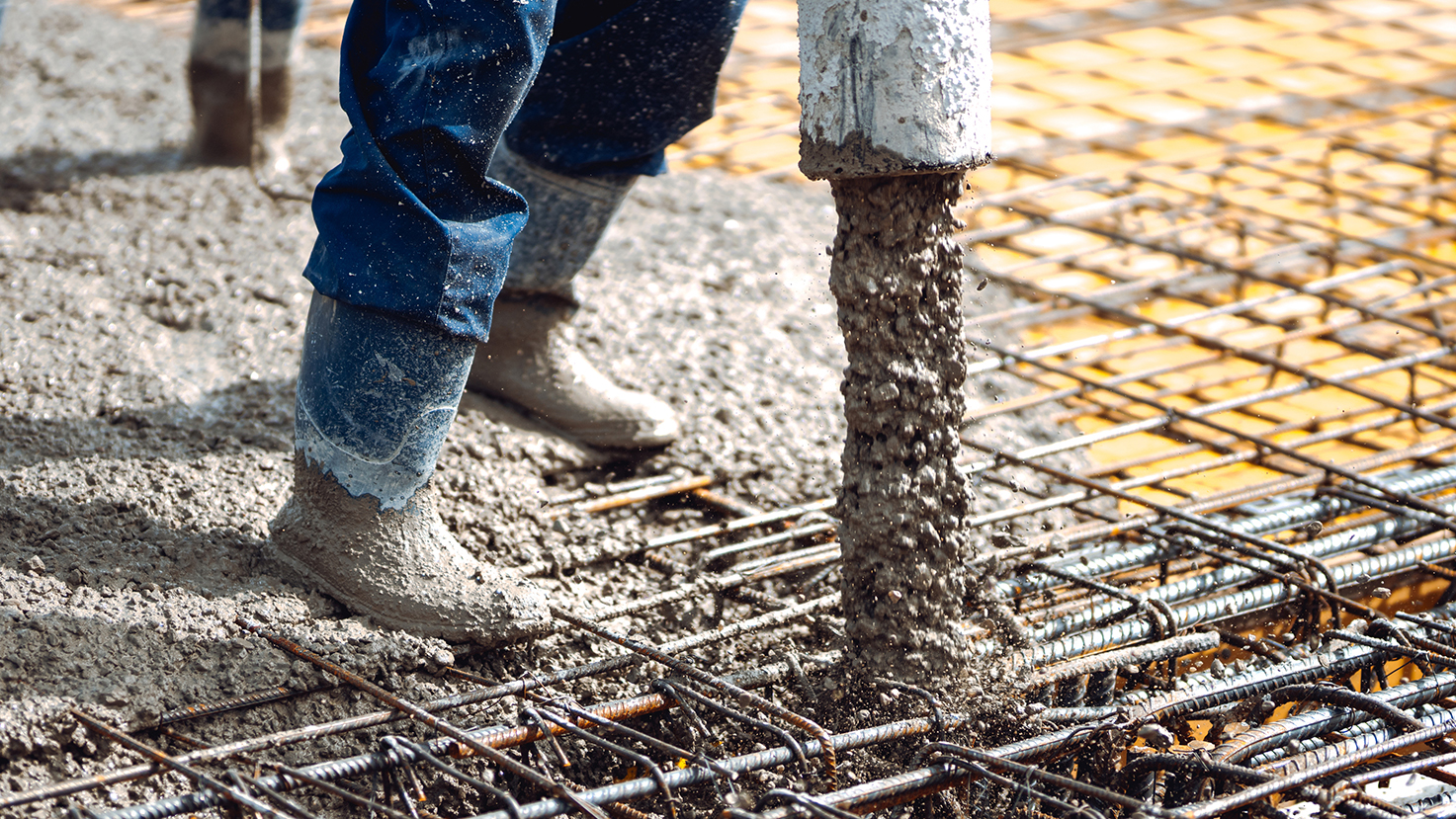
Tales of low-carbon concrete abound, but what exactly does that mean? Kristina Smith looks at what’s in the mix.
In September 2022, HS2’s Euston station site saw the UK’s largest ever low-carbon concrete pour: a 232 cu m temporary slab that will support polymer silos for piling works.
Depending on how you look at it, the mix used – Earth Friendly Concrete (EFC) from Capital Concrete – has saved either 75% or 50% of embodied carbon, compared to a ‘standard’ mix. The press releases have, of course, gone for the former, but the question is whether a standard mix is one that contains 100% Ordinary Portland Cement (OPC) or one that contains a mix of half OPC and half ground granulated blast furnace slag (GGBS).
“Some of the big concrete suppliers are referring to concrete with 50% slag as ‘lower-carbon concrete’, but that’s an everyday concrete in London,” says specialist concrete consultant Charles Allen, director of OTB Concrete, who is an advisor to Capital Concrete. “I have been using 70% slag in foundations for 30 years.”
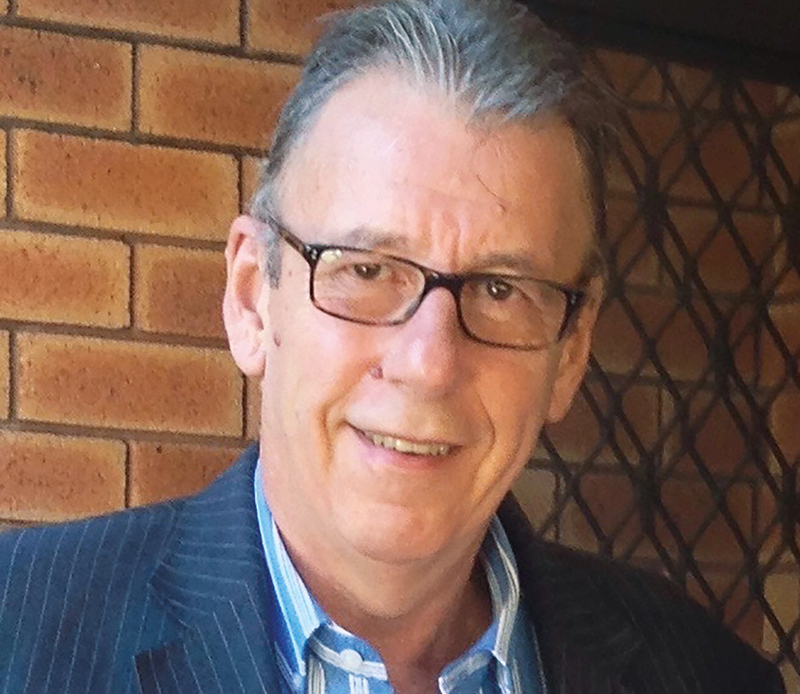
“Some suppliers refer to concrete with 50% slag as ‘lower carbon’, but that’s an everyday concrete in London.”
Materials such as GGBS and pulverised fuel ash (PFA) are often used to replace some of the OPC in large-volume concrete pours to reduce the heat of hydration. This in turn reduces the chance of cracking and can allow the amount of reinforcement to be reduced.
We need to get far more specific in our definition of low-carbon concrete, says the Low Carbon Concrete Group. In its Low Carbon Concrete Routemap, the group says that different strengths of concrete should be given an embodied carbon rating graded from A++ to G, similar to energy efficiency ratings for appliances. And the baseline should be calculated from contemporary industry values.
The other challenge is that concretes that use GGBS and PFA are not a long-term fix. There are already limited supplies – which will diminish as steel-making processes change and coal-fired power stations become fewer.
“Slag and GGBS are transition technologies,” says Noushin Khosravi, sustainable construction manager at the Concrete Centre, which is part of Mineral Products Association (MPA). “We need to invest in longer-term solutions at the same time.”
One of MPA’s current projects is to look at what type of UK clay would produce the best calcined clay – another alternative cementitious material which could be in greater supply than PFA and slag.
How low can we go?
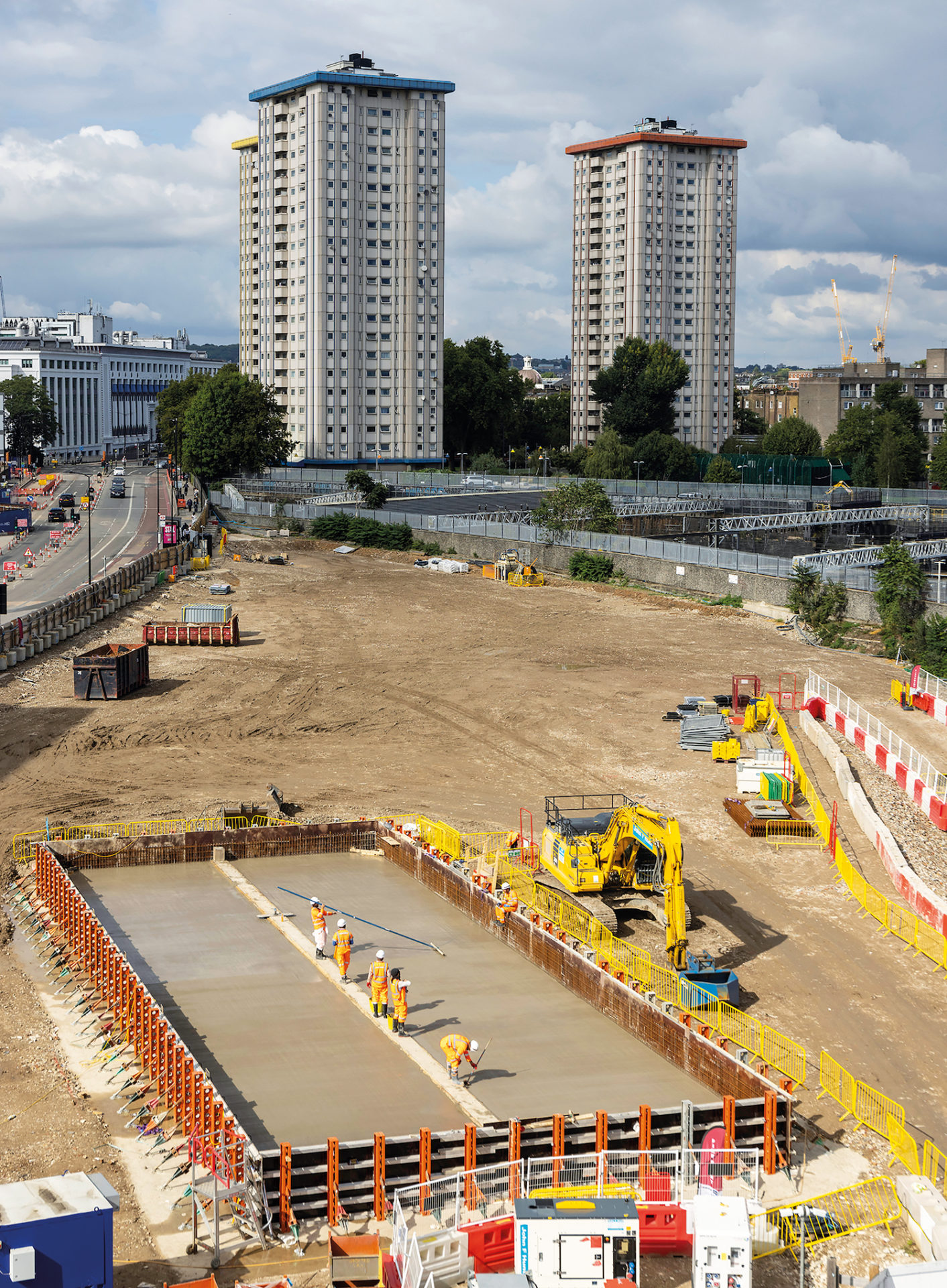
Producing cement, or rather clinker which is the main constituent of cement, delivers a double whammy of carbon emissions. First burning fuel to heat up the limestone releases carbon dioxide, and then the chemical reaction itself releases it too.
The oft-quoted statistic is that cement contributes to 7% of the world’s carbon emissions. However, MPA says that in the UK concrete and cement account for just 1.5% of emissions. “From 1990 we have reduced our absolute emissions by 53%, which is faster than the overall economy, mainly by improving energy efficiency at the plants,” says Khosravi.
Using low-carbon cements and concretes can only drive down emissions by 12%, says MPA, due to its limited and reducing supply. Other factors that will reduce emissions are decarbonising electricity, transport, fuel switching and carbon capture, usage and storage (CCUS) which MPA says will have to contribute over 60% of the reduction needed to reach net zero.
There are some clever ideas out there for using concrete itself to capture and store carbon. Companies such as Nova Scotia, Canada-based CarbonCure Technologies are injecting carbon dioxide into concrete where it undergoes a mineralisation process to become embedded in the concrete. Closer to home, startup company Seratech is developing a technology to sequester carbon which – in the lab at least – can already produce zero carbon concrete (see box).
One difficult issue for the UK cement and concrete industry is that, if other countries are less stringent with their carbon-reducing regulations, we may end up increasing our imports of cement from overseas because it is less expensive to produce. Currently imports account for around 20%.
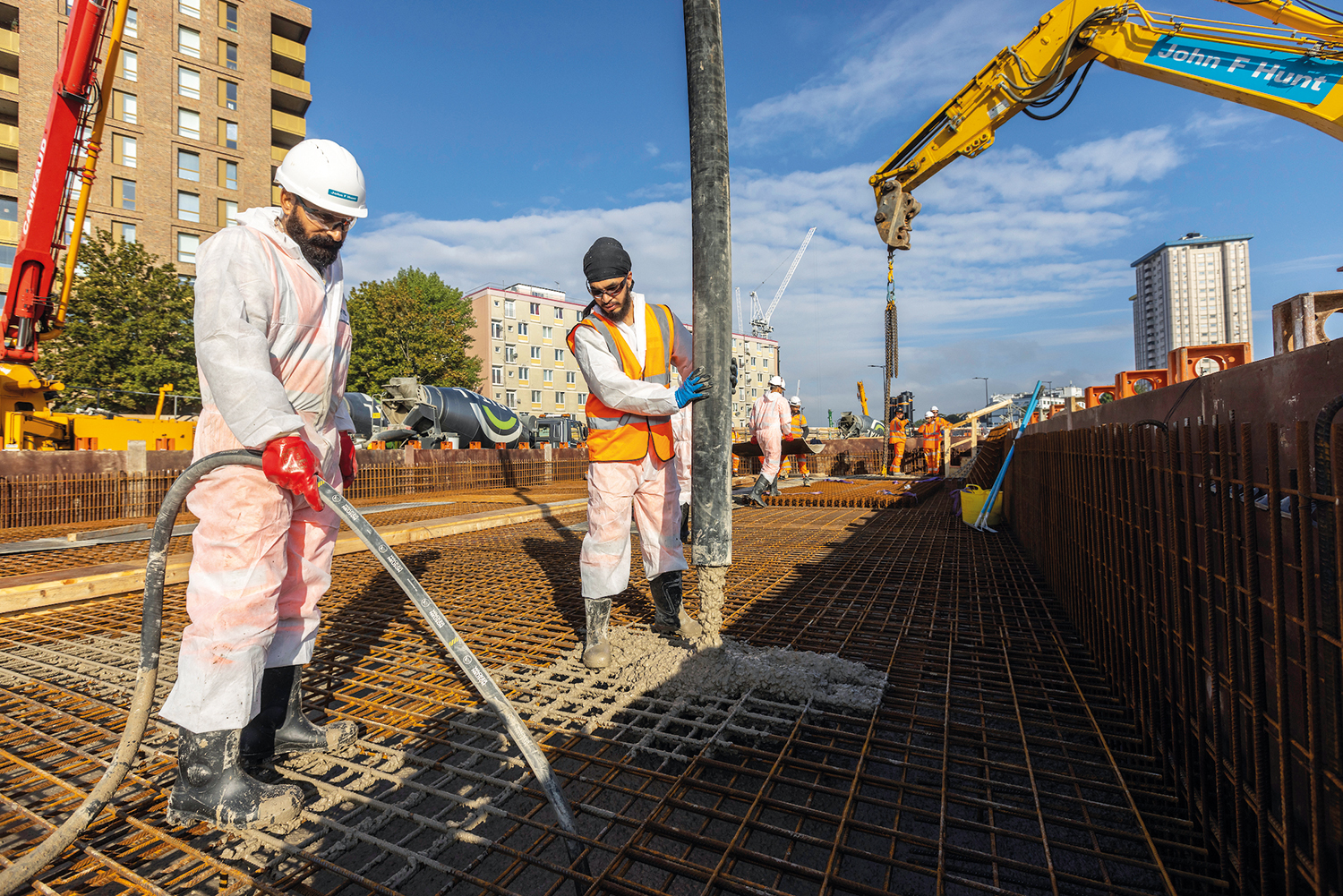
Alkali-activated concretes
While we wait for the grid to decarbonise and CCUS technologies to develop, concretes such as EFC are at least available today. Other similar concretes currently on trial in the UK include Cemfree from the DB Group and Exegy from Vinci. All contain some combination of slag, possibly PFA and an alkali activator.
Collectively, concretes which use slag, PFA, calcined clay or other waste materials which are high in aluminosilicates are called alkali activated cementitious material (AACM) concretes. Geopolymer concretes are a sub-group of AACMs, containing PFA and slag.
The secret to the performance of such concretes is the alkali activator used. This important ingredient impacts on early-age and long-term strengths and the rate of strength gain; these differ considerably between brands.
AACM concretes perform differently to OPC ones, which should be considered in both the design and installation phases. For instance, Allen says that EFC has a higher flexural strength, which means that it may be possible to reduce both the depth of a slab and the amount of reinforcement.
From a workability perspective, there should not be an issue. “It is thixotropic, so it looks different, but it flows. It is not difficult to work with,” says Allen of EFC.
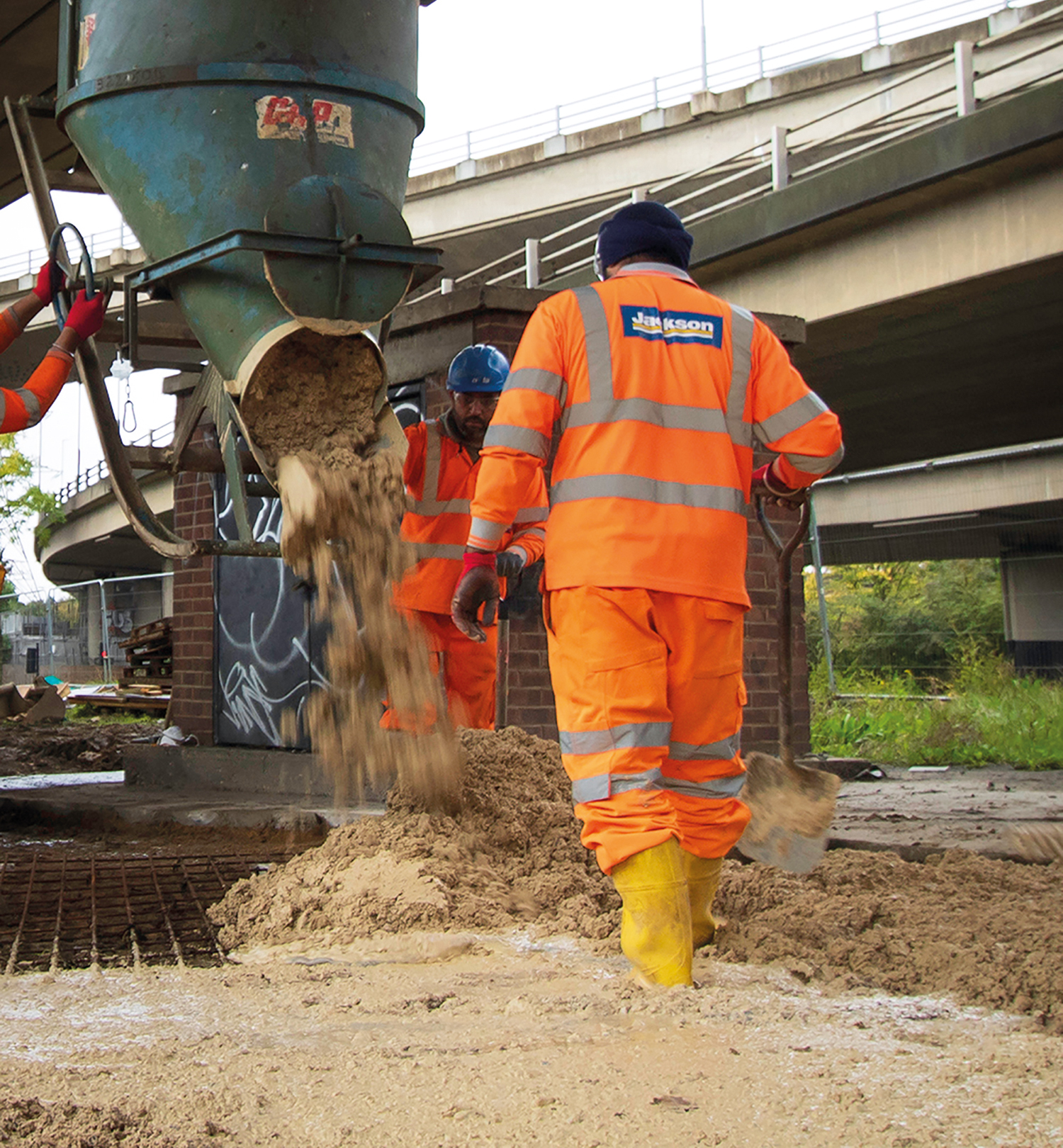
However, temperature at the time of the pour can be a consideration. “AACM concretes can be difficult in cold weather,” says Allen. “You might have to use hot water to help it react because it does not generate much heat at all.”
There are barriers to the wider use of AACMs: the limited supply of materials, as already explained, a lack of standards and the cost of the alkali activator which could make the price of an AACM concrete between 30% and 40% higher.
The issue of standards is already in hand, says Khosravi. MPA, with the government, has invested in research on multi-component cements so that they can be incorporated into a new version of BS 8500 Concrete which will be out this year, according to Khosravi.
Definitions of low carbon concrete
There is a long way to go in terms of defining what low-carbon concrete is, and in carbon accounting and reporting generally. However, the drive to reduce carbon is shining a light on construction materials and their complexity. Construction professionals will need to engage with materials technology on a deeper level.
“With more different types of mixes coming through, and modern technologies we need to be careful that we are using the right technology,” cautions Khosravi. “The key is early engagement and collaborating to find out what the best approach is.”
Seratech – a new concrete frontier?
Two researchers at Imperial College London have joined forces to produce zero-carbon concrete.
It took the Covid lockdown for Imperial College London researchers Sam Draper and Barney Shanks to find time to talk to each other about their research projects. When they did, an amazing opportunity emerged.
“Sam spotted this silica material I am working on and asked whether it worked in normal cement,” recalls Shanks. That was back in November 2020. Today the pair, working in their company Seratech, which they founded in 2021, have found a way to produce zero-carbon concrete.
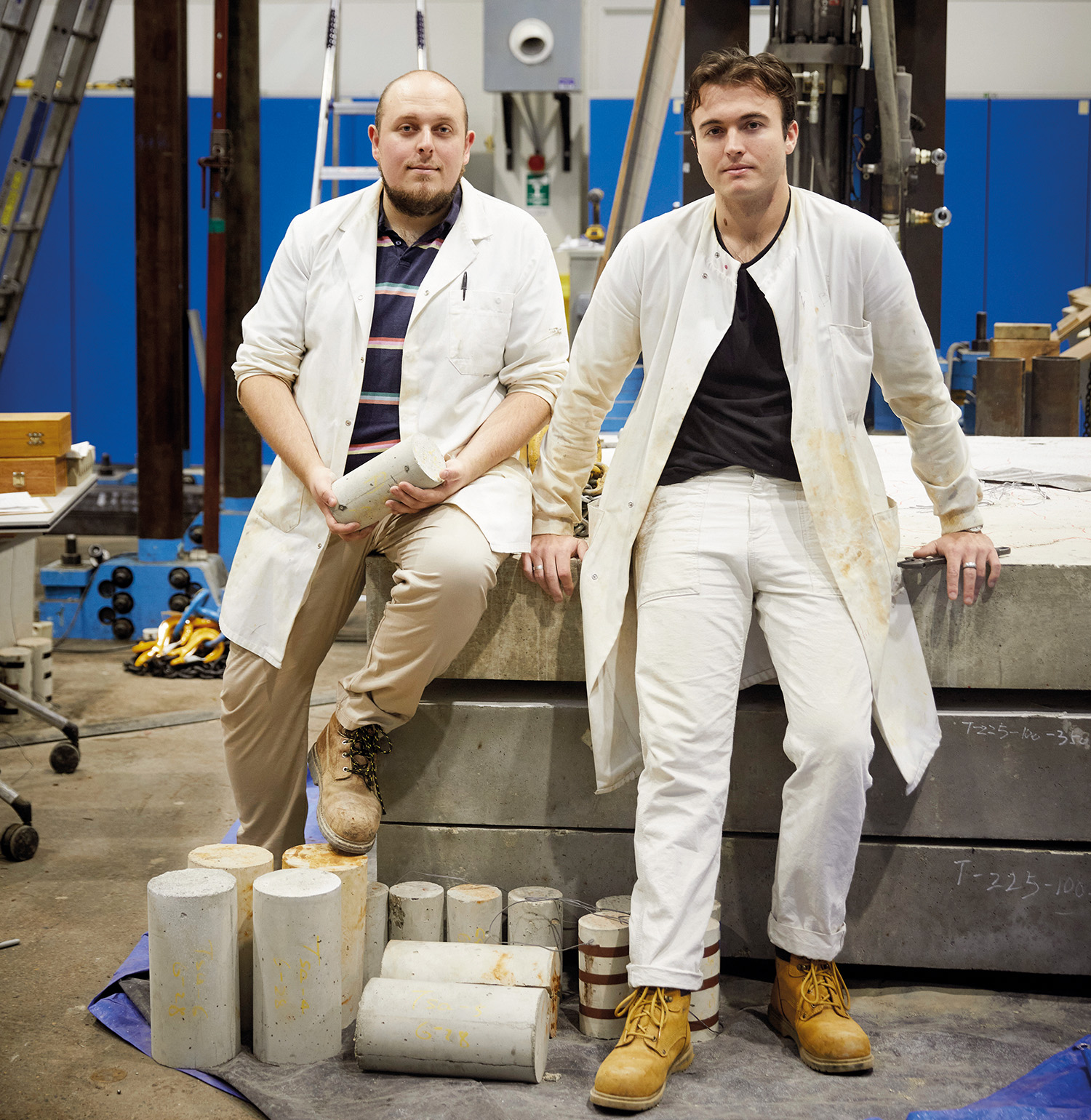
At the time of the initial conversation, Shanks was working on a magnesium-based cement derived from olivine, a magnesium silicate mineral. His PhD was investigating how the commonly occurring material could be used for concrete, splitting it into magnesium and silica and then recombining them with water to form a new bonding phase similar to cement, but without carbon dioxide being created.
Magnesium-based cements are in their infancy and don’t work well enough yet to be interesting to industry, says Shanks. However, they found a way of combining the two separated elements Shanks was producing with carbon dioxide to create a cement replacement material similar to fly ash.
“Because the magnesium component is very reactive, we don’t have to purify or liquify the carbon dioxide, we just take it directly from flues and pass it over the magnesium to form magnesium carbonate.”
Replacement mixes
Shanks and Draper then experimented with a couple of mixes, replacing 20% and 35% of the cement with the new material, to correspond to CEM IIA and CEM IIB cements. Due to the carbon sequestered, the 35% replacement mix leads to zero-carbon concrete.
And it performs well too, says Draper: “It has good compressive strength performance, 40MPa-plus,” he says. “It’s stronger than the fly ash mix and getting close to CEM I in strength. Its early-age strength is good too because the silica is very reactive.”
The potential of the Seratech process, which is currently progressing through the patenting process, has already been recognised. It has won awards and attracted grant funding.
The next step is to transform the laboratory process into something that can be applied to cement plants.
The goal is to create a system that can be easily retrofitted to any cement plant, or to another process that produced carbon dioxide, such as steel manufacture or energy production. If all goes to plan, they could have a pilot facility in operation in late 2023 or early 2024.
Early this year, the company plans to scale up production to allow more comprehensive testing. “After that we would look to do a couple of carefully selected pilot projects,” says Draper.
Comments
Comments are closed.
This again raises the issue that there are many uses of OPC that do not require a cement of that quality. OPC is manufactured using high temperatures, and produces a structural material. Other cementitious products have been used as alternative technologies, such as rice hull ash, and there are more. There is scope here for lower carbon developments.
Have a look at what Versarien PLC are working on with their Cementene their graphene enhanced cement. A white paper is available from their website.