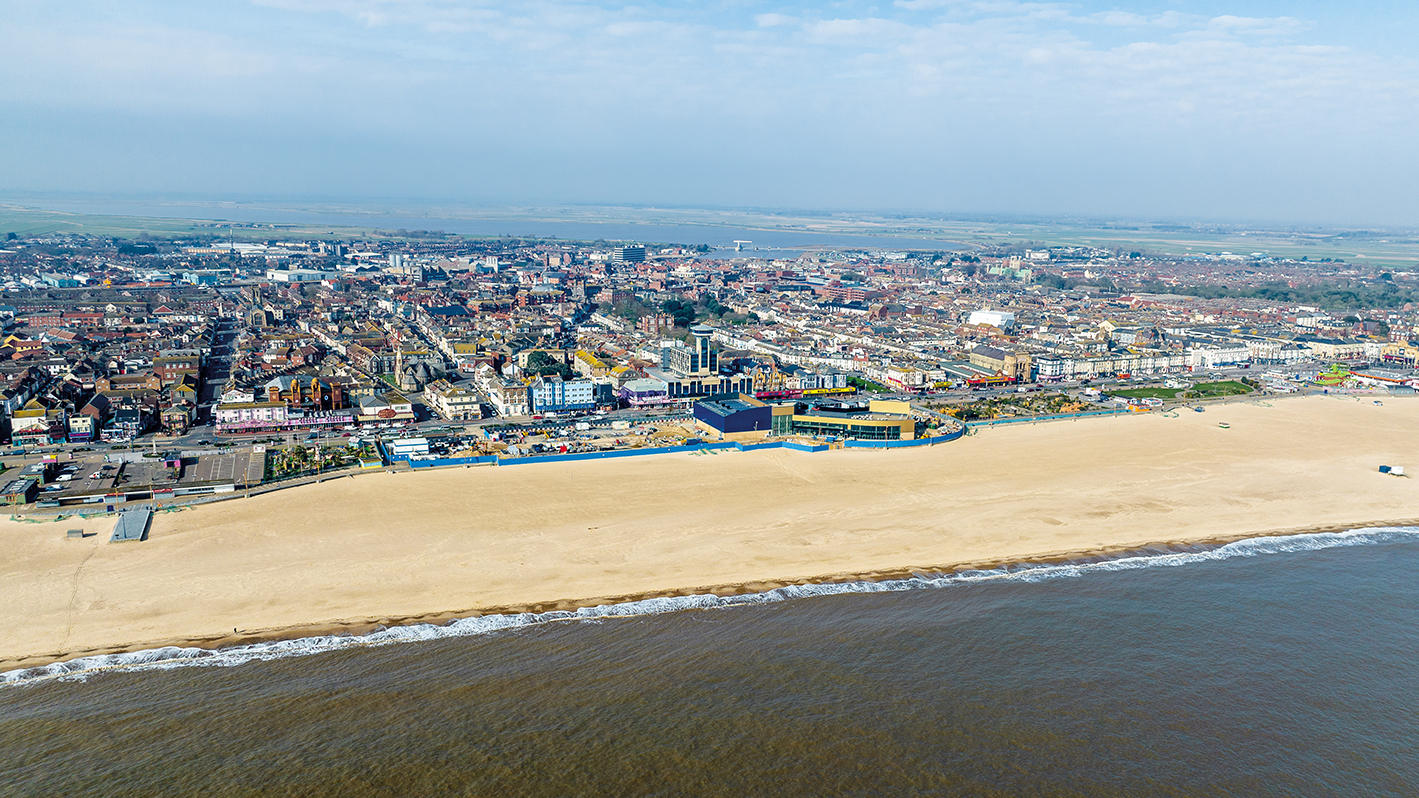
Morgan Sindall is building the new Great Yarmouth Marina Centre beside the beach. Kristina Smith hears about the construction challenges from senior contracts manager John Stedman.
Viewing the new Great Yarmouth Marina Centre from above, through the eyes of a drone, it looks like five or six linked buildings. In fact, it is just one with nine different roof levels.
This building had to look interesting. It is replacing the previous Marina Centre, a brick-clad structure, and has been designed by Saunders Boston Architects to be more sympathetic to its surroundings. Although the finished building will not be quite as striking as the architectural images released back in 2019 suggested, its variety of shapes and levels, together with a curved glass facade along the side facing the sea, make Marina Centre Mark II more pleasing on the eye.
For Morgan Sindall, which won the design-build contract to build the £26m centre at the end of 2020, the centre’s unique geometry adds to the challenges that this type of project always bring.
Project team – Great Yarmouth Marina Centre
Client: Great Yarmouth Borough Council
Contractor: Morgan Sindall
Architect: Saunders Boston Architects
Project and cost manager: Mace
Structural and civil engineering consultant: Furness Partnership
Cost: £26m
Contract: JCT design and build 2016, two-stage
Programme: 79 weeks
Start on site: January 2021
Completion: July 2022
Specialist contractors:
Vibro piling: Keller
Concrete: Acrabuild
Steelwork: H Young
Cladding: A20
Roofing: Voland Roofing, S&G Industrial Roofing
M&E: Kershaw Mechanical Services, FG Fennell, Allied Building Services
Pool: Barr and Wray
Flumes: WhiteWater
“Leisure centres are notoriously tricky,” says Morgan Sindall senior contracts manager John Stedman. “We have had that message instilled into us by the senior management team that we should make sure that no stone was left unturned.”
Some of the stones turned by Stedman and his team have included the specification and treatment of materials for a marine environment, getting the waterproof concrete for the pools right and dealing with the high ground water table that sits beneath the building.
Regaining popularity
Like many English coastal towns, Great Yarmouth is a seaside resort which hopes to regain the popularity it enjoyed during the last century as UK families rediscover the joys of staycations over cheap package holidays in the sun. Great Yarmouth Borough Council, which provided most of the funding for the new Marina Centre, hopes that this development will help with that ambition.
The previous Marina Centre was built in the early 1980s, doing over 40 years of sterling service. The council did consider refurbishing it, but in the end decided that a more affordable long-term solution would be to demolish it and start again.
The new building has a significantly smaller footprint than its predecessor but contains many of the same facilities. There is a 25m, six-lane pool, a learner pool with movable floor and a leisure pool with two flumes. There will be a route through the building from road to beach, providing opportunities to attract custom for a cafe on the way through. The building will also house a four-court sports hall, a gym and a climbing wall.
The council appointed Freedom Leisure to run the centre in November 2021. The operator has required some changes, says Stedman, although the building was already high spec: “We have worked together to incorporate changes as best we can, some as variations and some we have been able to accommodate.”
De-risking interfaces
The contract to design and build the new centre was awarded over two stages. Stedman prefers this route because it allows more planning and preparation time: “For me that’s better than single-stage bids where you have to react really quickly and have less mobilisation time.”
The design team, led by architect Saunders Boston, were not novated over on this project; instead, the council agreed to take responsibility for the design up to Stage 4, at which point the contractor took over the employment of the designers.
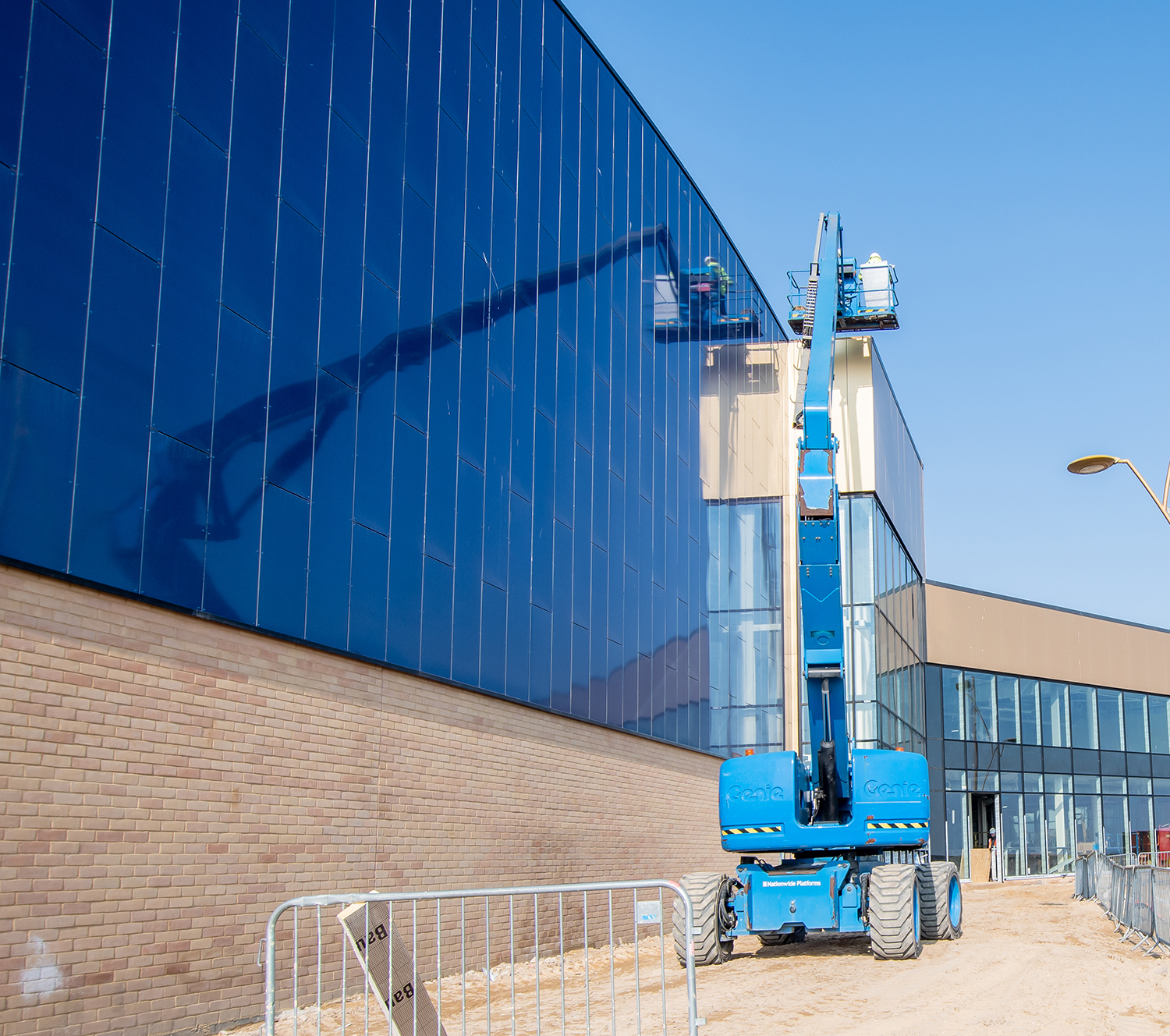
Work on site started in January 2021 with earthworks to reduce the ground level, followed by the installation of vibro piles across the site. The demolition of the previous building had already been done under another contract.
In operation the ‘wet’ area of the building, which houses the pools, and the dry side, with the other facilities, will be separated by an environmental line: a membrane to prevent the aggressive chlorine-laden air getting through. “The membrane is very expensive and needs a really high level of quality checks to make sure that it is installed and lapped and sealed correctly,” says Stedman.
Stedman came up with the idea of separating the wet and dry areas of the building from the earliest stages of construction with a sheet pile wall which then wrapped around the section of the building which will house the three pools and the basement which contains their filtration systems. This meant contractor H Young could erect the steel for the dry section as the excavation and concrete work for the wet section was under way, rather than waiting for everything to be ready at ground level.
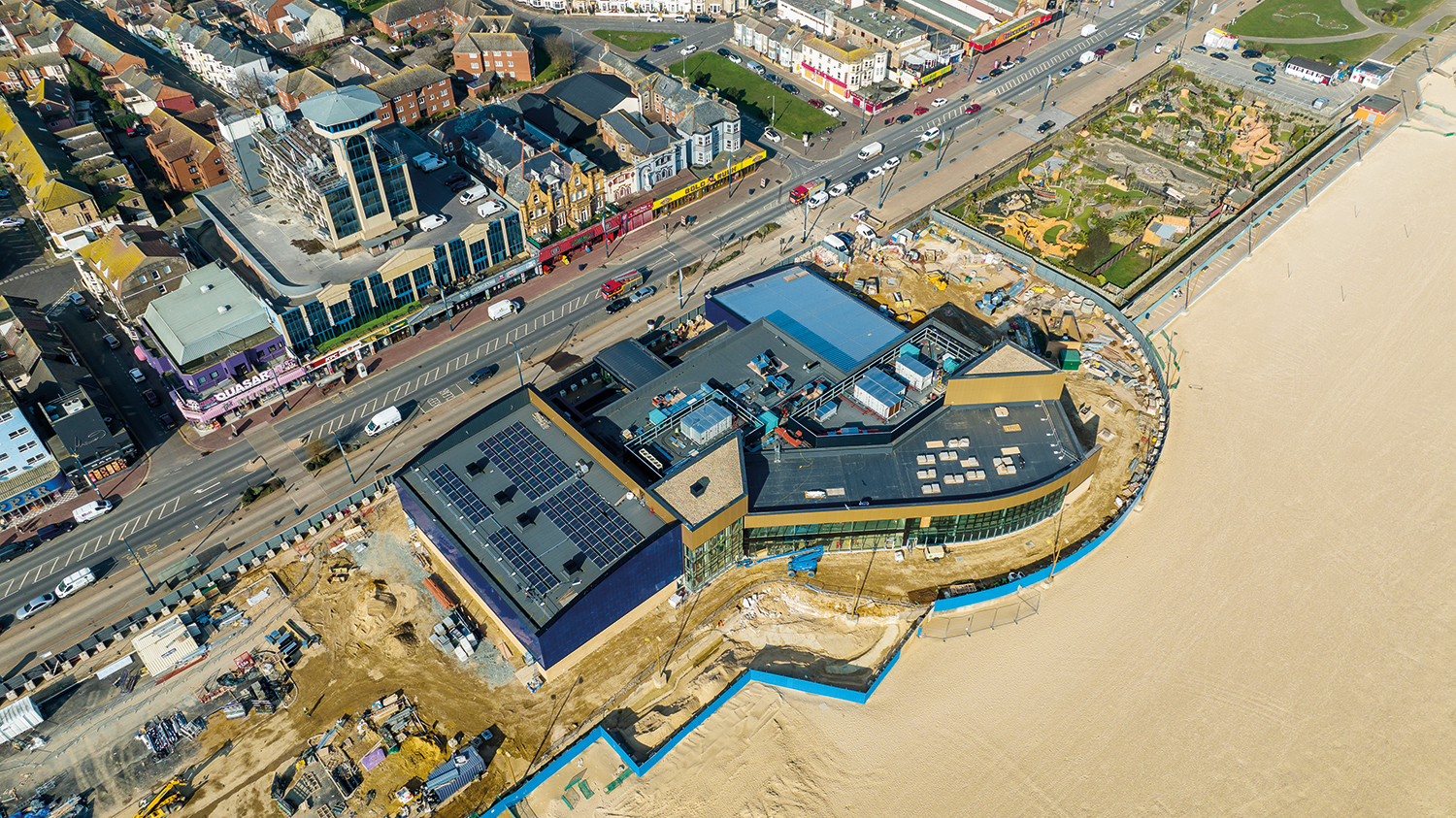
“Removing an interface means that you are de-risking it,” explains Stedman. “You are not reliant on finishing one activity before you can move on to the next.”
Another risk was the water table below the site. Morgan Sindall needed to determine what level it sat at and whether it fluctuated with the tides in order to plan its dewatering strategy for the wet side of the building.
The solution was to dig a 1.5m-deep hole and install a prefabricated manhole chamber, monitoring the level for a few months. This showed that the ground water was not tidal; fluctuations were seasonal rather than daily and the water was not saline – something Stedman confirmed with the use of a refractometer, an instrument he is more than familiar with, since he keeps saltwater fish as a hobby.
The dewatering strategy involved digging 1.5m-deep wells around the perimeter of the sheet-piled areas. The plastic tubes that formed the wells were all linked, leading to three pumps, set up to extract water at a certain rate. The water was discharged at the other end of the site in a temporary soakaway. “Because the ground is sandy, it drains really easily,” says Stedman.
Getting the concrete mix design right was another upfront activity that required a lot of attention, says Stedman. Not only must the concrete keep the water in the pools, it must keep the groundwater out of the filtration equipment basement. The selected mix has a high amount of cement replacement – ground granulated blastfurnace slag (GGBS) – and an additive from supplier FIS which reduces the permeability and water absorption of concrete.
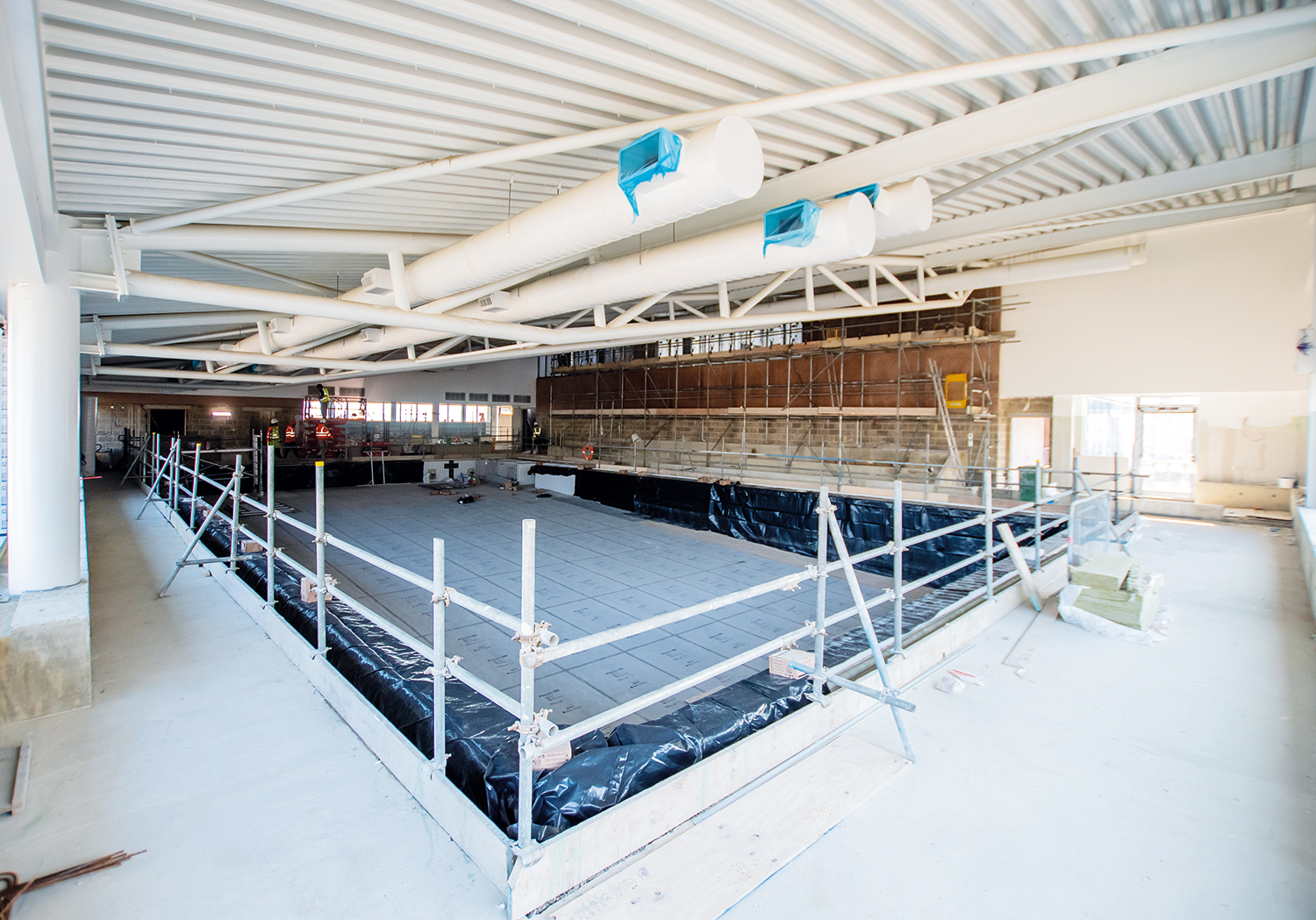
Stedman decided to test the performance of the waterproof concrete early in the programme. This involved filling the shaft with water and measuring water loss in line with British Standard BS 8007: Design of Concrete Structures for Retaining Aqueous Liquids. “Lots of theory had been applied to this element of works so we decided to test it and mock up the details in the lift shaft. That allowed us to proceed with further confidence.”
Harsh environment
One of the elements which has made this project interesting for Stedman is working in a marine environment. While swimming pools are aggressive environments due to the chlorine and other chemicals deployed in them, the products and materials used in this build had to endure even harsher conditions during the construction phase.
“Leisure centres are notoriously tricky. We have had the message instilled into us that we should make sure that no stone was left unturned.”
This has meant interrogating the specifications, ensuring that things are installed and treated correctly and then going through every detail of the warranties and guarantees to make sure they will be valid. “It has been a big journey to understand that,” says Stedman. Measures that came as a result have included additional layers of protective coating on the steel frame and the instigation of annual cleaning on the building’s aluminium cladding.
There’s a variety of cladding materials on the centre: buff bricks up to a certain level, perhaps to remember its forebear, then VitraDual aluminium cladding and the curved curtain walling. Morgan Sindall removed another interface in planning the cladding construction; rather than having to wait for the brickwork to be complete before installing the aluminium cladding on top, the contractor installed ‘helping hand’ brackets off the steel frame to support the cladding.
In April, Netherlands specialist Variopool was installing the movable floor in the learner pool. Morgan Sindall has worked with them recently and with Canadian contractor WhiteWater, which is responsible for the flumes and play equipment in the leisure pool on the Britannia Leisure Centre in Hackney, east London. It is impossible to find local firms to do such work, since the work is so specialist that few of them exist worldwide, explains Stedman.
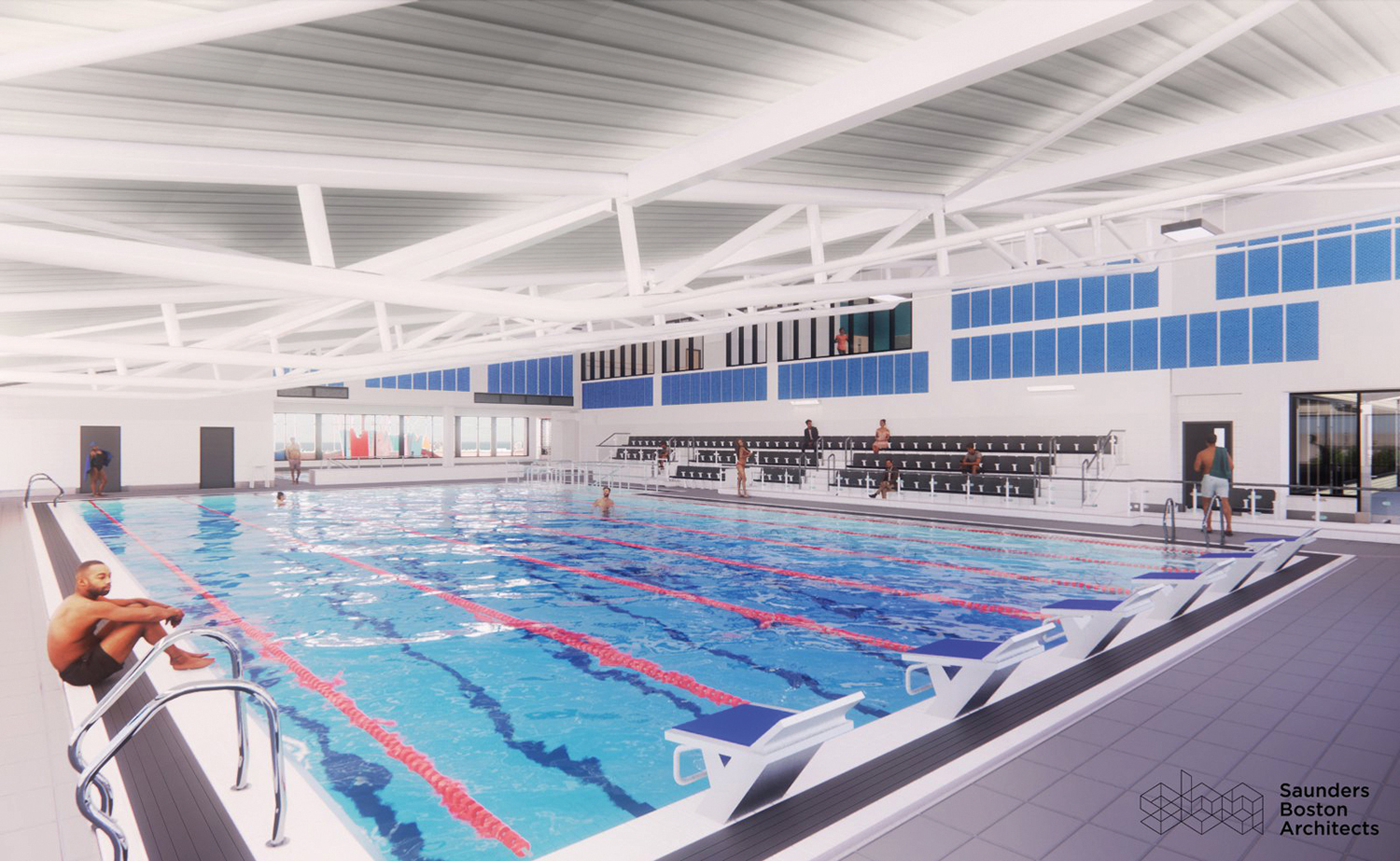
Those very specialist elements aside, many of the subcontractors on this job have come from Morgan Sindall’s established supply chain in the eastern region. That means that quite a few of the people working on the new Marina Centre have fond memories of the old one.
“What has been nice is that a lot of the subbies have been quite keen to work on the job because of their memories of Great Yarmouth from the past,” says Stedman.
Unfortunately, one of the contractors on the scheme, M&E specialist Kershaw Mechanical Services of Cambridge – a firm with a 75-year history – went into insolvency earlier this year, something that Stedman does not want to comment on. That just goes to show that it is impossible to turn every bad stone on a project like this.
However, Stedman remains confident that the Marina Centre will be handed over on time in July this year. If that happens, the combination of invested workers, meticulous planning and de-risking of interfaces will have paid off. “It will be the best project of my career when completed,” says Stedman.
CV: John Stedman MCIOB
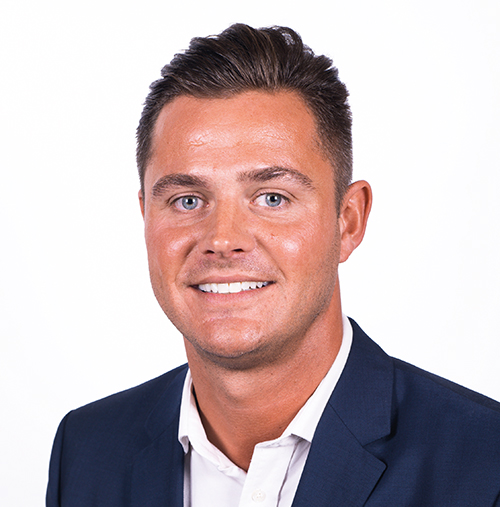
John Stedman didn’t understand the point of studying when he was at school, but all that changed when he started working for regional contractor RG Carter and got an appetite for learning.
He followed an apprenticeship as a carpenter with a foundation degree in Construction followed by a first class BSc in Construction Management and later a NEBOSH health and safety qualification.
“Getting a degree was quite significant for me because of the application that was required to get it. I could not have done it after my A-levels,” he says.
“People take different times to mature. My advice to anyone starting out would be to find something you are really passionate about and to believe in yourself. That’s massive.”
After 11 years with RG Carter, Stedman moved to Morgan Sindall six years ago and hasn’t looked back. He was promoted to senior contracts manager in 2019. He loves complex jobs with technical details, like the linear accelerator facility for Norfolk and Norwich University Hospital that he worked on when at RG Carter – and the Marina Centre.