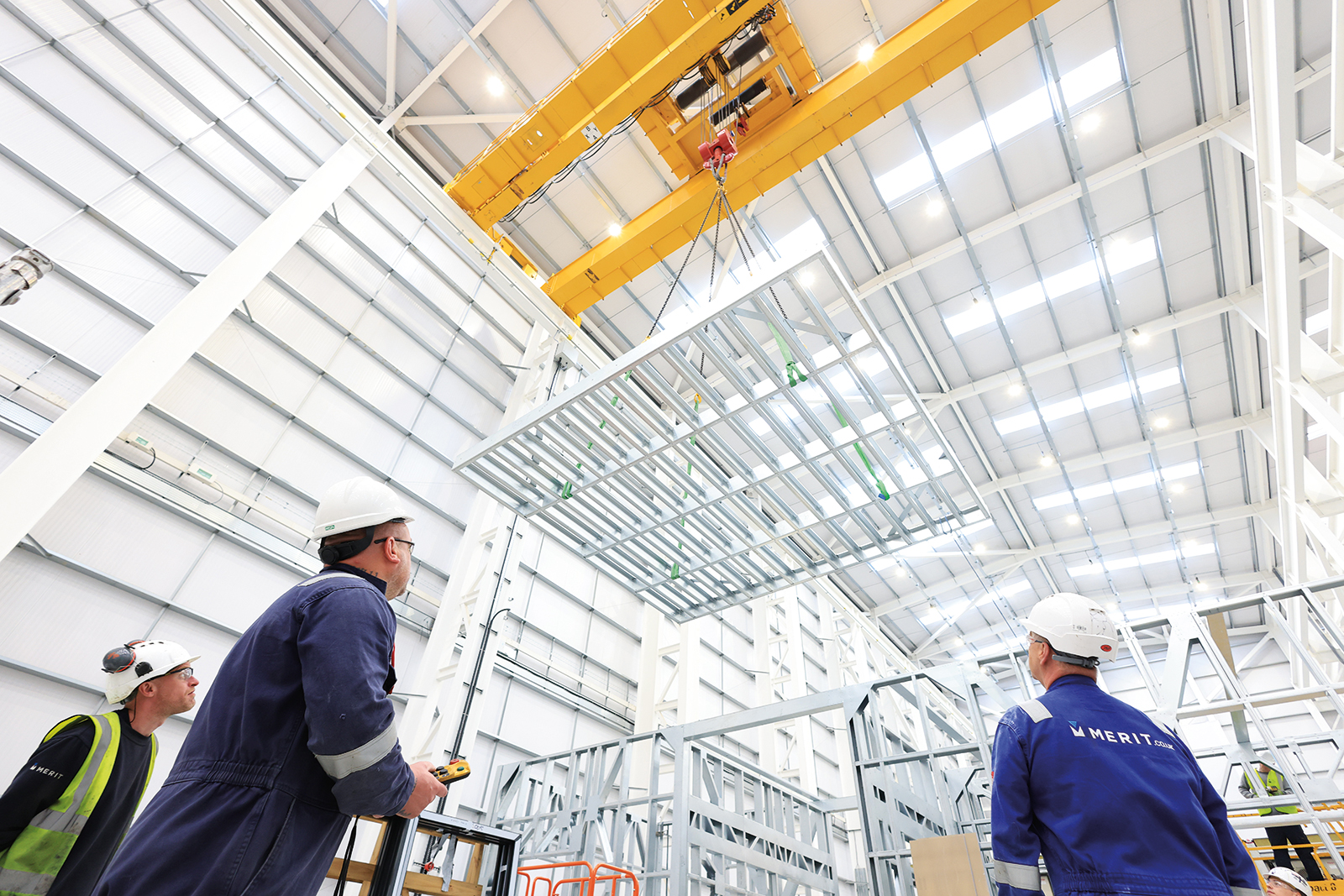
In the north-east, Merit is turning construction on its head, designing and building from the inside out. Kristina Smith visited its manufacturing base to find out how.
There is an energy of positivity and urgency about Merit, which exudes from CEO Tony Wells, and seems to permeate his young and enthusiastic team. Based in Cramlington, near Newcastle, the company is trying to achieve something that has evaded the construction industry for decades: a significant uptick in productivity.
“We are trying to prove we can deliver buildings in one-third of the time, compared to design and build, with fixed-price certainty,” says Wells.
It’s difficult to find the right words to describe what Merit does. Offsite construction or MMC (modern methods of construction) company doesn’t really cut it.
Wells calls Merit a ‘platform manufacturer’. The company designs buildings from the inside out, configuring them around its platform of premanufactured elements that include plant rooms, building services modules, room pods and walls.
More than MMC
David Philp, chair of CIOB’s innovation panel and chief value officer at Bentley, who has visited Merit’s facilities, says this: “Their operating model is different from a traditional MMC company, more what I think 4.0 would look like, the way they facilitate flexibility into their approach.”
Merit doesn’t deliver just any type of building. It is focused on certain sectors: pharma, biosciences, healthcare, semiconductor, aerospace, battery tech and education. “We have stuck with more complicated buildings rather than trying to be Ilke Homes,” says Wells.
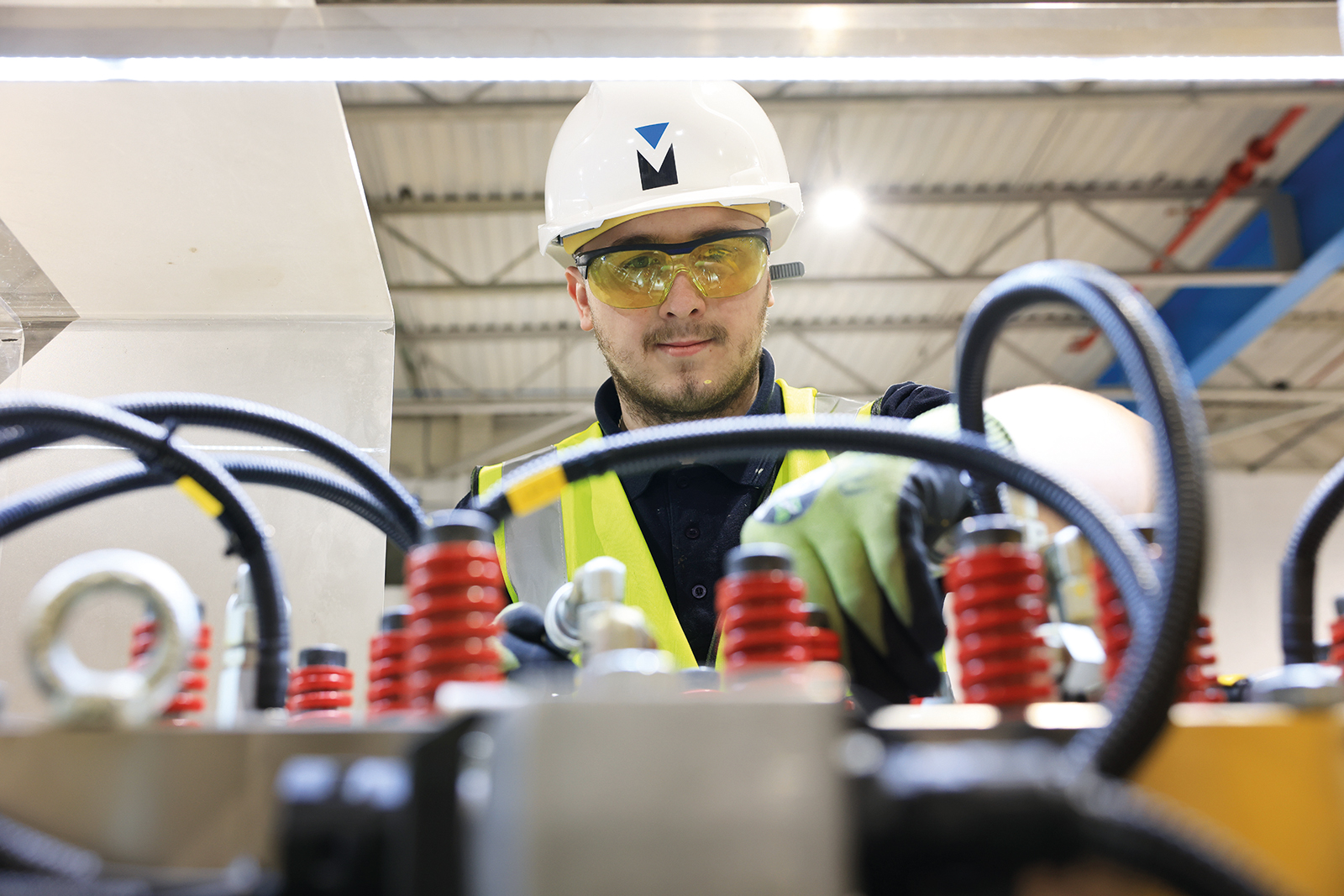
Ilke Homes, once lauded as a pioneer of offsite construction, went out of business in 2023, after investors pulled the plug. Merit’s business model is very different.
“We can get a higher output per square metre than an offsite housing manufacturer, probably 10 times as much in terms of overall sales,” says Wells. “The products we make are more concentrated in terms of value. With a house there’s a lot of empty box.”
Another key difference is that Merit is self-funding the development of its products, increasing automation in its processes and the expansion of its manufacturing facilities.
Reinventing construction
Wells, whose career has spanned semiconductors, startups and multiple continents, took over Merit – then a £2m turnover pipe-fitting company – in 2002. It grew rapidly to around £50m turnover by 2008 with an electric array of projects that included mechanical services for the Diamond Light synchrotron at Didcot, an M&E fit out at the Halley VI research centre in Antarctica and M&E upgrades for Harrods.
Frustrated by an inability to break through the £50m turnover barrier, Wells embarked on a new direction, ripping up the business plan and telling his management team they were going on a “journey of reinvention”. The idea was to create a platform of products that allowed flexibility and even “flamboyance”, says Wells.
A decade down the line, Merit is on version 6.2 of its platform and is turning over just shy of £80m. It delivers buildings through two routes which it calls Flexi Pod and Ultra Pod – and sometimes through a combination of the two.
Flexi Pod sees a building’s frame constructed traditionally in steel with various offsite-manufactured units slotted into it. It involves pods containing plant room equipment, pre-assembled modules (PAMs) which slot together to distribute building services, and specialist room pods such as bathrooms. Merit also manufactures the framing to support cladding.
Modular build system
Ultra Pod is a modular build system, where individual or multiple pods are fully kitted out and transported to site. These are designed for smaller buildings – generally up to 1,500 sq metres and no more than four storeys high.
The latest additions to its platform – all patented or patent pending – are a wall PAM and a transition PAM. The wall PAM is an alternative to British Gypsum’s framing system which uses 80% less Gyproc but gives the same fire and acoustic performance. The transition PAM is a version of the wall PAM through which services pass, with the passive fire protection built in during the manufacturing process.
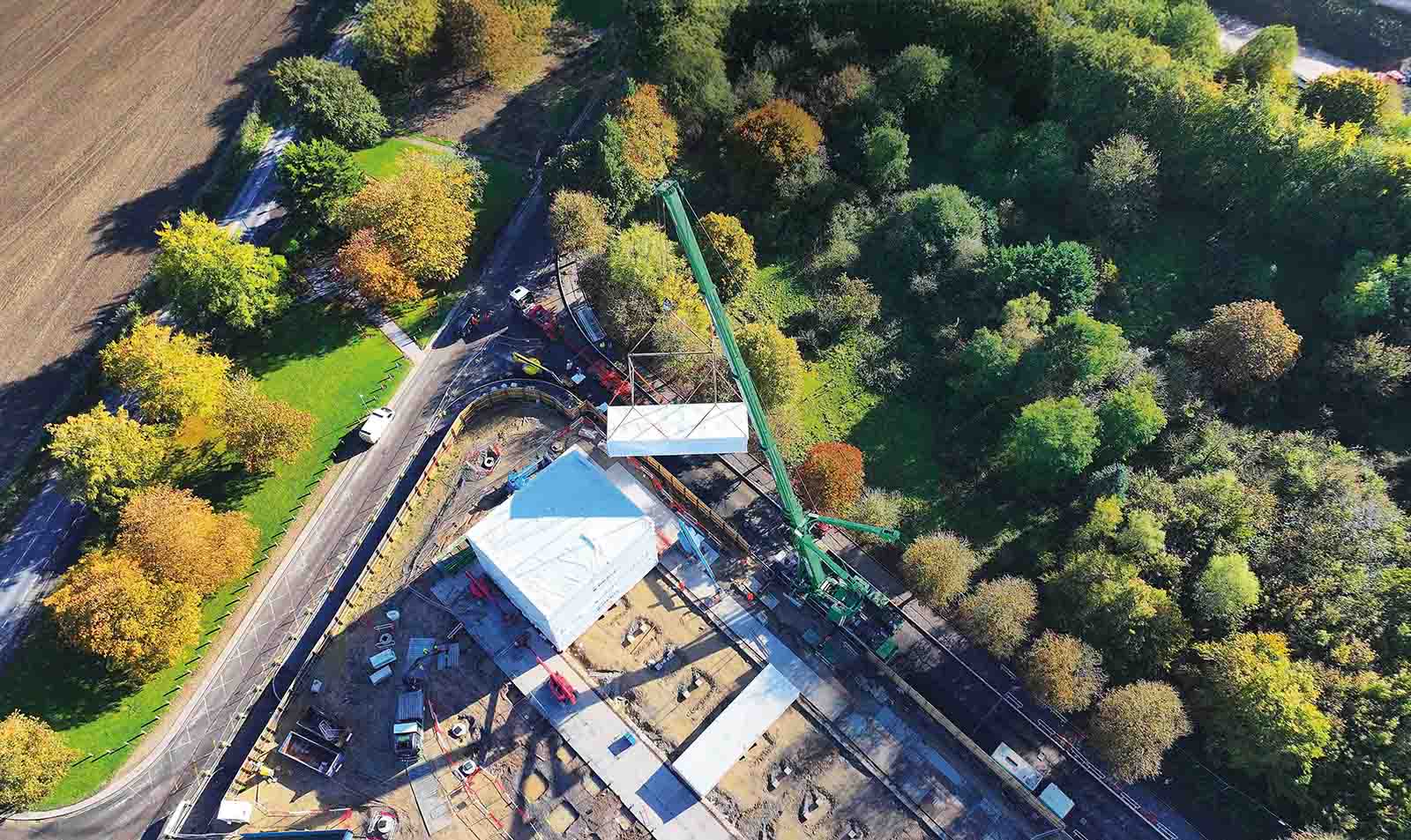
“We have spent £100,000 on fire testing to validate that wall system,” says Wells. “There’s an awful lot of product development gone into these designs. We don’t sell any of these to anyone else.”
In getting to variant 6 of its platform, Merit has honed its plant rooms to be more compact and more efficient than any traditional design. That means air source heat pumps, heat recovery, with all the building management services and controls integrated into plant room pods.
“The running costs are about one-third with electricity compared to gas because it’s a very different strategy for M&E and HVAC,” says Wells. “Air source heat pumps are not a replacement boiler; you have to apply them differently.”
Less energy use
For instance, says Wells, the new 10,500 sq metre Berwick Community Hospital which Merit is delivering for Northumbria Healthcare NHS Foundation Trust will use 69% less energy than the CIBSE benchmark.
Whereas plant takes up 32% of space in a typical healthcare building, Merit can more than halve that. For a current project to build an emergency care unit for Bedford Hospital, plant will take up 15% and the goal is to get even lower, says Wells. That means it can offer its customers more space for their operations, or smaller buildings – hence lower capital and running costs and lower carbon footprints.
“We can build you a Scope 1 zero carbon enabled building for less cost,” says Wells. “People would say you pay a premium for that. I say that’s not true.”

Alongside its physical products, Merit has been developing its design process and its in-house team to deliver that design. The goal is to move more and more aspects of the design and construction process in-house. To that goal, an in-house architectural team was created five years ago. Soon to be 14-strong, this is headed up by Molly MacDonald, who joined Merit in 2020 as a graduate.
Merit is a young company, with an average age of 31 and an industry-average-busting 20% women. Oliver Calimer, virtual design and construction (VDC) model engineering manager, graduated in 2018 and joined Merit in 2021 and now heads up a team of 27 people.
Thinking in 4D
For these designers it is business as usual to think and work in 4D. When a tender comes through the door, one of the first activities for Calimer’s team is to work out the ‘Pod PAM strategy’: which of the premanufactured elements will go where. “We look at the M&E design with a focus on offsite manufacturing constructability,” says Calimer.
Merit disbanded its estimating team in 2023 and now uses a process that Wells calls parametric costing. “We have a very well-developed square metre rate,” explains MacDonald. “The areas go into the cost model, and the number comes out.”
This fast pricing mechanism has several benefits, says Wells. Merit can give its clients an understanding of what they can afford upfront, it doesn’t have the overhead of an estimating department and, in a market where contractors are reluctant to enter into fixed-price contracts, Merit can give cost certainty.
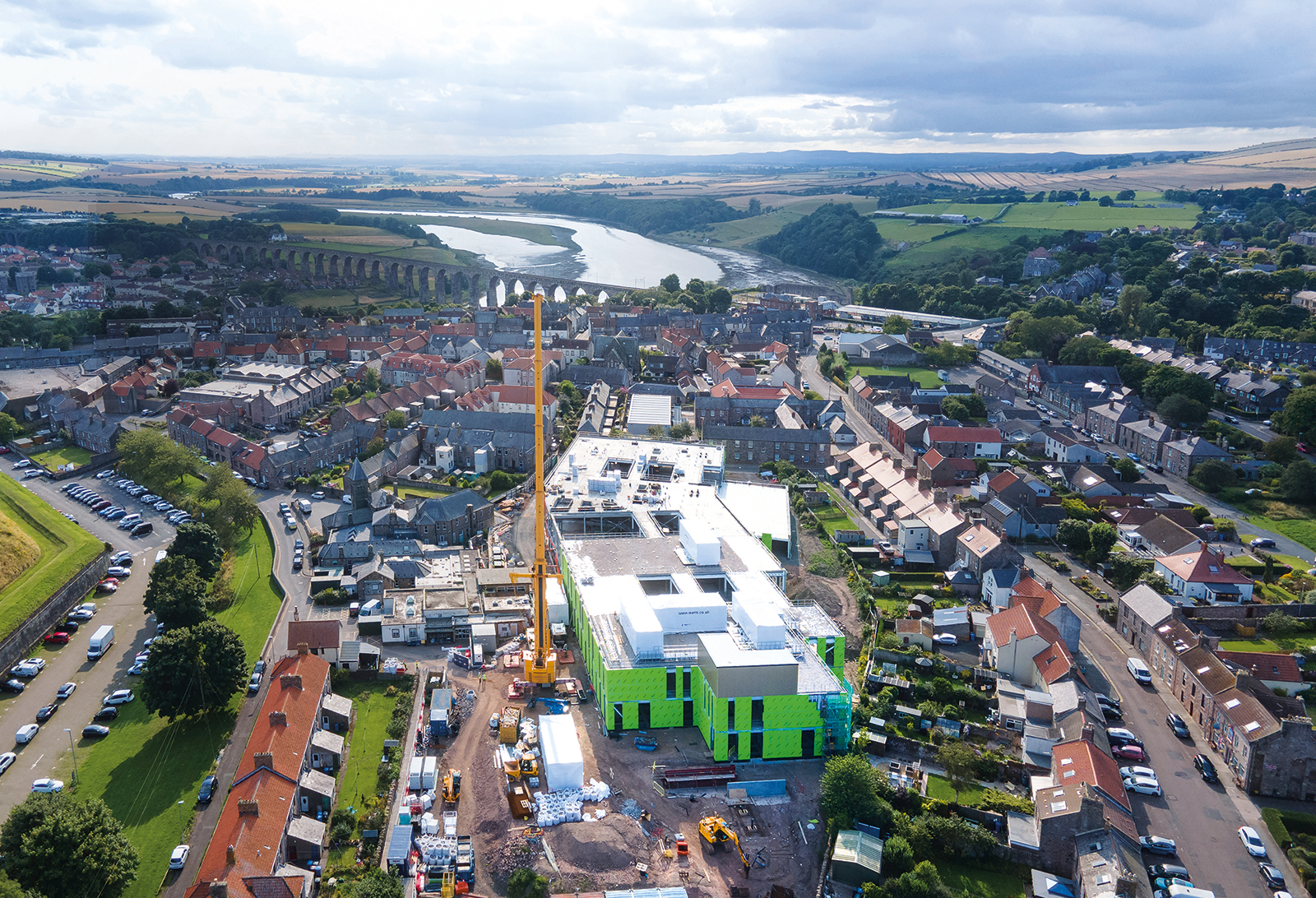
There is no federating of multiple BIM models, as there would be on a traditionally delivered project. Merit has the one model, with in-house people writing Python codes that automate the translation of the Revit model into drawings for fabrication.
“We create an identical digital twin of what we will be manufacturing in the factory or on site down to the nuts and bolt bolts level of detail,” says Calimer.
Calimer explains that his team runs computational fluid dynamics (CFD) simulations at RIBA stage 4 to fine-tune things such as the position of grills and to check out thermal performance and noise issues. After that, it runs clash detection.
“We then use commissioning data live from site to check on the simulations and it’s always very close,” says Calimer. “All our future projects are based on what we find out.”
Procurement change
Despite Merit’s growing list of successfully delivered projects, the challenge of persuading clients to do things differently is still one of the biggest it faces, says Wells. “The issue for us is adoption, getting onto a framework, convincing clients to buy new things. That’s the hardest part of bringing new technology to the construction industry.”
Philp thinks that the industry needs to innovate on its procurement rates too to get more value from platform delivery models like Merit’s.
“We talk about sector advancements but yet we are still using a traditional project level approach,” he says. “We need to think about what the potential procurement routes look like for a more DfMA (Design for Manufacturing and Assembly) approach.”
The argument is getting easier, says Wells, since Merit can now compete with traditional construction on both time and cost. “In 2021, we were a bit more expensive but now we are doing it even quicker,” says Wells.
“And, since then the cost of traditional construction has gone up, and we have got better at what we do, we have now gone over that crossover point. If we’re competing against a larger company, we are there or thereabouts and also significantly quicker.”
Advanced manufacturing facilities
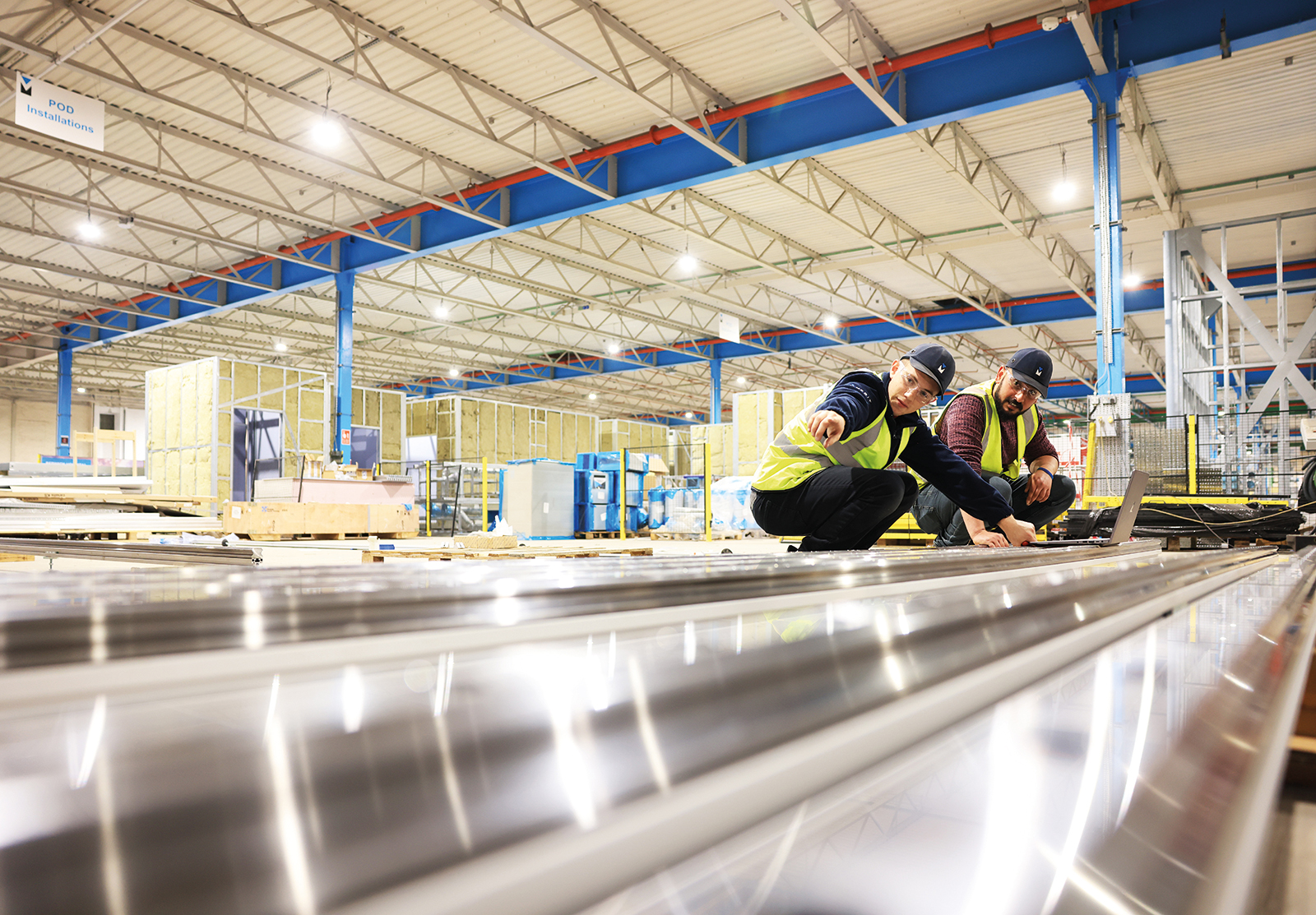
Merit has two factories on two sites, both a short drive from its offices in Cramlington. It bought the second facility in 2020, extending it in 2023 to bring its total manufacturing space to 24,500 sq metres (264,000 sq ft).
At the new site, piles are already in the ground to allow for a further expansion of 11,240 sq metres (121,000 sq ft) for which it already has planning permission.
Some 127 people work across the two factories, with that number set to grow. Many have come through the apprenticeship route: Merit has taken on 95 since 2013, 18 of those this year.
While most MMC facilities look like a construction site under a shed roof, Merit’s factories are different, observes Philp: “It feels more like an advanced manufacturing facility. Every workstation is spotlessly clean and information is flowing all the way through.”
With £3m worth of machinery in the factories, and over 30 machines purchased in the last three years, there are plans for further investment in equipment, says automation manager Justin Moorton: “We have 12 engineers looking at factory automation and digital automation. We want to automate anything that is dull, dirty or dangerous.”
His team is working with manufacturing colleagues to streamline the way that work flows through the factories.
12m-long plant room pod
The pods in the high bay area of the newer of the two factories are impressive. We look at one 12m-long plant room pod which contains air handling units, heat recovery, air source heat pumps and a building management system.
Some of the PAMs are pretty big too.
“I remember when we did the first PAM, it was 800kg. Some of these are 2.5 to 3 tonnes each,” says manufacturing director Steve Smith, who has been with Merit since 2004.
What differentiates Merit from other companies that manufacture M&E modules offsite is that it integrates almost everything into its PAMs, aiming to do most of the second fix – as well as the first fix – in the factory. Lights are ready to just drop down, data cabling is cut to length.
“A lot of MMC is first fix in the factory and second fix on site,” says Smith. “We pre-test everything here,” he says. “Our speed on site is much faster, and we need fewer people on site.”
Another benefit of Merit’s approach is that lessons learned on one project are baked into the next one, speeding up delivery.
“It’s set up in a way that facilitates continuous improvement, rather than requiring constant reinvention for every project,” comments Philp.