The rapid rise of internet shopping has led to growing demand for distribution warehouses, which in turn are getting bigger and quicker to build. Martin Cooper reports on structural steelwork’s largest UK market.
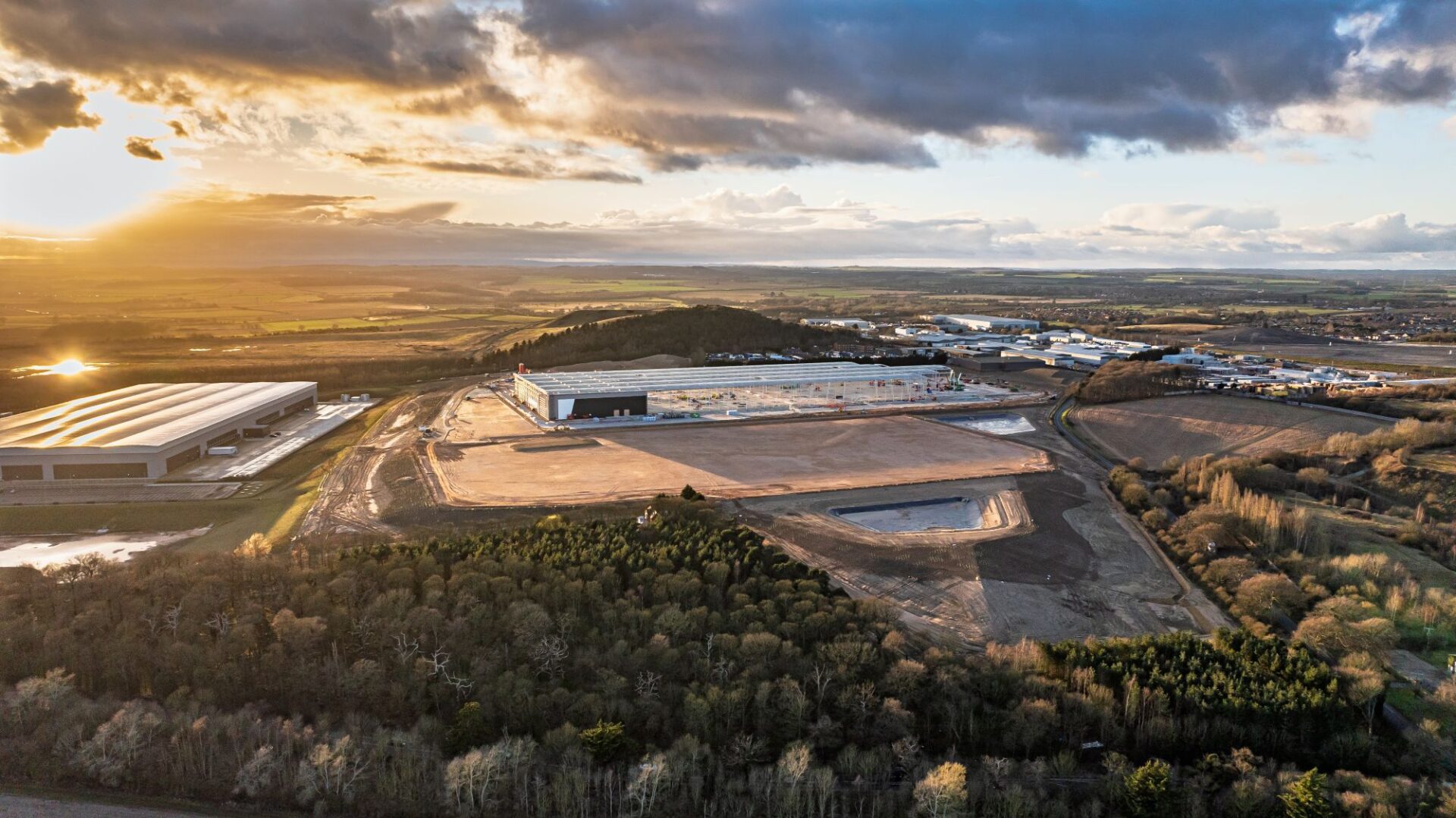
Online retail has more than doubled in the past decade. And thanks to the increasing volume of goods that come to us via deliveries from companies like Amazon, there has been a boom in the construction of logistics centres over the past decade.
These ‘super sheds’, typically constructed with steel frames, are also growing in size, with warehouses of over one million sq ft not uncommon these days.
Structural steelwork has traditionally dominated the single-storey warehouses market, and during 2024, it had a 94.1% market share. According to the annual survey commissioned by Steel for Life and the British Constructional Steelwork Association (BCSA), and conducted by independent market research consultant Construction Markets, this important sector accounts for almost 50% of the overall UK structural steelwork market by tonnage.
Steel’s attributes, including cost-effectiveness, adaptability and its contribution to the circular economy through reuse and recycling, are all factors that continue to be valued by developers, contractors, designers and building users.
Size is everything
One design feature that stands out in this sector is the growth in size of the warehouses over the past 30 years. Where once a structure exceeding 200m in length was considered a giant, portal-framed distribution centres are today commonly over 300m long, with internal spans exceeding 35m in length.
The large spans, which create the all-important open-plan areas needed for distribution centres, are usually created with a series of roof rafters. For ease of transportation, spans over 25m long will usually have rafters fabricated and delivered to site in two sections, which are then bolted together during the erection process to form the overall length.
The rafters are supported by columns, arranged in a regular pattern along the building’s perimeter, while internally, they can be set out in a hit-and-miss configuration, whereby every second member is omitted to create even more column-free space.
Developers want to maximise the footprint and available space of their sites, and so distribution centres have also become higher. In the past, designers would have settled for a height of 12m, but today the standard is 15m, while 18m and even 21m clearances are regularly built.
The UK’s largest distribution centre is the Amazon fulfilment centre in Tilbury, with a floor space of two million square feet.
But how much bigger can distribution centres get?
It’s all about economics and cost, according to Caunton Engineering sales director Ian Oliver. “The overall building can be as long as a client wants, but internally, portal-framed structures are only efficient with spans of up to around 40m,” he says.
“Anything longer than that and the design moves into a more bespoke realm and the roof would have to be formed with trusses, which are heavier than single rafters and require more steelwork.”
The UK’s largest distribution centre is the Amazon fulfilment centre in Tilbury, which contains pretty much everything any household would want. The centre has a floor space of 185,806 sq m (two million square feet).
The ‘golden logistics triangle’
Being close to the major port facilities on the River Thames has obvious benefits for the online retailer. But Essex is not the most favoured location for distribution centres. That accolade goes to the East Midlands and an area dubbed the ‘golden logistics triangle’.
Encompassing parts of Leicestershire, Northamptonshire and Warwickshire, the area has excellent transportation links, being close to the M1 and M6 motorways. This strategic location, in the centre of the country, allows goods to be transported to anywhere in the UK within a matter of hours, while the A14 also links the triangle with Felixstowe, the UK’s largest and busiest container port.
The triangle is home to an array of warehouse parks, including Magna Park Lutterworth, which is said to be the UK’s first and Europe’s largest dedicated distribution location.
Developed by GLP, as its flagship park, it is home to 29 different occupiers, including Toyota, BT, Asda Walmart, Amazon, DHL and Britvic.
It is a private estate and offers a fully managed, dedicated logistics park environment with 24/7 access, 24-hour security and a controlled HGV circulation.
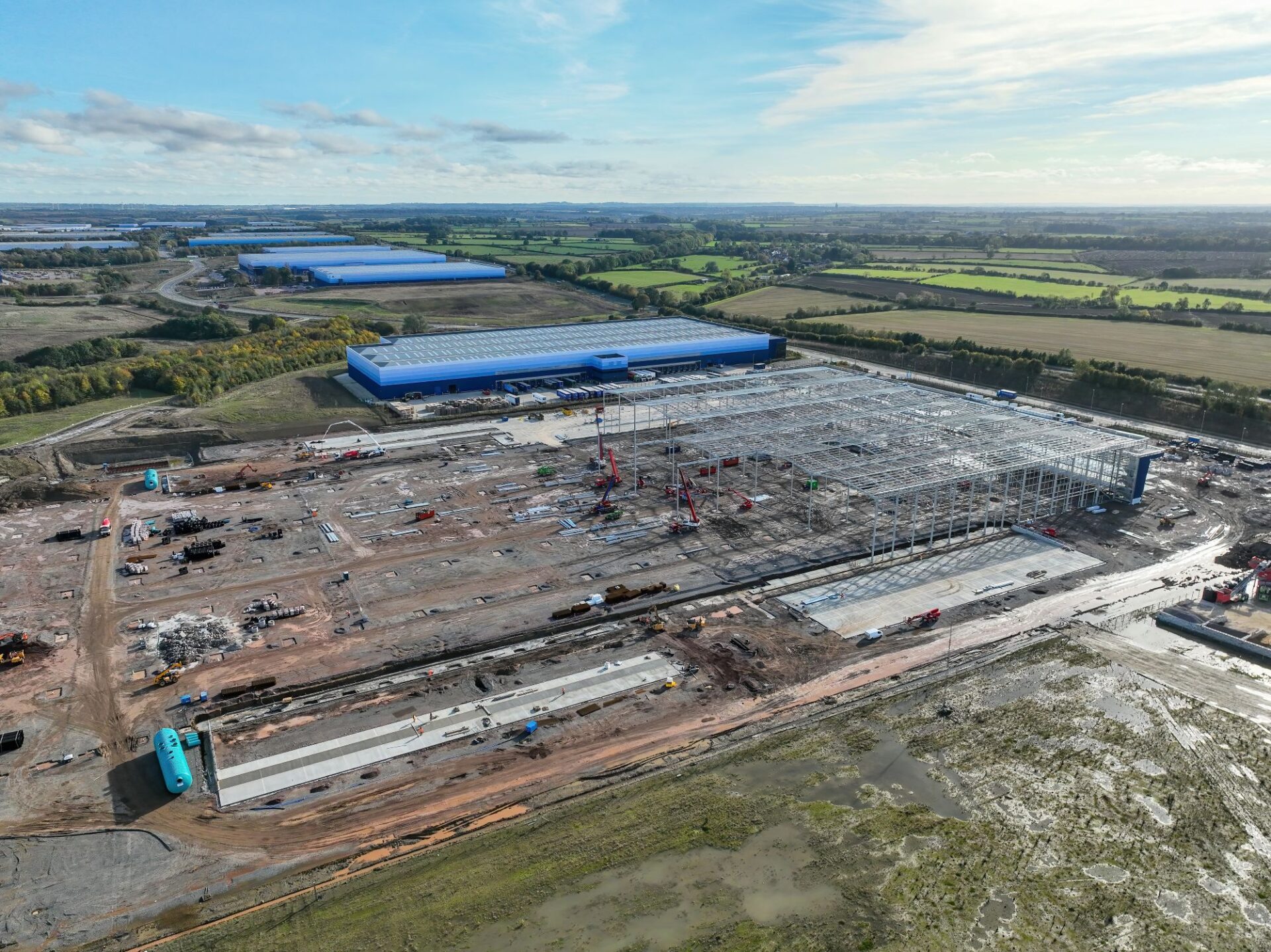
The park, which is divided into north and south areas, is continuing to expand and currently, Winvic Construction is building the largest speculative unit GLP has developed to date. Known as MPN 761, the steel-framed 70,699 sq m distribution centre, which is due to complete this summer, features six 30m-wide spans, has an 18m clear height to haunch, and includes a three-storey office and two transport hubs.
Peter Baird, senior construction manager at GLP, says: “The next important phase of development at Magna Park North is a testament to our confidence in the resilience of the UK logistics market and the strategic importance of the Midlands in particular. We are delivering a best-in-class mega-distribution unit with occupier demand, technological advancements and environmental, social and governance principles at its core.”
Net zero at Magna Park
To this end, a number of sustainability initiatives are in place as the project has been designed to achieve net-zero carbon in construction and a BREEAM Outstanding rating.
“We have partnered with a carbon-neutral subcontractor for the earthworks package and have set up an onsite batching plant for all the required ready-mix concrete,” explains Winvic project manager Charlie Caldicott.
“This has the environmental benefit of cutting down on truck movements in the local area.”
Work started on site in June 2024, with an enabling earthworks package and the installation of pad foundations, in readiness for the steel frame erection.
Speed is of the essence for all construction projects, and distribution schemes are no exception. Developers want the buildings up and ready as soon as possible, which is one of the most important reasons for using a steel-framed option.
Proving how quick and efficient a steel erection package can be, using up to four 70 tonne-capacity mobile cranes, the 384m-long structure, requiring 2,470 tonnes of steelwork, was installed in just 11 weeks.
Elsewhere in the Triangle at Magna Park Corby, VolkerFitzpatrick, working with Severfield, has recently completed two portal-framed warehouses, with a combined floor area equivalent to more than 20 football pitches, while next to East Midlands Airport and incorporating its own rail freight terminal, SEGRO’s logistics park has plans for further expansion.
As well as Tilbury, UK’s other ports also offer strategic and desirable locations for distribution centres.
With nearby major international docks and rail freight facilities, as well as being close to both the M4 and M5 motorways, Avonmouth near Bristol has become a prime location.
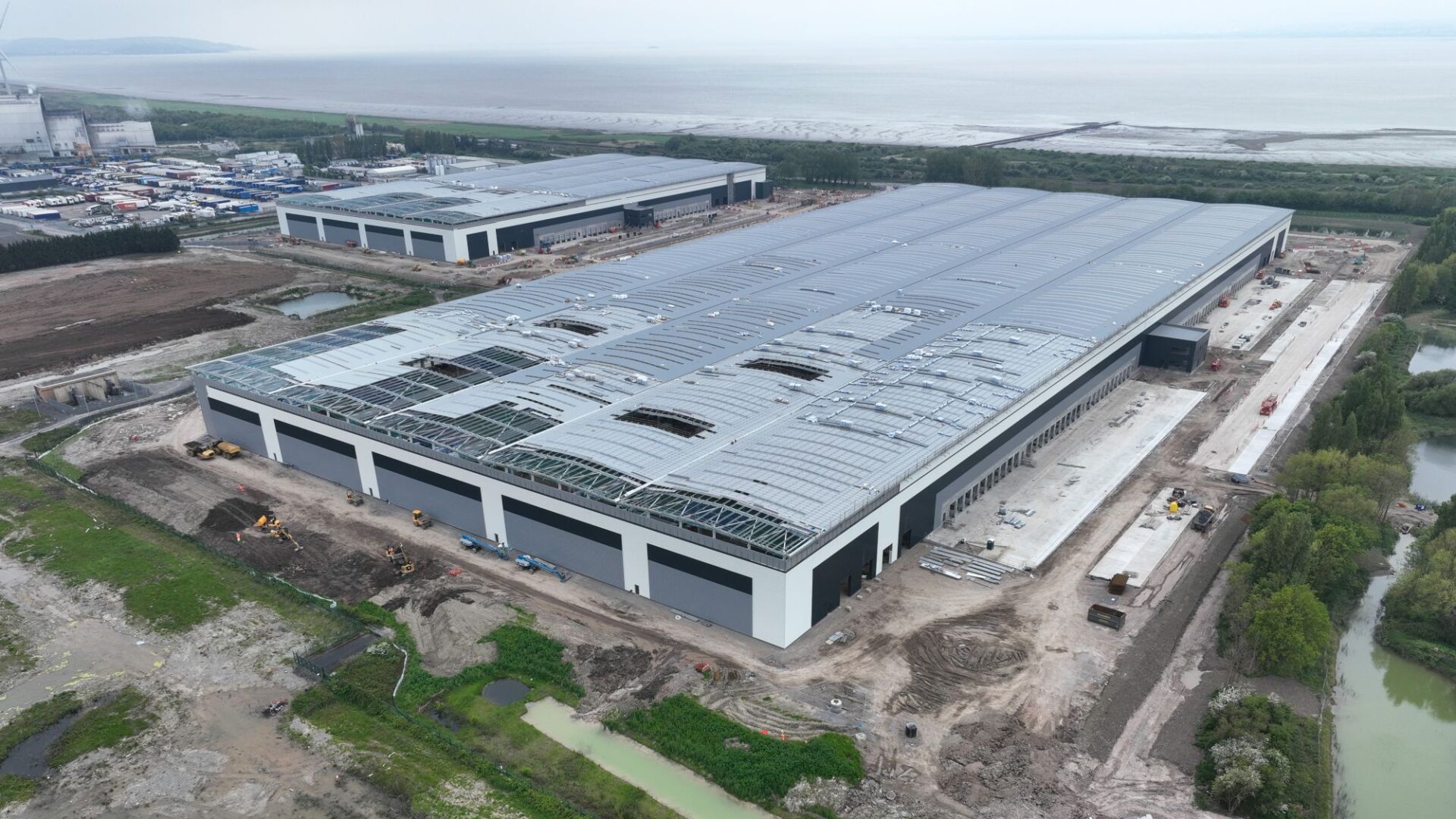
A short distance from the River Severn, developer Panattoni recently constructed one of the UK’s largest-ever speculative developments. The scheme, known as Panattoni Park Avonmouth, consists of two 17m-high units; one offering 37,718 sq m of floorspace and a much larger warehouse, measuring 425m by 188m, providing 82,727 sq m.
Working on a design-and-build contract for the now defunct main contractor ISG, Severfield fabricated, supplied and erected 4,900 tonnes of steel for the project. Ensuring a cost-effective and sustainable approach, the company says that all the steel sections used were engineered to be as efficient as possible.
Sustainability was at the heart of the project as both warehouses achieved a BREEAM Excellent rating and an EPC rating of A. They also benefit from roof-mounted solar PVs, rooflights and EV charging points.
Trusses offer industrial solution
While distribution centres are predominantly designed as portal-framed structures, when the building has an industrial or manufacturing use or the span exceeds 40m, steel roof trusses are invariably used to create the internal open-plan space.
Trusses can form larger spans and are also rigid and robust enough for large equipment items to be supported from their underside.
One of the biggest examples of this design is the SeAH Wind facility being built on the south bank of the River Tees. Standing 40m high and measuring 800m in length, on completion the £450m manufacturing plant will be the world’s biggest monopile (foundations used for offshore wind farms) factory and the first of its kind in the UK.
With a maximum width of 210m, the structure has four spans at its widest point, but just one single span for nearly half of its length. A series of large steel trusses, forming a significant portion of the 35,000 tonnes of steelwork supplied by British Steel and erected by Severfield, create the roof of the factory.
A similar steel arrangement was used to build the Guala Closures factory at Gartcosh in Scotland. The company, one of the world’s largest manufacturers of bottle tops, required a building with wide open-plan areas for its production machinery.
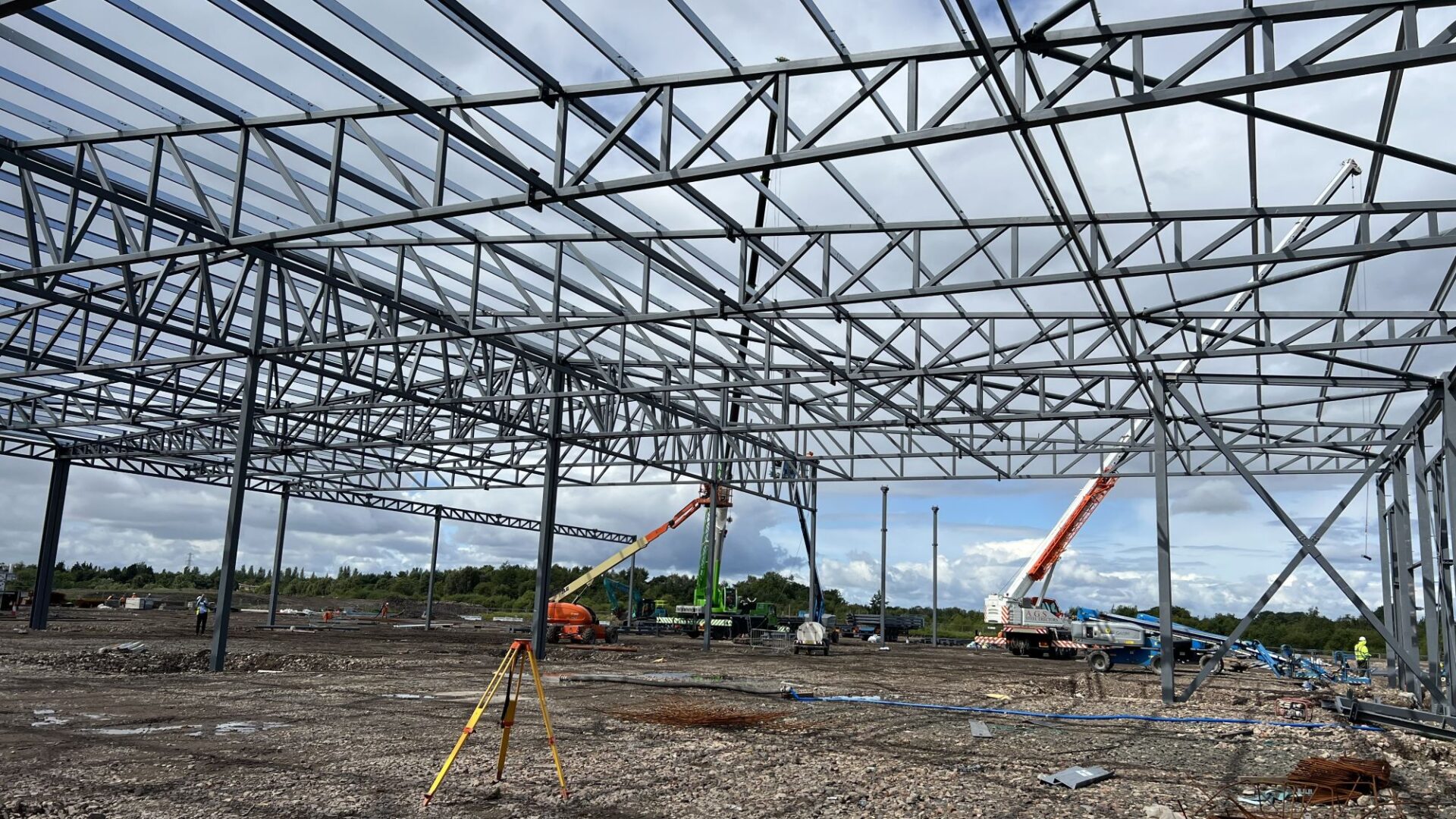
The steel frame, which measures 180m by 120m, has perimeter columns spaced at 7.5m centres. These columns support a series of trusses that form the building’s five spans.
“The project was always going to be a steel structure because of the required large open spans, but there was a design discussion about whether to go for a portal frame or use trusses,” explains Hector Munro, managing director of consulting engineer Grossart Associates.
“In the end, trusses were the favoured choice as they create the spans, while also providing the support for internal cranes and space for services within their depth.”
Working on behalf of main contractor Luddon Construction, Walter Watson erected the structural steelwork for the project in a 10-week programme.