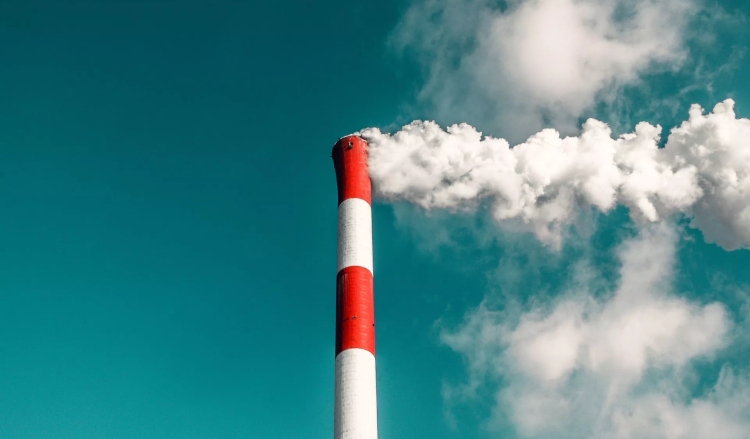
Researchers have found a way of introducing more CO2 into concrete at the curing stage, paving the way for emissions captured from industrial processes to be used in cement-making.
The researchers from Saudi oil company Aramco and the Korea Advanced Institute of Science and Technology (KAIST) claim the carbon-cured concrete sets much faster than the industry norm, and is more durable.
They added that if the global precast concrete industry implemented CO2 curing technology, it could recycle at least 63 million tons of CO2 every year, the equivalent of taking around 14 million cars off the road.
The actual figure may be as high as 246 million tons of CO2, the equivalent of approximately 53 million cars, they said.
“This is all the more worthwhile given the manufacture of cement, the principal ingredient of concrete, produces around 7% of annual global greenhouse gas emissions,” said Aramco senior research scientist Issam Amr, who led the industry-academia research project, in a note to Global Construction Review (GCR).
From research that began in 2014, Aramco and KAIST found that by using steam to introduce the CO2, they could store up to 200kg of CO2 in a ton of precast cement.
Researchers chose precast concrete because it was easier to carry out the curing process in a controlled environment.
They said their concrete cures much faster, reaching the industry required strength of 35 megapascals (MPa) in just three days, rather than the usual 28, and that it can be demoulded after eight to 10 hours.
Carbon-cured concrete is more durable, less permeable and showed a greater resistance to sulphate and chlorine, a potential advantage in offshore construction, researchers added.