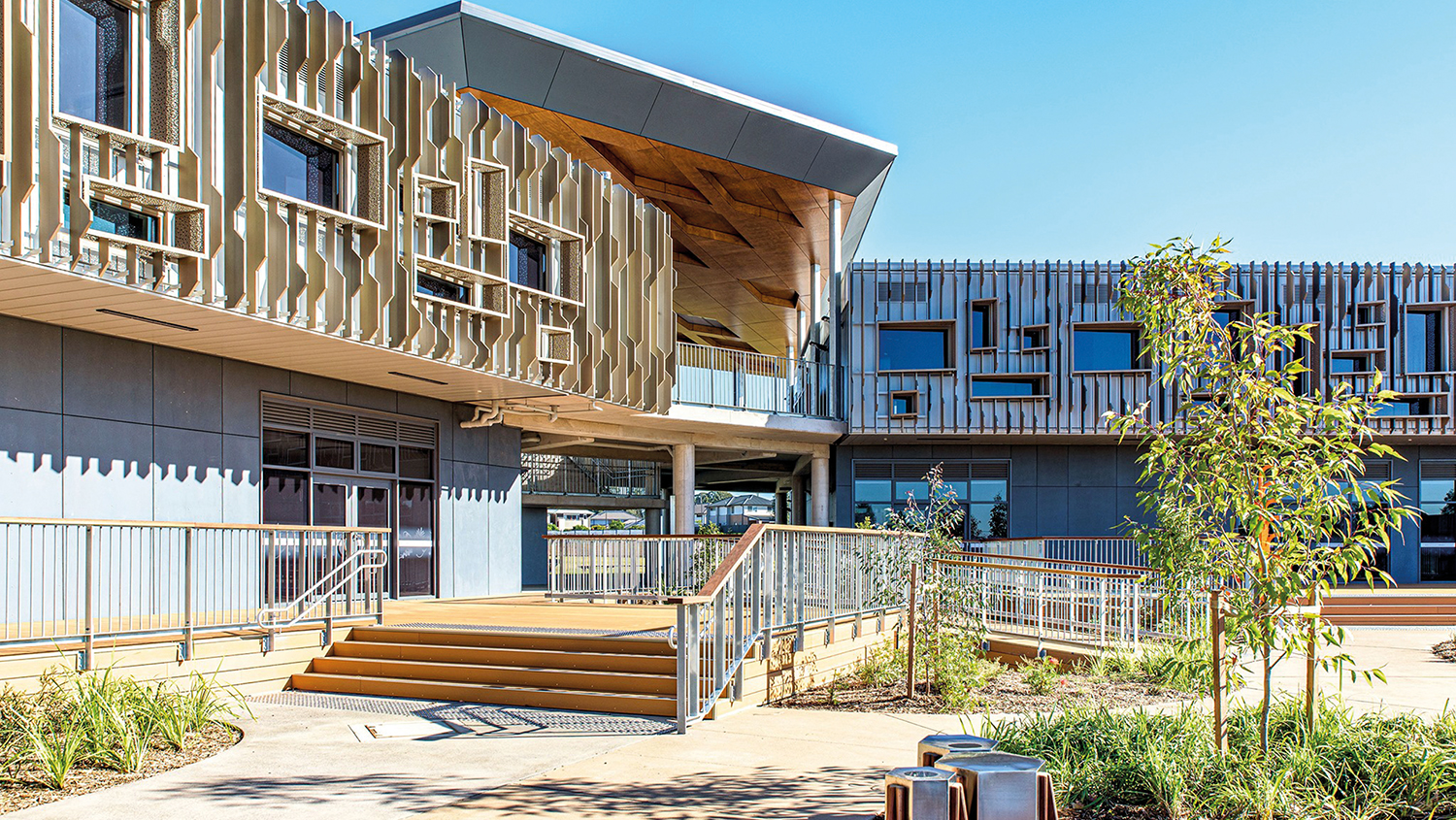
Sydney-based CIOB member Martin Fenn examines Australia’s recent forays into offsite construction – and what it could learn from the UK.
There’s a conundrum at the heart of Australian construction. The sector is booming, with huge transport and energy infrastructure schemes underway across the board. The value of work done rose 8.5% in the year to September 2023, led by engineering (up 14.9%) and residential (up 4.4%), the Australian Bureau of Statistics reported at the end of November.
But it has been called a “profitless boom”, marked by the lowest productivity growth in over three decades and more than two-thirds of builders reporting decreasing profit margins in 2023, according to a survey by financial advisory firm BDO Australia.
The causes are familiar: severe labour shortages, escalating material costs and a fraying global supply chain. Coupled with the urgency to accommodate a growing population, these predicaments compel industry to seek alternative solutions. No wonder, then, that attention is turning towards modern methods of construction (MMC), an approach that holds immense promise.
MMC prioritises offsite manufacturing techniques, cutting-edge digital technologies and standardised processes. It strives to boost productivity, enhance quality and reduce risk – achieving faster construction with fewer resources.
Comparing two countries
Despite a spate of recent modular builder failures, the UK stands out as a global leader in MMC, with an estimated 7% of construction projects delivered through it.
It has both a higher adoption rate and more structured approach, with MMC classified into seven categories including volumetric, panellised, 3D printing and onsite optimisation techniques such as pre-assembly and technology like drones.
There is also a more resolute government commitment, exemplified by Homes England’s pledge to employ MMC for a minimum of 25% of its project pipeline. But Australia does not enjoy this backing.
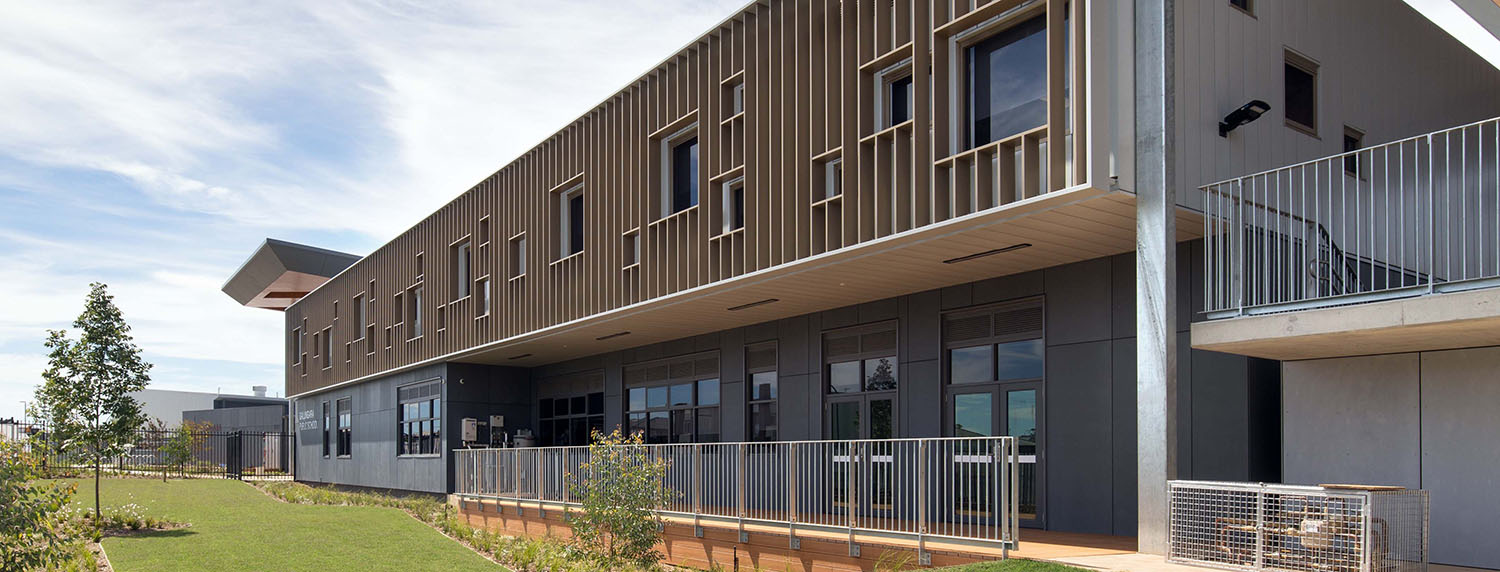
So, what’s behind the disparity? First, Australia’s vast and diverse geography and climate pose unique challenges and opportunities. Approximately 32 times larger than that of the UK, it has eight different climate zones, from hot desert and equatorial to alpine. This stands in sharp contrast to the UK’s single, more uniform climate.
Moreover, the UK’s population is more than 2.5 times larger than Australia’s, and Australia’s population density is primarily concentrated in its major coastal cities.
It is worth noting that, although the UK comprises four nations, central government remains powerful. In contrast, Australia operates as a federation, comprising a federal government and multiple states and territories, with a three-tiered system of governance: federal, state and local. This adds layers of complexity to fragmented decision-making.
Unions, risk and business as usual
Australia’s construction industry is heavily unionised compared to the UK. While unions prioritise fair labour practices, the associated regulations and negotiation processes can hinder the ability to change quickly. Change means risk and, with profit margins under strain, companies understandably ask why they should transition to new practices when there’s no margin to absorb the pitfalls.
Australian tradespeople often earn significantly more than their UK counterparts, largely owing to Australia’s higher minimum wage. It is not uncommon in cities like Sydney to see the driver of a convertible Maserati don a hi-vis vest. When people are earning well with business as usual, the impetus for change will necessarily be weaker.
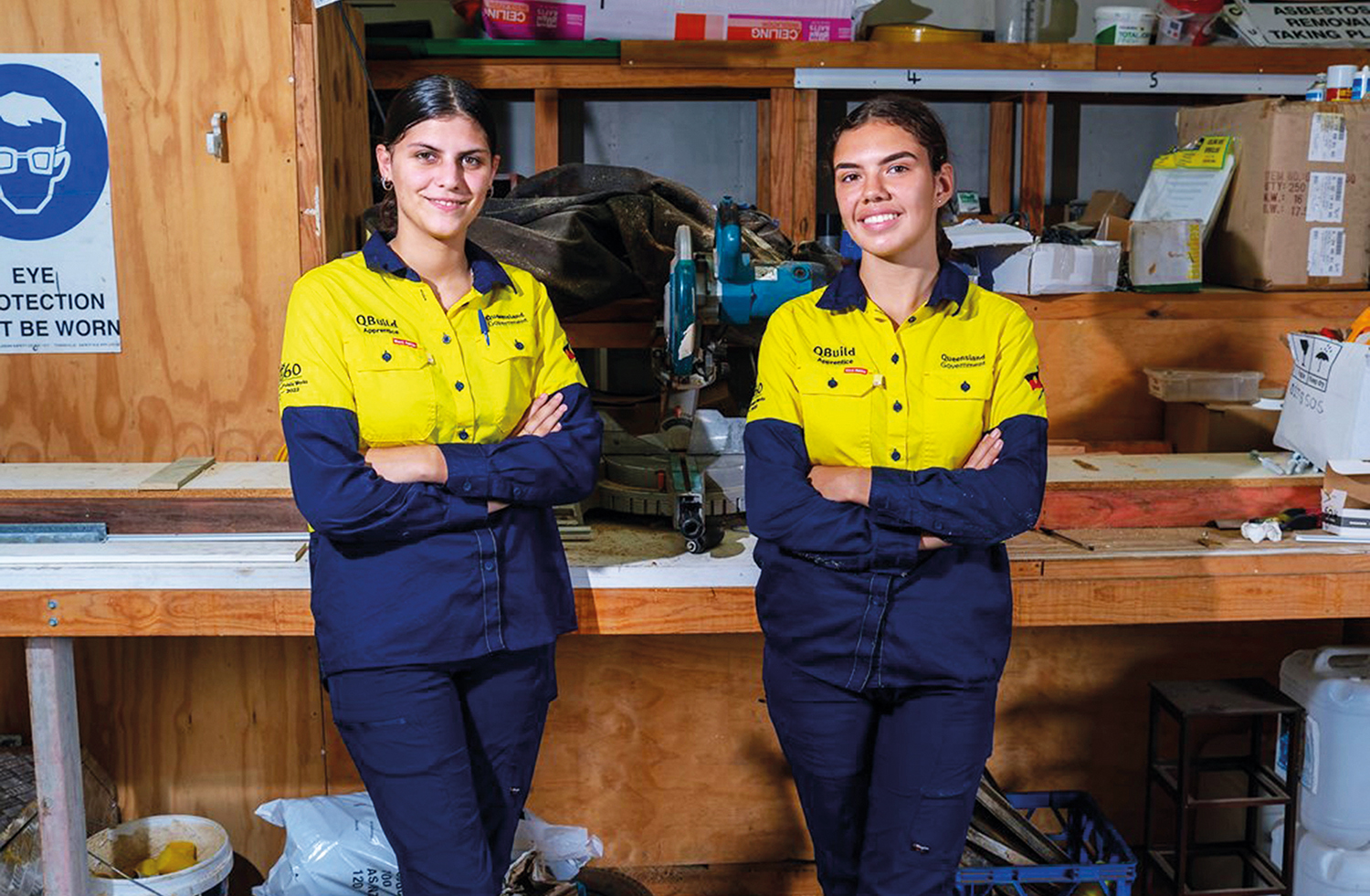
Despite all this, there are notable instances of MMC’s successful implementation across Australia. In the state of Victoria, the Victorian Permanent Modular Schools Program (VPMS) has achieved an impressive track record with the delivery of more than 100 modular school buildings.
They say necessity is the mother of invention, and here the state faced an urgent need for more classrooms while addressing asbestos removal in schools. The offsite, modular approach effectively halved construction timelines.
Signs of change
In New South Wales, state agency School Infrastructure New South Wales carried out a successful volumetric modular school pilot programme, resulting in a standardised kit of offsite-manufactured building components.
This was to prepare for a programme covering hundreds of schools. It will be rolled out under a common digital platform with a goal of promoting advanced manufacturing, allocating risk fairly and achieving high quality and safety standards.
In Queensland, a severe housing shortage has driven the state’s foray into MMC. QBuild is a commercialised business unit of the state government. It teamed up with the Office of the Queensland Government Architect and industry suppliers to deliver around 100 homes by the end of 2023.
At the federal level, the government has pledged to build 1.2 million homes in the next five years – an annual construction rate of 240,000 houses. But current projections for 2024 foresee only 180,000 houses built.
This raises the question: has the Australian industry learned enough from its pilot projects to use MMC to meet this ambitious housing target? I’ll be watching keenly.
Martin Fenn MCIOB is CIOB’s MMC lead for Oceania and a consultant to emerging contech companies.