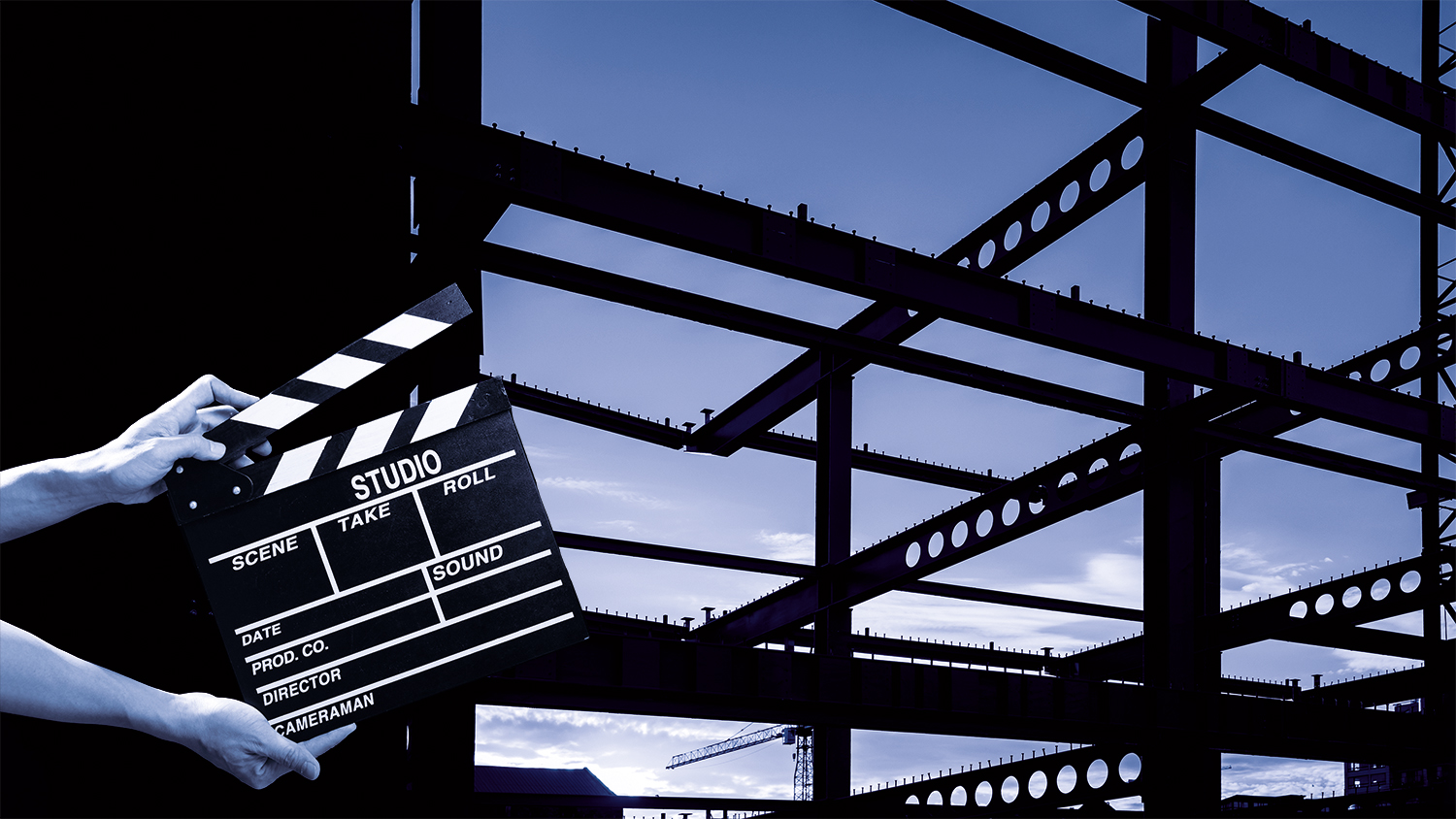
Flexibility, speed of construction and large column-free spaces mean steel is the preferred framing solution for the UK’s booming film and TV studio sector. By Martin Cooper.
The UK’s film and TV sector is booming. Recent research by ScreenSkills and the British Film Institute says the sector is riding the crest of a wave and estimates that continued growth will require the equivalent of between 15,130 and 20,770 additional full-time crew within three years.
A bigger workforce is needed as an estimated 250,000 sq m of additional stage space will be available by 2025. Recent investments by the likes of Sky, Netflix, Amazon Prime, Apple TV and Disney have seen billions of pounds committed to the UK sector.
Huge sums are being spent on enlarging existing studios and on building new complexes. More than 20 new sites are in the pipeline, including an expansion of the famous Pinewood Studios and the redevelopment of the former Dagenham Ford works, with plenty more currently under construction.

“Steel is lightweight and efficient and allowed an elegant structural design at Kelvin Hall.”
Steel is playing a leading role in this sector as the majority of film and TV studios in the UK are built using a steel-framed solution.
“Structural steelwork is ideal for the construction of studios as the material can provide long clear spans and is quick to erect,” says Fairhurst partner Hugh O’Neill.
“In simple terms, the studios can be thought of as hangars with increased acoustic insulation, as they both have similar frames with roof trusses. The trusses form the important open-plan interiors and in the sound stages they are also used to support multiple pieces of equipment, alongside access gantries and walkways.
“The driver is to create the open space to allow flexibility of use by the set designers. Building the superstructure quickly allows earlier commencement of the follow-on fit-out works.”
Sky Studios at Elstree
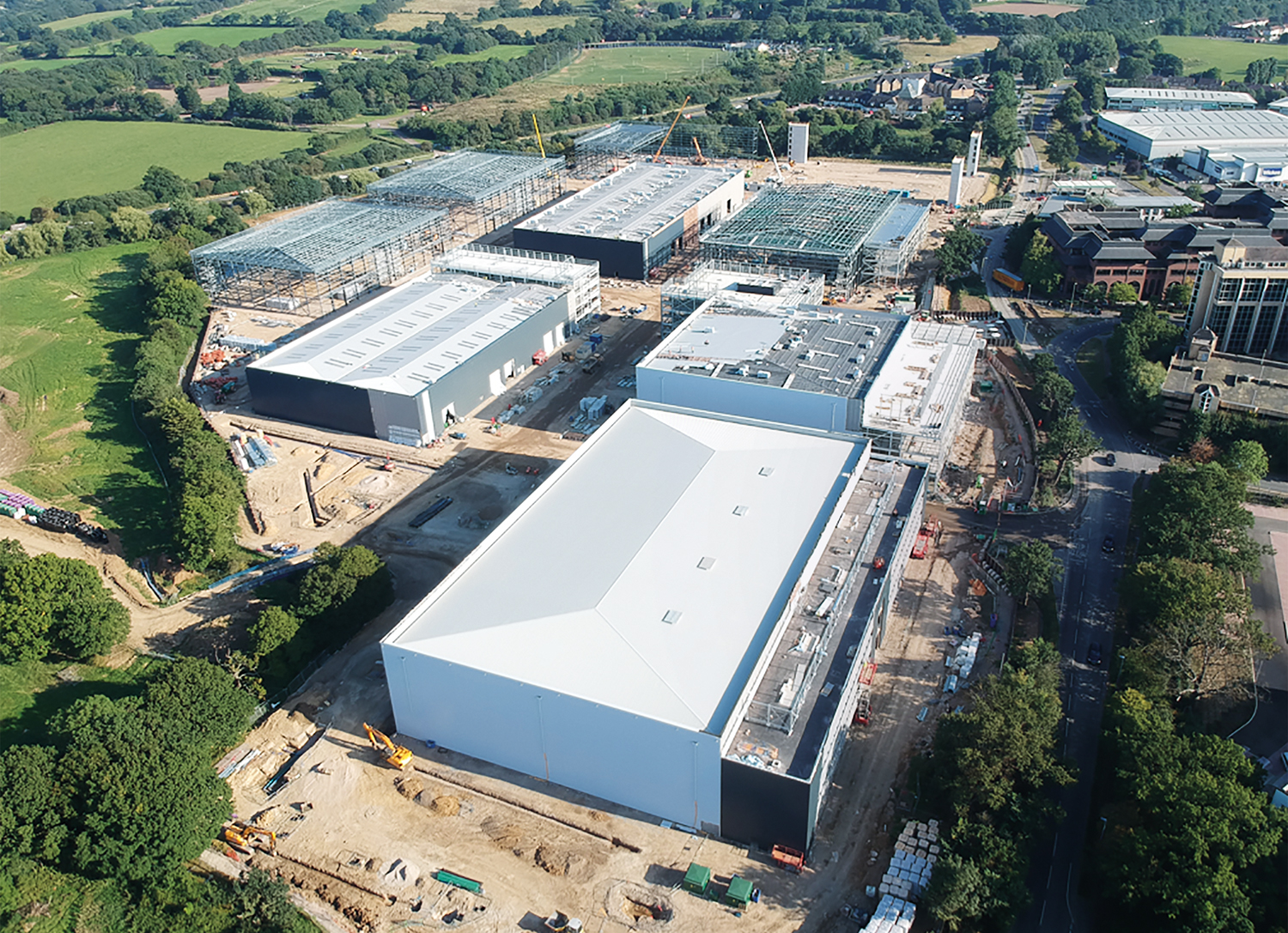
Flexibility is another important attribute of steelwork, as studio buildings are quite often designed so they can be subdivided into smaller spaces if required. This has recently been highlighted at the new Sky Studios project at Elstree, where a number of stage buildings have demountable steel walls.
Located just north of London, Elstree has been home to a significant slice of the British film industry for more than 100 years. This current project will be one of the largest. Housing 13 sound stages, it will be host to a range of film and TV productions from Sky Studios and NBCUniversal.
Once operational, the scheme will have the capacity to host productions from third-party producers, allowing the European and International creative community to do their best work in the UK.
There are nine main steel-framed buildings in total: eight stage and production structures and a multi-storey car park. Working on behalf of main contractor BAM Construction, Severfeld fabricated, supplied and erected 6,500 tonnes of steelwork for this prestigious scheme.
Flexibility for reconfiguration
The stage studio buildings are up to 54m wide, with column-free internal spans formed with long steel trusses. Three of the studios have demountable partitions to allow them to be subdivided into smaller spaces, with two structures having the flexibility to be reconfigured into four studios instead of one large space.
“The demountable walls can be up to 1m thick as they are acoustically treated partitions, but they can be removed, albeit in a few days or so,” adds O’Neill. “A steel design gives the project this desired flexibility in terms of functional use of the space.”
In line with Sky’s commitment to become net zero carbon by 2030, and matching developer Legal & General’s drive to deliver major ESG (environmental, social and governance) projects, Sky Studios Elstree has the ambition to become the most sustainable film and TV production studio in the world.
As part of design process, the businesses have looked at all sustainable development opportunities, with the project using reduced embodied carbon in construction. The site will only use renewable energy, with much of this coming from onsite solar panels.
“All framing solutions were looked at and steelwork was the best option. Once the initial design was finalised, we then undertook a carbon reduction programme, that involved value engineering all of the steelwork to create the leanest and most efficient frames,” explains O’Neill.
Glasgow’s Kelvin Hall film hub
Showing the nationwide scope of the sector’s current boom, in Glasgow a new film and broadcast hub is being constructed at the city’s famous Kelvin Hall.
Built in 1918 then rebuilt in 1926‑27 following a fire, Kelvin Hall has had a varied existence, housing large national and international exhibitions as well as motor shows, sporting events and classical and rock concerts. It was also converted to a barrage balloon factory during the Second World War.
Jump forward to 2023 and Kelvin Hall – which closed its doors in 2014 – is in the middle of a redevelopment programme that has already seen two of its four halls return to life as upgraded exhibition space, a sports centre and a health and fitness club.
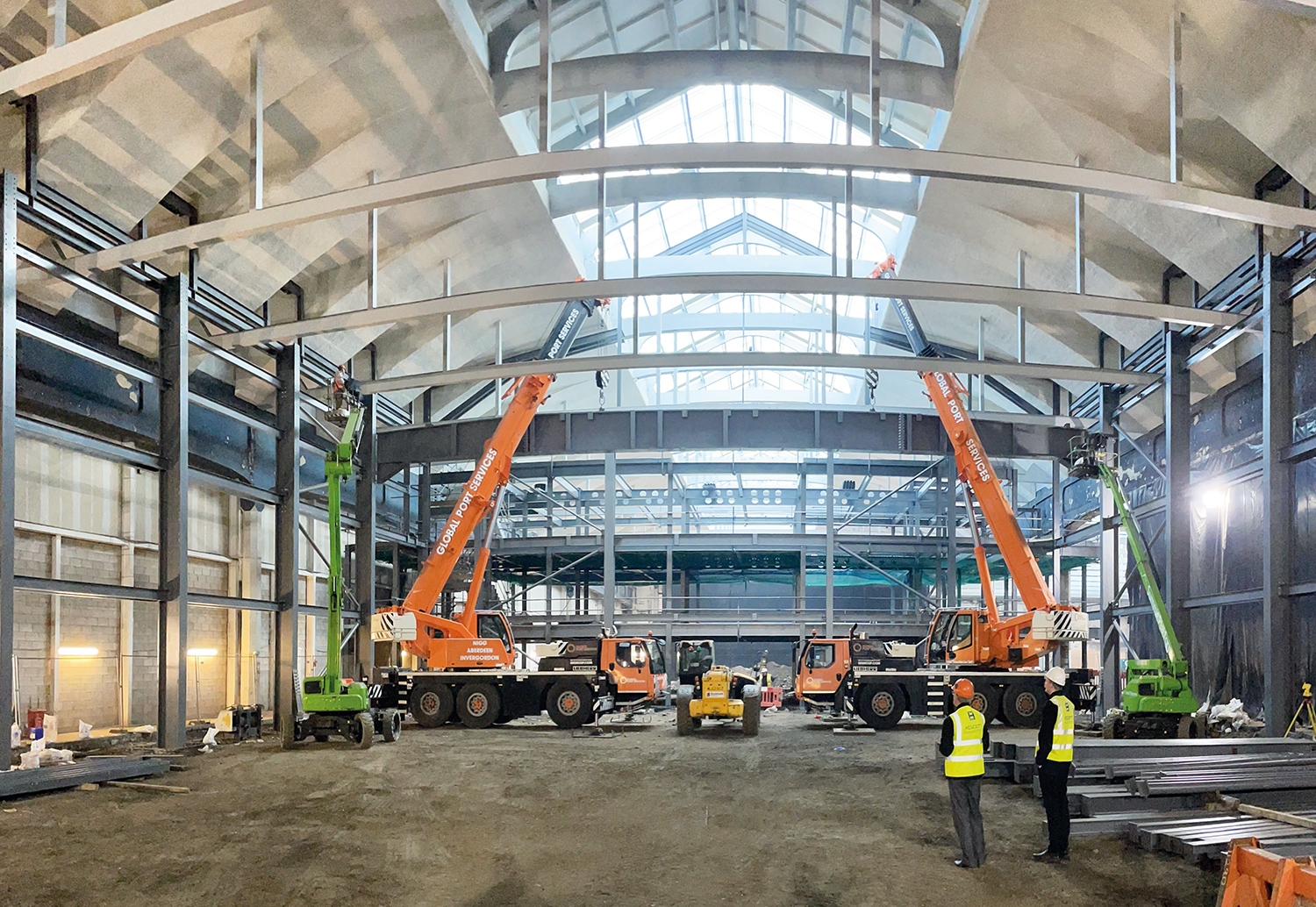
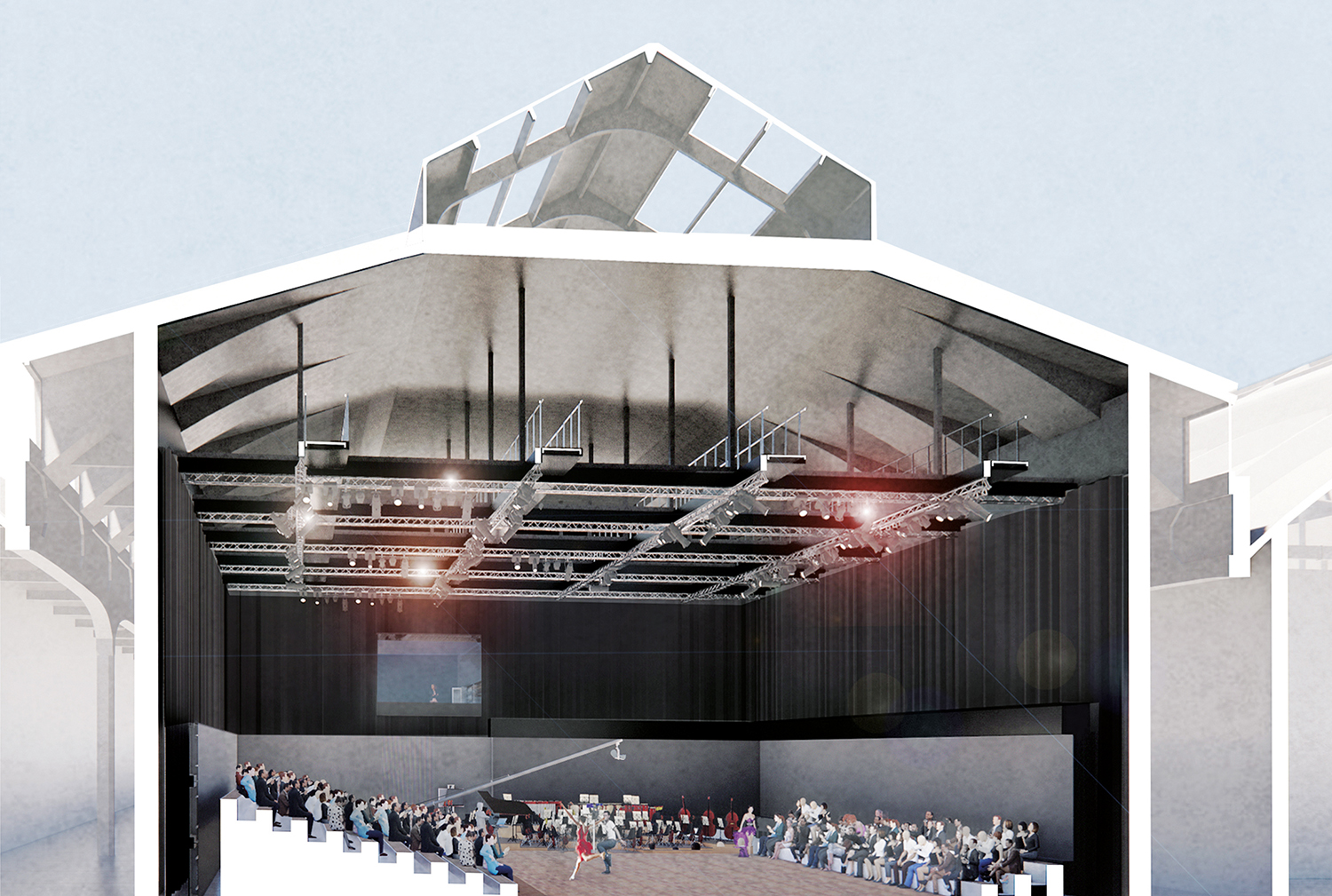
Phase two is now underway, which includes the construction of the steel-framed Kelvin Hall Film & Broadcast Hub, in hall number three.
Once complete, the facility will be operated by BBC Studioworks, a commercial subsidiary of the BBC which provides studios and post-production services to the industry.
Scottish hub for TV
Co-funded by Glasgow City Council and the Scottish government, the facility will house a wide array of entertainment shows across multiple genres. It will become the Scottish hub for major TV broadcasters and production companies and will help meet the growing demand for TV shows in Scotland, providing studio space and post-production services to companies including the BBC, ITV, STV, Sky, Channel 4 and Netflix.
Working on behalf of main contractor City Building, Hescott Engineering erected 300 tonnes of steelwork for this project.
Explaining the choice of a steel design, Woolgar Hunter project engineer Paola Pappas says: “Steel is lightweight and efficient and allowed an elegant structural design.
“Essentially, the building is a braced box with perimeter steel bracing, with secondary and tertiary steel supporting layers for TV cameras and access.”
The steel frame is divided into two parts that are acoustically isolated from each other: a column-free studio measuring 28m long x 30m wide, and a three-storey element that will contain recording and production suites, costume rooms, green rooms and workshops.
Liverpool’s The Depot
Another steel-framed project that recently opened is The Depot in Liverpool, built by Morgan Sindall. Already favoured by filmmakers for doubling-up for locations such as New York and London, Liverpool is said to be most filmed city in the UK. Requiring 220 tonnes of structural steelwork, which was erected by Leach Structural Steelwork, this project comprises two 1,850 sq m soundproofed film and TV production units.
Flexibility is at the heart of this project’s design, as the two steel-framed studio buildings have large internal spaces that can be utilised for a variety of productions and even sub-divided into smaller zones, if required.
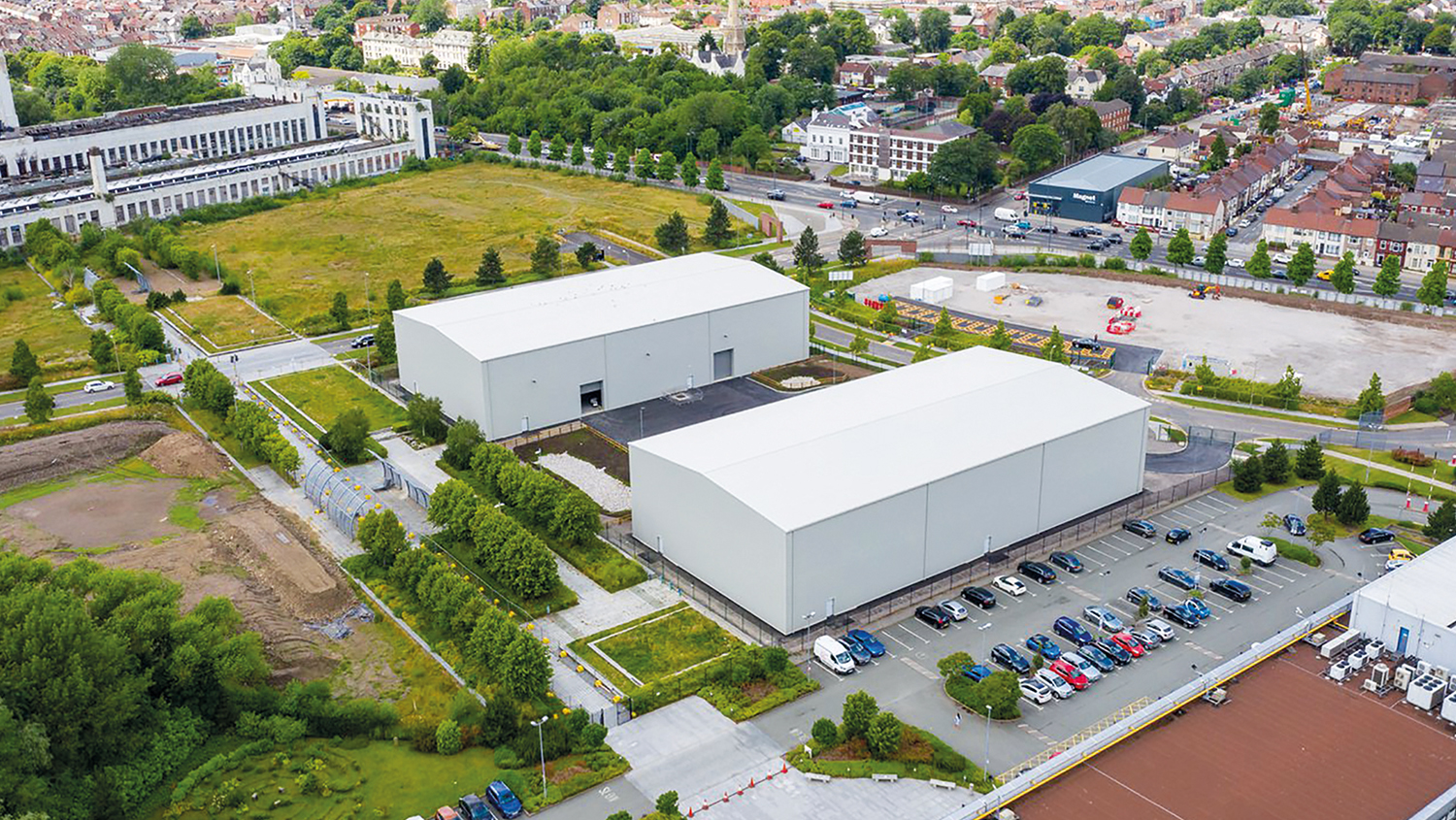
A steel-framed design proved the most efficient solution as the project team wanted a quick construction programme, a lightweight frame and two buildings containing large column-free spaces. All of the steelwork is left exposed within each of the structures, including the stability-giving bracings located at gable ends of both buildings.
Preventing noise entering and leaving the buildings is of utmost importance for film and TV studios, so the steel frame supports acoustic roof and wall cladding panels.
Steve Rotheram, metro mayor of the Liverpool City Region, said: “Our ambitious plans are to help make our region the ‘Hollywood of the north’.
“These new facilities will help us keep [film and TV productions] here and offer the full package to productions, from providing stunning filming backdrops to the more technical editing and recording work.”