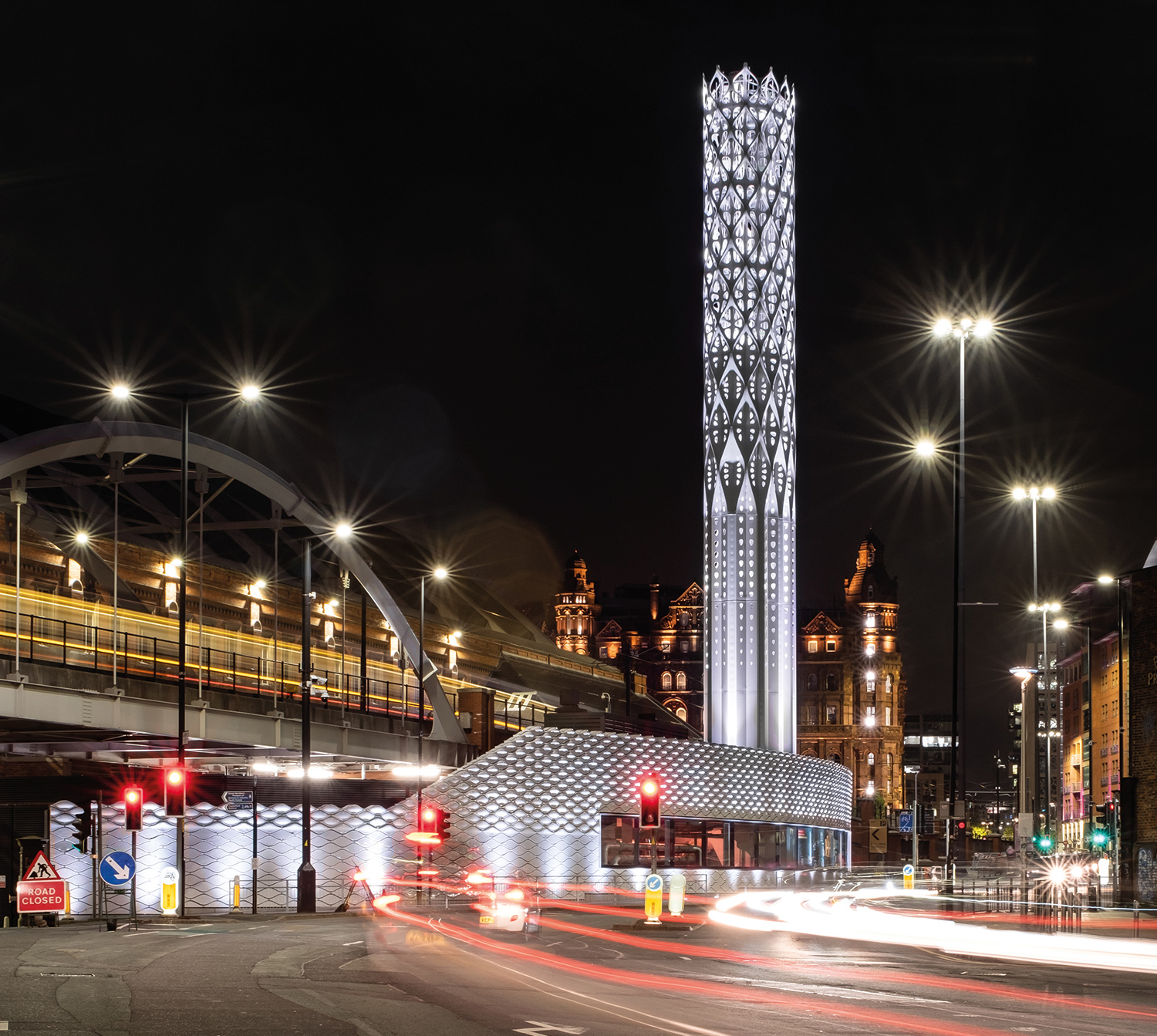
Adorned with laser-cut steel plates, a 40m-tall tower that supports five flues is a key component of a city-centre combined heat and power energy centre.
Helping to improve the city’s air quality, Manchester’s Civic Quarter Heat Network project will supply several local buildings with low-carbon energy much of which will be derived from a new combined heat and power (CHP) energy centre.
Award: Tower of Light, Manchester
Architect: Tonkin Liu
Structural engineer: Arup
Main contractor: Vital Energi
Client: Manchester City Council
Alongside the environmental benefits, the CHP’s city-centre location meant the client wanted the facility’s five flues housed within a structure with some architectural merit.
To satisfy this brief, the flues are accommodated in a 40m-tall steel tower, which has a curved perimeter shell and is known as the Tower of Light. The shell is tailored from 6mm and 8mm-thick laser-cut steel plates, which have been curved and welded together to create a stiff, strong surface.
The geometric stiffness is provided by the curves, folds and corrugations in the shell that enable the thin steel plates to resist buckling without the need for any additional stiffeners.
Digital workflows
The geometry of the shell’s corrugations and perforations was developed using digital workflows to identify a structurally optimal form. Parametric tools were used to quickly generate and analyse several variations of the geometry. This allowed the design team to study the effect of changes in the form of the shell on the buckling and fatigue performance of the structure.
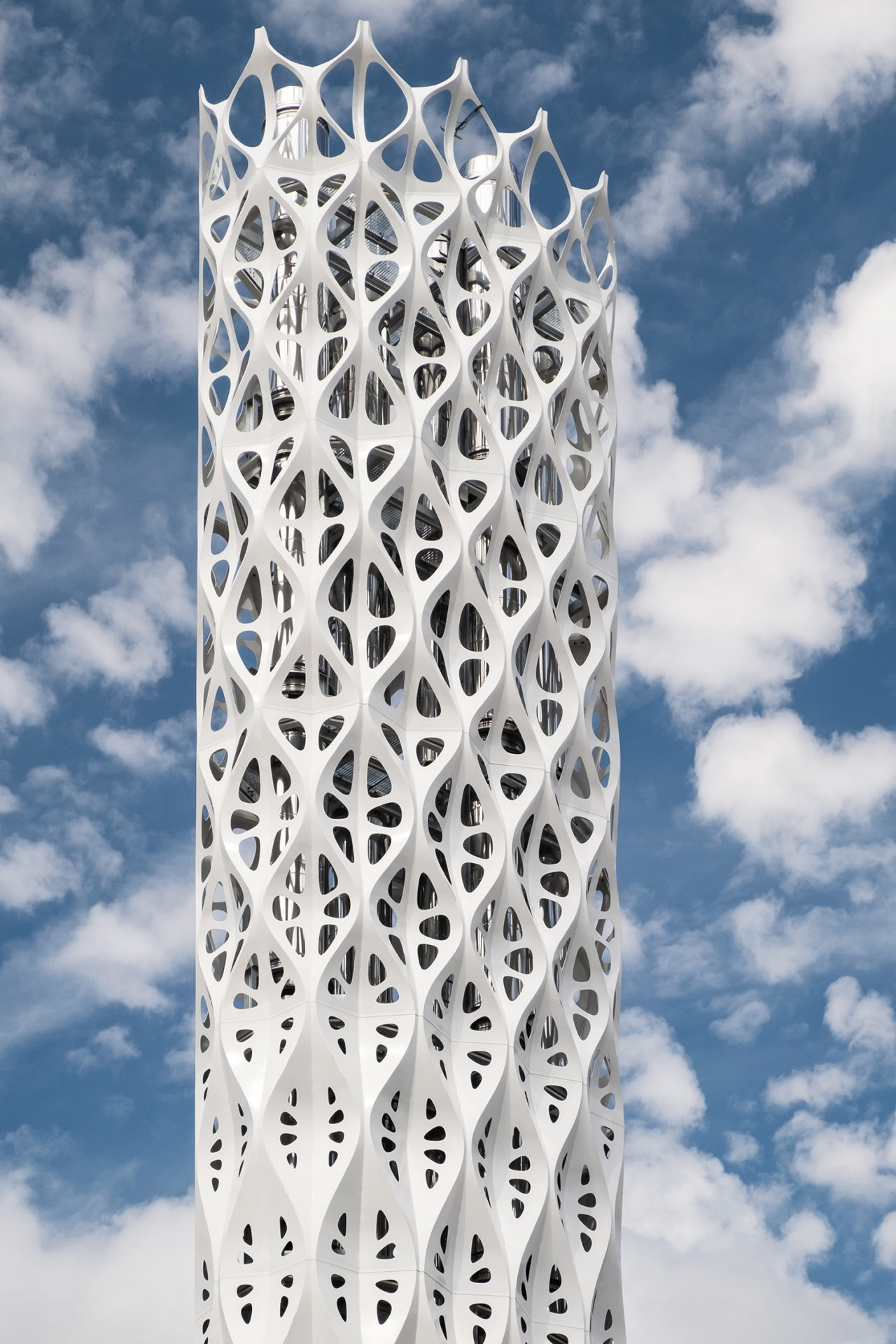
“Designing and fabricating the complex geometry of the unique structural steel perimeter shell of the tower was very challenging,” says Arup structural engineer Chris Clarke. “A structural shell of this form and scale could not have been formed in any other material, so the use of steel was integral to the realisation of the tower.”
The perimeter shell structure has the dual purpose of also acting as the facade of the tower. Using the same material to provide both the structure and the facade had a material efficiency benefit over a more conventional braced frame flue tower, which would require a non-structural facade system.
A study to compare the embodied carbon of the shell tower with a more conventional flue tower showed that the embodied carbon of this project was lower, with a vastly reduced number of components.
Stainless steel offers corrosion protection
Due to the high number of edges and corners in the tower, there was a risk that a painted corrosion protection system would not be sufficiently reliable. Therefore, stainless steel was selected for the tower shell to ensure excellent durability. The tower is painted white for architectural reasons, but this also allowed a lower grade of stainless steel to be used and avoided expensive surface treatments, thereby reducing the project costs.
“Exemplifies the synthesis of striking architectural form, advanced engineering, iterative technical analysis and craft-based fabrication. A superb example of how design can transform a utilitarian chimney into a piece of urban art, intelligently conceived and impressively executed.”
A series of decks at 4m intervals up the height of the tower support the flues and transfer their loads back to the tower shell. The decks also enable access and maintenance of the flues and have been designed with removable panels to facilitate replacement of the flues if required.
In total, the tower was fabricated as a series of nine modules. Once fabricated, modules were transported to site, stacked on top of one another and fixed together by internal preloaded bolted flange connections at the top and bottom of each module.
Flue sections were pre-installed in each of the modules prior to lifting. These flue sections were then connected when the construction of the tower structure was complete.
Produced by the BSCA and Steel for Life in association with Construction Management
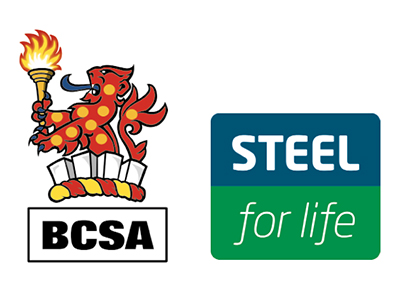