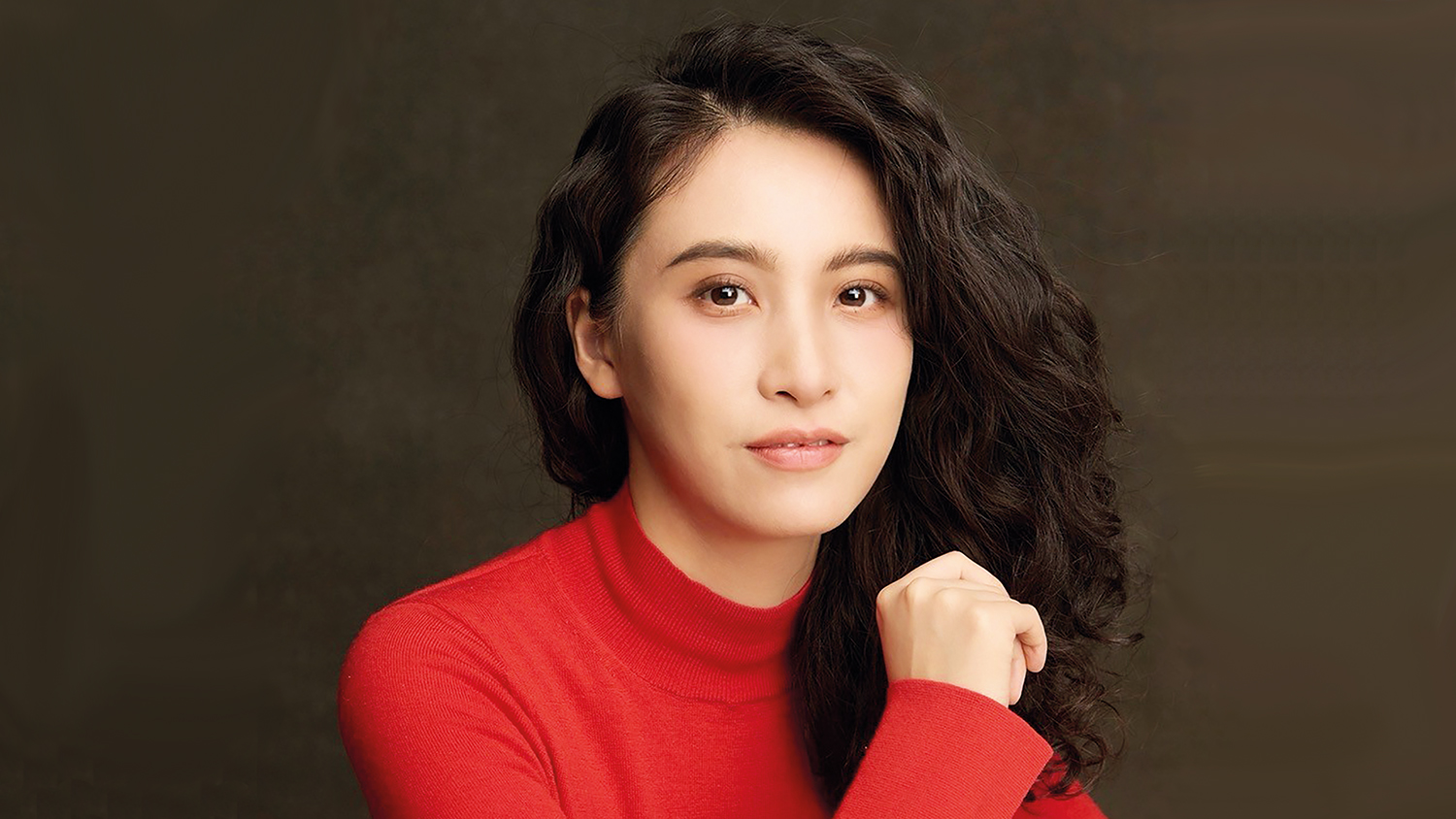
Dr Liz Zijing Li FCIOB’s PhD led to multiple awards and the creation of Mimicrete, which she now runs. She explains the innovation to Nicky Roger.
Tell us about your research
At Mimicrete, we are researching an innovative approach to self-healing concrete, where durability and reduced maintenance are crucial.
The collaboration with the Global Centre of Rail Excellence (GCRE) and Cardiff University is critical to this project, as it focuses on testing the real-world application of self-healing concrete in demanding railway environments.
Our technology embeds a bio-inspired vascular system into the concrete matrix, which allows cracks to be repaired autonomously using healing agents stored within the structure. This research is not just advancing concrete’s functional capabilities; it’s offering a sustainable, cost-effective solution to one of the biggest challenges in infrastructure – maintenance.
What is new about this research?
Mimicrete’s self-healing technology addresses significant limitations present in traditional concrete repair methods. The ability to self-heal cracks larger than 500µm [0.5mm]without the need for manual intervention sets it apart from earlier self-healing solutions, which often address only micro-cracks and have a limited capacity for repair.
Dr Liz Zijing Li CV
Work
- Co-founder, COO and inventor, Mimicrete (multiple projects), 2022-current
- Management consulting in digital, customer & marketing, Deloitte, 2021-22
Education
- PhD in Engineering, University of Cambridge, 2017-21
- Bachelor of Science in Geology, China University of Geosciences, Beijing, 2012-16
Our system goes beyond microcapsules or bacteria, which are generally limited in the size of cracks they can fix and their effectiveness over multiple repair cycles.
The healing agents in our system, which are based on advanced materials like polyurethane, sodium silicates or epoxy, can react faster due to the bio-mimetic network design. This allows for repeated cycles of repair, increasing the longevity of the infrastructure, especially in high-stress environments like railway tracks, tunnels and water-defence systems.
The combination of biological design and advanced chemistry is truly novel, and we believe it represents the future of concrete construction.
Why is this research important to the construction industry?
Concrete is one of the most widely used materials in construction worldwide. It is robust and versatile, but it is also prone to cracking due to its low tensile strength, especially in environments subject to heavy loads or extreme weather conditions.
Cracks, if left untreated, can lead to the ingress of water and other corrosive materials, eventually leading to structural failure. This is particularly problematic in railways and bridges, where safety is paramount and failures can lead to catastrophic consequences.
The railway industry, in particular, spends billions globally on maintenance and infrastructure upkeep. The UK alone spends over £51bn annually on infrastructure maintenance, a large portion of which is directed towards upkeep of concrete-based structures.
Traditional repairs are labour-intensive, time-consuming and often require significant operational downtime, disrupting essential services and increasing costs. By enabling concrete to repair itself, Mimicrete’s technology offers a radical shift in the way the industry approaches maintenance.
How will construction companies apply this research?
Construction companies can incorporate self-healing concrete into critical infrastructure projects, particularly where high durability is required, such as in railway sleepers, retaining walls, tunnels and marine structures.
The integration process involves replacing traditional concrete blocks with Mimicrete’s self-healing concrete, ensuring that cracks can autonomously repair during the structure’s lifespan.
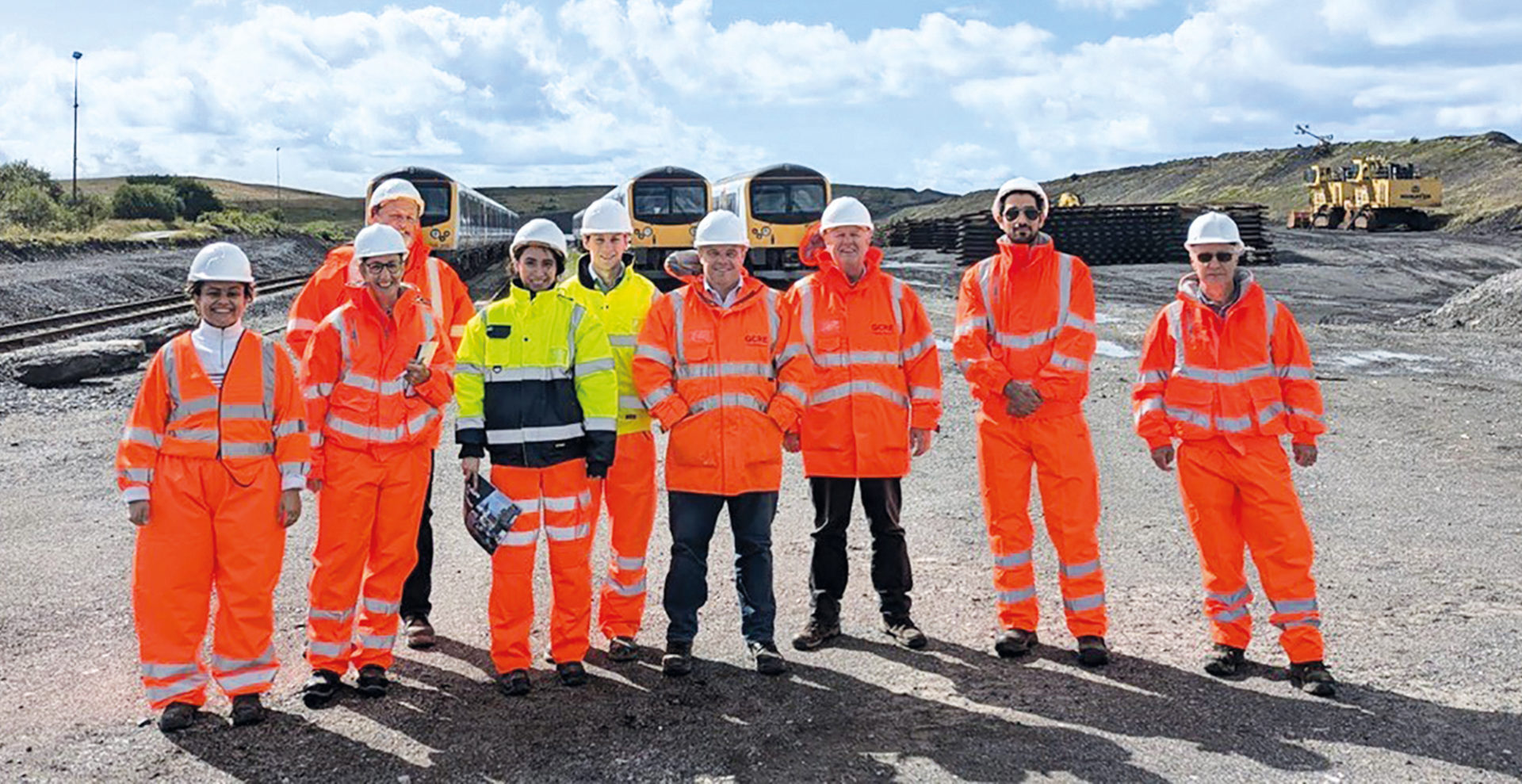
This not only reduces the need for regular maintenance but also extends the operational lifespan of the structure, making it a more sustainable and economically viable solution. In the railway sector, for instance, using self-healing concrete for sleepers and ballast support can ensure minimal service disruptions and improve safety standards.
Moreover, because our system works well in environments with high humidity or temperature variations, it is suitable for a range of applications in diverse climates – from Europe to Asia.
So it bridges a common gap between academic research and industrial application?
One of the key challenges in the construction industry is the gap between academic research and industrial application.
Often, innovative materials like self-healing concrete remain stuck in the research phase, unable to be scaled for industrial use due to high costs or lack of real-world testing.
Our collaboration with GCRE, as well as our partnerships with leading manufacturers, allows us to take our research from the lab to large-scale, real-world application.
Government support, in the form of grants and collaborations, further helps us bridge this gap, enabling us to take cutting-edge academic research and transform it into practical solutions that can be deployed at scale.
What are the future opportunities?
Other opportunities exist in sea defence, maritime infrastructure and largescale public buildings, all of which face structural stress from environmental factors.
As climate change exacerbates environmental conditions, structures will need to withstand more frequent and severe weather events, making the use of self-healing concrete a critical tool.
If you’re interested in academic membership visit www.ciob.org/membership/become-a-member/educator.