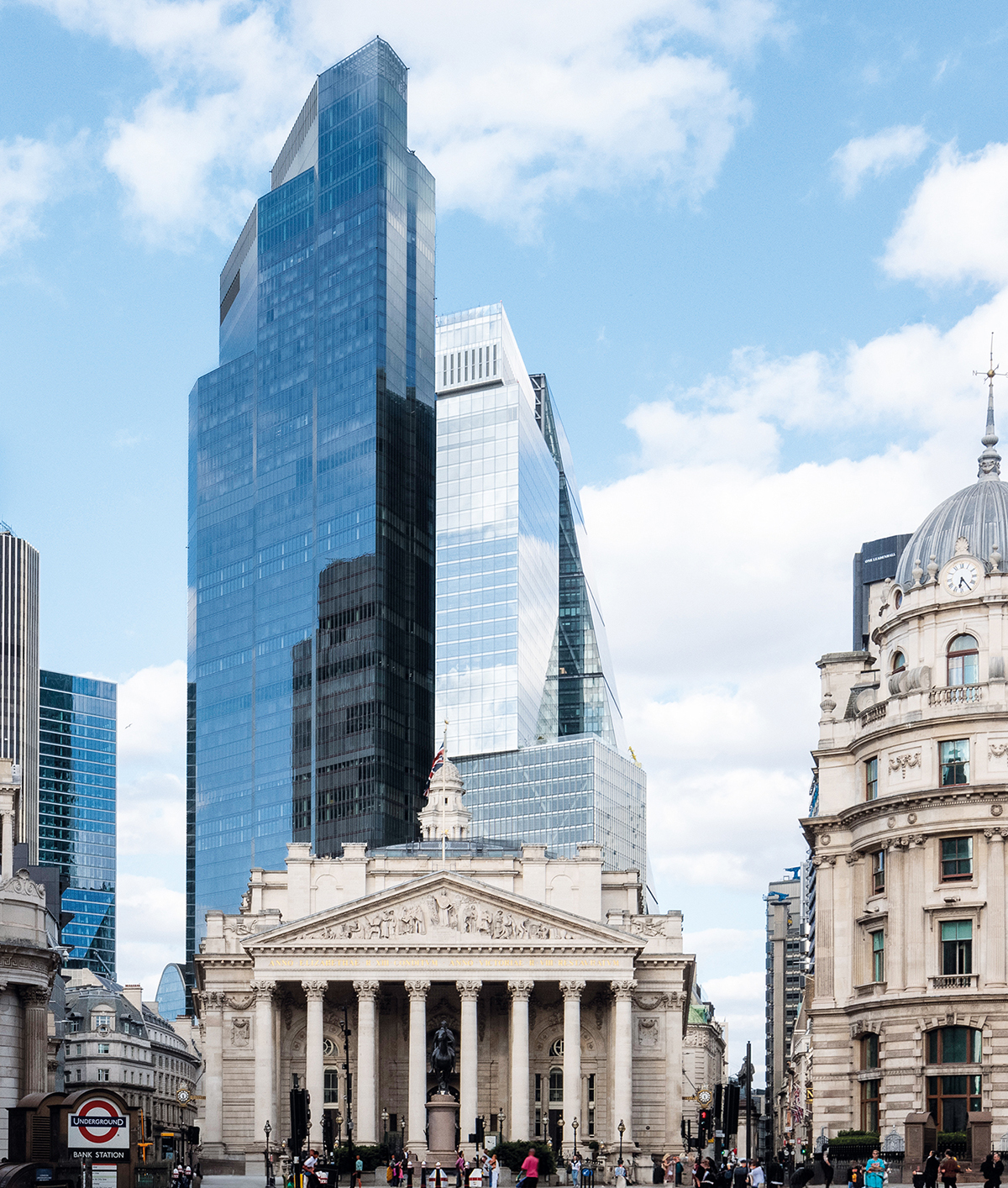
Soaring from a plot bounded by two of the City of London’s busiest thoroughfares, 8 Bishopsgate is the UK’s tallest structure to achieve a BREEAM ‘Outstanding’ rating.
Award: 8 Bishopsgate, London
Architect WilkinsonEyre
Structural engineer Arup
Steelwork contractor William Hare
Main contractor Lendlease
Client Stanhope
Breaking away from the traditional office block design, the 50-storey 8 Bishopsgate project has also achieved a number of sustainability credentials, making it a standout structure in many ways.
Containing 30% less structural embodied carbon than London tall building benchmarks, the building’s design revolves around the breaking down of its massing into smaller blocks. This allows the tower form to address the site constraints and brings human scale to the scheme.
The blocks are differentiated by scale, materiality and structural function, while the building’s stepped form is accentuated by terraces and cantilevers that contribute to a visually dynamic composition.
Starting at ground floor level, the steel frame incorporates three distinct blocks that are stacked up to form the overall building.
Unique identity
Each has a unique identity related to the cladding module, the addition of fins to the mullions or how the structure is seen through it. While the building is mainly glazed in a double-skin curtain walling, the lowest block is clad in stone to respond to the street context.
A low-rise block extends up to level 11, while a mid-rise one, positioned behind it, rises from level six to level 26. A slim high-rise block tops out at floor 48. A pavilion above this incorporates a public viewing gallery and plant zones.
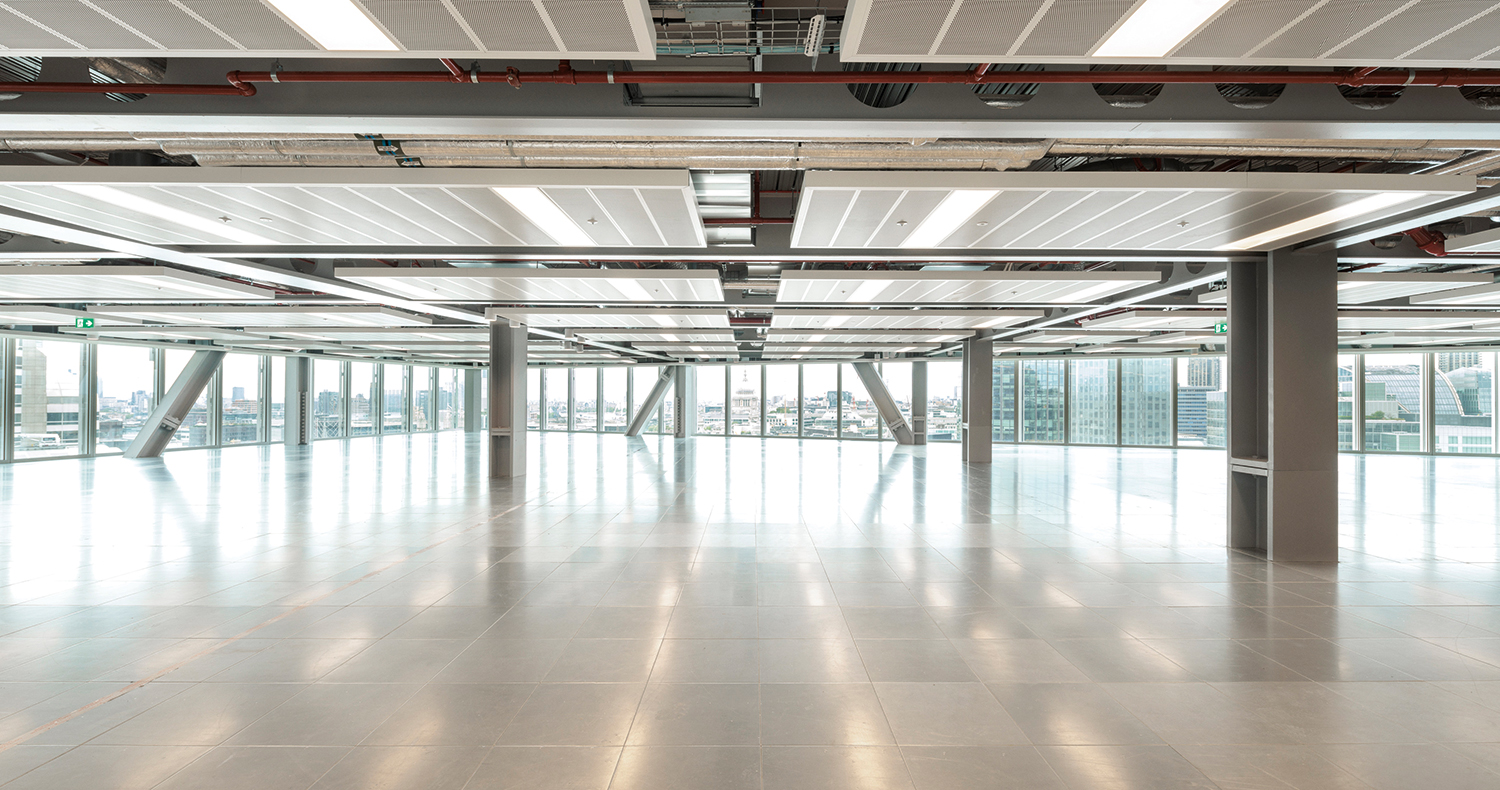
WilkinsonEyre director Oliver Tyler says sustainability has been a key design driver from the project’s inception, and one of the main goals was to achieve material efficiency.
“We used bespoke fabricated steel sections throughout, which were optimised for individual unique loads. By rationalising the building’s frame, we needed 25% less steel, which saved approximately 5,000 tonnes of carbon.”
The primary internal grid for the majority of the building is based around a 12m x 9m column pattern, using 620mm-deep plate girders with circular and rectangular openings to accommodate the building services.
“The column positions were selected in order to mitigate any column transfers, whereby the internal columns in the low-rise block continue upward to become perimeter members on the mid-rise part of the project,” says Arup project engineer Jeremy Edwards.
“Eschewing the creation of a simplistic City icon, this 50-storey building successfully combines a fragmented form, determined by function and site constraints, with a rigorous structural system. The resulting variety of spaces has proved a letting masterstroke. Impeccably constructed through a construction management contract,
this is a top-class project.”
Using the same column grid pattern, the high-rise block has no internal columns. Beams span directly between perimeter steel columns and the core, creating 21 storeys of column-free space.
Concrete cores
Providing the stability for the 50-storey building are two concrete cores. The north core extends to the full height of the structure, while the south core terminates at level 24.
Giving some extra stiffness to the structure, the mid-rise block is a braced box, featuring perimeter steel bracing that connects the two cores and mobilises the perimeter columns to resist horizontal loads. This stiffens up the low and mid-rise blocks and allows for a narrower north core for the uppermost block.
To further maximise floor space, the building cantilevers out along its western elevation, oversailing the pavement along Bishopsgate. This overhanging west face reinforces the architectural concept, while providing 15% of the net internal area, improving the scheme’s viability.
The western elevation’s overhang commences at level six and initially extends up to floor 26. Further cantilevers begin at level 26 and 48, with the former overhanging by up to 3.8m.
Produced by BCSA and Steel for Life in association with Construction Management
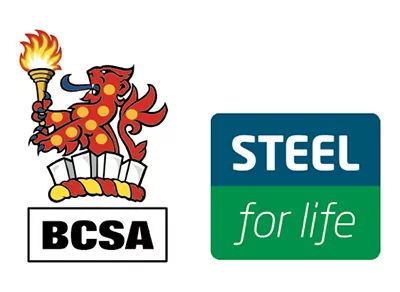