Glen Peters, technical support manager at Viega, discusses the growth of multilayer composite pipe (MLCP) and what should be considered when selecting both the pipe option and connection method
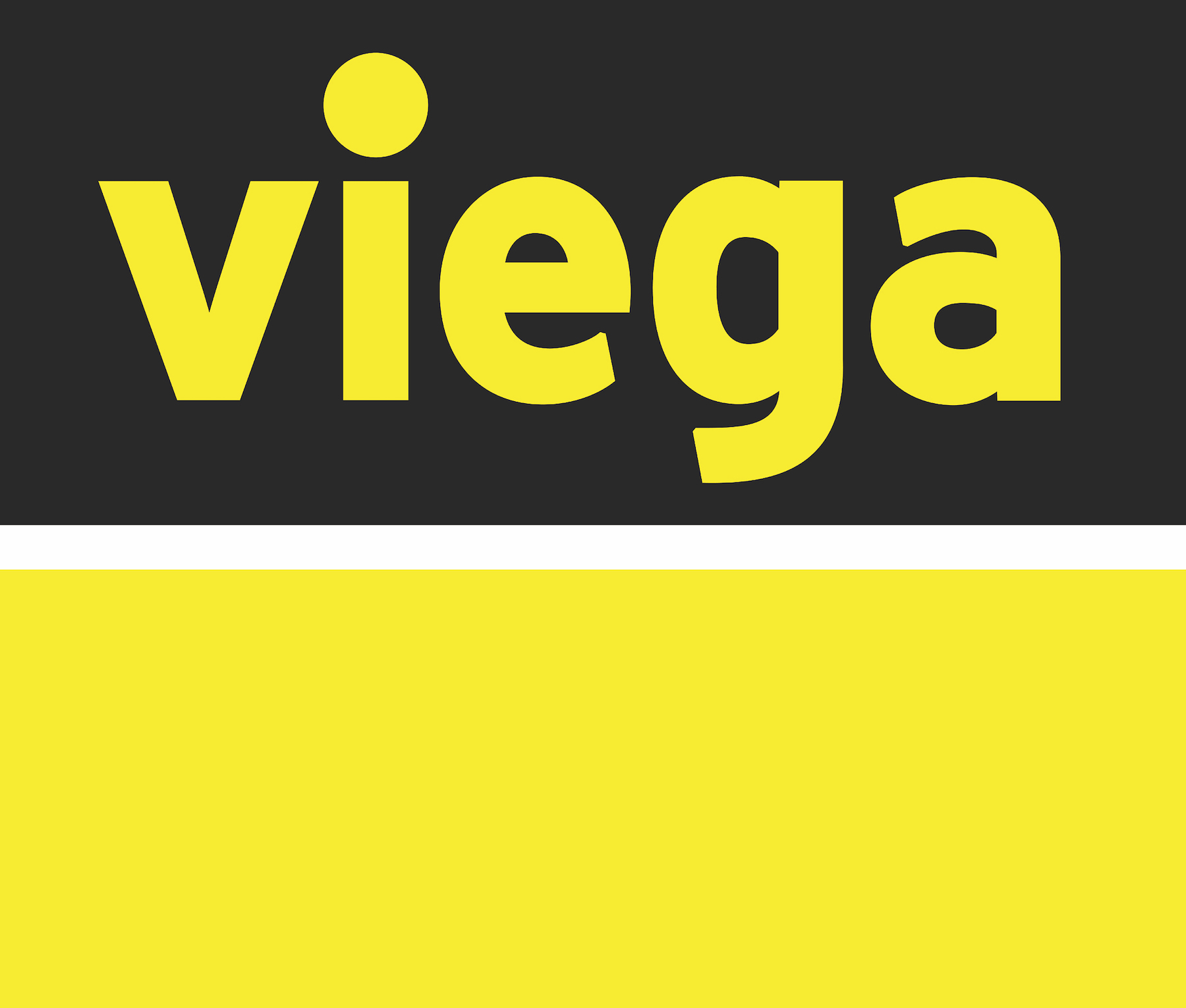
Multilayer composite pipe (MLCP) has seen a boost in popularity for applications including heating, hot water and potable water applications. MLCP is made up of an inner and outer layer of cross-linked polyethylene (PEX) with a layer of aluminium between. This design combines the strength of metal pipe with the installation flexibility and corrosion resistance of plastic.
One of the key advantages of MLCP is its flexibility. The pipe can easily and accurately be bent using handheld tools without buckling and it can be used directly off the coil. This can be beneficial on projects that have many corners and long stretches of corridor. By bending the pipe rather than cutting it, the installation can be completed much faster.
Strength of connections
To reduce installation time, MLCP can be paired with press connection technology. Using a press connection process is not only quick but also ensures a strong and permanent seal is generated with a single press.
Despite the attractions of MLCP, one of the most common causes of failure is a damaged O-ring within the fitting when low quality press connections have been used.
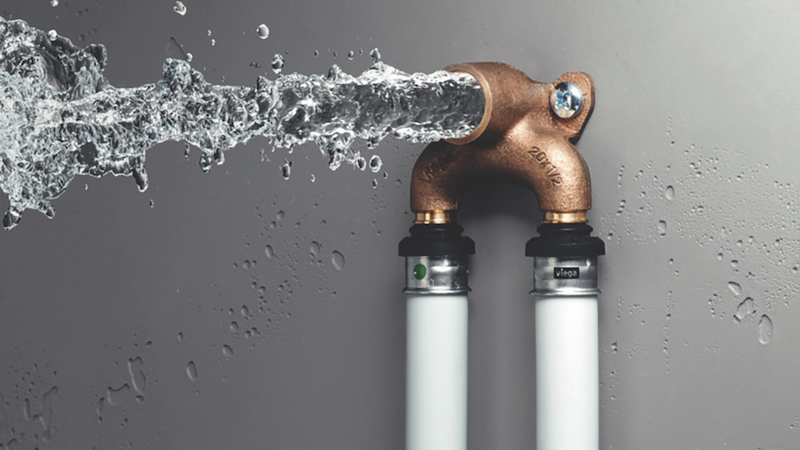
However, there are alternative products that provide a solution. For example, Viega Smartpress is a high-quality, flexible system, designed without the need for an O-ring.
The O-ring is replaced in all Viega Smartpress connectors with a robust and durable polyphenylsulfone (PPSU) support structure which, when pressed, creates a seal across the entire connected surface between the pipe and the fitting. There is no need to widen, deburr or calibrate the pipe, and without an O-ring there is no risk of damaging the seal and causing a leak.
Specify the right material
Not all MLCP is manufactured to the same standard and it is vital to select a high-quality product. It is also important to select a pipe that has the correct level of flexibility. If the pipe cannot achieve the required angle, then it might buckle rather than bend when shaped.
Another consideration when choosing a product that will carry drinking water is its suitability for the application. Any material used in the delivery of potable water must have been tested and certified to ensure that it does not contaminate the water.
“Using a press connection process is not only quick but also ensures a strong and permanent seal is generated with a single press”
Finally, during installation it is important that any unpressed connections can be easily identified before further work commences. Some press connection products will appear to be sealed during the commissioning process when in fact this isn’t the case. Once the system is up and running, even a minor leak can eventually lead to significant and costly remedial work. This is why the SC-Contur technology included in products across the Viega range incorporates a flowpath channel, meaning any unpressed joints are clearly visible during leak testing or when the system is filled for the first time.
With a wider range of pipe materials now available and press connection options suitable for every type, teams can select the one that best suits the needs of the project while still utilising a familiar and reliable connection method.
Increasingly, contractor teams are looking to press connection technology as a modern yet proven approach that can help to de-risk their projects.
Glen Peters is technical support manager at Viega.
This article was published by CM in partnership with Viega. To find out more about the Viega’s Smartpress connection system and the training and technical support available, visit www.viega.co.uk.