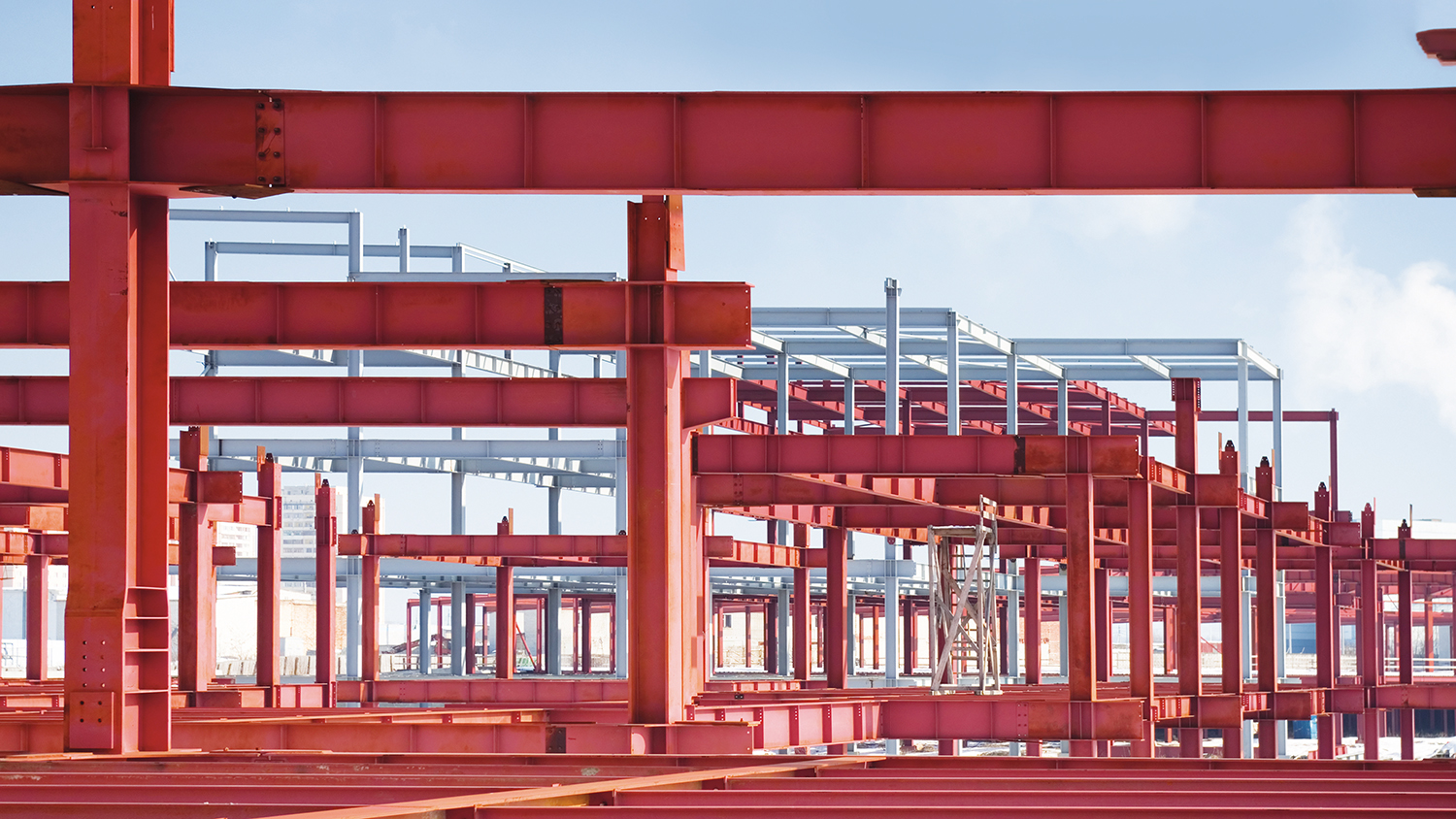
There has been a surge in demand for scrap steel recently – but there are better ways of reducing carbon emissions in constructional steelwork, Nick Barrett says.
Given the pressure on the construction industry to cut carbon emissions, the appeal of specifying scrap steel should come as no surprise.
Steelwork contractors are reporting a significant increase in client requests for steel manufactured using the electric arc furnace (EAF) method, which uses scrap steel, rather than the traditional basic oxygen steelmaking (BOS) process that creates steel mostly from iron ore, although it also uses a moderate amount of scrap steel in the process.
But the British Constructional Steelwork Association (BCSA) advises that simply insisting on EAF steel is not the best way to reduce global carbon emissions, although it is a necessary step towards decarbonising the steel sector.
CEO Dr David Moore says: “Clearly, clients wish to minimise the carbon impact of their projects today, which is a laudable aim and will provide further encouragement to the steelmaking industry to decarbonise.
“However, while EAF steel has a lower embodied carbon than BOS steel today, there is not currently enough scrap to meet the global demand for steel through EAF manufacturing alone. So, while specifying EAF steel for one project will minimise the carbon footprint of that project, it will not reduce global carbon emissions as it will merely displace BOS steel to another project.”
‘Misunderstanding steel manufacturing’
Mark Smith of steelwork contractor Billington Structures says: “Some clients see EAF steel as being more environmentally friendly than the BOS method, but BOS uses a lot of scrap steel itself – approximately 25% of the steel produced by BOS is from scrap. Scrap is vital to the BOS process.
“Insisting on EAF steel as a way of reducing carbon content shows a misunderstanding of steel manufacturing. The steel sector is on a route towards being carbon neutral and demanding EAF is a distraction from that.”
Alan Dunsmore, CEO of Severfield, says: “It is just displacement because the overall mix of steel produced globally remains exactly the same, regardless of what steel is used on any individual project. And this mix cannot really change because of the requirement for scrap steel to support the EAF process, the supply of which is limited.”
Dash for scrap
Manufacturer British Steel also warns about the dangers of a ‘dash for scrap’. Commercial director for construction Ben Cunliffe says: “We can’t produce more steel purely from scrap – we need to produce new steel. Asking for steel made only from scrap is being done increasingly for commercial reasons rather than for genuine reduction of CO2 levels, perhaps making buildings superficially more attractive to people who don’t understand what they are asking for.”
Matthew Shimwell, managing director of steelwork contractor Caunton Engineering, says he welcomes the debate it generates: “When clients specify EAF steel they create healthy competition across the supply chain, which pushes others to improve.”
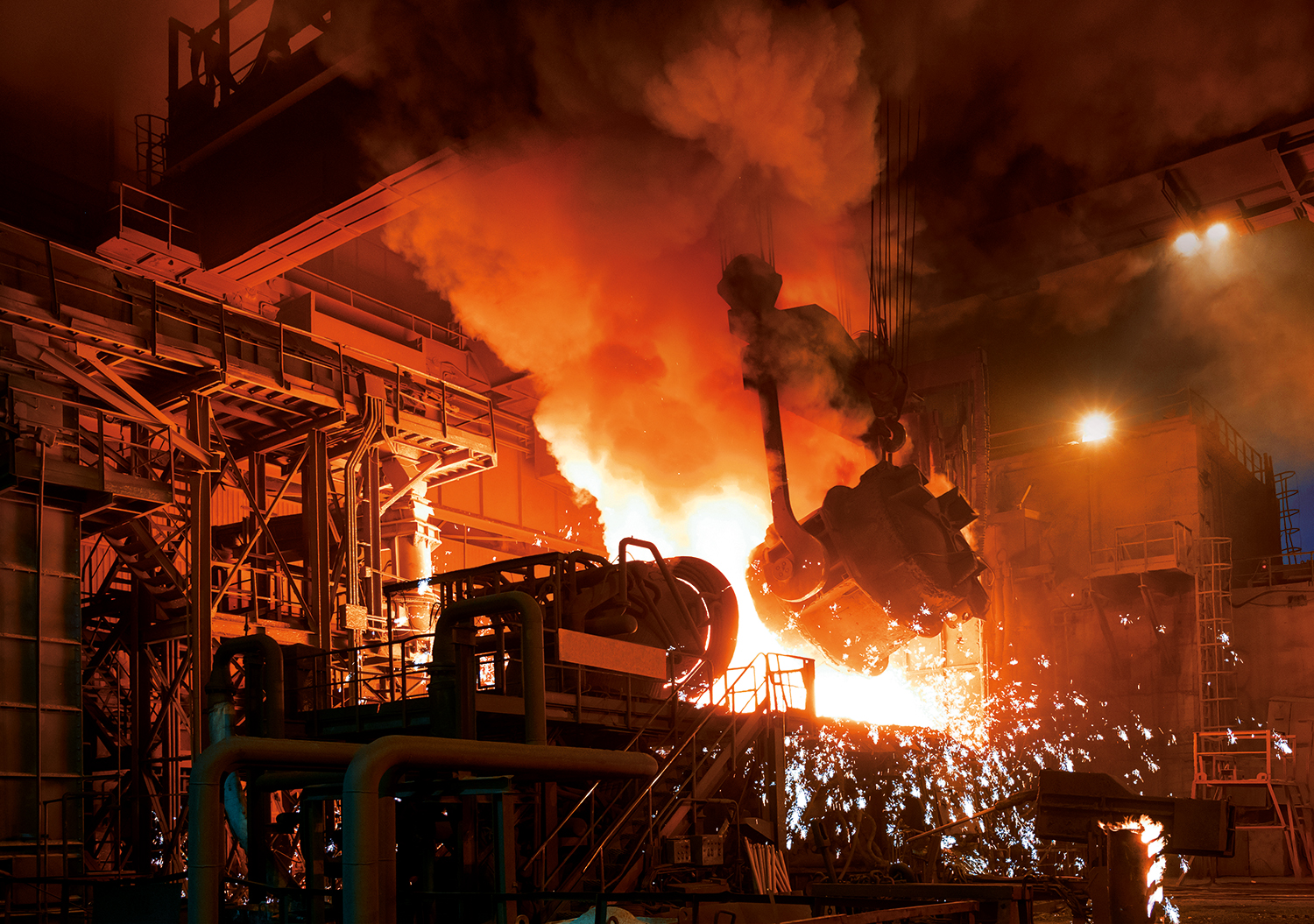
He adds: “It’s important that primary steel manufacturers (BOS) are supported during their transition to greener steel, as ultimately it’s their carbon reduction strategies that will have the biggest impact on reducing embodied carbon. Once out of this primary steelmaking phase, of creating virgin steel, we can then benefit more fully from steel’s ability to be recycled endlessly.”
BCSA published its UK Structural Steelwork: 2050 Decarbonisation Roadmap in November 2021, which shows a credible pathway to transition to net zero by 2050. EAF steel is part of the solution, but BCSA says it is not a silver bullet. It encourages clients to talk to the industry to help understand the issues to consider.
Engage early with steelwork contractor
BCSA argues that the best way to reduce the carbon footprint of projects is greater collaboration and early engagement, leading to increased design efficiency.
“Cost and sustainability are two of the driving concerns of developers of buildings and other structures. Both ambitions can be targeted by a single strategy – early engagement with your steelwork contractor,” says Moore. “The price of steel itself is not under the control of steelwork contractors, but ours is a highly competitive sector, which ensures that the keenest prices for fabrication and erection of steelwork are always available.
“Developers, designers and contractors know this, which is why steel is the market leader in key sectors like multi-storey buildings and single-storey industrial buildings or sheds. They all increasingly need to ensure that the products and services they use are being produced to the highest possible sustainability standards.”
There is a recognition of the need for greater collaboration across the industry. Smith says: “The spirit of collaboration that we saw as a response to the challenges of the pandemic is being maintained. Clients are taking a more strategic approach to procurement, with many of them having recognised the benefits of early engagement with their suppliers, rather than passing risk down the supply chain.
“The sustainability focus is ever increasing and that is coming from our own direct clients as well as from their clients.”
Cost price squeeze
Cunliffe says steelmakers have faced a significant cost price squeeze since summer 2022, with prices falling month on month due to lacklustre demand, while raw material steelmaking input costs remained largely flat.
“Prices appear to have now bottomed as the market is accepting that price levels are no longer sustainable with the continued high levels of raw material costs,” he says.
British Steel says there is no issue with capacity constraints or supply, and lead times for most types of steel sections are four to six weeks from placement of order.
It is estimated that as much as 20% of the steel requirement for some projects can be eliminated by the more efficient design that a steelwork contractor can suggest if engaged early enough. Lead times can also be cut.
Shimwell says: “Early engagement of a steelwork contractor is the single best way to reduce carbon. Some clients have had intellectual property worries but trust comes into it, and pre-contract agreements can also help. I think we are winning the debate.
“Clients are moving away from the traditional way of procuring, which meant appointing designers, contractors and materials suppliers in a linear fashion, first one then the next and so on. This pushed key suppliers off the critical path, which is now recognised as a waste of time and money, as well as leading to less efficient designs and hence a sub-optimal carbon-related performance. More efficient design can also cut waste.”