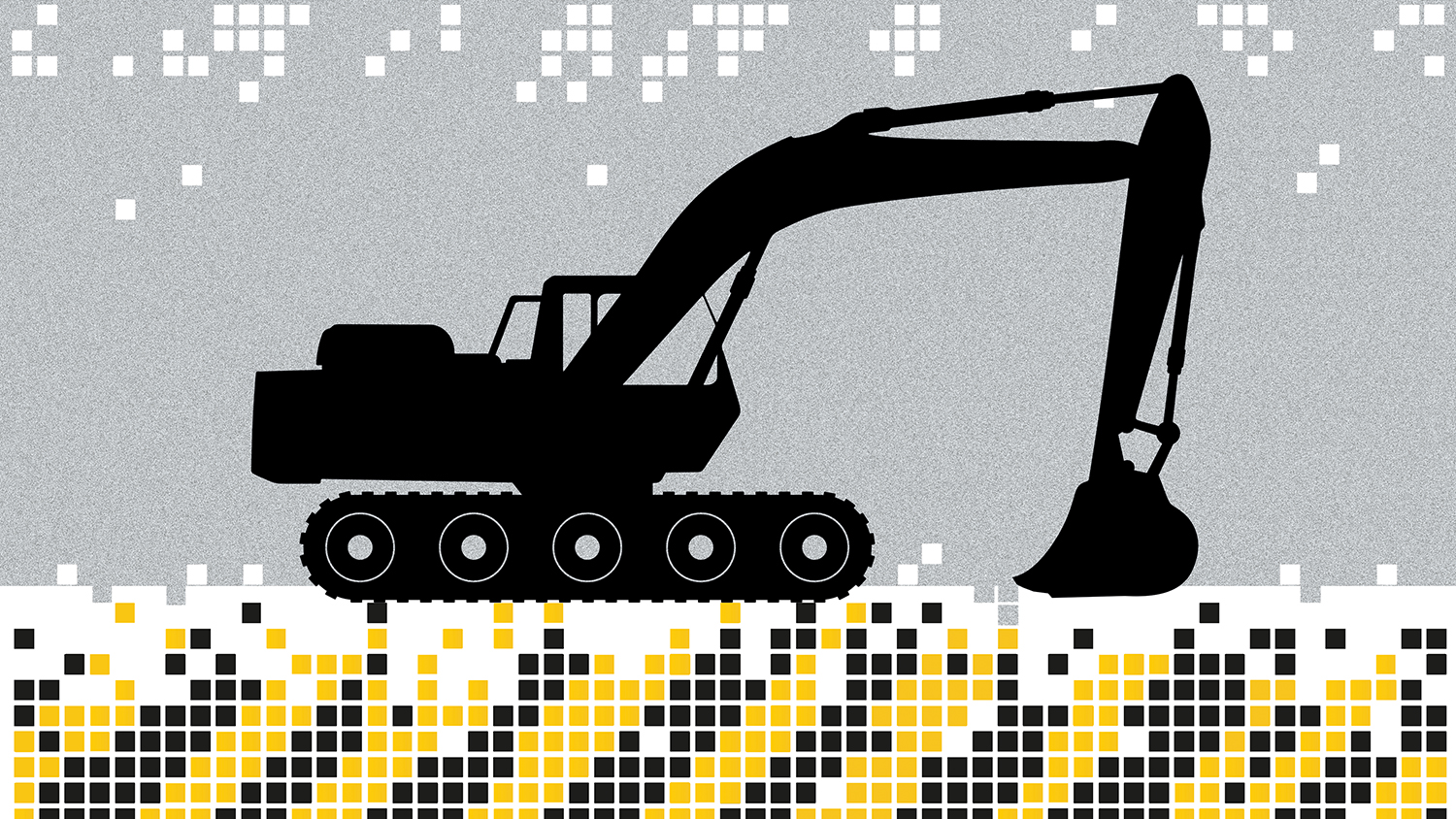
A traditional Canadian earthwork contractor hired CIOB candidate member Caia Yeung to help move from unreliable paper-based systems to full digital project coordination. She shares her story with CM.
The construction boom currently under way in Toronto has put pressure on companies to improve how they handle information. Everyone is stretched and old, paper-based systems are slow and prone to error. This leaves companies vulnerable to margin-killing mistakes and delays.
My employer, Orin Contractors, is an earthwork company specialising in excavating and landscaping. We’re subcontracted to help with the Finch West Light Rail Transit project to build an 11km light railway with 18 stops running along Toronto’s Finch Avenue West. The scope of our contract includes road excavation and construction, landscaping and building retaining walls.
Orin decided to digitalise its processes a few years ago, and hired me in the summer of 2022 to fulfil a hybrid role that combined site planning with digital pioneering. I’m one of several new hires working with senior leaders and Orin’s IT department to move the company into the digital age. Together, we implement new technologies and work out new ways of using them to improve our productivity.
It was an interesting decision to hire me. I had no construction experience; I trained as a town planner. But as someone who sits between the Millennial generation and Gen-Z, technology is second nature. Clicking, scanning, tapping and scrolling are my four main daily workouts!
The way we were
Orin used to print all construction drawings, including revisions, and stack them on a big drawing board occupying some 10% of the project office space.
This presented a number of issues. Revisions were not always up to date and, if an incorrect drawing ended up with the construction team, there was a high risk of incorrect work, leading to expensive rework. We’d waste lots of time travelling from site cabin to the work area just to verify that work done matched the latest revisions provided by the consultants.
Paper also means cost. Printing is expensive and, when details change daily in a large infrastructure project, getting documents printed, delivered, replaced and disposed of added significant administrative overhead.
“We’d waste lots of time travelling from site cabin to the work area just to verify that work done matched the latest revisions provided by the consultants.”
Paper and water don’t mix, so, given the weather in Toronto, where you can experience four seasons in one day, unless you’re laminating all drawings (more cost), you might need to print the same drawings over and over.
Much can go wrong
Foremen and site supervisors used to write critical information – about material deliveries, site inspections, site visits and manpower and weather-related information – in their individual notebooks.
If another staff member needed the information, they’d have to locate the notebook and be able to read the foreman’s writing, trusting that the information is correct.
In a decentralised and fragmented industry like construction, a reliance on paper can make it difficult to manage the contract well.
Take time and material work orders (T&Ms). They pertain to work that falls outside the scope defined in the contract, which is either requested by the client or is needed because of unanticipated site conditions.
T&M forms need to be collected from the team and submitted to the client weekly, and the client must approve the T&M before you can do the extra work. Much can go wrong when this process is paper-based.
A lack of information on the T&M form, work completed before being approved by the client, or a failure to submit the T&M form in the first place can all result in delays or extra work not being claimed.
What we are doing
Orin now uses a raft of software applications to make sure information flows to where it’s needed, when it’s needed. They include:
- Procore, for construction project management;
- SiteDocs, for safety management and inspections;
- Bluebeam, to review documents and drawings;
- SoilFLO, for tracking earth movements;
- Smartsheet, for document sharing;
- Sage, for accounts payable/receivable; and
- SmartUse, for sharing drawings.
All drawings, including revisions, are saved on Procore and SmartUse, which can be accessed by mobile devices or desktop computers. No printing is necessary as all senior staff have tablet computers, allowing them to review large-scale drawings with ease.
A similar process applies to material specifications, which allows the team to order the correct material with confidence and to plan work better as they understand the dimensions, weight and other properties of a material to ensure proper storage and handling.
No more notebooks
Now, digital daily logs let teams instantly access information formerly hidden away in notebooks. It can be used to create reports on productivity levels, material quantities, reasons for a delay and more.
The SiteDocs application brings all safety information – inspection forms, safety certifications for workers and incident reporting, for example – together in one portal.
Entering data live on SoilFLO lets us track all soil transported to and from the site. This generates accurate reports for environmental regulatory bodies.
Although we’re at the early stages of digitalising our processes, we’re already seeing the benefits of better project communication and coordination. There’s less confusion, frustration and stress.
Caia Yeung MSc is a CIOB applicant. Hamza Momade MCIOB, project manager at Orin Contractors, contributed to this article.