
Mace’s steel-framed Edenica office project at 100 Fetter Lane in London features the first use of Waterman’s ‘materials passports’ system – which could transform the industry’s ability to reuse materials. Martin Cooper reports.
A steel-framed office development in the City of London is pioneering a new concept known as ‘materials passports’ – helping to address the challenges of the climate emergency and advance the construction sector towards its net zero targets.
Developed by BauMont Real Estate and YardNine, Edenica at 100 Fetter Lane is the first project in the City of London to use these digital data sets. They describe characteristics of materials and components in products and systems, giving them value for present use, recovery and future use. In this way, a project such as Edenica is designed as a storage bank where materials are held for future reuse.
Launched by Waterman Group, materials passports offer a standardised approach to documenting and managing materials throughout their life cycle. It is hoped they will become an industry standard, driving collaboration and sustainability.
Project overview
Client: BauMont Real Estate Capital, YardNine
Architect: Fletcher Priest Architects
Main contractor: Mace
Structural engineer: Waterman Group
Steelwork contractor: Bourne Steel
Steel tonnage: 1,100 tonnes
“The Waterman team has been integral in helping us create and bring to life this truly exceptional scheme that pushes the boundaries of sustainable design,” says Maxwell Shand, co-founder of YardNine.
The Edenica scheme has embraced the pioneering concept of materials passports to enable the circular reuse of materials and a design that minimises the environmental impact during the building’s construction and its operation.
“It’s setting a new precedent for London,” explains Mace senior project manager Romain Dennison. “This digital asset stores each and every one of the project module’s weight, dimension and component characteristics in a BIM database, which creates a robust platform for material circularity, so they can be reused if and when the structure is refurbished or demolished.”
Adding to this project’s sustainability credentials, it is also targeting the highest environmental standards of BREEAM Outstanding, as well as WiredScore, SmartScore and WELL certifications.
Mace started on site in December 2022, inheriting a cleared plot where the previous six-storey concrete-framed office building had already been demolished. Preliminary works included deepening the existing basement and installing piled foundations to support the new steel-framed structure.
Steelwork was the preferred framing solution for the Edenica project as the material provided the necessary speed of construction. Another important consideration was the need for a lightweight design, as the project’s footprint sits directly above a live and operational Thames Water sewer. A similar-sized concrete-framed structure might well have proved too heavy for the site.
Starting in the basement
The steel frame starts in the basement, with a series of columns founded on the subterranean level’s slab. The columns, delivered to site as single-storey-high members, were installed early in the programme.
“They form part of the basement structure, and we installed them during an early visit to site,” says Bourne Steel project manager Theodoros Pitrakkos.
“Once in place, they were encased in concrete and the ground floor slab was cast around the top of them, leaving a small section protruding above the floor, in readiness for the main steel erection to begin.”
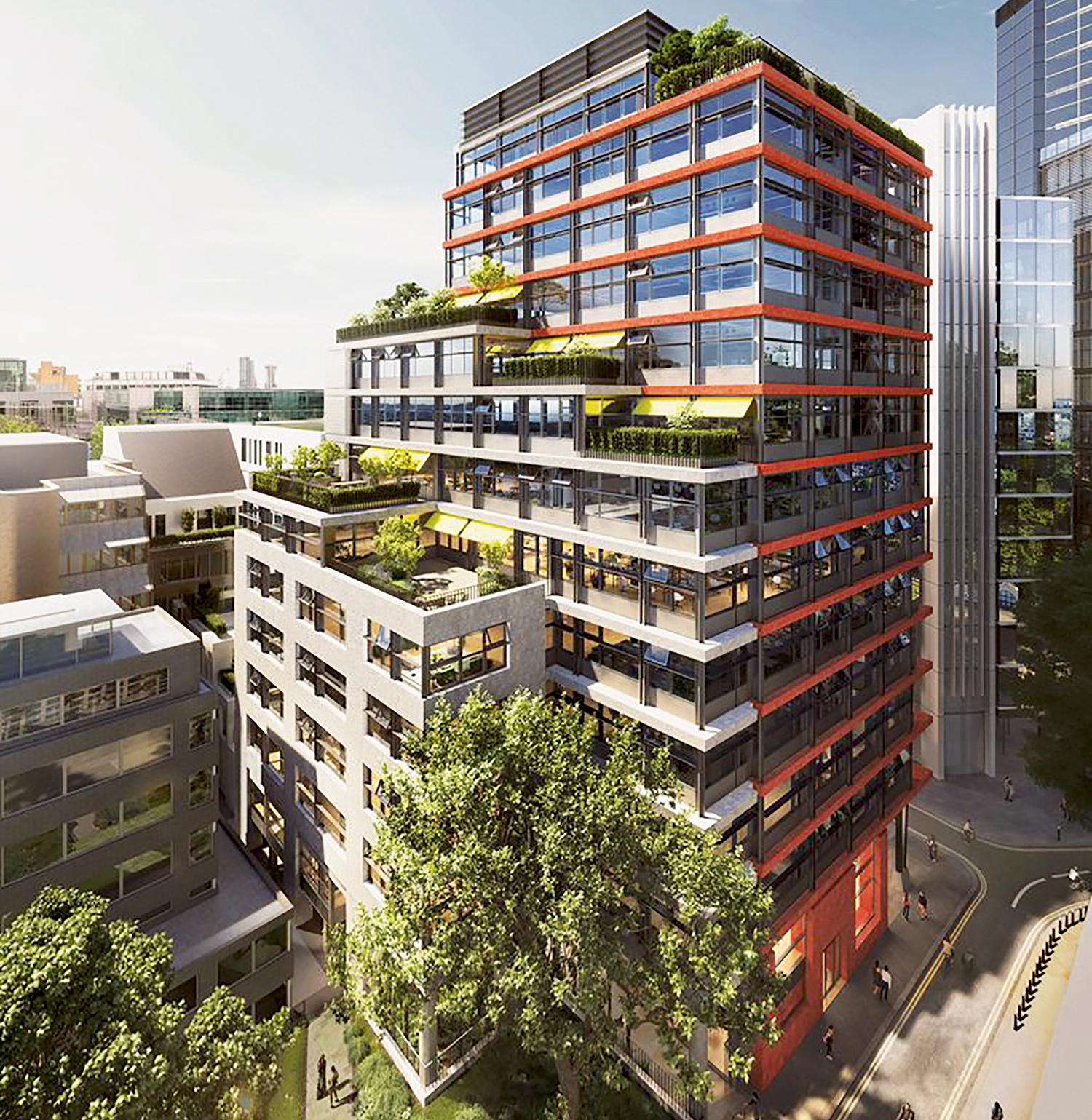
Prior to the remainder of steelwork erection programme getting underway, the main stability-giving jump-formed concrete core was also begun. The core is offset, positioned on the eastern Fetter Lane elevation, which allows the internal floorplates to be opened up and maximised.
Above ground floor, the structure consists of steel beams and columns supporting a series of 4.5m x 1.8m precast floor planks. This solution was chosen as the design incorporates an exposed soffit and the planks have the desired smooth high-quality architectural finish to their undersides.
The exposed nature of the project extends to the majority of the internal steelwork as well as the building’s services and the core, which will also be left exposed within the main reception area. Complementing the exposed aesthetically pleasing look to the building’s interior, the column’s steel-to-steel connections are made with countersunk bolts, which provides a flush finish. Most of the steel frame has a decorative paint finish, which was applied on site.
The steel columns are predominantly based around a regular grid pattern, one that is dictated by the terrace setbacks at the upper levels. Internally, there are clear spans of up to 11m in some areas, providing the building with the desired open-plan floorplates.
Column-free space
Creating the main entrance, which is on the corner of Fetter Lane and Bream’s Buildings, a clear column-free space has been formed by doing away with the corner column line below level five.
At the underside of this level, the corner member is replaced by two raking sections that splay inwards towards the adjacent bays, framing the entrance to the building and leaving a clear space for the entrance.
Aiding the project’s wellbeing strategy, from level five upwards, Edenica features a number of setbacks, mostly on the southern and eastern elevations that accommodate outdoor terraces. With an abundance of plants and greenery, they will offer tenants plenty of welcoming breakout space.
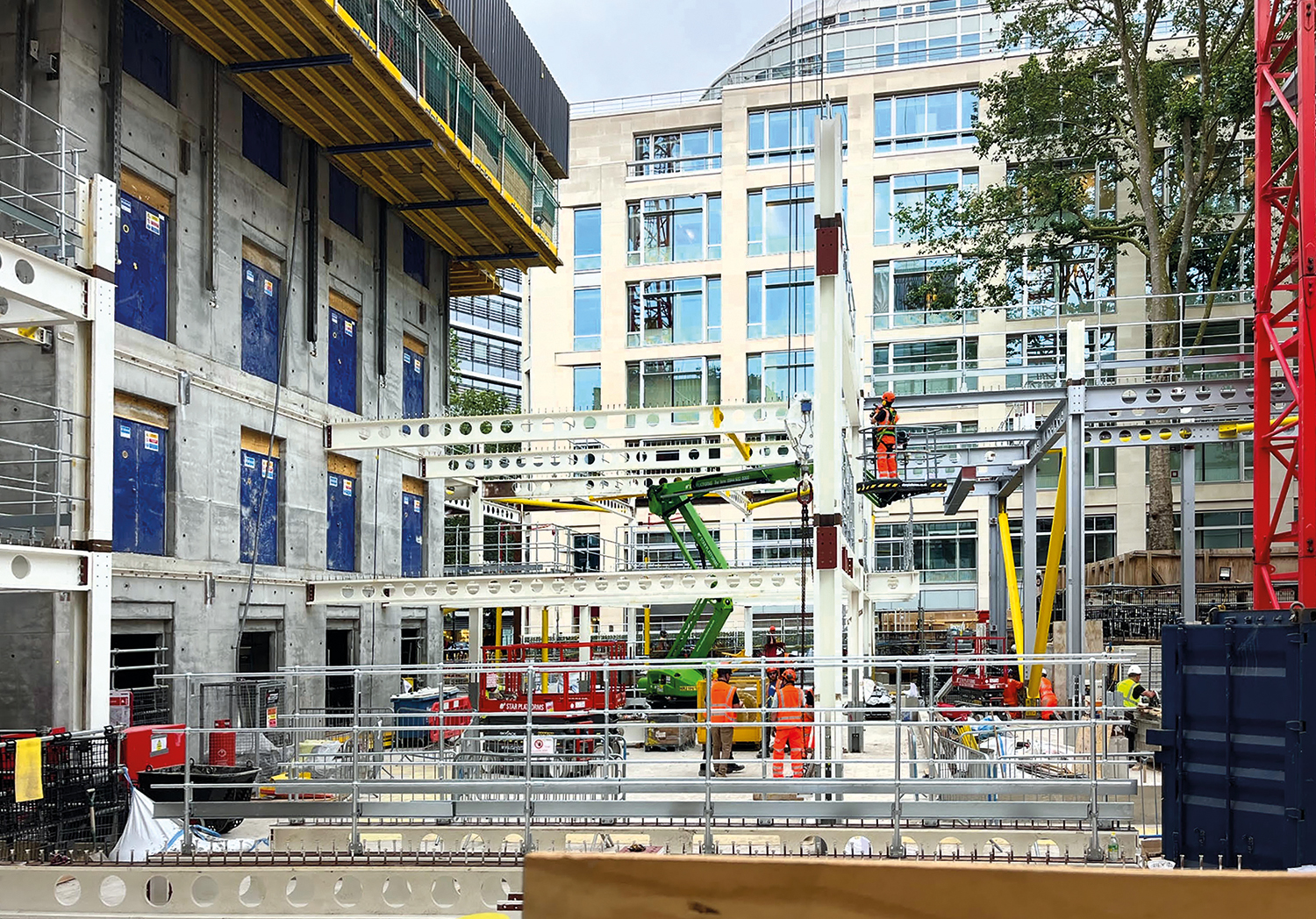
Having terrace setbacks means the structure reduces in size towards the upper levels. This presents a less formidable block in an area of the City that, in contrast to the well-known eastern cluster, does not have many buildings above 15 storeys high.
“To maximise the number of floors within the structure, the transfer beams that support the terraces needed to be as slim as possible,” explains Waterman Structures director Julian Traxler.
“Consequently, the slim transfer beams need to be supported by internal columns, which has been another factor in determining the project’s steel grid pattern.”
According to Bourne Steel, the transfer beams represented the heaviest individual members in the steel frame erection programme, with the uppermost section, supporting a terrace at level 12, weighing 10.9 tonnes.
Jump-forming process
Using the site’s two tower cranes, the steel erection was coordinated around other onsite trades, which earlier in the programme included the installation of the core. During the jump-forming process, Bourne Steel, the supplier of the embedment plates, progressively welded stubs to the plates to accept the frame’s beams.
As well as erecting the steelwork, Bourne Steel also installed the precast planks. To coordinate both installation processes, the steel frame was erected two floors at a time. With five separate zones, two fed by one crane and three supplied by the other tower, the erection proceeded in a sequential manner, working around the site in a clockwise direction.
A temporary propping system was employed to support each phase of the precast plank installation. The props ensured the flooring units were aligned, which is vital for the exposed and aesthetic finish. They remained in place during the pouring of the concrete topping that completed the 150mm-thick flooring solution.
“The completed scheme will have 100% electric building services, ensuring Edenica achieves carbon neutrality in use,” says Dennison.
“Alongside our sustainability credentials, coordination between the project’s different trades has also been key on this project. It’s a very tight and confined site, bounded on two sides by busy streets, on which we have been able to accommodate our pit lanes, that feed our cranes with materials, keeping the job on schedule.”
Edenica is due to complete by the end of 2024.
What are materials passports?
Materials passports are structured as a pyramid, with various levels of passports aggregating and refining data, from capturing manufacturer-provided product details to presenting data for specific building element categories.
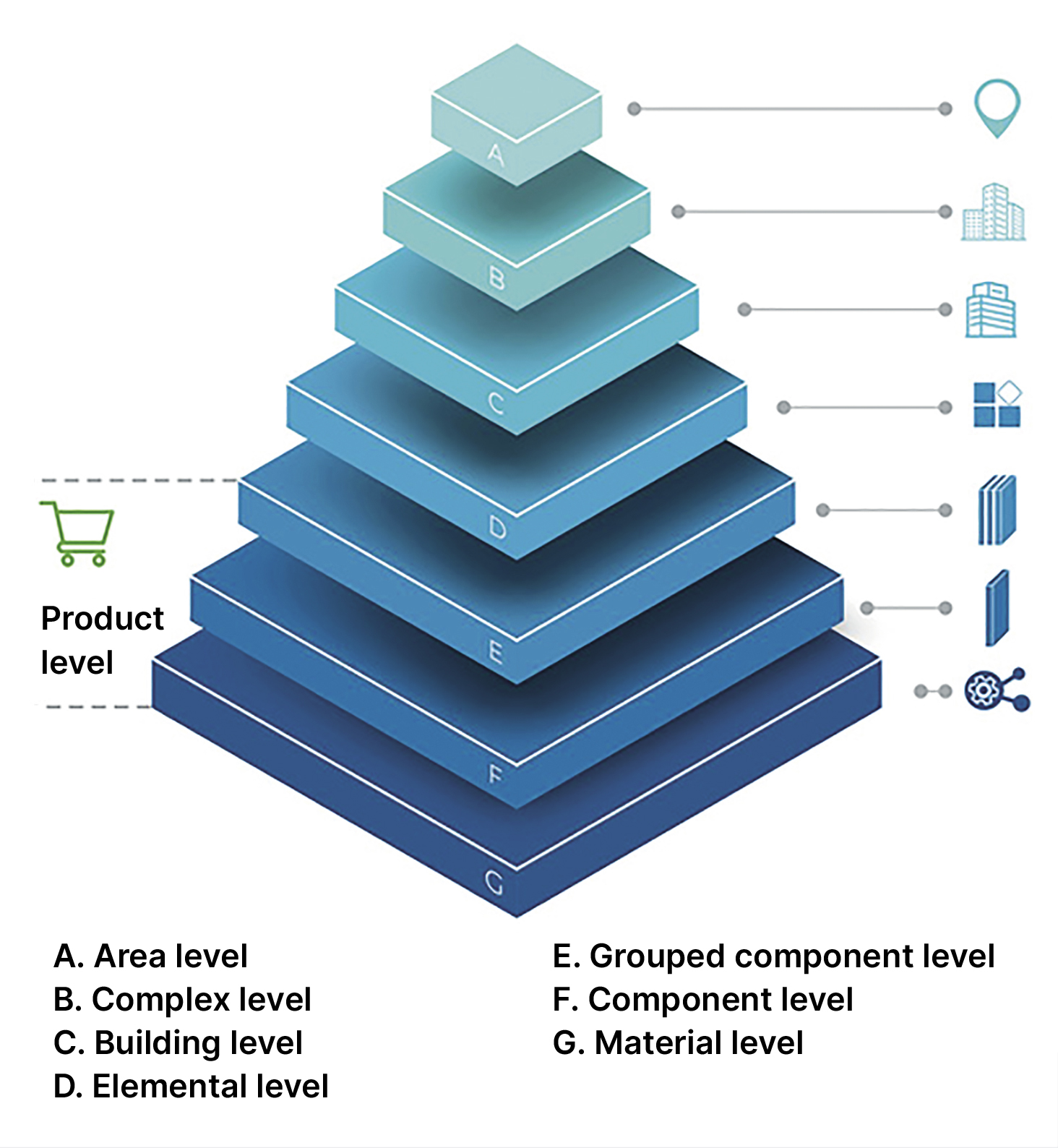
The pyramid approach is said to offer holistic overviews of building performance against sustainability metrics.
To add to their usefulness, Waterman Group is working with software developer Circuland to deliver a digital platform designed to host materials passports data and linked directly with BIM models.
The platform’s transparency in material types, recycled content, disassembled materials for reuse and an online marketplace for selling materials are all expected to enhance the resource-efficient use of materials and lead to a more sustainable future.
Mark Terndrup, Waterman’s managing director for building services – south, says: “With the launch of our Materials Passports Framework, we aim to drive material circularity and kickstart the circular economy throughout the construction industry with a robust process any scheme can follow.
“The impacts of the climate emergency are more prevalent than ever, and extending material lifespans is fundamental to minimising the embodied and whole-life carbon impact of development schemes across every sector.”