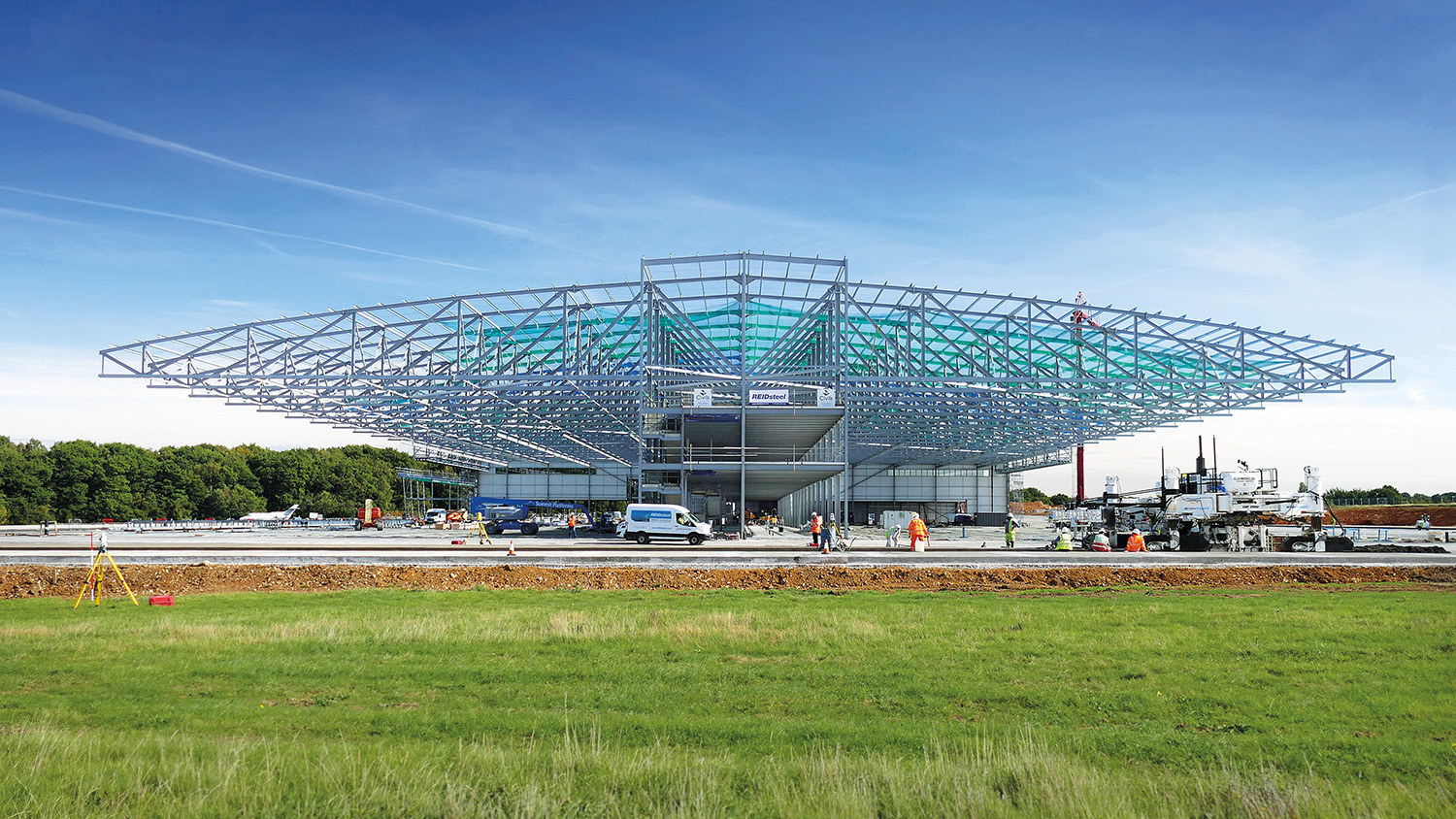
The UK’s largest dual cantilever hangar has been completed at Biggin Hill Airport for aerospace company Bombardier.
Famous for being one of the main Royal Air Force bases during the Battle of Britain, London Biggin Hill is today one of the fastest growing business airports in the UK.
Complementing a number of recent investments at the airport, a new Maintenance, Repair and Overhaul (MRO) hangar featuring a dual cantilever has recently been completed for Bombardier.
Award: Bombardier Maintenance Hangar, Biggin Hill
Architect: Civils Contracting
Structural engineer: REIDsteel
Steelwork contractor: REIDsteel
Main contractor: Civils Contracting
Client: Biggin Hill Airport Development
The hangar features two 160m clear span entrances, internal cranes for servicing aircraft, offices and a VIP lounge.
The project team say the early engagement of REIDsteel as the structural steel design and build fabricator, the hangar door manufacturer and the cladding company significantly helped the successful completion of the scheme.
Complex hangar door
The company’s input was essential as steel elements needed to be erected and aligned on 45m-long cantilever trusses that had to accommodate complex hangar door head gear and underslung cranes.
After investigating traditional hangar solutions, a more cost-effective design was proposed, which included a cantilever truss design for the hangar, conventional construction for the offices and an elegant, glazed lounge that has minimal bracing by virtue of the diaphragm within its roof structure.
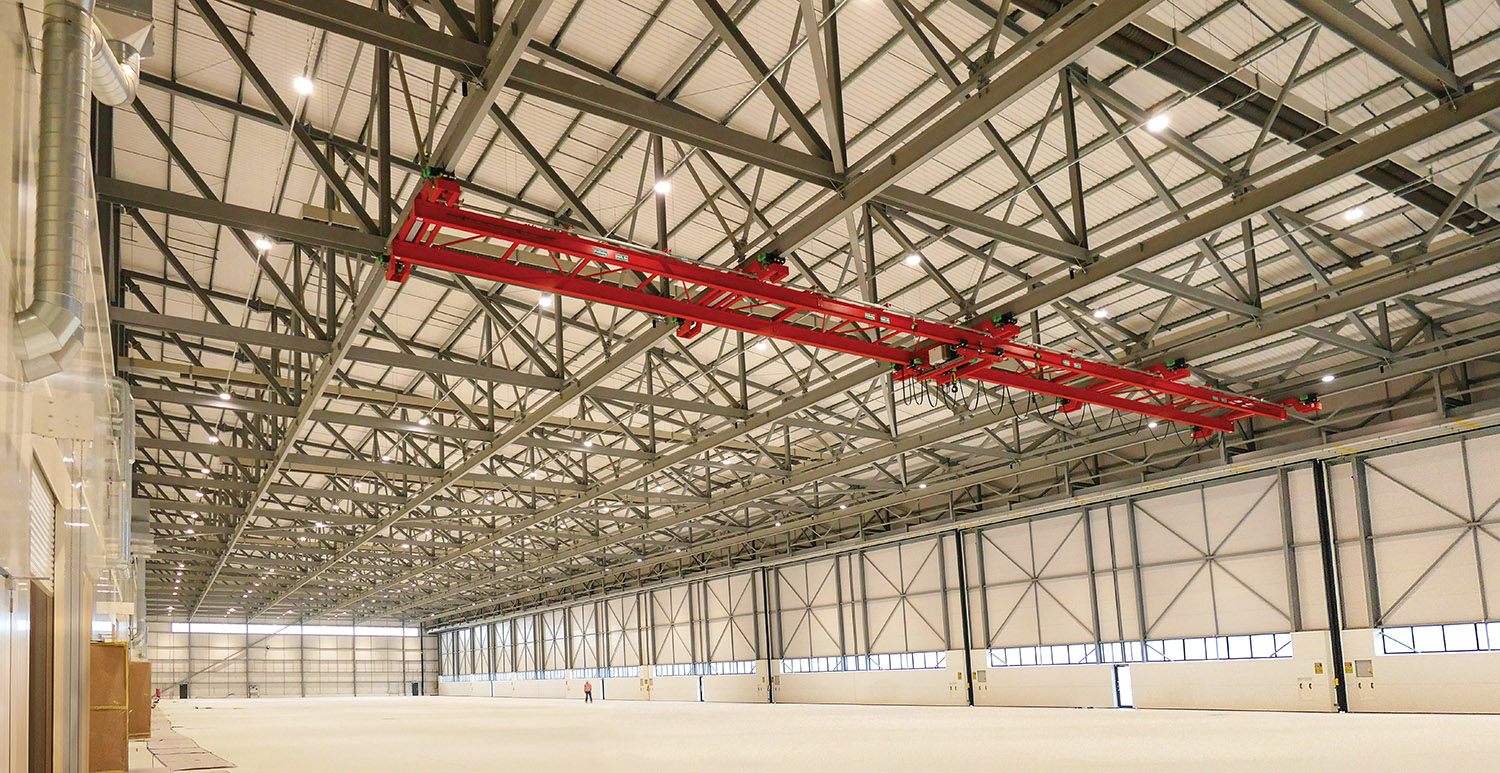
The value-engineered cantilever design, along with load-sharing elements, allowed significant reductions in material use, producing a much lower steel tonnage at 1,600 tonnes compared with more conventional designs.
The design also allowed the roof of the hangar to safely span without support from internal columns, thereby achieving the client’s aspiration for two vast, unobstructed hangar floor spaces of 7,200 sq m each.
Long span cantilevers are said to be inherently vulnerable to disproportionate collapse, due to the nature of the tension connections in the top chord. To alleviate this, and to help meet the stringent deflection criteria, load-sharing trusses were used to ensure that each frame could be supported by its adjacent frames.
“The central spine of the building anchors the cantilevers as well as housing the building’s functional spaces. The structure achieves remarkably good embodied carbon figures, in line with the LETI 2030 aspirational values.”
Unacceptable loads
This created a new issue, in that fabrication tolerances could cause a frame sitting higher than its neighbours to attract unacceptably high loads. The solution lay in leaving the load-sharing trusses ‘loose’ until all permanent loads were applied and only then tightening up the slotted preloaded bolted connections.
The design allows for the internal underslung cranes to have a 100% coverage of both hangars, rather than the previously proposed 50% of one, which has futureproofed the project.
The dual cantilever design also means the hangar can be extended to meet changing requirements over its 50-year design life.
Sustainability was a key consideration and a value-engineering exercise ensured that the final design used steel efficiently while also reducing the environmental impact.
The resulting reduction in steel weight was key in minimising the embodied carbon and saved 850 tonnes of CO2. The roof is designed to take solar panels and, assuming that the client achieves 50% coverage, this has the potential to save 300 tonnes of operational carbon per year.
Produced by the BSCA and Steel for Life in association with Construction Management
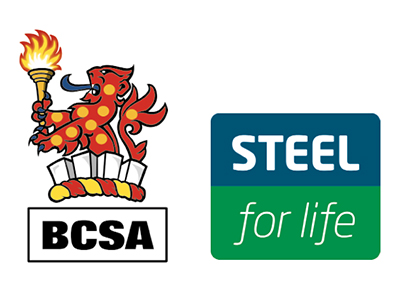