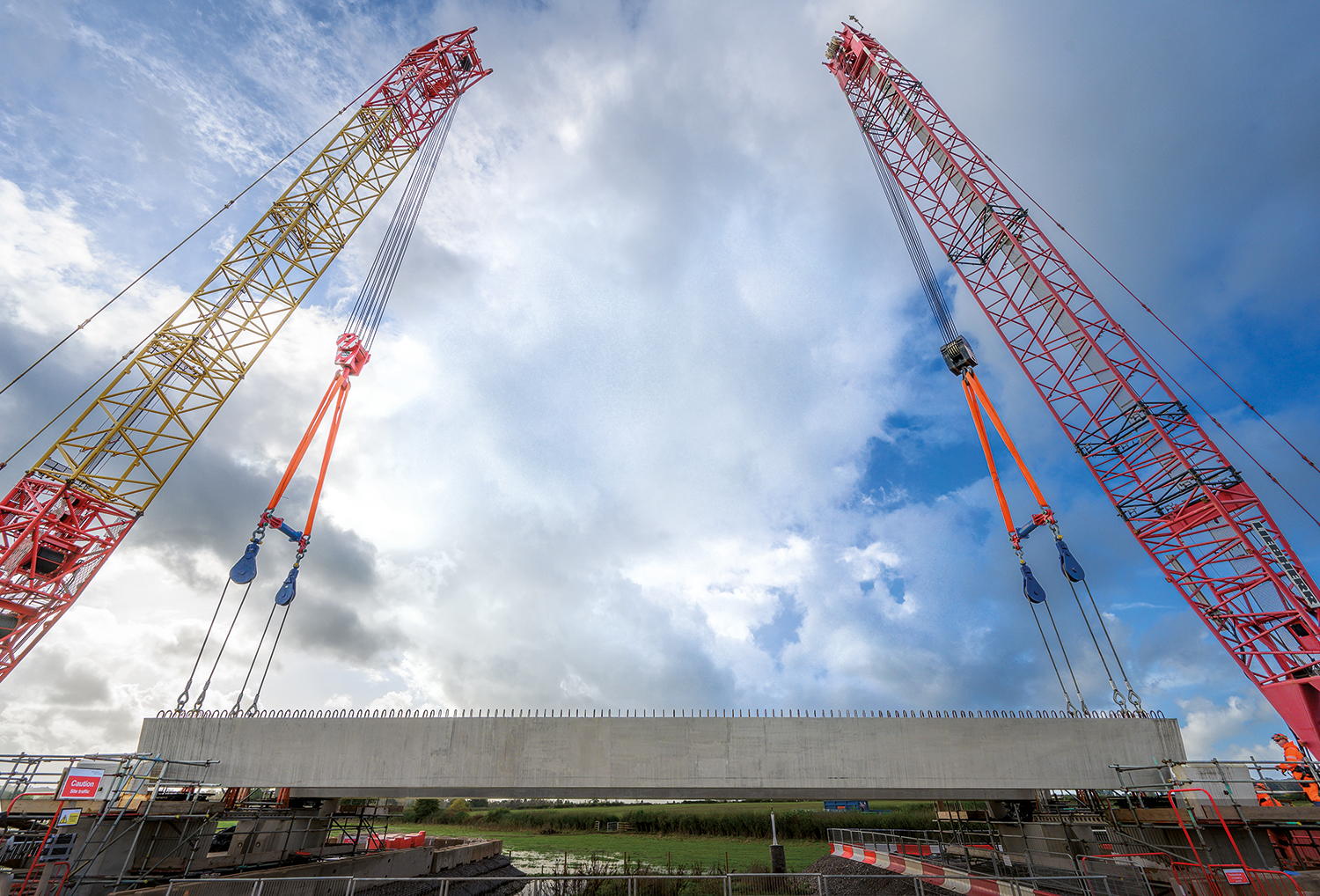
Chicharro says initial concepts for the viaduct would have involved a high degree of temporary works, including propping for beams. But research into alternative solutions for the site led to a simpler approach being adopted.
Typically, viaduct beams are connected via a concrete diaphragm, which is cast in situ. However, the precast beams on the Thame Valley Viaduct are secured directly to one another, removing the need for the diaphragm. Meanwhile, the deck on top of the beams, which will carry the actual rail track, is also made from precast planks. Every major element of the structure – the piers, beams, deck planks and parapets – is being prefabricated and slotted together.
Lighter structure
HS2 says this will make the viaduct a lighter structure, which is expected to save 19,000 tonnes of embedded carbon versus the previous design, cutting its carbon footprint by around a third.
“The design we are using is a more efficient structural solution,” says Chicharro. “Delivering components ready to install on site means improved health and safety during construction, a significant reduction of temporary works and a much better quality of product.
“It also means we can save time on delivery, which means less disruption for the local communities in the area. And as well as the carbon footprint reduction, thanks to the form the viaduct will take, people will see a railway which fits in with the surrounding landscape really well.”
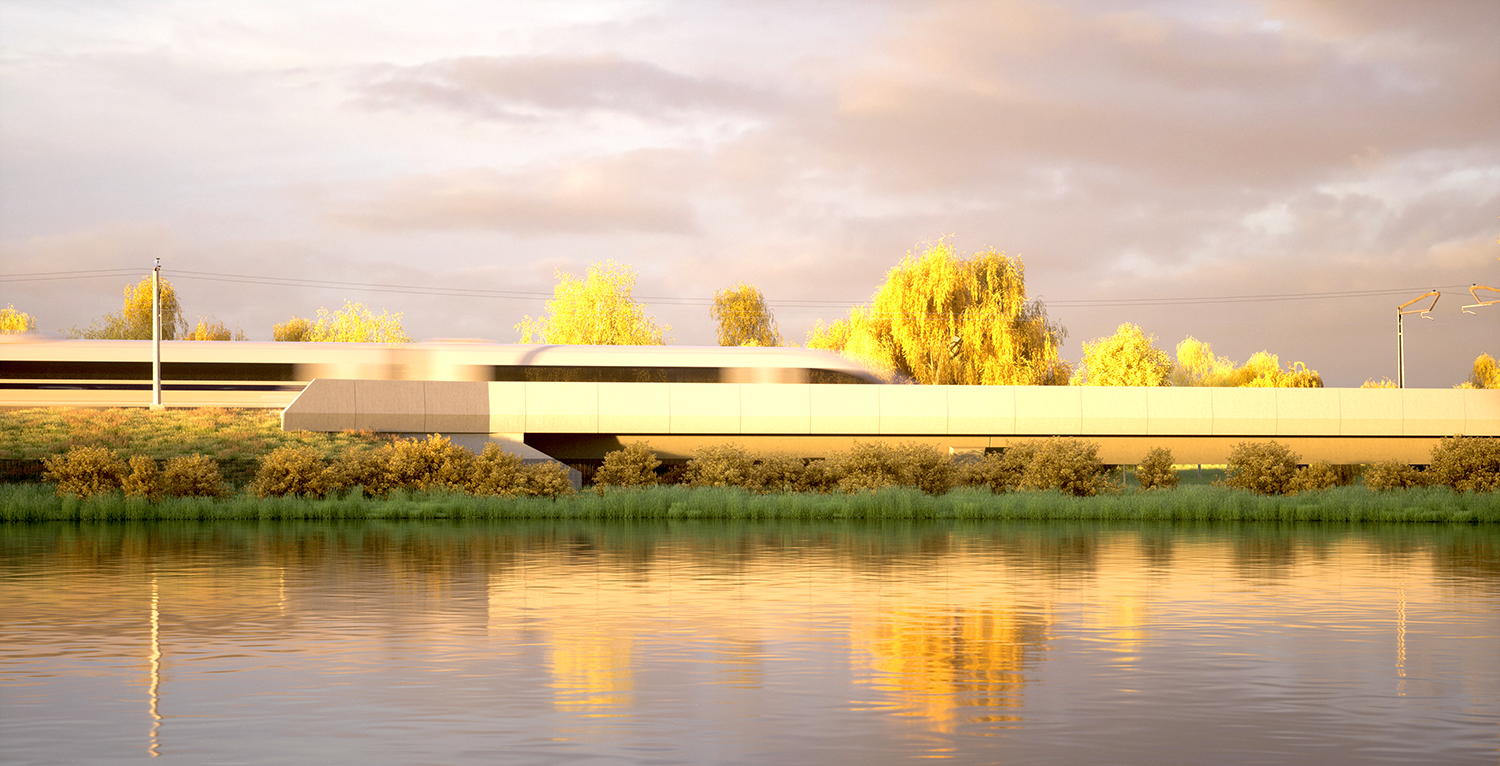
However, the design proposed was quite controversial, since the UK government had imposed a moratorium on building viaducts and bridges using precast components around 30 years ago.
Rigorous approach to quality
The moratorium dates from the early 1990s, when HS2’s lead bridge and viaduct engineer David Smith was beginning his career. Back then, there had been issues on some bridge structures with the durability of the joints between component sections, meaning water ingress could be a problem. Europe doesn’t have such a moratorium, Smith notes, “perhaps because they don’t have the same chloride levels and environment as the UK”.
So how did HS2 get around the problem? Smith says his team looked at what the moratorium was trying to address, namely issues like the quality of grout, the expertise of the personnel on site and long-term monitoring of the structure. As a result, the Thame Valley Viaduct takes a rigorous approach to quality and structural integrity.
“The viaduct is designed to last for 120 years, so we have developed a strategy for monitoring the health of that structure over that time, to give us early warnings when things are going wrong, as well as developing techniques to stop things going wrong in the first place,” he adds.
The viaduct’s design was in part inspired by examples developed in Spain, where Ferrovial has its headquarters, and Smith says this expertise was used in developing
the connections for the beams.
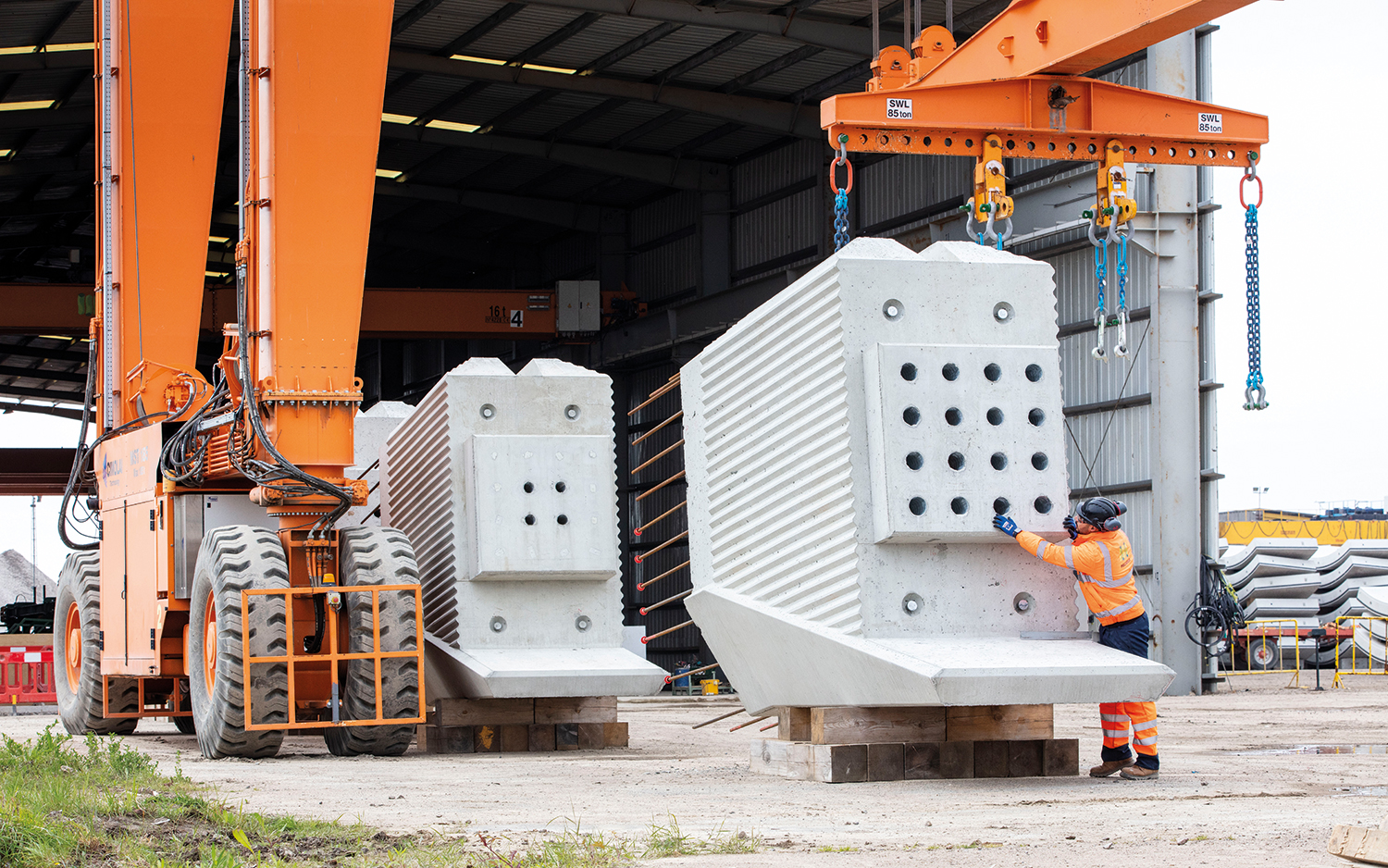
“In our technical specifications and technical standards, we wrote in specific performance requirements to allow this form of construction, so we can ensure an airtight end duct across the joints after they’ve have been connected together,” he explains.
Low maintenance goal
Nothing, Smith admits, is maintenance-free. But the goal is certainly to be low maintenance, so that any repair or assessment activity can be done in a very narrow window to ensure the two lines carrying high-speed trains have minimal interruptions.
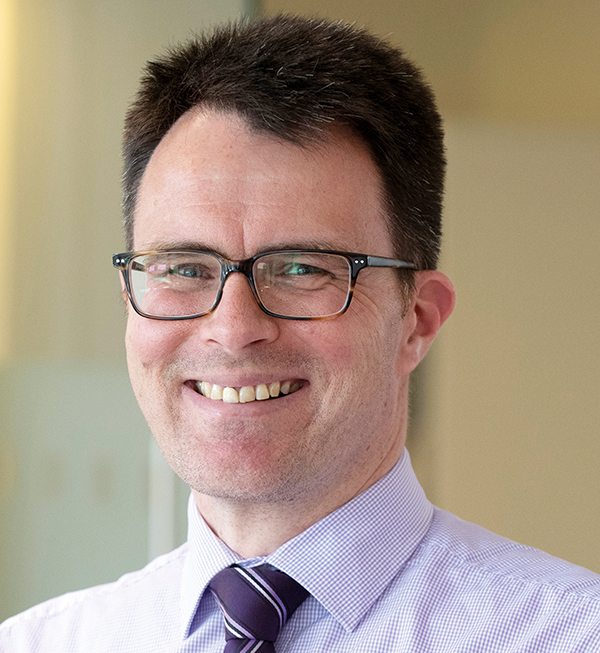
CV: David Smith, lead engineer for bridges and viaducts, HS2
A specialist in bridge engineering, David Smith is currently seconded from AtkinsRéalis to High Speed 2 Ltd as lead discipline engineer for bridges and viaducts throughout the whole route, following his leadership of the viaduct design development in the southern half of the route for the Phase One Hybrid Bill.
A chartered engineer and fellow of the Institute of Civil Engineers, he has more than 25 years’ experience, skilled in the design, assessment and strengthening of steel, concrete and composite bridges and highway, light rail and high-speed rail structures, including the Medway Viaduct in Kent.
Responsible for the development and maintenance of the route’s bridge technical standards and aesthetic design requirements, he is delighted to play a role in delivering the first railway viaduct in the UK to be built using prefabricated concrete components.
“If I achieve nothing else on this project, just showing what the UK can do with regards to precast segmental construction is what I really want to achieve out of it,” he says.
From a construction viewpoint, there are huge advantages to the offsite approach, Smith says.
“The main benefit of having such enormous parts being built in a factory is that you can be much more precise,” he says. “You can use the same adjustable moulds so that they are capable of producing precise lengths of beams. That means greater efficiencies and greater accuracy. So we are able to work perfectly capably with tolerances that are mere millimetres.
“We’ve also saved five, maybe even six months’ worth of construction time compared to a traditional approach.”
The beams and piers are being made by the UK operation of Spanish precast concrete specialist Pacadar, which is also responsible for producing the concrete linings for many of HS2’s tunnels.
Pacadar manufactures the viaduct’s components in huge moulds at its factory on the Isle of Grain in Kent. Once moulded, delivery of the concrete sections is a complex logistics affair. They are transported overnight to the Thame Valley site, four hours’ drive from the factory, to minimise disruption to local road networks.
FC Civils Solutions is charged with installing the huge precast units. This delicate operation involves two huge cranes – one of 300 tonnes, the other 350 tonnes – raising the beams from the flatbed lorries and lowering them onto the piers where they are effectively bolted into place.
Boosting biodiversity
Completion of the Thame Valley Viaduct is expected in the third or fourth quarter of 2025. HS2 says that once the viaduct is completed the floodplain will be enhanced to boost biodiversity and improve flood water management. Work will include replacing existing arable land with new areas of woodland and wetland to promote wildlife.
Smith is excited about the level of innovation that HS2 is facilitating and says he is “passionate about leaving a legacy for the next generation of engineers, and for the next generations of projects”.
The scrapping of the northern section of the HS2 line “was a surprise”, he adds, “but there’s still a lot we can do, and indeed we are doing, across the length of phase one, from London to Birmingham.
“The learning from the design for the Thame Valley Viaduct will be taken forward and used on high-speed rail projects both in the UK and across Europe in future,” he says. The Thame Valley Viaduct design will also be used by HS2 on the nearby Edgcote Viaduct in Northamptonshire.
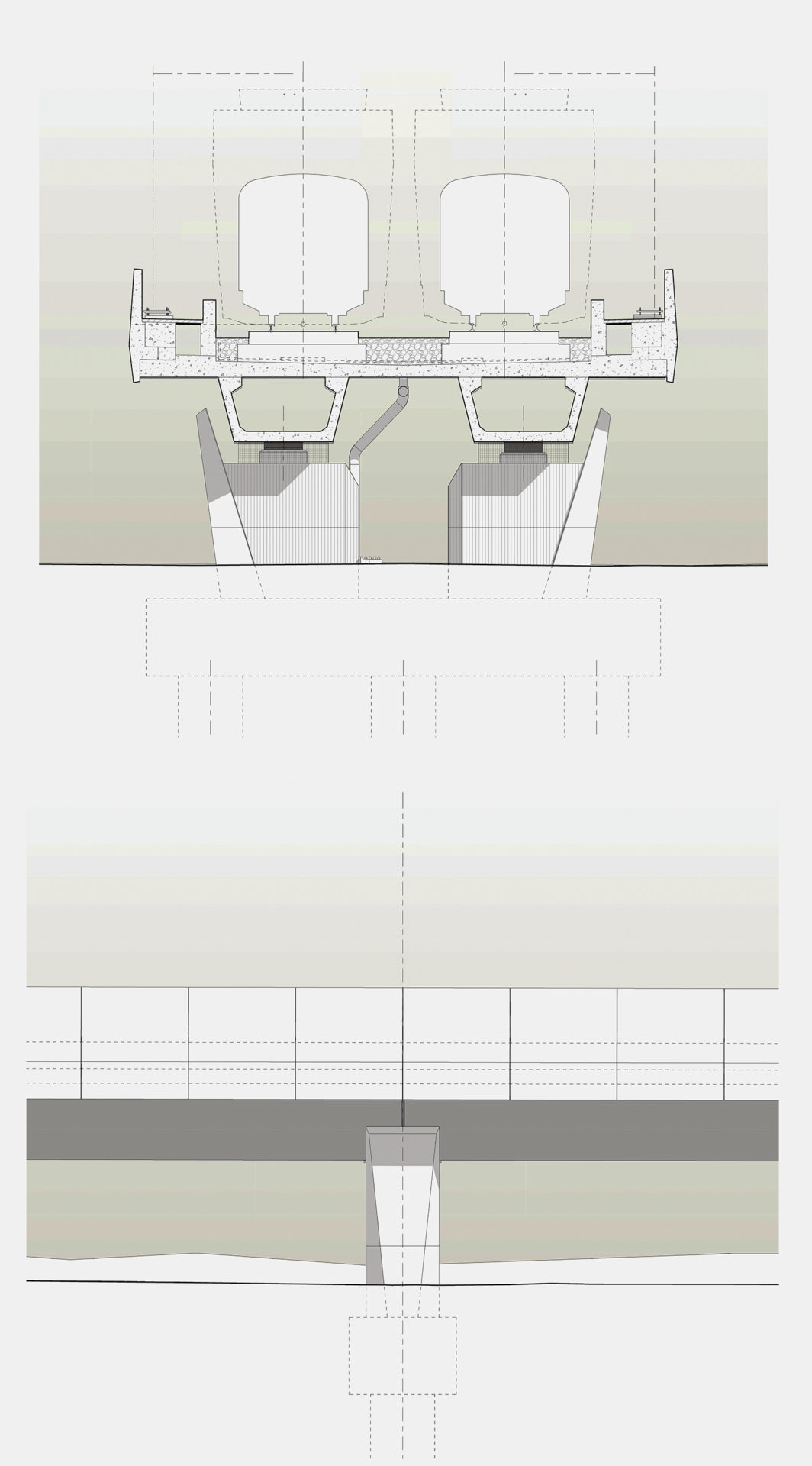