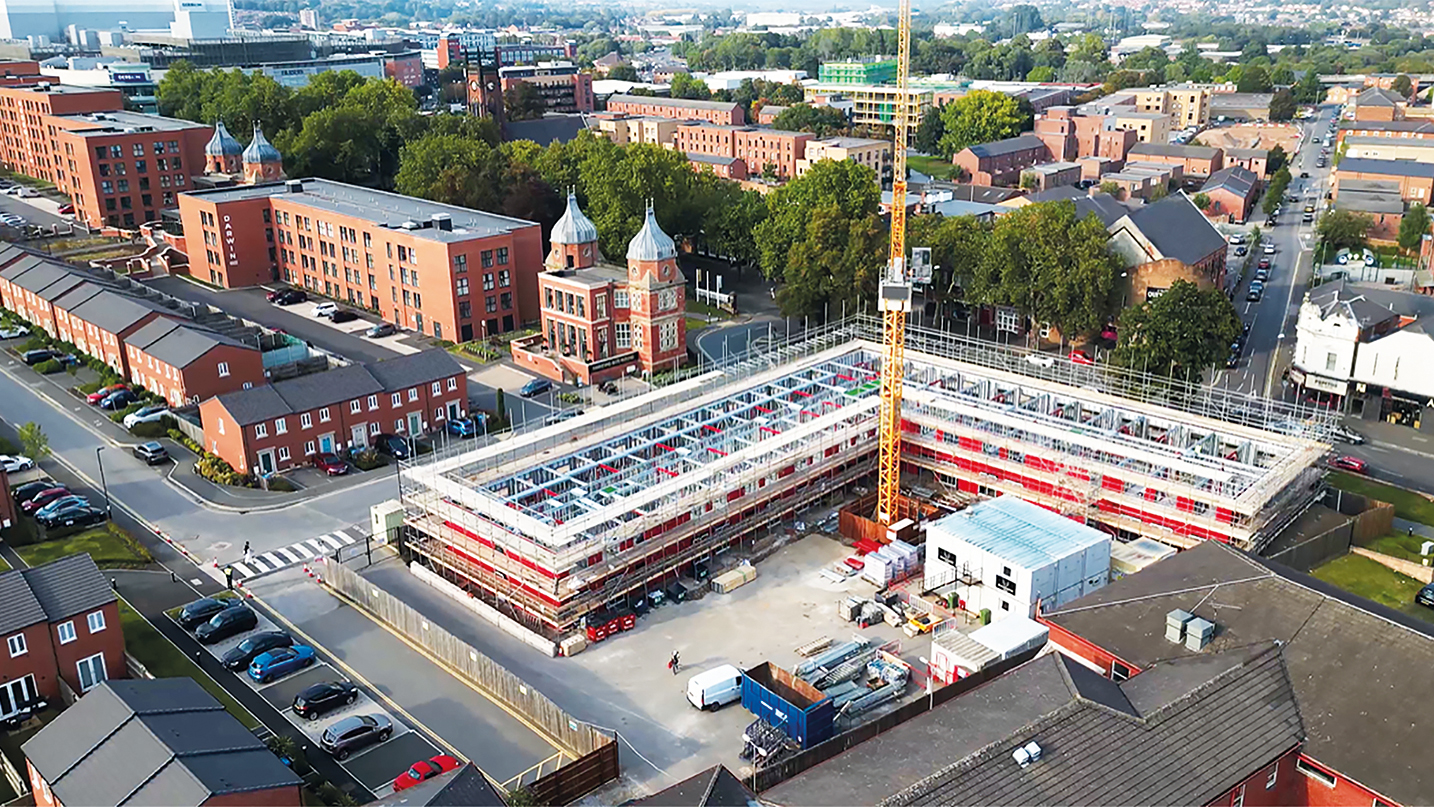
A new light-gauge steel specification offers help for housebuilders looking to accelerate delivery. By Nick Barrett.
Modern methods of construction (MMC) will be invaluable in tackling the UK’s housing shortages, and light-gauge steel will have a key role to play.
Pioneers of MMC have of course been pushing the merits of light-gauge steel for many years, and can point to long track records of successful projects. Specific standards for the production and use of light-gauge, cold-formed, steel have been lacking, however. A new specification has just been launched that aims to fill that gap.
The British Constructional Steelwork Association’s (BCSA) National Light-Gauge Steelwork Specification (NLSS) aims to support more widespread use of light-gauge steel by giving the industry documents that can be incorporated into construction contracts. It is expected that the specification will be incorporated into the individual project specification, and thus be part of the total building contract.
“The new specification has been developed with input from the wider construction as well as the light steel manufacturing industry and will give the supply chain confidence that the steel on their projects is a quality assured product, manufactured and used to the highest regulatory standards,” says BCSA CEO Jonathan Clemens.
Light-gauge steel frame structures use galvanized cold-formed steel sections as the primary structural components, assembled off site into prefabricated panels. The material is strong, lightweight and has proven to be durable.
The specification sets out a framework of requirements to reassure designers, clients and contractors that the light-gauge steelwork industry is able to establish and maintain high standards in all areas of its operations. It establishes what the high standards are exactly and delivers clarity of expectations, outputs and outcomes.
Greater transparency
When the specification comes into force from April 2025, it will harmonise the approach to the use of light-gauge steel and provide definitions of the common terms used in the industry. This transparency will reduce risk, improve communication and lead to raised quality standards.
The information to be included in a project specification is spelled out for the first time, covering areas such as the materials to be used, transfer of design information, manufacture and assembly, installation, requirements for protective treatment and quality management.
The specification provides a uniform set of requirements for the manufacture and construction of light-gauge steel structures in compliance with the requirements of European standards. It also includes a section on quality management, which requires the designers, manufacturers and installers for light-gauge steel structures to have the necessary facilities, skills and quality management systems in place.
“The specification will initially be voluntary, but support is being given by all the relevant key trade associations, so its use is expected to be widespread,” says Clemens.
Light-gauge steel creates landmark neighbourhood
Derbyshire residential project demonstrates effectiveness of new specification.
Wavensmere Homes is demonstrating how housebuilders can benefit from the increased assurance that the new light-gauge steel specification will bring.
The 925-unit Nightingale Quarter development on the former 7.5ha Derbyshire Royal Infirmary site is being built for Wavensmere by light-gauge specialist HadleyFrame, which designs, engineers, details, manufactures and installs its system using Hadley profiles.
The development overall comprises 800 apartments and 125 houses. Currently under construction is the five-storey Block E6. Block E6 comprises 95 apartments, using 164 tonnes of cold-rolled steel and 42.5 tonnes of hot-rolled.
Offsite manufacture
The facade is of traditional masonry. Offsite-manufactured, pre-panelised load-bearing
light-gauge steel framing is being used for the block. External panels with sheathing board and breathable membrane were constructed off site in factory conditions.
Stephen Hall, technical fellow with Hadley Construction Technology, who was involved in developing the new specification, says: “When working with advanced construction technologies it is crucial that our works match the state of the art.
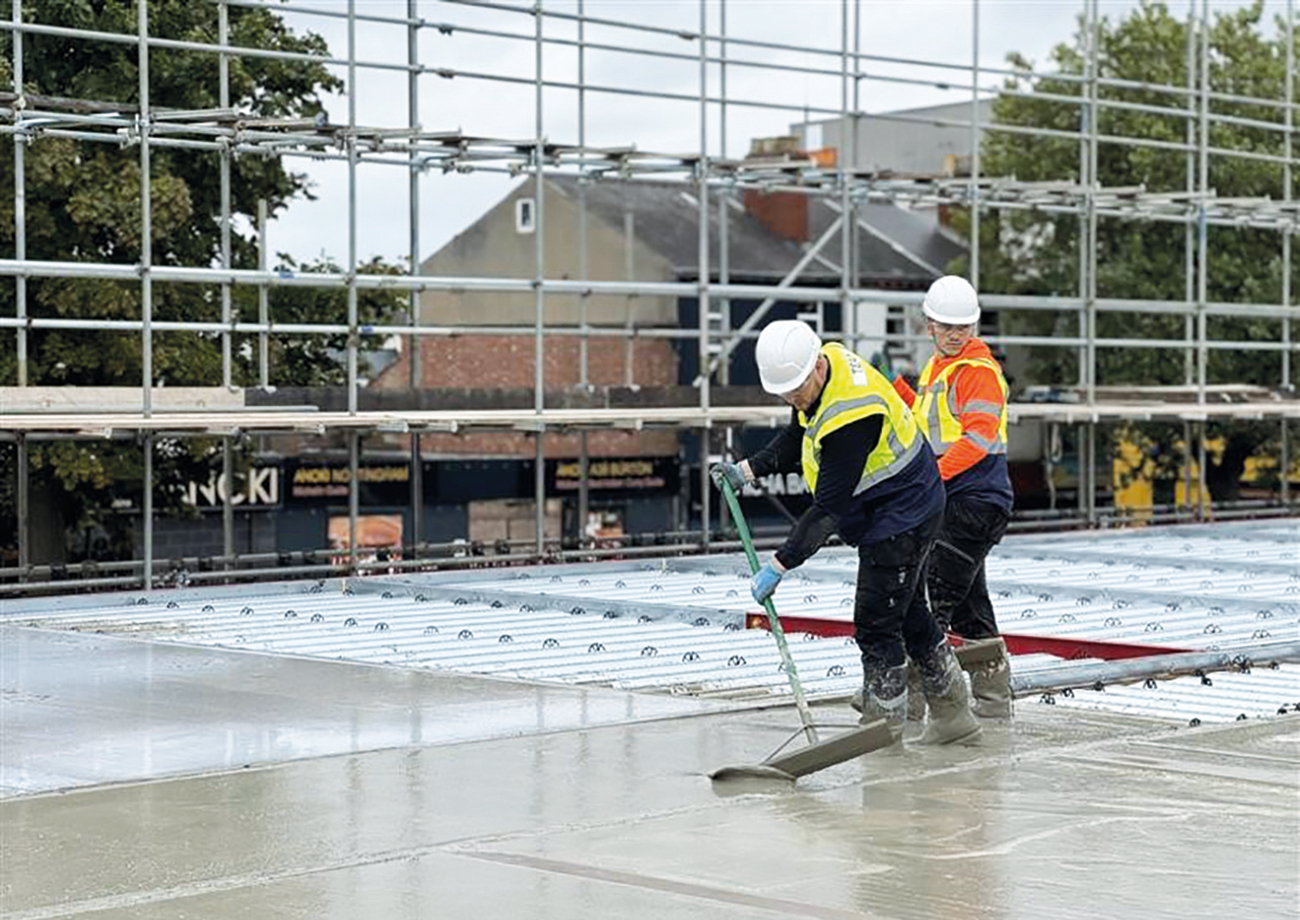
“With that in mind, and knowing that the publication of the specification was on the horizon, aligning with the proposed requirements was at the forefront of our minds on this project.
“The specification provided us with guidance covering everything from exchange of information to material and component compliance, and a suite of stringent execution tolerances. Having these requirements within a single resource streamlined our quality compliance and provided a consistent framework that we adhered to at Derby and will continue to do so across future schemes.”
Matt Brighton, commercial director at Wavensmere Homes, says: “The demand for housing continues to rise and steel-frame MMC is an excellent way to meet that demand, allowing us to achieve requirements for engineering, performance and programme. The HadleyFrame pre-panelised system is perfect for our projects as we build up to 15 storeys and need follow-on trades on site at the earliest opportunity.
“E6 is the final phase of the Nightingale Quarter development, and we have occupants in the first phase where the units outperformed building standards for acoustics and airtightness, so our residents have comfortable, low-energy homes.”