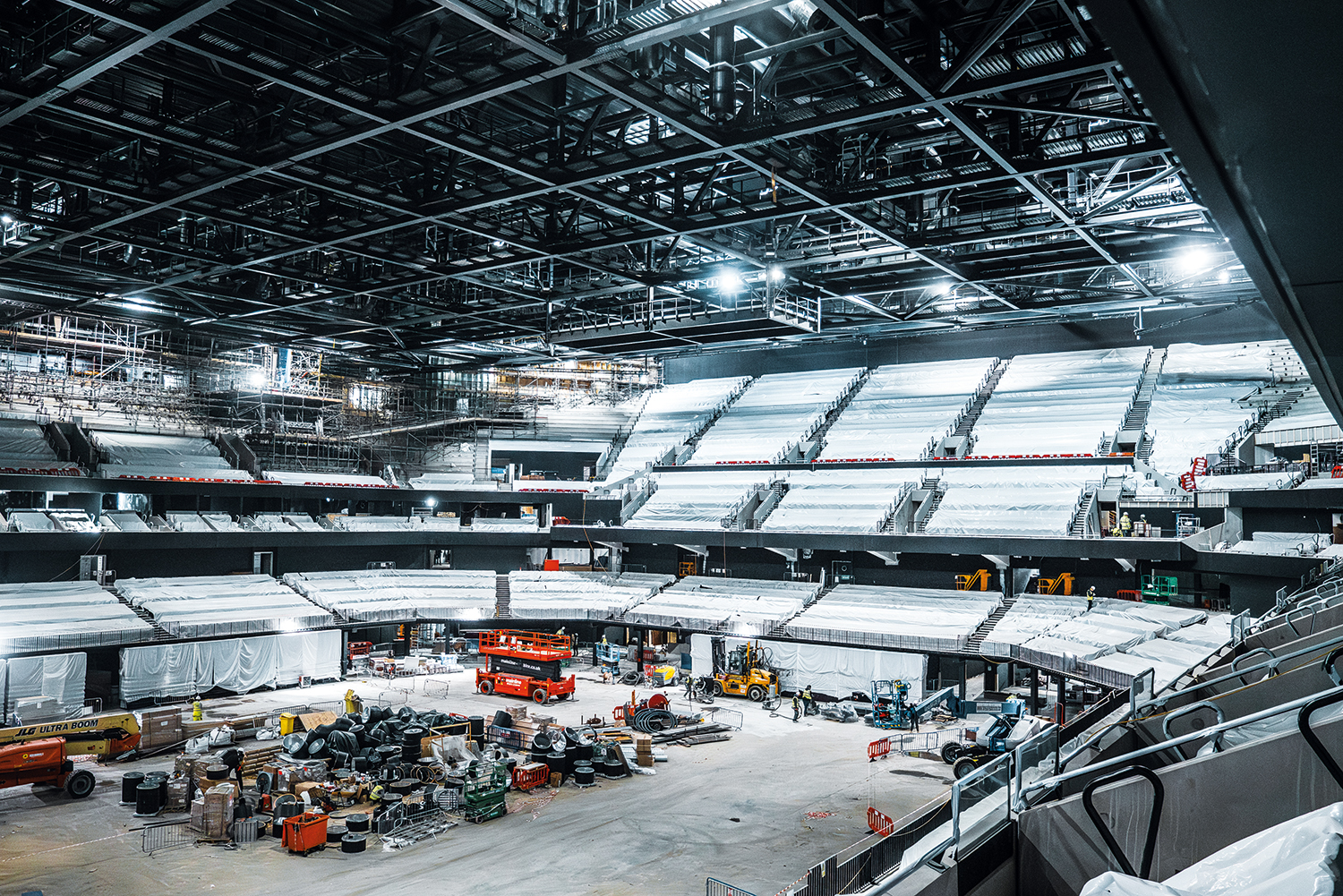
Structural steelwork has helped create the UK’s largest indoor venue, which boasts a 23,500 capacity alongside 41 bars and restaurants.
Award: Co-op Live Arena, Manchester
Architect Populous
Structural engineer Buro Happold
Steelwork contractor Severfield
Main contractor BAM Construction
Client Oak View Group
With the largest floor space of any UK indoor venue and a significantly lower ceiling, the Co-op Live’s tiered seating allows fans to be closer to the artist. Unlike venues designed primarily for sporting tournaments or public exhibitions, the arena is also claimed to be the first of its kind to be built around concert acoustics.
In accordance with the client’s brief, sustainability was at the heart of the project’s construction. The venue, which has been designed to support Manchester’s Zero Carbon 2038 commitments, includes numerous sustainability features
to create an inclusive, low-carbon and low waste structure.
The building is powered entirely by electricity with no reliance on fossil fuels, while renewable energy purchased from the National Grid will be supplemented by the large photovoltaic array mounted across 10,500 sq m of roof.
Steel-framed structure
The venue is a large steel-framed structure that is set out on a regular 8.5m column grid pattern. It comprises steel members supporting precast terrace units for the seating areas. Below these, horizontal beams support a composite metal decked flooring to create the circulation and concession zones.
Stability for the steel-framed structure is provided by the arena’s seven precast concrete cores, which work in conjunction with some strategically located internal bracings.
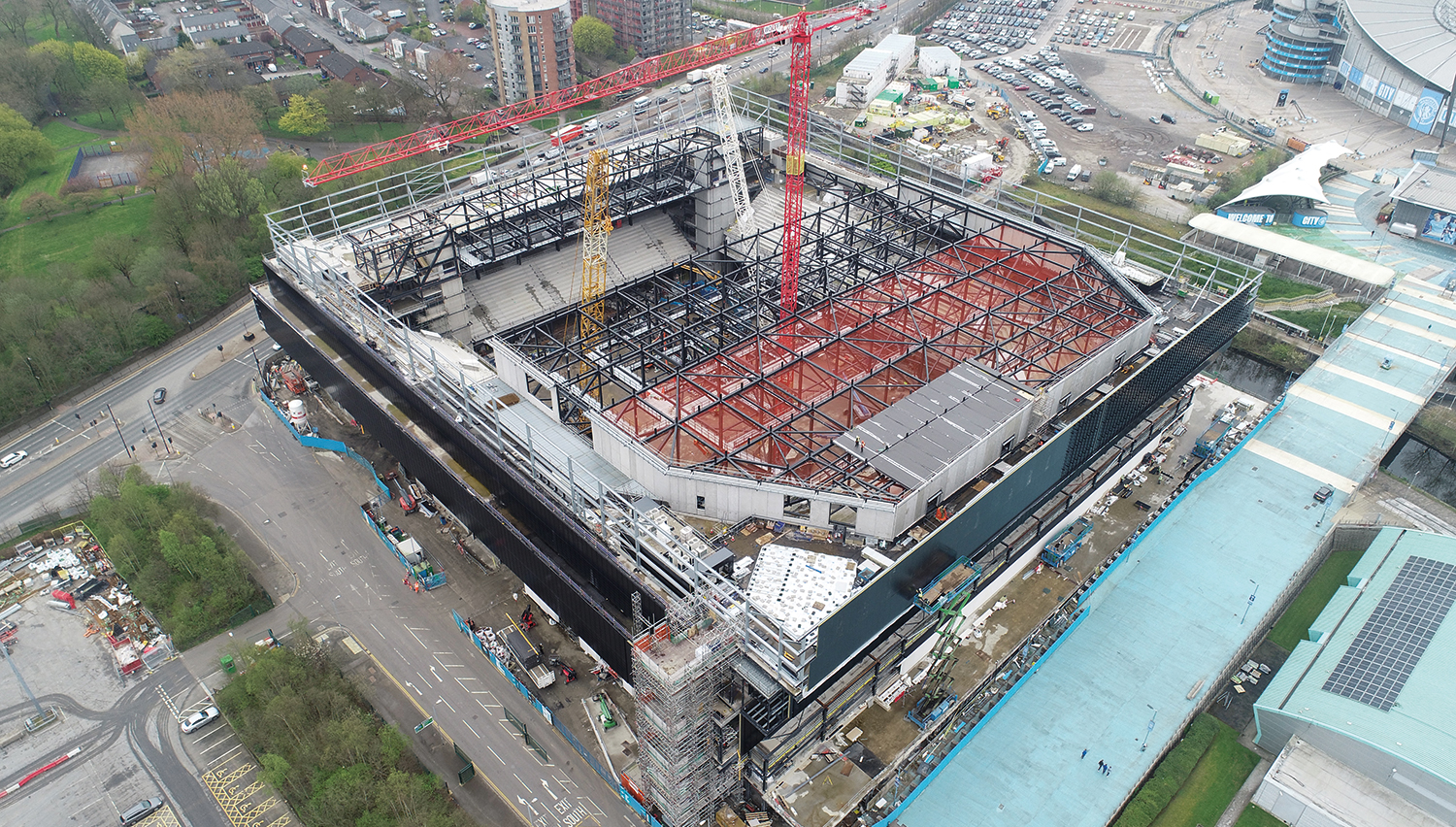
Around the bowl, the arena is predominantly three-tiered, with the middle tier containing hospitality boxes. The exception is the east stand, which accommodates the stage for concerts but also has a single upper tier of seating. This adds flexibility, as the stage can be removed where events require the central standing area of the bowl, allowing the seating to wrap around the four sides.
Once the main bowl superstructure had been completed, the roof steelwork was installed. Due to site constraints, this was brought to site in small components, assembled into larger sections on the arena floor and then erected from within the building’s footprint.
“A 100m-clear spanning roof forms the dramatic focus of this state-of-the-art purpose-built black box performance venue. Skilfully controlled surrounding spaces are defined, but never dominated, by the expressed structure that creates them. Built to exacting standards, this is a holistic and architecturally confident solution of high quality.”
The size of these components was dictated by the size of crane that could be rigged safely within the bowl’s footprint, combined with the requirement for it to be subsequently derigged underneath the completed roof structure.
A series of 100m-long trusses, each capable of supporting approximately 30 tonnes of equipment, make up the roof.
‘Roof is a machine’
“As well as forming the roof, all of the trusses are also supporting walkways, rigging strong-points and a host of important equipment for the lighting and sound,” explains Buro Happold partner Rob Amphlett. “The roof is a machine that enables the various productions. It is also the engine room of the arena.”
Because of the short design programme, the team adopted a strategy of suspending most of the building services beneath the steel floor beams and composite decks. Meanwhile, the venue’s location close to residential buildings, meant the roof cladding had several strict acoustic requirements.
An offsite solution was used, with acoustic cassettes that slotted into the main roof steel structure. Metal decking and a concrete topping was then added to the top of the acoustic liner to carry waterproofing and the photovoltaic units.
Produced by BCSA and Steel for Life in association with Construction Management
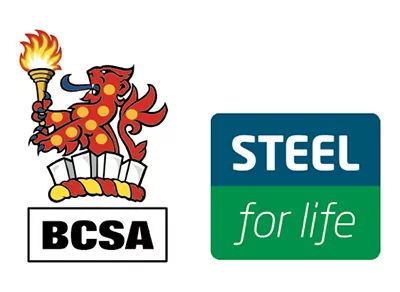