The healthcare JV between Vinci and Sir Robert McAlpine transformed a former railway station into the north west’s covid-19 hospital in just two weeks. Will Mann hears the construction story from Vinci director John Roberts.
Patients admitted to Manchester’s new Nightingale hospital will be able to look up at the distinctive arched roof of the city’s former central railway station. Turned into a vast exhibition centre after the station’s closure in 1969, with over 17,000 sq m of floor space, Manchester Central was quickly identified as a suitable venue for one of the covid-19 field hospitals once the pandemic struck Britain.
Integrated Health Projects (IHP), a joint venture between Vinci and Sir Robert McAlpine, was selected to convert the convention centre, after delivering numerous other hospital projects in the north west through the P22 framework. The P22 contract template was used for this 750-bed hospital project.
Related
John Roberts, regional managing director for Vinci and IHP, picks up the story: “The call from the NHS came on Friday 17 March at 5pm and we confirmed our interest in the Manchester Nightingale Hospital. We didn’t expect to hear anything further for a week or so but on Saturday morning at 11am IHP was confirmed for the job.
“We didn’t have much of a weekend. The Saturday was spent calling our key suppliers, notably M&E specialist NG Bailey. On Sunday, our director Gary Bowker and contracts manager John Fowler walked around the centre with McAlpine’s clinical liaison manager Caroline Mulholland, plus designers, key subcontractors and the army.
“On Monday, we started on site. Our flooring contractor Horizon laid over 2,000 sq m of vinyl that first day and would lay 14,000 sq m in total.
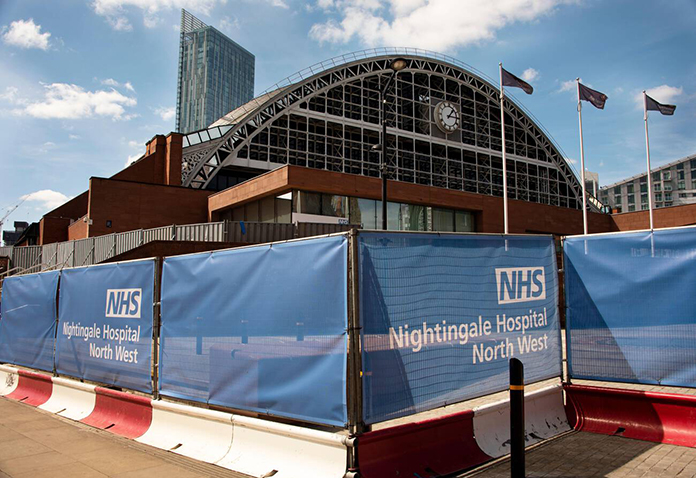
Project team
Main contractor: Integrated Health Projects (Vinci/Sir Robert McAlpine JV)
Project managers:
Mott MacDonald, Archus
Architect: BDP
M&E contractor:
NG Bailey
“Some subcontractors wanted letters of authority before continuing, but most got on with it. We didn’t get our letter of authority till the Monday after we’d started, but money has been largely removed from the picture here; the usual commercial blockers were put to one side, with the whole team focused on actually delivering.”
IHP worked with architect BDP, which had experience from the first field hospital built at ExCeL in London, to develop the design for Manchester Central. As the Nightingale name suggests, the wards were laid out in long rows of beds, to help nurse observation. Fitting a new hospital into a listed building while achieving healthcare compliance was a major design challenge, says Roberts.
“The army had been in beforehand and worked out a basic plan to max out bed capacity, but the design hadn’t been finished when we started building. As the spec changed, bed layouts and corridor widths had to change too. We used 13 different 3D Revit models which were adapted as work progressed.
In numbers: NHS Nightingale Hospital North West
- 13 days construction programme
- 300 workers on site
- 750 beds
- 14,500 sq m of flooring
- 150km of cabling
- 7.2km of copper pipes
“On the first Monday, we constructed a mock-up of a bed head. By the next morning, we were building 750 of them. As we built more and more, we had to find another supplier. The bed heads and ward separation use demountable hygienic wall panels, 2.3m high and 600mm-wide, which were also used to form corridors, line old walls and create staff areas. We fitted over 6,000 of these panels.
Modular M&E
“There was variation after variation. Medical air was added midway through the first week. IT was added to every bedhead in the second week. But the trust worked closely with us and any design questions could be answered quickly as the team were based on site.
“Most of the M&E plant was modular. The morgue, which can handle up to 100 bodies, was essentially made from giant fridges, which would normally be used for outside catering, and tented over. For clean air areas, we used mini air-handling kit which would also typically be used for event hire. We also had to bring in back-up generators though the centre was well-served for power.
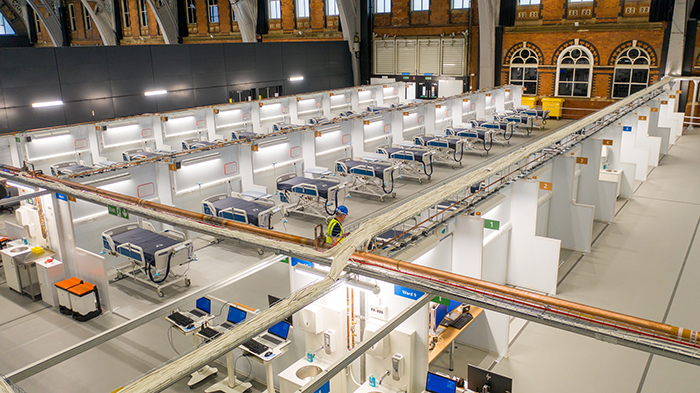
“Some materials were hard to source. Every spare oxygen connector in the country was taken up by the Nightingale hospitals during the period we were working at Manchester. We had to install over a mile of oxygen piping on this project. Any shortages were compounded by existing hospitals increasing their capacities to overcome the demand covid-19 patients created.
“The other big shortage was PPE. And toilet rolls. In the first two weeks, half of my time was spent to trying to buy toilet rolls, because people were stealing them as they didn’t have them at home. Toilet rolls were even being used in card games.”
Despite the fear and uncertainty created by the lockdown, IHP had no problem finding suppliers and labour to work on the project, Roberts says, with workforce peaking at 300.
“Our supply chain have reacted extremely well. Furloughing created a short-term glut of labour which would normally be delivering non-hospital projects.
“The Department of Health letter allowed our workforce to be classed as key workers, making it easier to get factories reopened or make special deliveries. We sometimes had to pay up front, due to lacking existing accounts. The police registered the number plates of our people and this avoided any of them being pulled over.
“Workspace, our furniture supplier, produced specific units for our covid-19 wards and I’m guessing their team never slept, as they delivered over 1,000 kitchen units in a fortnight, including nurse bases.
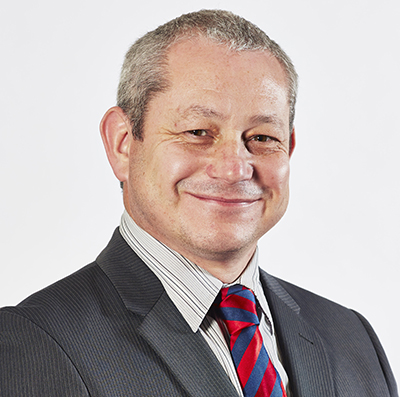
“The army presence has also made a difference. Having soldiers on site in camouflage focused minds on how serious this was.”
John Roberts, Vinci
“The army presence has also made a difference. Having soldiers on site in camouflage and berets probably focused minds on how serious this was. Major Matt Fry from the Royal Engineers would address a room and say, ‘Right, what’s the problem – we’re not leaving here until we’ve solved it’. The army helped us open up hotels for workers on the project to use and we fed them with an onsite canteen.”
“Yes, the 2m social distancing rule posed significant challenges. For tasks like installing the 600mm-wide panels, where two workers had to work within 2m of each other, specific risk assessments were carried out and face masks and other PPE were worn. The 24/7 working helped as with three shifts there was more space for the operatives.
“We took the temperature of workers every day as they came on to site, which was actually quite a quick and painless operation. In the men’s toilets, we blanked off urinals with tape to observe the 2m rule, and we turned off hand driers and used paper towels instead. Queueing for the canteen, which we set up with the army, and a staggered break system, worked well. Management meetings were held standing up at 2m spacing.
“None of our team at Manchester – or the 1,000 workers across all our north west covid-19 hospitals – showed any symptoms of the virus.”
IHP completed the Manchester Central Nightingale hospital in 13 days. Additionally, IHP’s north west healthcare business delivered a 31-bed covid isolation ward for The Christie in Manchester inside six weeks, plus further coronavirus hospitals in north Wales at Deeside – a 430-bed scheme in a leisure centre – and at Bangor, providing 223 beds.