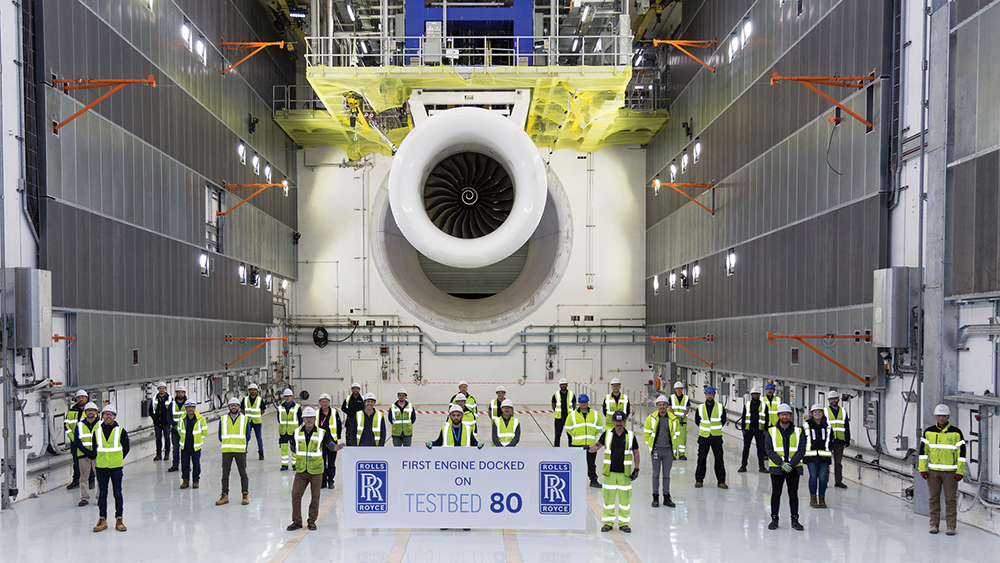
Matthew Stowe was project manager for the ground-breaking Rolls-Royce Testbed 80, which opened this year. He shares his experience of creating the world’s largest and smartest indoor aerospace testing facility.
Testbed 80 is an incredible project. What was the construction experience like?
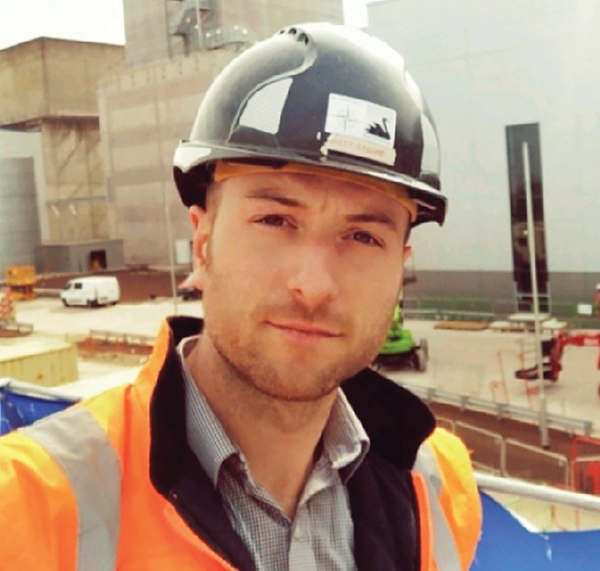
Projects like Testbed 80 for a client like Rolls-Royce don’t come around often. Although challenging along the way, it was incredible to be part of such a prestigious project and one that means so much to the people of Derby and for the future of Rolls-Royce Aerospace.
With it being the first of its kind around the world, it was a learning experience for everyone involved. As a construction team, we first had to learn and understand about the function of the facility and the importance of its design, before we could enter the construction phase.
It carried out new experimental developments – what challenges did that present? Any technical issues that had to be overcome? Any innovations to share?
The way the facility was going to be used certainly brought its challenges. One of the biggest elements to the facility was its capability to run the largest aero engine in the world and to use X-ray imagery to test it.
We had to secure an engine loading dock to the ceiling of the test room, which meant casting in around 40 holding-down bolts through a 1.1m ceiling slab, with less than 1mm of accuracy. This was to ensure no movement of the engine as it produced 155klbf thrust – enough power to launch a Boeing 747 with one (huge) engine.
The next challenge was to ensure Rolls-Royce could carry out X-ray testing without affecting the surrounding area of the test bed. Whereas previous test beds had to have a one-mile radius ‘no go’ zone during testing, Testbed 80 was designed with two thick concrete walls with Z- shape penetrations cast into the inner 1.2m thick wall, to ensure X-rays would not penetrate the facility. This was a new design concept to the industry.
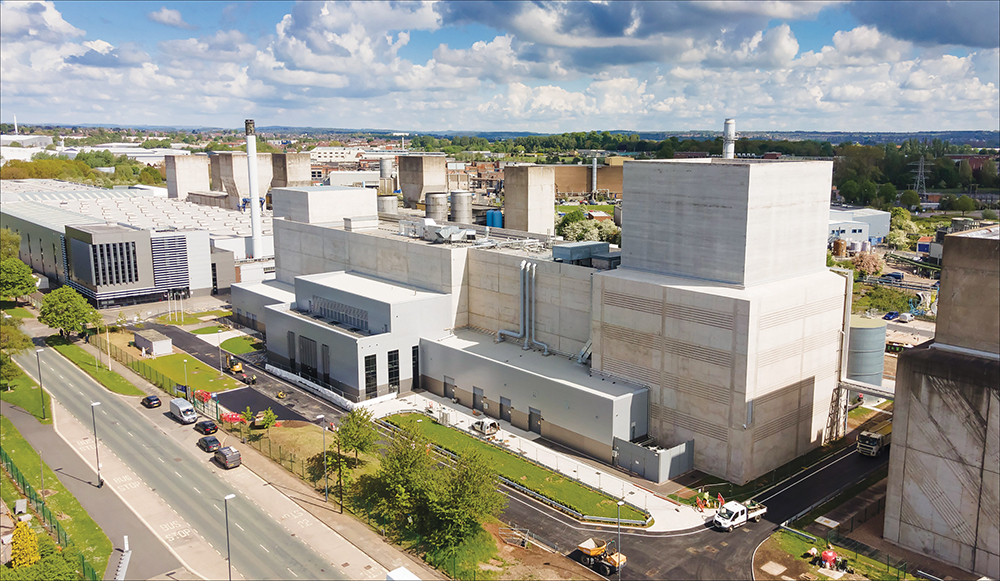
The sheer scale also brought challenges. The indoor area is bigger than a Premiership football pitch. The walls are made up of a 1.2m inner skin and a 0.9m outer skin using over 3,000 tonnes of steel and 17,000 cu m of concrete; enough to fill seven Olympic-sized swimming pools. Even the X-ray door to the testbed weighed 380 tonnes and had to be craned into position.
What did you learn from it?
Every project is different; personally, I have built prisons, schools, sports facilities, offices, distribution centres, and more, but never have I experienced building something like Testbed 80.
You always learn and never stop in construction. Testbed 80 taught me not only new methods of construction but what it means to deliver such an important project to the client. One of the biggest achievements was the construction of the exhaust tower, a 42m high concrete structure with 0.8m thick reinforced concrete walls, which were poured 24/7 over 11 days.
The engine was tested successfully earlier this year and, from talking to staff at Rolls-Royce, I understand all were extremely impressed and proud of the moment it fired up. A proud project for all to be involved with.
A time lapse of the construction can be viewed at www.youtube.com/watch?v=a8-xFwDdHZs.