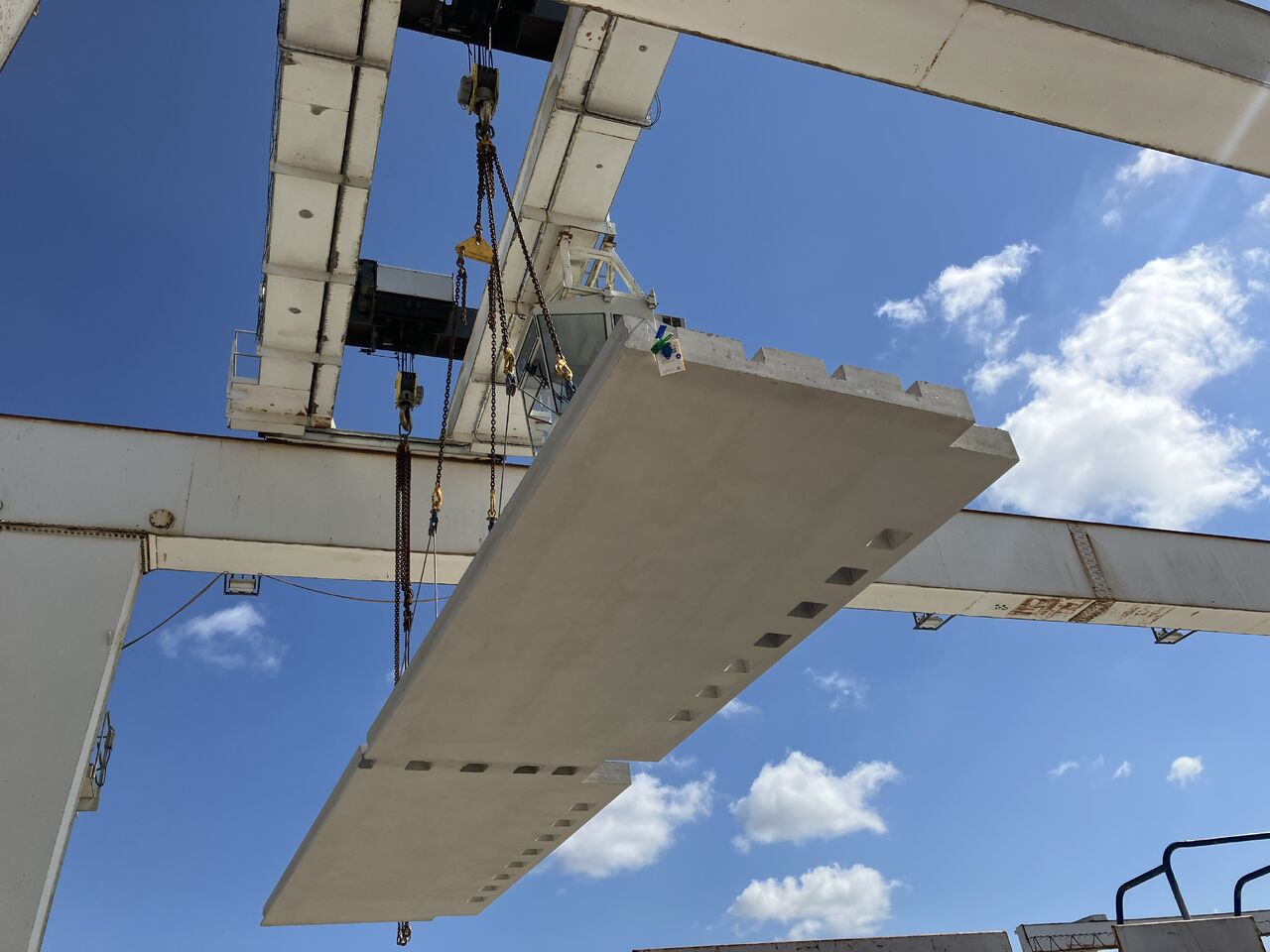
Skanska is using 3,000 precast slabs made from 50% ground granulated blast-furnace slag (GGBS) in its 105 Victoria Street scheme, which the contractor calls “London’s most sustainable office building”.
Laing O’Rourke is designing, manufacturing and supplying the precast slabs for Skanska through its pre-assembly concrete manufacturing facility near Worksop, called Explore Manufacturing.
Severfield, which is installing the planks on site, has laid around 600 across four levels to date.
GGBS, also called ‘slag cement’, is a cementitious by-product of the blast furnaces used to make iron. It is mainly used in concrete.
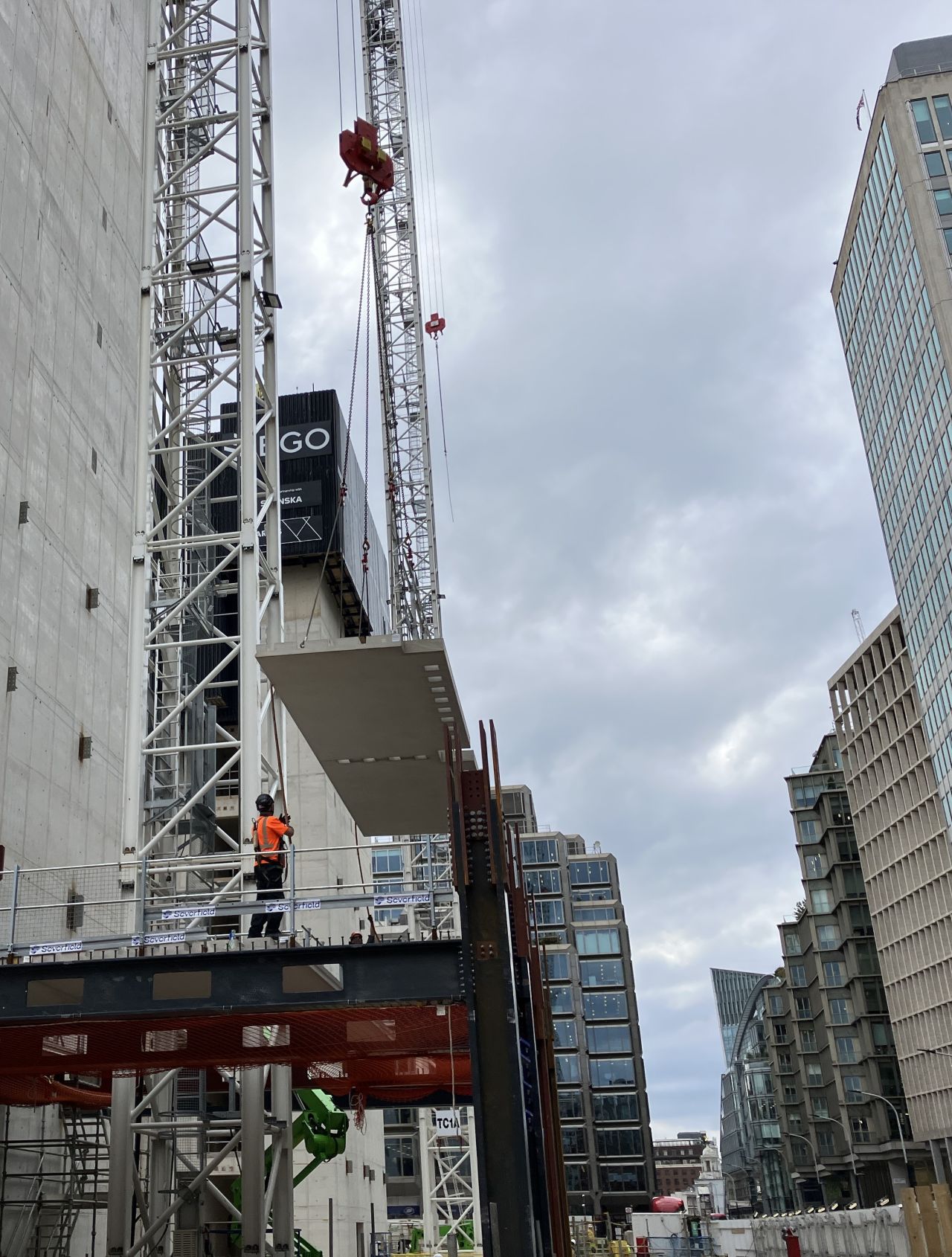
It is considered more sustainable than other cement alternatives because it has a lower carbon footprint and, as a by-product of iron-making, so it doesn’t require quarrying of new materials.
Additionally, its manufacture requires less than a fifth of the energy needed to make Portland cement.
Finite resource
A downside of GGBS is that it is a finite resource. As a by-product of blast oxygen furnaces, which rely on coal derivatives as fuel that are gradually being phased out, GGBS supply is shrinking and struggling to meet its growing demand.
The planks used in 105 Victoria Street consist of a single layer of reinforcement in the bottom mat to reduce embodied carbon.
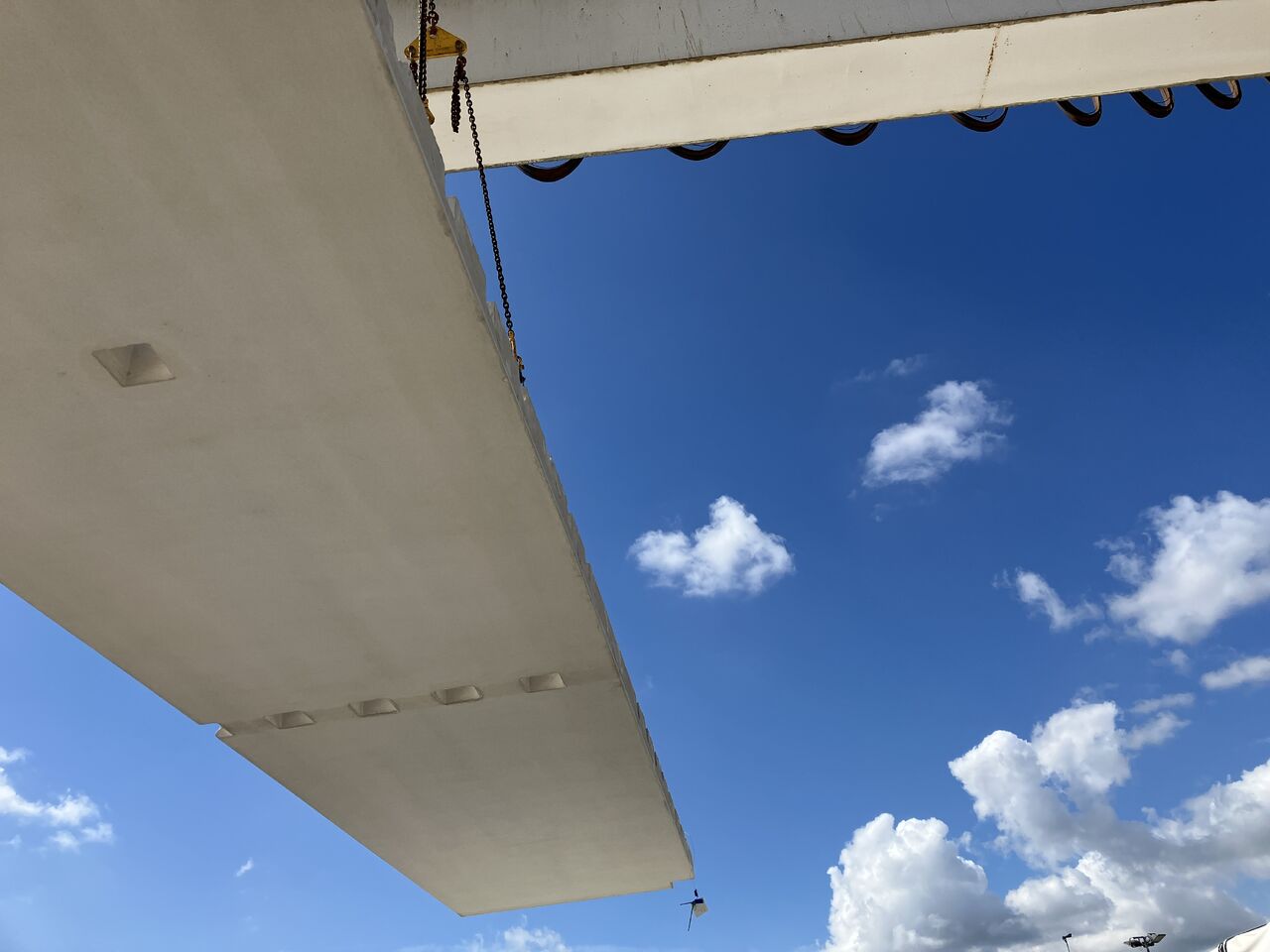
The remaining product used in the precast planks is CEM1.
Skanska is building 105 Victoria Street for US private equity real estate company BGO. The 100% electric and net-zero in operation ‘ultra-sustainable‘ office scheme is designed to achieve BREEAM Outstanding, EPC A and WELL Platinum certifications.
The building includes more than 2,000 sq m of green space and terracing, which the developers say is a record for a commercial building in the West End.
Skanska predicts that the savings for construction embodied carbon against the project’s Stage 4 baseline are equivalent to the amount of carbon it takes 151,600 trees to sequester over 60 years.
The contractor said it is prioritising carbon reductions over offsetting.