Civils firm O’Keefe has been trialling new technology to ensure offsite modules line up with groundworks, explains Ross Halliday.

One of the many benefits cited by modular construction advocates is the enhanced quality and precision that comes from the factory building environment. But this can give rise to problems when the modules arrive on site. This is where the close tolerances of factory precision come up against the inevitable approximations of traditional site methods. It is not uncommon to take delivery of a factory-made module only to find some misalignment of service penetrations or even foundation elements.
The basic issue is not so much site operations mismatching the precision of the manufactured module, but the need for collaborative coordination between the factory and the site.
This was demonstrated on a project where O’Keefe provided the groundworks and constructed the bases for a row of new homes built using a modular system.
As the first unit was craned into position, it became apparent that services did not line up and installation had to be temporarily suspended while onsite adjustments were made.
Once the problem had been rectified, the project continued as planned, but we started to think about how we could prevent this from occurring again. This was not a BIM project, and in any case, we find BIM models are not widely shared by our offsite manufacturer partners due to intellectual property concerns. Nevertheless, we decided the answer was to create point cloud surveys of the site as built.
Using proprietary design software (BIM 360 and Navisworks) we can produce images that the modular manufacturer can overlay on top of their drawings to ensure complete compatibility.
Just as modular buildings are repeatable to a very high level of consistency, we considered that some method for replicating our substructures would help to ensure compatibility with offsite modules.
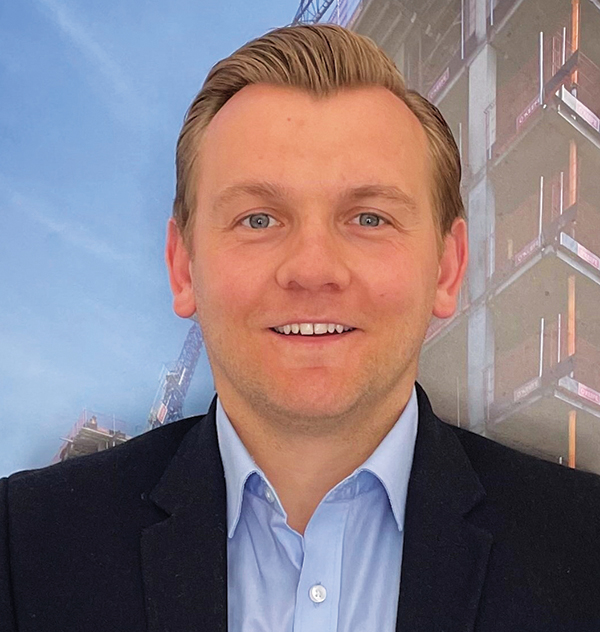
“Using BIM 360 and Navisworks we can produce images that the modular manufacturer can overlay on their drawings to ensure complete compatibility.”
But although this seemed a logical extension of the modular concept, it proved expensive and unwieldy in operation, and we are now preparing to demonstrate with a precast option. In truth, there will probably always be the need to have a variety of options for this foundation connection.
We have to date experimented with several options, comparing traditional brick and blockwork with alternatives such as reinforced concrete upstands. The latter was expected to deliver benefits from the use of reusable steel formwork.
But back to BIM. The use of the technology can help with sequencing as well as design compatibility. For example, it can help decide the extent of hard and soft landscaping to complete before modules are installed. In an ideal world, all landscaping, footpaths and flowerbeds would be finished in advance of the modules arriving on site. But careful consideration for the modular deployment and lifting logistics needs to be front and centre for any decision-making.
We started searching for solutions to this problem around 18 months ago. Since then we have started working as the civils contractor on numerous modular-led projects. On the latest one in south London, we are putting into practice what we have learned. Early collaboration with the offsite manufacturer and the project lead – whether developer or contractor – is a priority and point cloud surveys are being produced and supplied directly to all parties.
We are pleased to say that our recommendations and findings are now turning into actual savings both in time and money.
Ross Halliday is a regional director at O’Keefe.