Onsite studies of MMC housing construction show significant cost and time benefits. Let’s work together to make that the norm, argues L&Q CEO Fiona Fletcher-Smith.
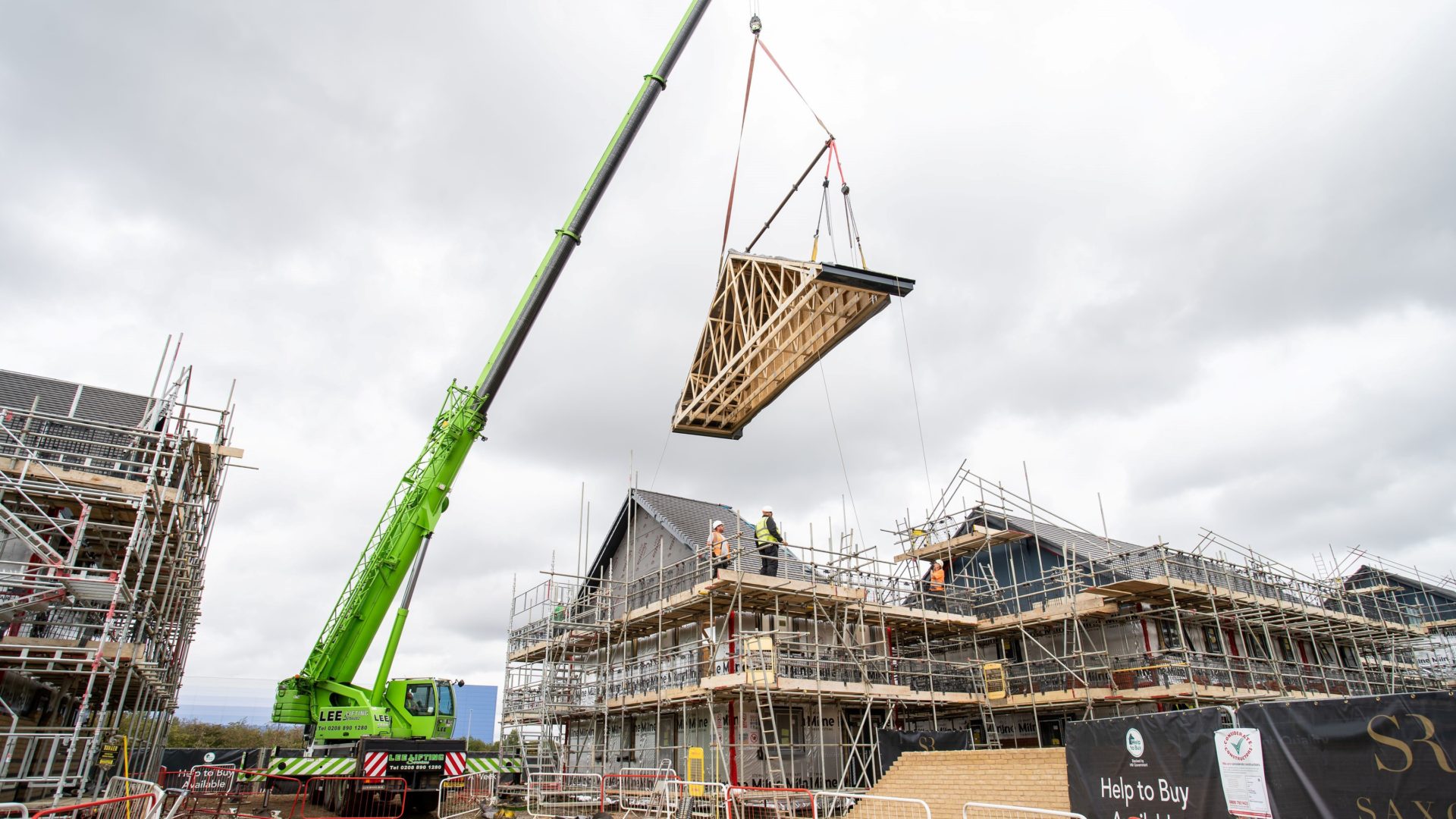
The triple impact of the net-zero agenda, skills shortages, and the rising costs of materials has led to growing calls for the housing industry to embrace modern methods of construction (MMC).
Moving to non-traditional methods, such as offsite and modular building techniques, offers a world of new possibilities – from faster build programmes and improved build quality to new jobs and zero-carbon technology – all whilst reducing costs. A study involving L&Q proves this.
At a time when the sector is under extreme resource strain, these are the things we need to tackle the chronic shortage of affordable housing.
“The MMC study showed homes can be built 20-40% faster, and labour and waste onsite reduced by 15-20%.”
Digital working and offsite construction are a catalyst for levelling up, improving neighbourhoods, and moving jobs away from the places where homes are built. MMC also presents a unique opportunity for the industry to diversify the workforce and attract new talent.
While the case for change has been gaining momentum, MMC is yet to break through, due to lack of cross-sector support, skills shortages, and regulatory barriers. How can the sector embrace change and transform the future of housebuilding?
MMC housing needs government support
First and foremost, government support will drive increased confidence and certainty in the approach: both financially through grants and subsidies for developers, and through planning policy incentives.
Setting regulatory standards around performance will motivate the industry to innovate, much like the car industry did when given emissions targets.
More strategic investment in training the workforce is required too. We need to upskill existing staff to cover site management, integration, and assembly, and hire new staff to lead on design and technology.
But with skills shortages prevalent across other sectors, the industry needs to collaborate end to end, from encouraging children to consider construction as a career, to ensuring the delivery of qualifications needed for MMC.
L&Q embraces MMC innovation
New pockets of cross-sector collaboration are paving the way for a sea change in how we construct homes. Working with other housebuilders we have pioneered MMC techniques, such as offsite timber frame construction through the Advanced Industrialised Methods for the Construction of Homes project (AIMCH). L&Q is progressively adopting these techniques, with 20% utilisation expected by 2026.
Funded by Innovate UK, AIMCH was a three-year research and development project that brought partners from the private rented and social housing sectors together with industry leading manufacturers and researchers. Participants came from different sectors and industries, including Barratt Developments, Construction Scotland Innovation Centre, Forster Group, L&Q, Manufacturing Technology Centre (MTC), and Stewart Milne Group.
Live housing developments successfully trialled advanced panelised systems. These can now be brought to the market in volume.
AIMCH has helped with the development of housing blueprints for L&Q which will further improve the efficiency in our delivery of homes.
MMC project data proves the benefits
Public uncertainty remains a hurdle to overcome. Brick and block methods are what people know and trust. Some house buyers are nervous when they hear part of their home is being built in a factory.
Yet MMC guarantees better environments for assembling and building than harsh outdoor climates. We now need comparative data to back this up.
The AIMCH project’s onsite monitoring of MMC systems identified quality improvements and set benchmarks for productivity and waste reduction. Across 42 plots, the project recorded more than 100,000 operative observations and collected 500,000 pieces of data, to evaluate masonry, timber frame and advanced closed panel methods.
The results showed homes can be built 20%-40% faster, and labour and waste on site reduced by 15%-20%.
As the dust settles on the appointment of the new cabinet, now is the time to get ahead of legislation and speed up the move towards new ways of building. With sector will and appetite in our favour, let’s work together to establish MMC as the new norm.
Fiona Fletcher-Smith is CEO of housing group L&Q.