Retrofitting and refurbishing is a way to reduce construction’s energy consumption, but can it work on large projects? Sir Robert McAlpine explains the hidden costs of carbon at the Westbury Hotel.
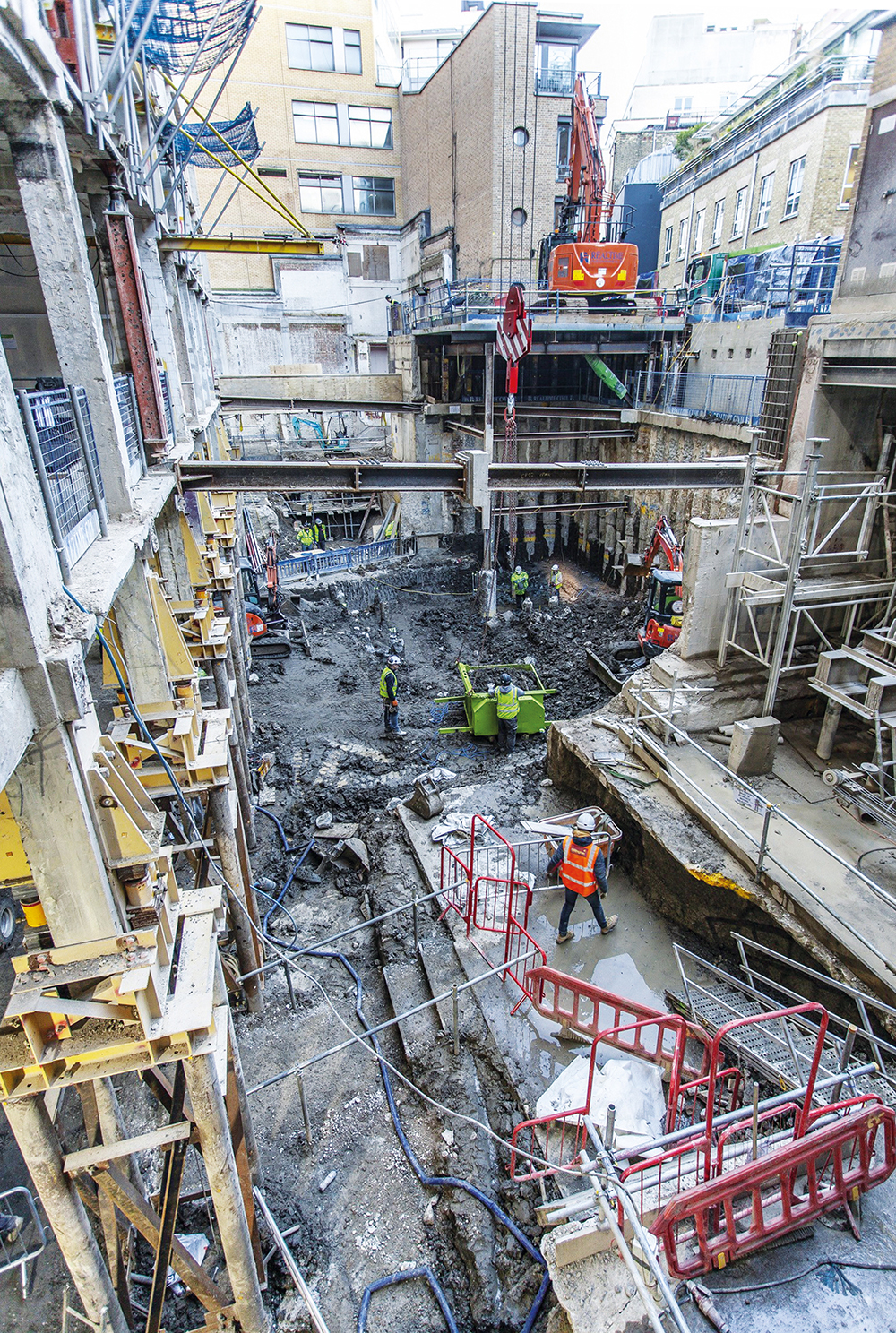
Retrofitting and refurbishing the UK’s building stock, instead of knocking down and rebuilding, is one of the key ways the UK’s construction industry can significantly reduce its energy consumption and carbon footprint.
The built environment is directly responsible for 25% of total greenhouse gas (GHG) emissions (UKGBC) and, while the industry appears to be promoting retention and retrofit to reduce emissions, it is crucial to acknowledge the consequences of larger refurbishments in terms of embodied carbon.
The Westbury Hotel in London involved horizontal and vertical extensions above and below a reinforced 1950s concrete frame to make it a ‘best in its class’ hotel in Mayfair. While its refurbishment saved over 2,000 tonnes of demolition waste and approximately 3,700 tonnes CO2e when compared to a demolition and new-build option for the same gross internal area, there were hidden carbon costs.
For example, jacking up an eight-storey reinforced concrete frame requires substantial temporary works. Each column needs unique steel jacking frames that transfer load from the existing column to temporary plunge column piles. Using mini piles in an existing building can also come with challenges, such as limited pile diameter and the use of fine aggregates and a higher cement content, which increases embodied carbon.
Refurbishments also typically require small tonnages of steelwork, and it is difficult to specify the mill or origin source of the steel, given the current procurement models of UK stockists. While reclaimed steel is preferred, it is sadly not yet standard practice.
Additional fire protection
Site investigations and fire analysis revealed the building’s existing reinforced concrete slabs and half of the reinforced concrete columns required additional fire protection to comply with fire regulations. These relatively carbon-intensive materials can add up.
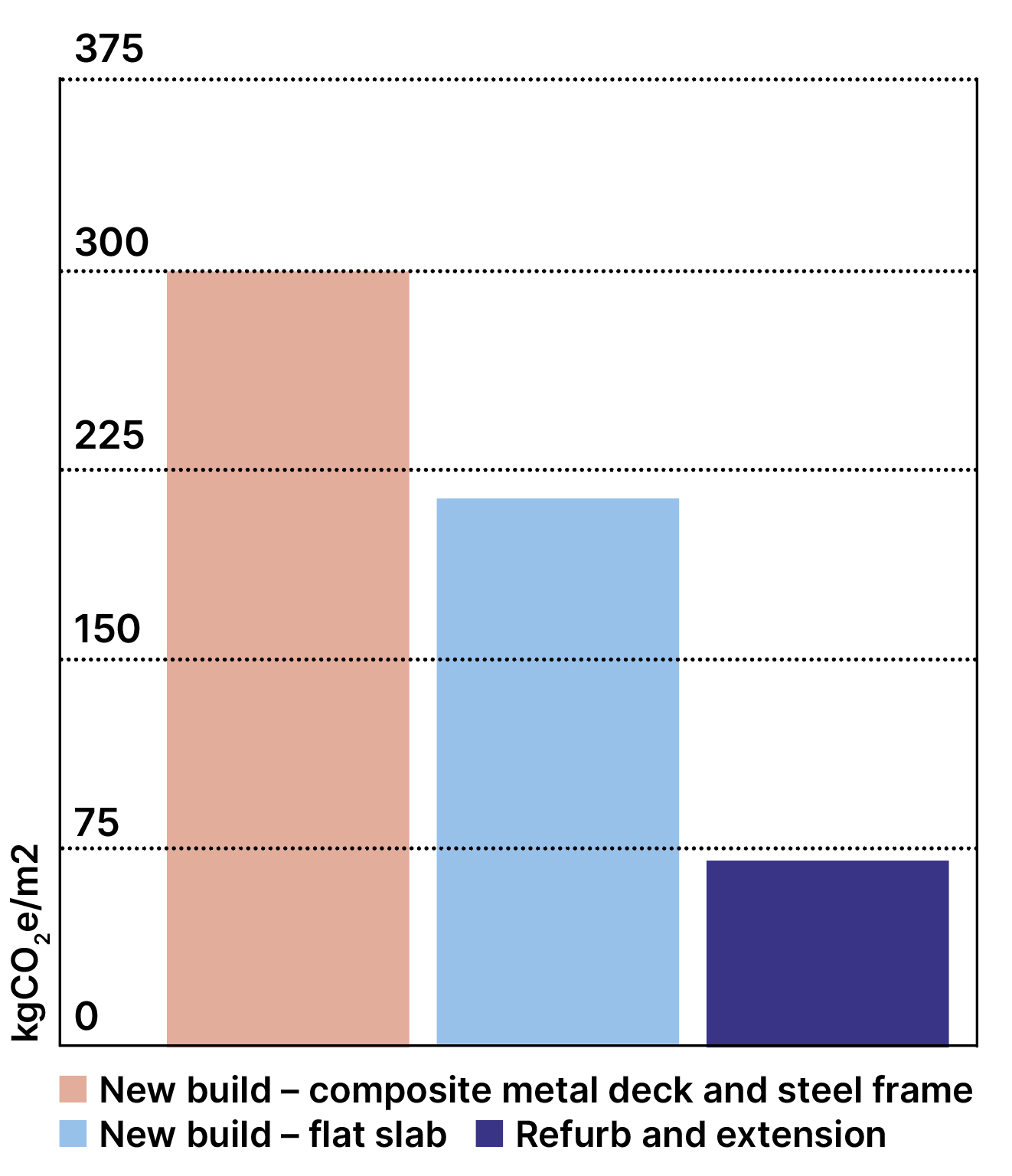
While retention and retrofit are great ways to reduce the carbon footprint of new buildings, it is essential to remember that extensive refurbishments can come with hidden carbon costs. By working with existing buildings and not imposing new-build aspirations, we can reduce carbon and improve overall design
quality. It’s key to be mindful of the small things that can quickly accumulate and increase the embodied carbon.
The Westbury Hotel is being delivered by Sir Robert McAlpine’s Special Projects division; Ramboll UK is structural engineer. Sir Robert McAlpine is committed to decarbonising its business and has developed ambitious emission reduction targets for its scope 1, 2 and 3 emissions aligned to a 1.5 deg C emissions pathway.
Sir Robert McAlpine has submitted these targets for validation by the Science Based Targets initiative (SBTi) against the Net-Zero Standard framework, currently the most ambitious designation available.
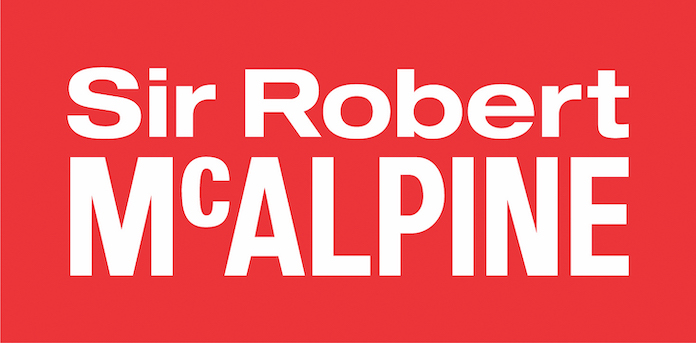
The writers – Brogan MacDonald, head of sustainability in building structures at Ramboll, Tom King, carbon manager at Sir Robert McAlpine, and Pedro Flores, sustainability manager at Sir Robert McAlpine – presented at the CIOB Conservation Conference in April 2023, where Sir Robert McAlpine Special Projects was a Gold sponsor.