Tom Adlington explains how battery energy storage systems are helping Sir Robert McAlpine and Keltbray cut costs while making their sites greener.
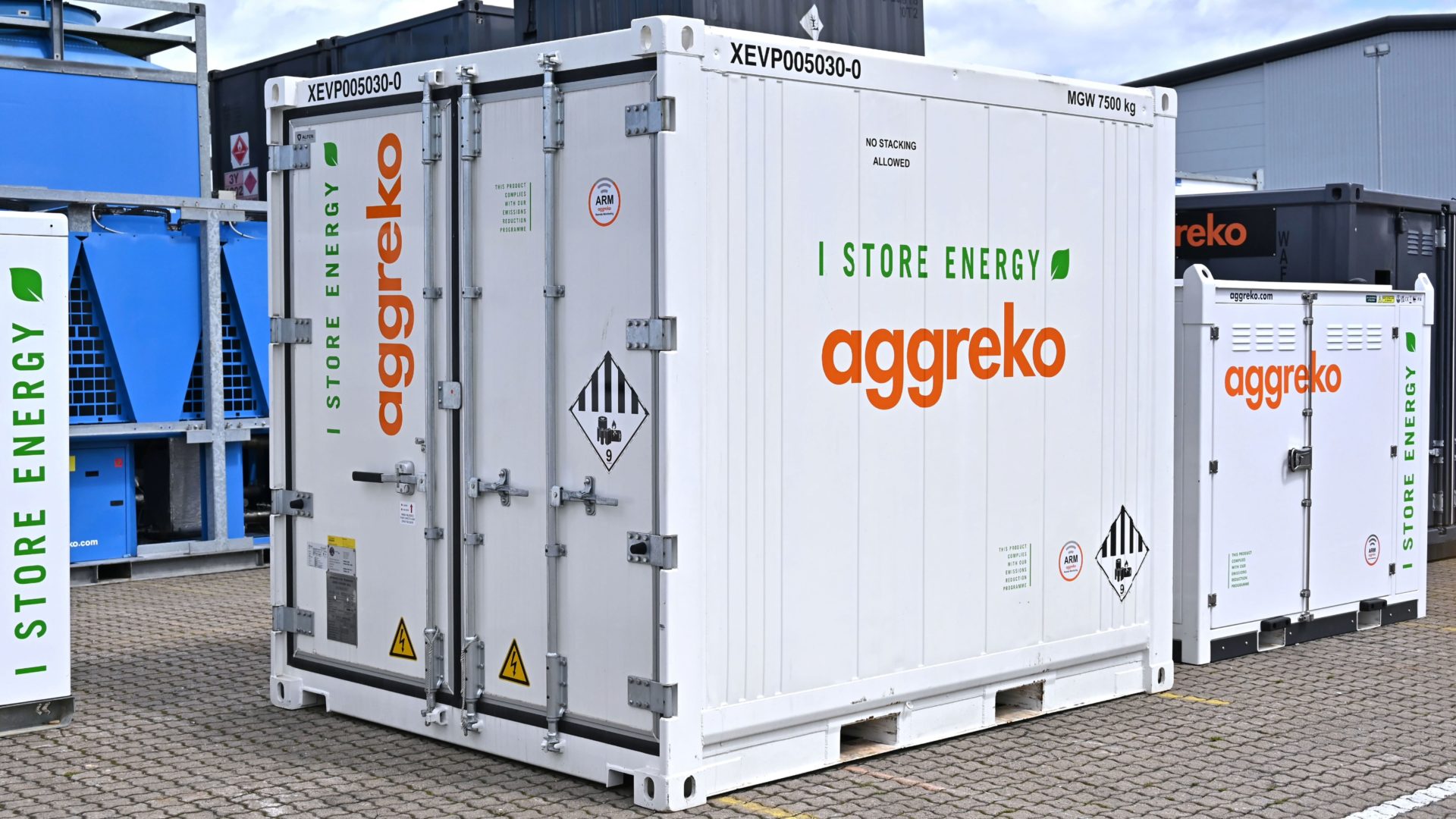
Construction managers face increasing sustainability challenges: from meeting decarbonisation targets, new emission regulations and decreasing fuel consumption on site, to capex spending and variable load concerns, the list is likely to continue growing.
While each challenge is different, incorporating battery energy storage systems (BESS) technology within a hybrid temporary power package can help overcome these obstacles.
This has been the case for Sir Robert McAlpine and Keltbray which, through partnerships with Aggreko, are tackling various challenges by incorporating BESS on site.
But to effectively reduce noise and emissions and address capacity limitations from constrained power connections or limited generator capacity, accurate specification is critical.
So, how do you achieve success with BESS?
Getting to grips with load profiles
On the surface, load profiles may seem straightforward. But when it comes to bringing BESS on site, it is essential to understand what needs to be powered and when.
The typical nature of power consumption on construction sites means peaks and troughs are common. However, this also means generators are often oversized due to the misconception of incorporating greater power to meet start-up demand.
Low demand, peak demand and the base load should be identified when assessing the load profile. Peak demand can be calculated using the highest power requirements and any high inrush currents caused by power-intensive machinery or motor starts. Notable periods of lower power demand or power loads that persist for extended periods can then be accounted for.
By understanding the load profile and any patterns or timings, we can understand where BESS can add value, and integrate the best generator and BESS combination. In the case of Sir Robert McAlpine, five live tower cranes were analysed for emissions and fuel savings after industry-first field trials identified where savings could be made. The tower cranes were then powered with smaller generators, BESS, and more sustainable fuels.
Overcoming environmental restrictions
Emissions and noise are critical considerations for decision-makers and complying with these restrictions is becoming increasingly challenging. Implementing BESS into a hybrid power setup can provide a greener intermediate power supply during peak demand.
Sir Robert McAlpine’s project achieved an 85% reduction in emissions across the five tower cranes with Aggreko’s BESS after rightsizing generators. That is equivalent to more than 234 tonnes of CO2 and 87,300 litres of fuel saved.
Over four months, the tower cranes were powered by HVO-fuelled generators and BESS with batteries operating the crane and generators only running at times of peak load or to charge the batteries.
Significant savings can also be achieved in urban areas where quiet periods at specific times are mandatory. BESS is a quieter alternative, making it particularly useful for sites bound by noise legislation.
Staying on top of costs
Temporary BESS solutions make incorporating the latest technology more affordable and do not require decision-makers to dip into tight capex pots.
As well as manageable upfront costs, fuel savings offered by BESS make it an attractive energy solution. Construction engineering specialist Keltbray saw this saving first-hand when Aggreko’s battery technologies were introduced across 12 projects.
In a bid to decarbonise its power usage and reduce running costs, Keltbray shifted from zero batteries on-site to 25% of its temporary power procurement being provided by them. This resulted in a reduction of more than 200 tonnes of carbon equivalent to 75,000 litres of fuel and a saving of over £100,000 in fuel costs.
Capitalising on controls
Controls can help further optimise BESS power distribution and support system reliability by controlling and monitoring parameters. Remote monitoring can also enhance flexibility and responsiveness while pushing cost optimisation by reducing fuel consumption.
The battery storage industry must ensure customers are aware of the possibilities of the technology to help improve standards and encourage broader awareness and adoption of BESS.
The above examples of success and best practice advance the case for the technology as a viable alternative to traditional power sources.
Tom Adlington is sector sales manager of building services and construction at Aggreko.