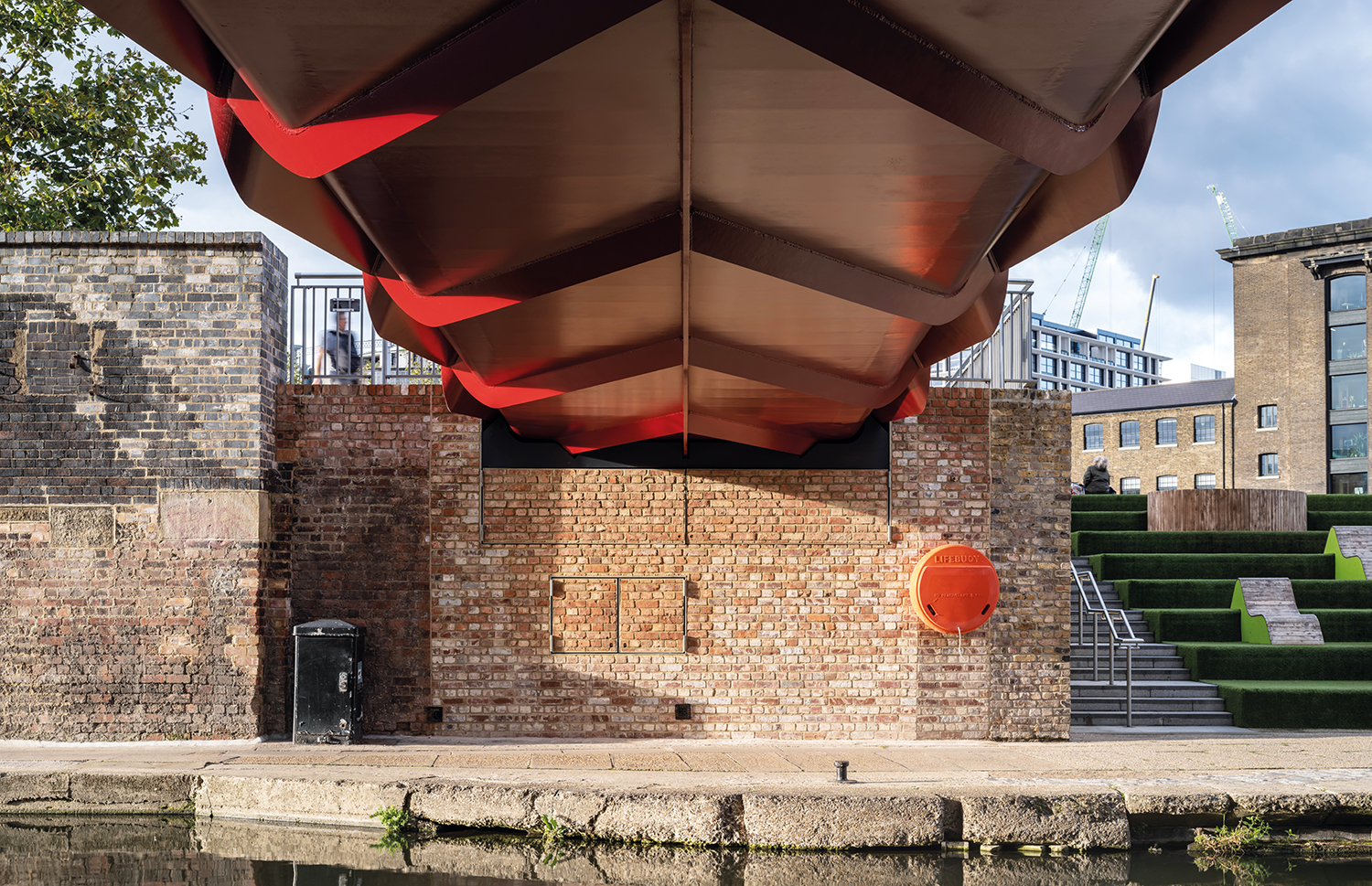
Providing a link across the Regent’s Canal, the 25m-long Esperance Bridge has an elegant and sculptural form created with tapering and folded steel plates.
Featuring high-quality finishes, such as bespoke balustrades and drainage channels, the bridge is a simply supported Warren truss made of welded steel plates with a steel-concrete composite deck.
The reinforced concrete deck controls the dynamic behaviour and acts compositely with the steel to carry the deck loads to the trusses.
Award: Esperance Bridge, King’s Cross
Architect: Moxon Architects
Structural engineer: Arup
Steelwork contractor: S H Structures
Main contractor: Galldris
Client: Argent
The top chord flows into the diagonal compression struts and continues around the bathtub-shaped structure to terminate at a longitudinal stiffener centred under the deck. Using this design, the flange provides improved buckling capacity for the struts and simultaneously restrains the top chord.
Fairing plates complete the expression of flow of forces from the top chord, down the diagonal struts and along to the bottom chord. Finally, the ties are stainless steel, expressing their differing function and reducing their visibility to emphasise the repeating truss module.
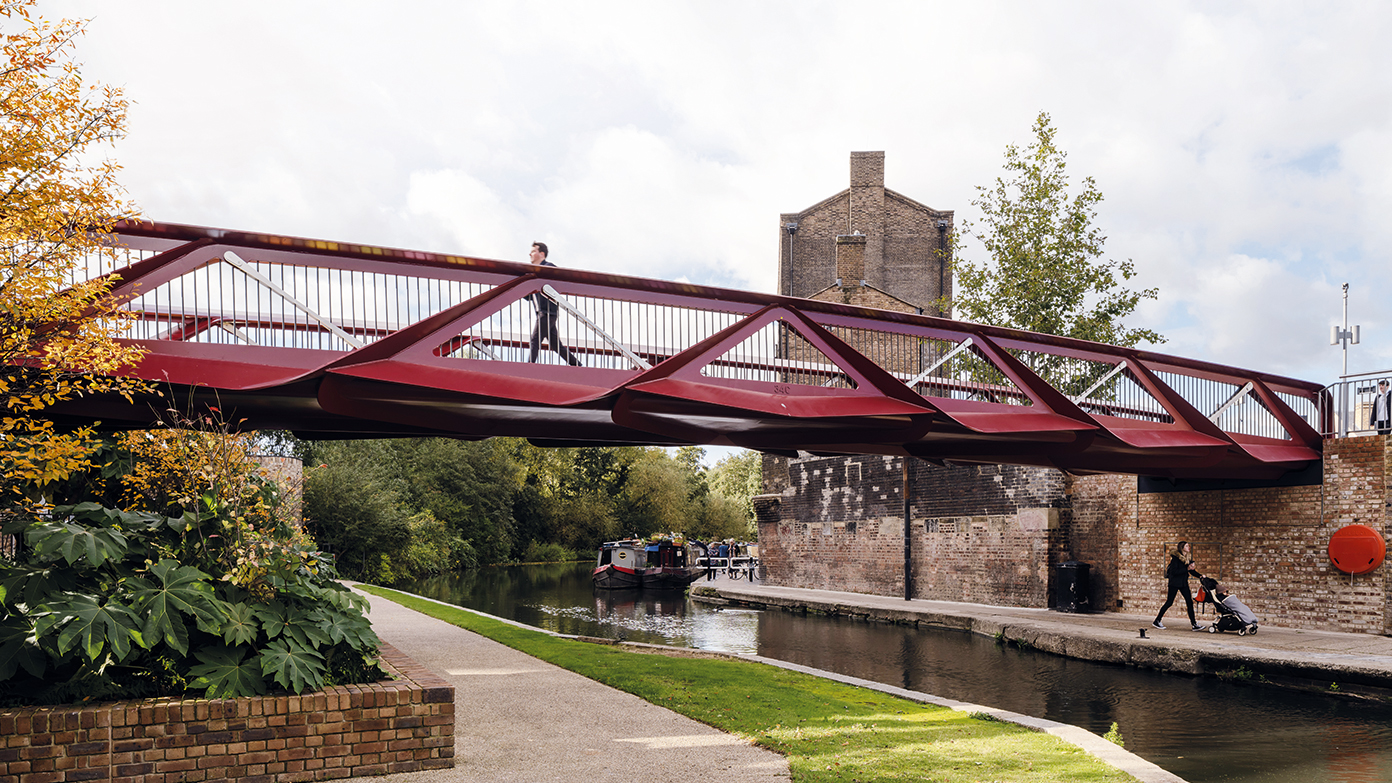
Recognising that the built environment has a critical role to play in reducing carbon emissions, the project team reused the existing Goods Way retaining wall on the south side of the bridge. This was made possible with local modifications and helped the final design for the footbridge to achieve a 20% carbon saving compared to a traditional build.
The definition of the geometry and the fabrication of the superstructure was challenging due to the complex curved shapes. The project delivery model had a period of early contractor involvement, which brought designer, architect, main contractor, quantity surveyors and steelwork contractor together at an early stage to define key details that were practical to fabricate.
“An elegant, pragmatic solution that is carefully crafted and beautifully made, its design appropriately reflecting the site’s industrial heritage. Thoughtful detailing of the curved steelwork to create the three-dimensional sculptural balustrade fully exploits the properties of steel and the potential it offers.”
Effective collaboration
The use of 3D models to review difficult details allowed for a more effective collaboration. With key details established, a mock-up of a standard truss module was produced to test the fabrication and to confirm the visual appearance of the most important plate interfaces. This allowed the team to hone visual details and push the fabrication and workmanship skills to the highest standard. While complex, the modular nature of the truss form allowed a high degree of repetition, eventually streamlining both design and fabrication.
The curved plates were formed before being welded into the final assembly by the steelwork contractor. The bridge steelwork was fully fabricated offsite, providing greater control on quality and ensuring minimal disruption to an active and congested site. For the installation process, the completed bridge was lifted over the canal in one piece.
“This exceptional design perfectly captures the proud heritage of the area that defines the development. A special thanks to our key partners that meticulously worked through every detail of the design without compromise, and to the delivery team that ensured the bridge was expertly manufactured and installed to sit perfectly across the canal,” says King’s Cross Central Limited Partnership development manager Ben Cooper.
Produced by the BSCA and Steel for Life in association with Construction Management
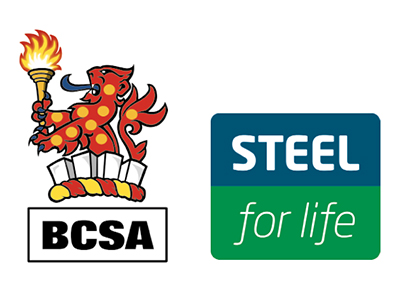