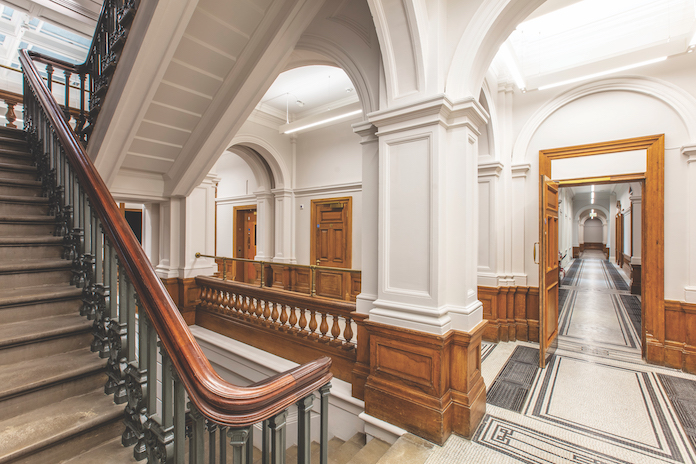
Heritage features such as oak panelling and terrazzo flooring were retained and restored
Willmott Dixon Interiors’ refurbishment of the historic Old Admiralty Building in Westminster is finally complete. Will Mann was given the grand tour
The oak-panelled corridors of the Old Admiralty Building reek with history. Backing on to Horse Guards Parade in the heart of Westminster, it has been the headquarters of the British Navy, home of Winston Churchill when he was First Lord of the Admiralty, and where naval intelligence officer and James Bond author Ian Fleming worked.
More recently, the OAB, as it is known in government parlance, has been undergoing a major refurbishment. Willmott Dixon Interiors (WDI) has been reconfiguring the Grade II-listed building with a CAT B fit out, creating over 250,000 sq ft of commercial office space across five floors, including a basement.
This has been a cut and carve operation on a staggering scale. The OAB is a rabbit warren of more than 650 rooms and the refurbishment has involved 1,000 penetrations, most of them to fit new MEP services. Heritage works have been a requirement of every corridor, room and staircase. And then there was the asbestos.
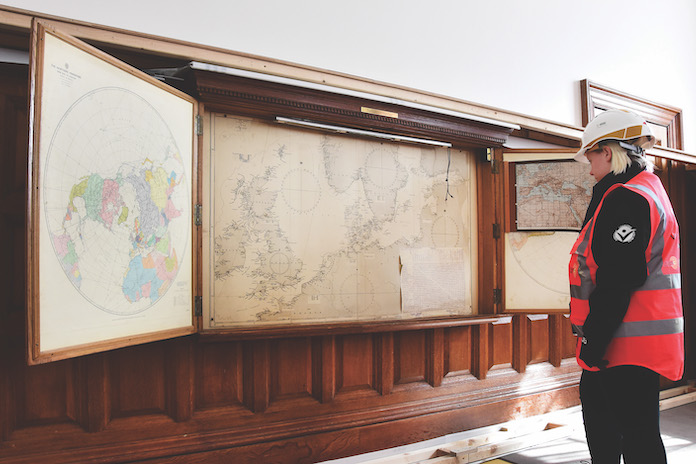
Historic maps were moved into storage during the refurbishment (Photo credit: Greg King)
“The design by BDP was about delivering a modern office, while striking a balance between the restrictions of the Grade II-listed masonry building, which was difficult to open out, and the presence of asbestos,” explains Chris Linfoot, WDI’s project director.
“Amosite is ingrained in the building fabric. It wasn’t possible to remove the asbestos so our work here has been to manage it. That has been the most difficult aspect of the project.”
The OAB dates from 1895, making it relatively modern compared to its neighbours. The masonry building comprises three wings: the north, where the main entrance fronts The Mall, was completed first, followed by the west, then the south in 1912. Its last fit out was in the 1990s, and it has been used since by various government departments. In June 2015, BAM was appointed to refurbish the building, with an anticipated contract value of £45m, but the job was retendered and awarded to WDI via the Scape Framework two years later.
There were two contracts for the project, one for the enabling works and one for the fit out, using a traditional NEC form, with a mix of options A and C. The fit out scope of work included new MEP services, about 30% of the contract value, ceilings, partitions, raised floors, window refurbishment and secondary glazing. WDI worked in JV with Willmott Dixon Construction to deliver the enabling works packages, which included demolition strip and structural alterations.
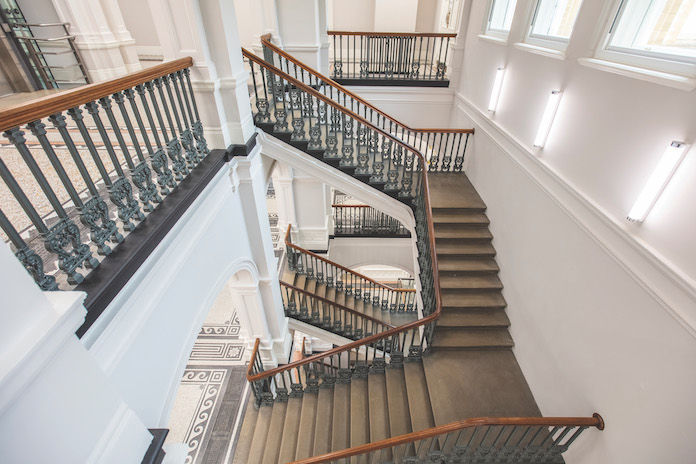
Wrought iron balustrades were restored to the original colour scheme
The presence of amosite meant WDI had to prepare a full asbestos management plan, in line with the Control of Asbestos at Work Regulations, working with two specialists, Decontaminate UK and eBrit Services. This included controlled working conditions, air locks, establishment of safe routes through the building and constant air monitoring.
“We didn’t know where the asbestos was located so we had to assume it was present when planning any intrusive work that would disturb the building fabric,” Linfoot explains. “That has been the case for all the MEP penetrations. Clinker blocks in the doorways also contained asbestos, so if we wanted to remove the door frame, that had to be done under controlled conditions. Even some of the doors had AIB (asbestos insulating board) panels in them. We had to create a sealed tent in which asbestos-trained carpenters could remove the board.
“It has affected every aspect of our work and required numerous Health & Safety Executive notifications plus visits from their inspectors.
“The amount of time we spent on managing the asbestos inevitably grew over the duration of the project. It was challenging – but we have achieved it.
“The tenants who occupy the OAB will also have to follow the asbestos management plan for the building,” he adds, “which means a ‘no drill policy’; they won’t be able to put nails into the walls to hang pictures.”
Structural alterations took place in nearly every room. Typically, these are about 1m square to accommodate the modern MEP services. Each of these required its own temporary works support structure before steel and concrete lintels were installed.
Some of the structural works knocked two rooms into one. “In one case, we had to put in extra structural steel and additional foundations in the sub-basement to support the new frame, as the existing masonry building wouldn’t support all the extra weight,” explains Linfoot.
Another structural consideration was the neighbouring MOD building, which ties into the OAB at ground and basement level on the north elevation. “This causes a pulling effect on the building and led to stress cracks appearing over the years,” says Linfoot. “So we had to insert Helifix metal rods into this elevation to effectively bind the wall together.”
The biggest structural addition was the frame to support the chillers in the main courtyard. Here, a building was demolished and around 100 tonnes of steelwork erected plus a concrete slab to support the giant chillers and pipework.
“The chillers were lifted in over the top of the OAB from Horse Guards Parade using a 350-tonne crane, in a single day,” says Linfoot. “City Lifting had to supply us with a higher-than-normal capacity crane as we needed a wider angle to lift the chiller units over the antenna wires running into the neighbouring MOD building.”
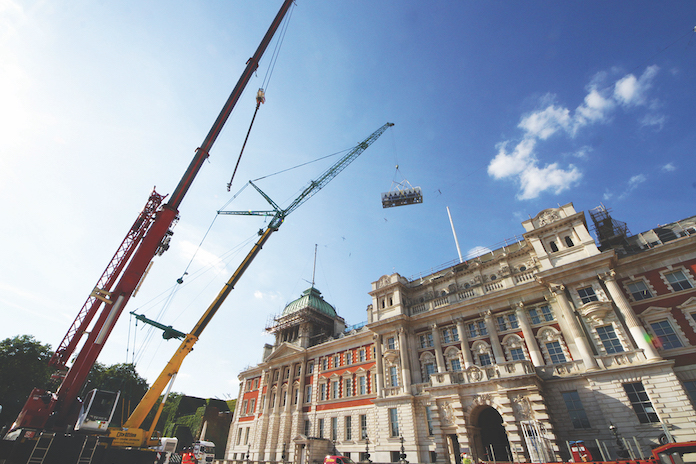
Giant chillers were craned into the courtyard over the top of the building (Photo credit: Inside Out Group)
The heritage features are strongest in the corridors, which the new MEP services mostly avoid. During structural works, heritage areas were protected with ply and decorative features removed and stored in the basement, including cornicing and around 400 oak doors.
“The original cornicing was moulded on to the ceiling and these sections were removed and later reinstated by our restoration specialist – AVV Solutions – who had to make good every individual cornice,” says Linfoot.
“A lot of the plaster on the walls had de-bonded – we used a ‘knock test’ to check this – and in these cases the plaster was removed under semi-controlled conditions because of the asbestos risk. This was replaced with lime plaster. The drawback here is the time it takes to dry, probably a week for two coats.
“Logistics was key to managing this work. We created a programme where eBrit would hack off the plaster, then AVV would follow through to replace it, moving from room to room. It gave continuity to the work.”
The project has also restored the original terrazzo flooring, oak panelling and wrought iron balustrades in the dark grey of the original colour scheme. Ironmongery for new doors has been matched with retained doors, radiators have been painted and the original glazed tiles re-exposed in the lower levels.
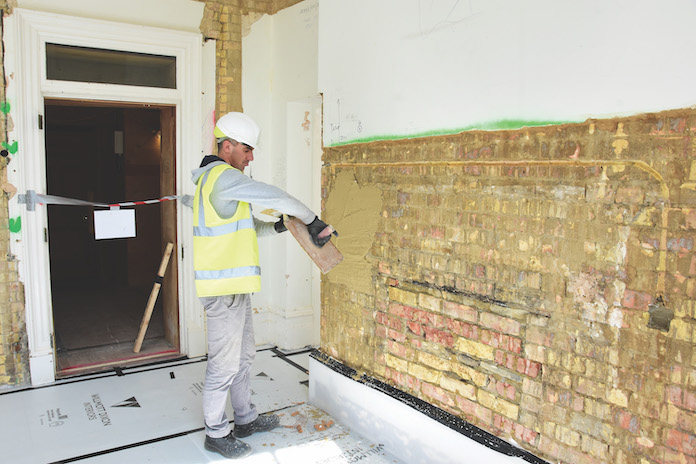
De-bonded plaster was removed and replaced with lime plaster
“The volume of the heritage works has been the challenge along with cataloguing all the items we put in storage,” says Linfoot. “This process was started by Deconstruct UK, who started on the job under BAM, logging the heritage items using spreadsheets, which we continued.”
Structural works were designed in 2D but Linfoot says a digital asset model of the new MEP has been created. “The MEP elements of the model are BIM Level 2 compliant, with asset data in COBie format, which the end user will be able to use to manage building services operations,” he explains.
WDI’s work on the project completed last month. The original completion target was late 2018 but both programme and cost will be well in excess of original estimates.
“We were constantly finding things that were not expected – inevitable on a complex refurbishment like this,” says Linfoot. “We had around 1,600 variations during the fit out, and 750 during the enabling works.”
He adds with relief that covid-19 had little impact: “We were nearing the end of our programme and the number of workers was quite low, so social distancing was easier to manage, plus we have plenty of space here to spread out welfare facilities and site offices.”
The 2,400-capacity office will house the Government Art Collection, with other tenants to be confirmed.
Project team
- Client: Central Government
- Main contractor: Willmott Dixon Interiors
- Architect: BDP
- MEP engineer: Hoare Lea
- Programme: June 2017 to October 2020
- Value: Undisclosed
Key subcontractors:
- Demolition: Deconstruct UK
- Asbestos: Decontaminate UK and eBrit Services
- Heritage plastering: AVV Solutions
- Ironmongery: John Planck
- MEP: Halsion