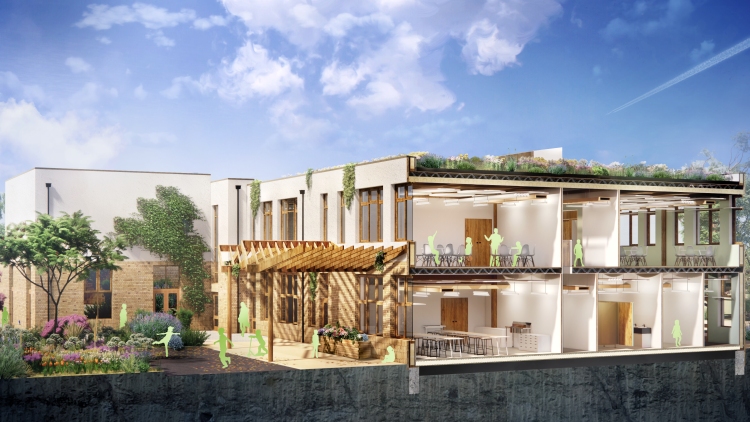
Morgan Sindall and a group of architects and consultants have digitally remodelled a school the contractor built four years ago to slash the project’s whole-life carbon by two thirds.
The Circular Twin project took a school Morgan Sindall constructed in 2017 and digitally reimagined the build process from start to finish with low carbon as the driving factor, rather than cost.
Compared with the school in real life, the reconceived version had a 67% reduction in whole-life carbon, a 72% reduction in the upfront embodied carbon, and a 39% reduction in forest consumption, according to BIM+.
Capex was delivered within standard budgetary parameters, although there was a “modest” increase in costs. However, the low-carbon version also delivered a 52% reduction in annual energy consumption, and long-term energy savings for clients.
“This initiative has uncovered a revelation – that low-carbon construction is inhibited by our industry’s reliance on traditional design and procurement approaches. The outcomes show that achieving low-carbon buildings is possible today,” said Louise Townsend, director of social value and sustainability at Morgan Sindall Construction.
“By engaging with contractors at the design stage, we can work with customers to design significantly lower-carbon buildings, whilst also working within their budget parameters.”
The project was brought together by Morgan Sindall Construction as a top tier contractor, with procurement specialist Scape, architects HLM and Lungfish, and multi-disciplinary engineering consultancy Cundall.
Townsend added: “By engaging with contractors at the design stage, we can work with customers to design significantly lower-carbon buildings, whilst also working within their budget parameters. Of course, there will be trade-offs and the ultimate cost depends on how far the client wants to go in terms of reducing carbon.”
Townsend said the study was “hard evidence” of what can be achieved, and was a “much-needed” and radical, industry-led response to the climate crisis. It could also empower local authority clients – of whom 300+ have already declared climate emergencies – and other organisations to reach increasingly ambitious sustainability goals.
Yasmin Nally, associate architect at Lungfish Architects said the project “demonstrated that a sustainable school with carbon at the centre of the decision making is completely possible without special measures, provided a collaborative team and environment is established early”.
A Lifecycle Cost Model, of 60+ years life expectancy, of the reimagined school was created from guidance of more than 250 supply chain partners. Study participants believe the project could be the first to put into practice the strategies of the Construction Playbook and guidance from the UK Green Building Council.
Chris Clarke, director of performance and improvement at Scape, said: “Any part of a project team basing decisions on cost alone is inhibiting low-carbon construction.”
Alex Carter, partner at Cundall, added: “Working with the supply chain on material selection and collaborating with the wider design team to develop low-carbon design options will allow us to make more informed decisions in the future. This not only increases the skills of all involved, but also helps the whole of the building industry to raise its game.”
Comments
Comments are closed.
This article would be more useful if it described how this carbon reduction was achieved over the life of the building and what percent increase in CAPEX was required.
No mention of cost uplift for this virtuousness
Oh please, a revelation? That low-carbon construction is inhibited by our industry’s reliance on traditional design and procurement approaches? This has been know for decades but with the industry driven by profit-first contractors, changes don’t happen until legislation forces it. Main contractors can no longer ignore the writing on the wall and it is correct and proper that they should begin changing. Late is better than never. And there’s another indicator – since when do main contractors have a director of social value and sustainability? Well, now, it seems. If you really want to see what is achievable, don’t look to small-scale, one-off theoretical efforts in the UK, look to countries with more extreme climates than ours and a building industry with a different ethos. They’ve been achieving trailblazing results for years now.
You missed out all the actual information!
“Compared with the school in real life, the reconceived version had a 67% reduction in whole-life carbon, a 72% reduction in the upfront embodied carbon, and a 39% reduction in forest consumption”… Really, HOW? from where to where…
This is like an article from the 1990’s! can we not start taking about real figures in TCO2eq, and what can really be done on the “next scheme”.
I’m less worried about the cost, but I do feel articles like give us very little beyond a worry this is simply greenwashing – I’m hoping to be proved wrong!
Gordon Brown
MCIOB CEnv.