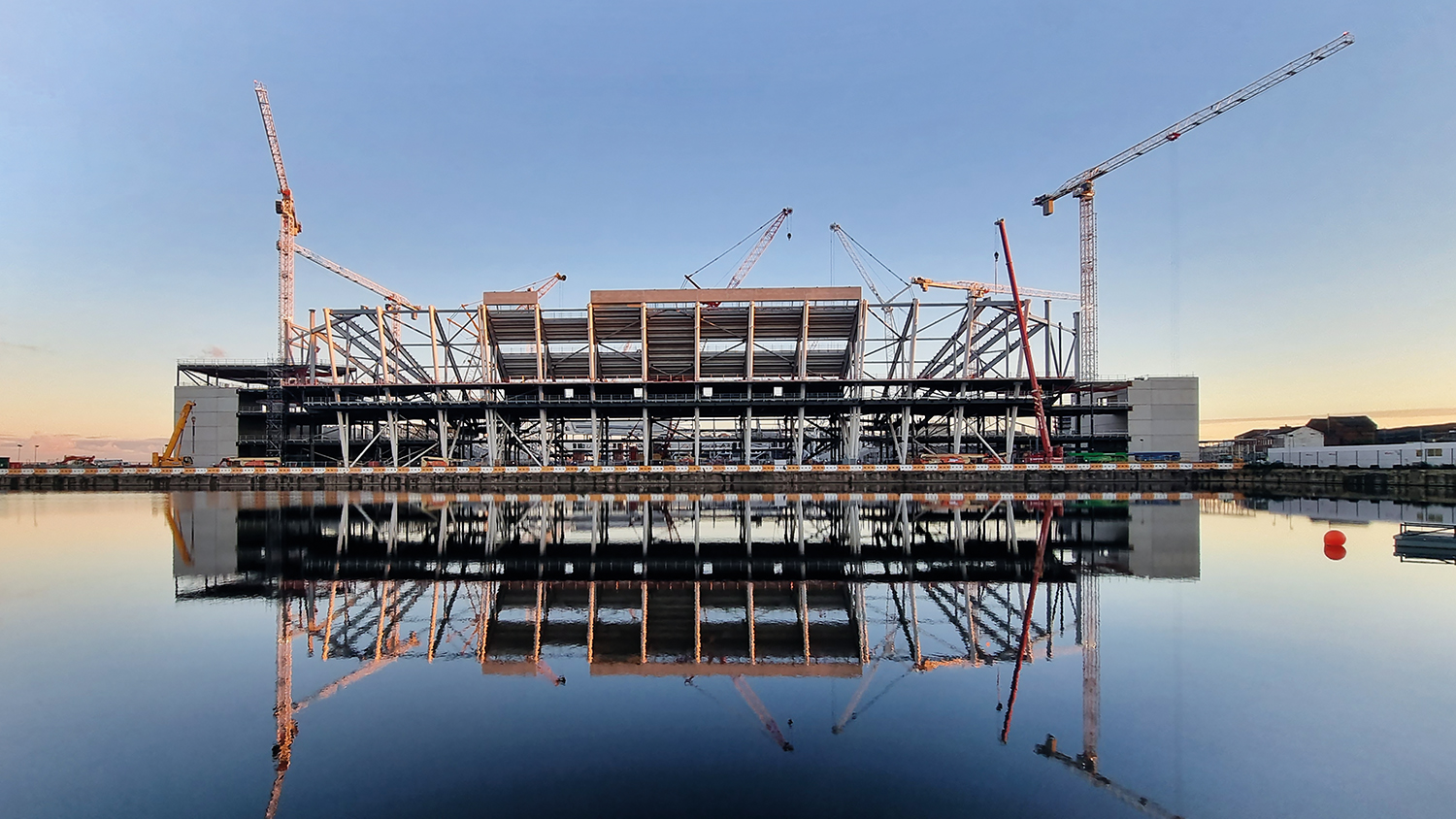
Could Everton FC’s beautiful new stadium, rising from the historical Northern Docks of Liverpool, be a metaphor for the fortunes of the club itself? Laing O’Rourke’s delivery so far certainly inspires hope. By Kristina Smith.
Walking the mile or so from Liverpool city centre to Bramley-Moore Dock – the site of Everton’s new stadium – feels like an industrial history tour, passing old brick buildings in various states of use and repair. Some have already been reinvented: the ex-rum warehouse across the road from the stadium, built in 1848, is now the swanky Titanic hotel with luxury apartments under development next door.
The new 52,000-seat Everton stadium, 3km from the club’s Goodison Park home, will feature bricks too: over half a million of them cladding the lower part of the walls. But unlike their historic neighbours, these bricks will not have been laid by brickies.
Everton Stadium project details
Client: Everton Stadium Development
Contractor: Laing O’Rourke
Value: £555m
Contract form: Bespoke, fixed-price contract
Start: 26 July 2021
Completion: 2024/25 season
Architect: BDP Pattern
Structural, MEP, civils design: Buro Happold
Key packages
Steel frame and gantry: Severfield
Precast bowl units: Banagher
Precast twinwall, columns, planks, panels: Laing O’Rourke (CEMC)
Envelope and roof: Lindner Prater
Landscaping: Vetter
MEP: Laing O’Rourke (Crown House Technologies)
Piling: Laing O’Rourke (Expanded Piling)
This stadium, being built for Everton Stadium Development by Laing O’Rourke, is a study in contemporary construction, using design for manufacture and assembly (DfMA) for many elements. So, every brick – or rather half brick – has been cast into a panel offsite, to be craned into position with no blood, sweat or tears, as every interface has been ironed out digitally before manufacture begins.
“That’s one of the great advances here,” says Laing O’Rourke’s technical lead John Edwards. “Hand-laying so many bricks would have been terrible for the workforce, due to the musculoskeletal problems it leads to in later life. Making the panels in a factory in Nottinghamshire means that people are working in a much safer environment, and it is a lot easier to control the quality.”
Game plan
The ‘LOR Game Plan’ for Everton’s stadium is displayed on the wall of the main project meeting room. The first of nine rules listed is ‘Make safety your highest priority’. Rule two is ‘Does it help the team on site? If not, why are we doing it?’
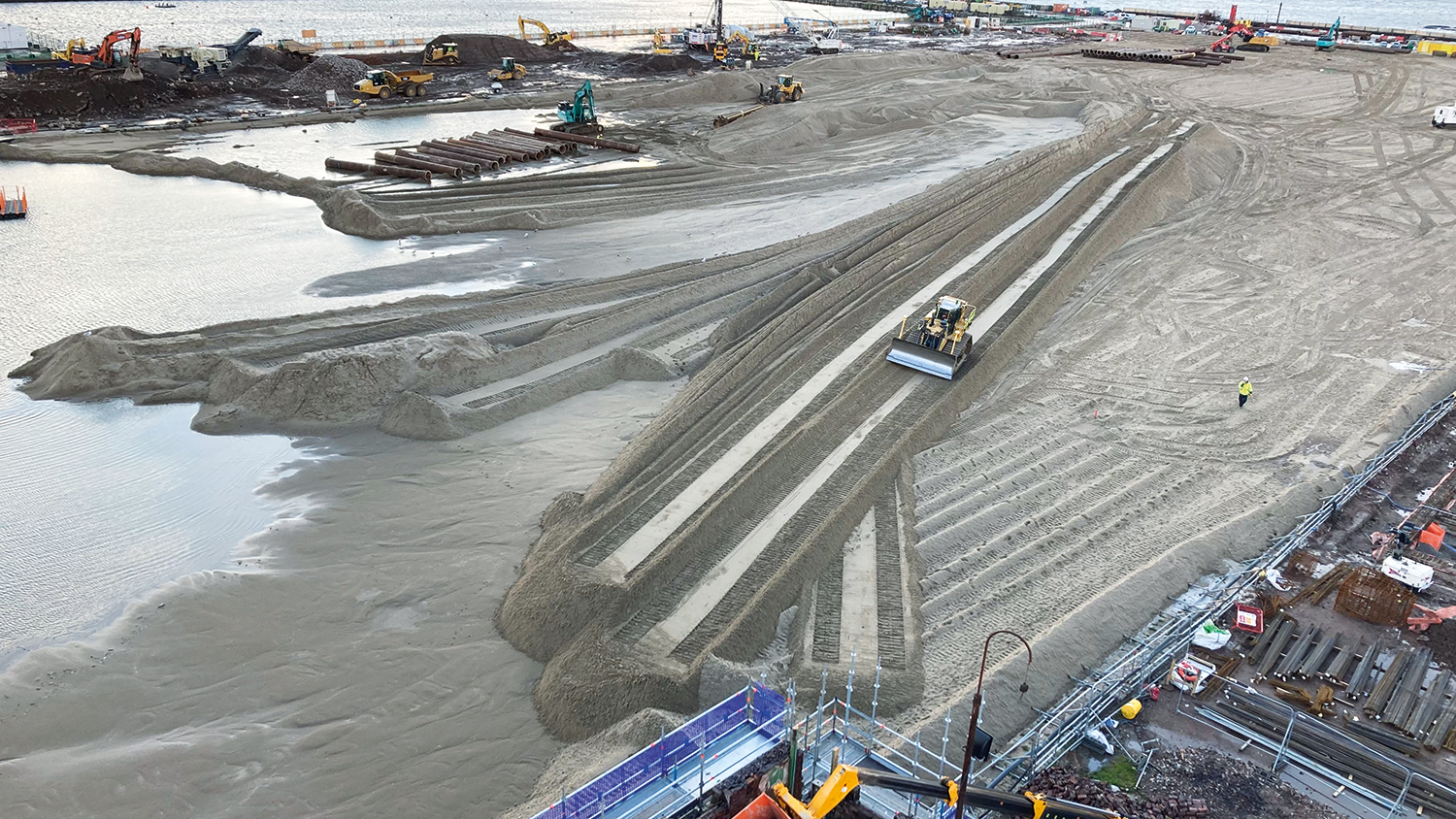
Further down the list is ‘We are not Building, Expanded or Crown House, we are Laing O’Rourke’, a reference to the group’s self-delivery of huge chunks of this project itself through subsidiaries Expanded Piling and Crown House Technologies (CHT). This rule reminds them they are all on the same side.
So far, the game plan here seems to be working well for the 150-strong Laing O’Rourke team, led by project director Gareth Jacques. Over the past year, the stadium has risen from the banks of the River Mersey to a point where the roof trusses are already being installed.
“It has been a phenomenal effort by the whole team to achieve this amount of progress,” says Jacques. “They have ensured the project is in a good position as we commence the fit-out stage.”
Everton has been planning a stadium move for over 25 years. Goodison Park, its home since 1892, is constrained by its location and a tight footprint. The club secured the new site in Liverpool’s Northern Docks area in 2017, signing a 200-year lease with Peel Holdings for Bramley-Moore Dock. It sits within the developer’s 200ha Liverpool Waters scheme.
Pre-construction service agreement
Everton Stadium Development appointed Laing O’Rourke as preferred contractor in February 2020 after a competitive tender process, with the parties initially signing a pre-construction service agreement (PCSA) for a design and build contract.
“The PCSA is when we can develop the details with the client and the design team,” says Edwards. For instance, in the plaza area through which fans will access the stadium, Laing O’Rourke and its designers carried out extensive wind modelling to test wind mitigation structures.
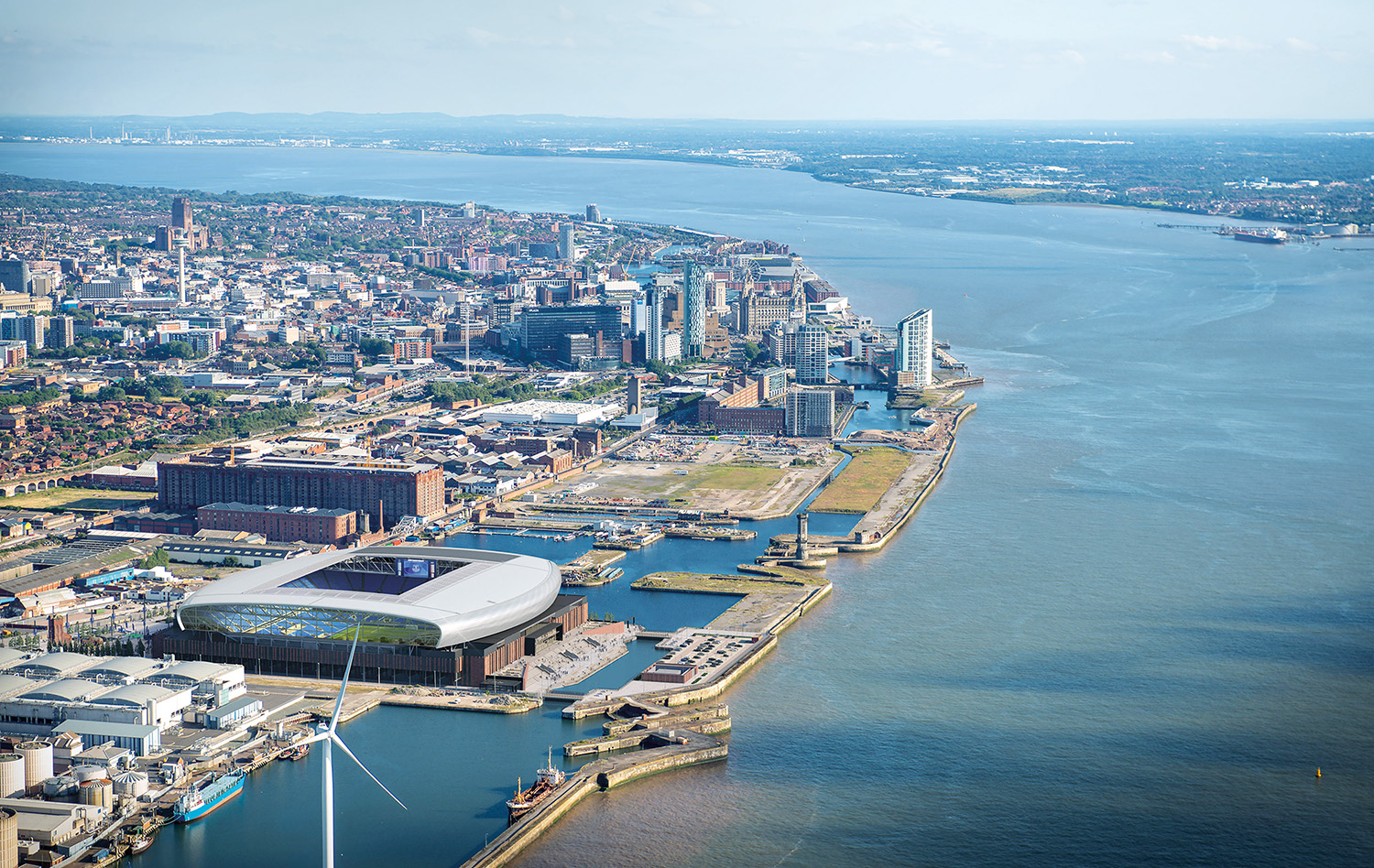
US architect Meis created the concept design, with technical input from BDP Pattern, which Laing O’Rourke then took on as its architect. BDP understands the contractor’s DfMA processes, Edwards says.
“BDP Pattern were appointed as lead consultant to deliver the Meis concept to suit our suite of DfMA products,” says Edwards. “Otherwise, it would be very wasteful.”
The building is founded on over 2,700 bored concrete piles which bear onto sandstone, connected by a cast-in-situ floor slab. The superstructure of the main stadium is steel with a barrel-vaulted roof and huge glass panels to make the most of the views across the city, the docks and the Mersey estuary.
Laing O’Rourke has removed, labelled and stored heritage elements from the original building and will painstakingly reinstate these. In the plaza, the Hydraulic Engine House which once operated the lock gates is being restored. The brick cladding is patterned to mimic the criss-cross steel work of Goodison Park.
DfMA philosophy
Laing O’Rourke’s DfMA philosophy is 70:60:30, delivering 70% of a build using offsite, making things 60% more efficient and saving 30% on programme. On the Everton stadium, around 70% of the superstructure and mechanical, electrical and plumbing (MEP) infrastructure has been delivered through DfMA.
The company’s Centre of Excellence for Modern Construction (CEMC) is supplying many of the precast elements: 564 twin wall units, 651 columns, 3,844 lattice planks and 731 facade panels. Precast specialist Banagher is supplying the 1,213 bowl units for the terraces, because the CEMC facility did not have the capacity, with other projects underway. Banagher’s units arrive from Ireland by sea.
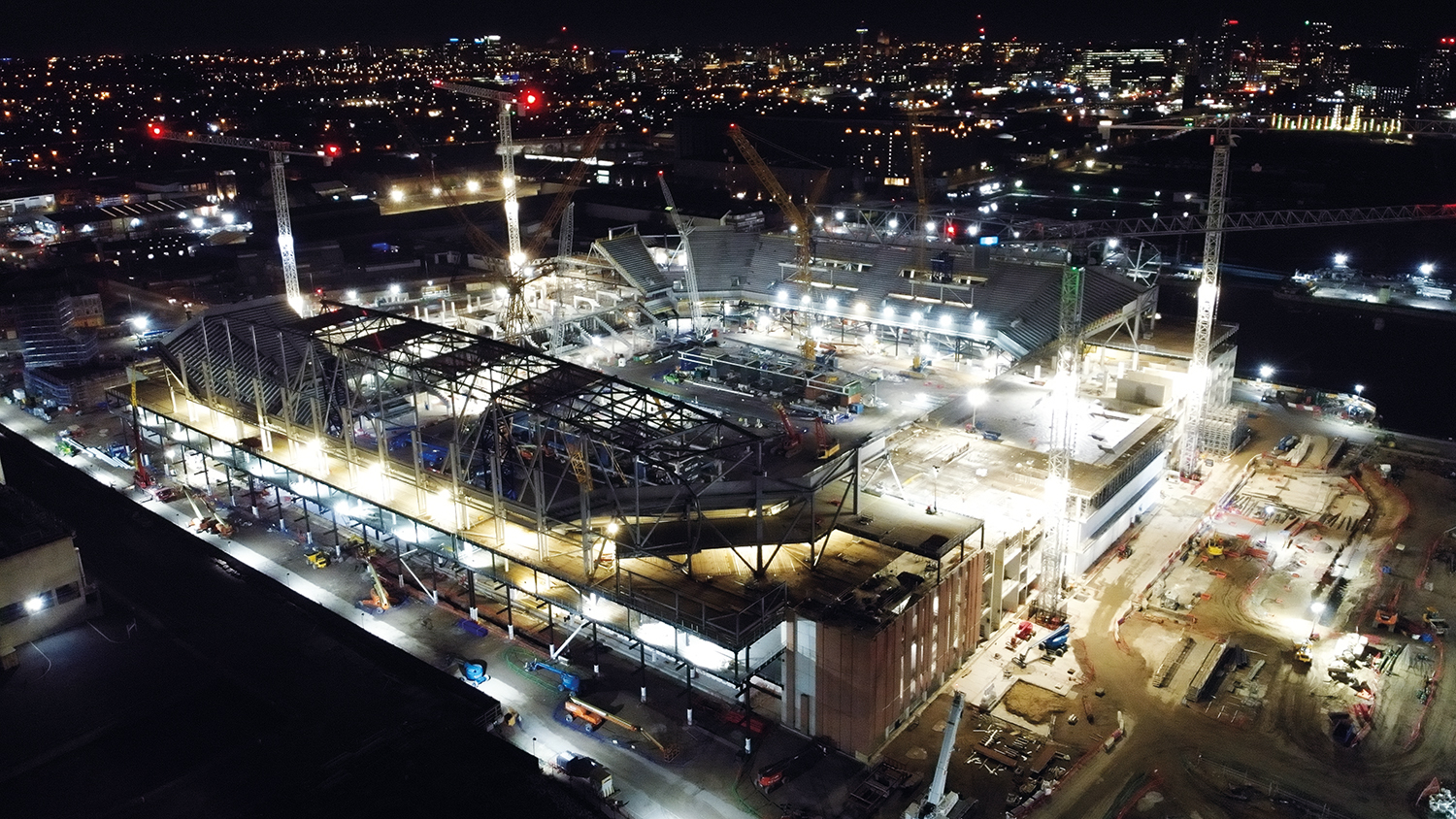
The MEP elements, supplied and installed by CHT, are also largely prefabricated, with vertical and horizontal routes and plant rooms arriving on site as modules. The team also developed a modular system for the plumbing of the 900 toilets.
The project’s ‘Engineered Safety’ approach takes the principles of CDM well and truly to heart, rethinking and redesigning to reduce as many potential safety risks as possible.
The erection of the stadium’s five huge roof trusses, currently underway, has been scrutinised and refined using 4D modelling which includes temporary works and logistics. Each truss comprises three 100-tonne sections which are assembled at ground level in specially designed containers on the floor of the stadium, then lifted into place and supported on temporary stands until the sections are bolted together. The roof modules are pre-clad at ground level, with the first of these lifted into place in November 2022.
Building on sand
The enabling works for the stadium began in July 2021: infilling the Grade-II listed Bramley-Moore Dock. Contractor Royal Boskalis Westminster pumped liquidised sand, dredged from Liverpool Bay, via a floating pipeline to fill the dock. Before that, the floor of the dock had to be raked and any debris removed, most commonly paint pots tossed into the sea as boats were painted.
The operation also turned up 12 unexploded shells from anti-aircraft guns posted round the dock during the Second World War; the team called in an ordnance team from the navy or army when these were found.
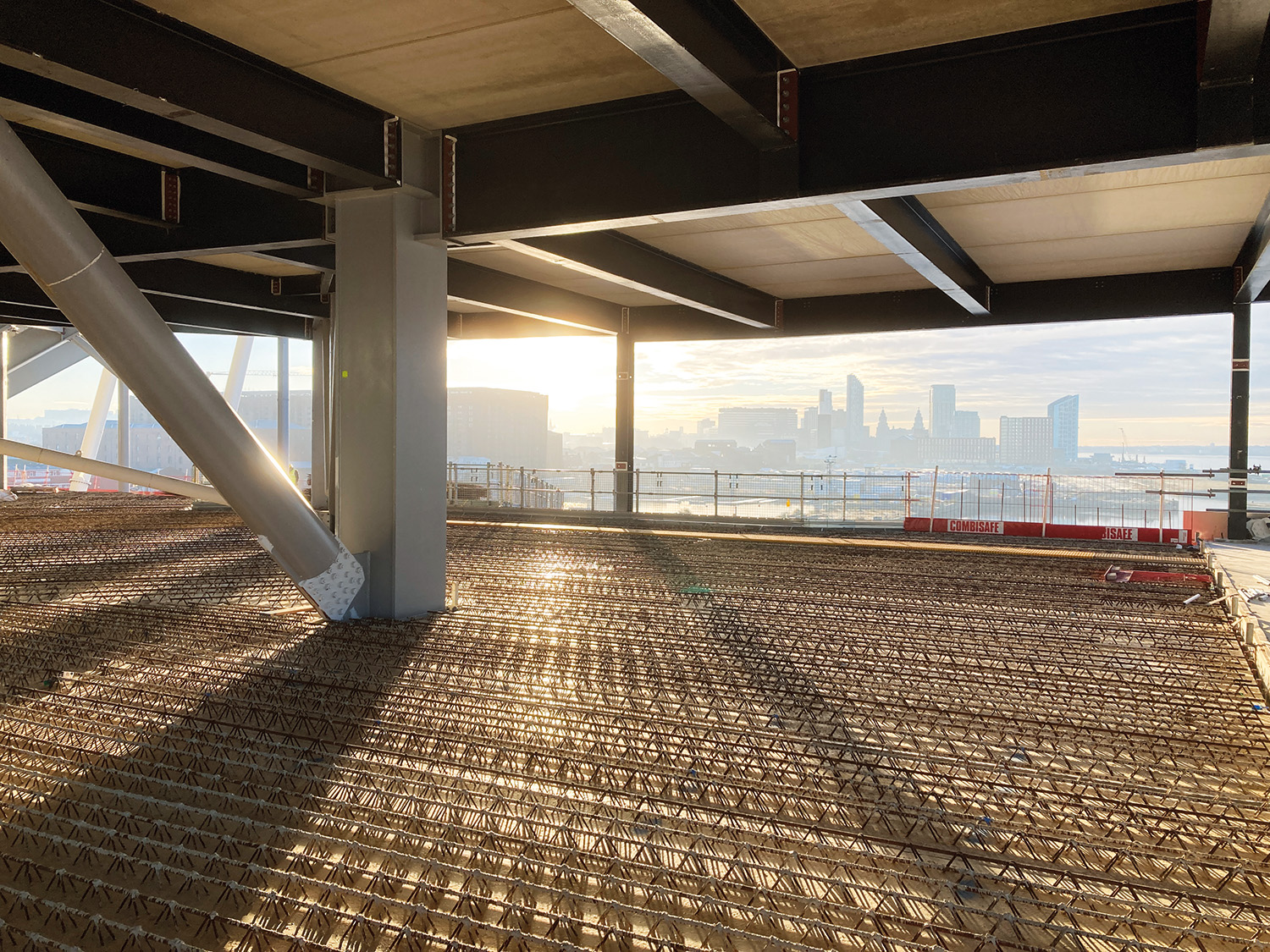
By December 2021 the dock was full and compacted. The pitch will sit on top of this sand, with the settlement closely monitored.“It’s beginning to flatline,” explains Edwards. “In reality, most football clubs relay their pitches every year or two, and we are talking about millimetres here.”
Piling began in October 2021 and ran until June 2022. In May 2022 the first steel column was erected, with the first terrace units and the first concrete raker on the West Stand installed in August. In January 2023 the first roof truss was in place. They should be in place by Easter 2023, with the whole roof complete by August. Come autumn, the site workforce will peak at just over 1,000.
Fixed-price contract
Laing O’Rourke’s contract is fixed price – £555m – and, given material and labour inflation, this could have caused the commercial team a few headaches. Fortunately, the DfMA elements have mitigated this, as materials were bought earlier than if the project was being constructed traditionally. Self-delivery helps too.
“Escalation has been assessed in detail and is being closely managed by the project’s commercial team, rather than being subject to opportunistic market fluctuations,” says Edwards. There’s also short-term uncertainty about Everton’s footballing future, with the prospect of relegation from the Premier League and all the financial repercussions that would have.
But Edwards and his Laing O’Rourke team are focused on the long-term impact of delivering a stunning new venue for Everton and the city of Liverpool.
“We are building this for an organisation that has a commitment – not only to its fans, but to its city. That makes a difference to how people feel around the project,” he says. “There’s more of a community feel than if you were working on a standard commercial development.”
Digital innovation by doing
Augmented reality and 4D BIM are among the tools Laing O’Rourke is trialling at Everton
The only way to trial and advance digital tools is in the thick of it. That’s the view of John Edwards, technical lead on Laing O’Rourke’s Everton project.
His team are certainly finding new ways of doing things digitally at Everton. Notably, 4D BIM: planning exactly how the work will be executed using the 3D BIM model and incorporating temporary works and logistics into the sequencing.
“We can work smarter; we achieve more because we focus our attention on making something more efficient or designing out safety issues,” says Edwards.
Not new, but a digital tool that has helped is BIMcollab, used for commenting on and developing the model, saving time taken to minute and review design meetings.
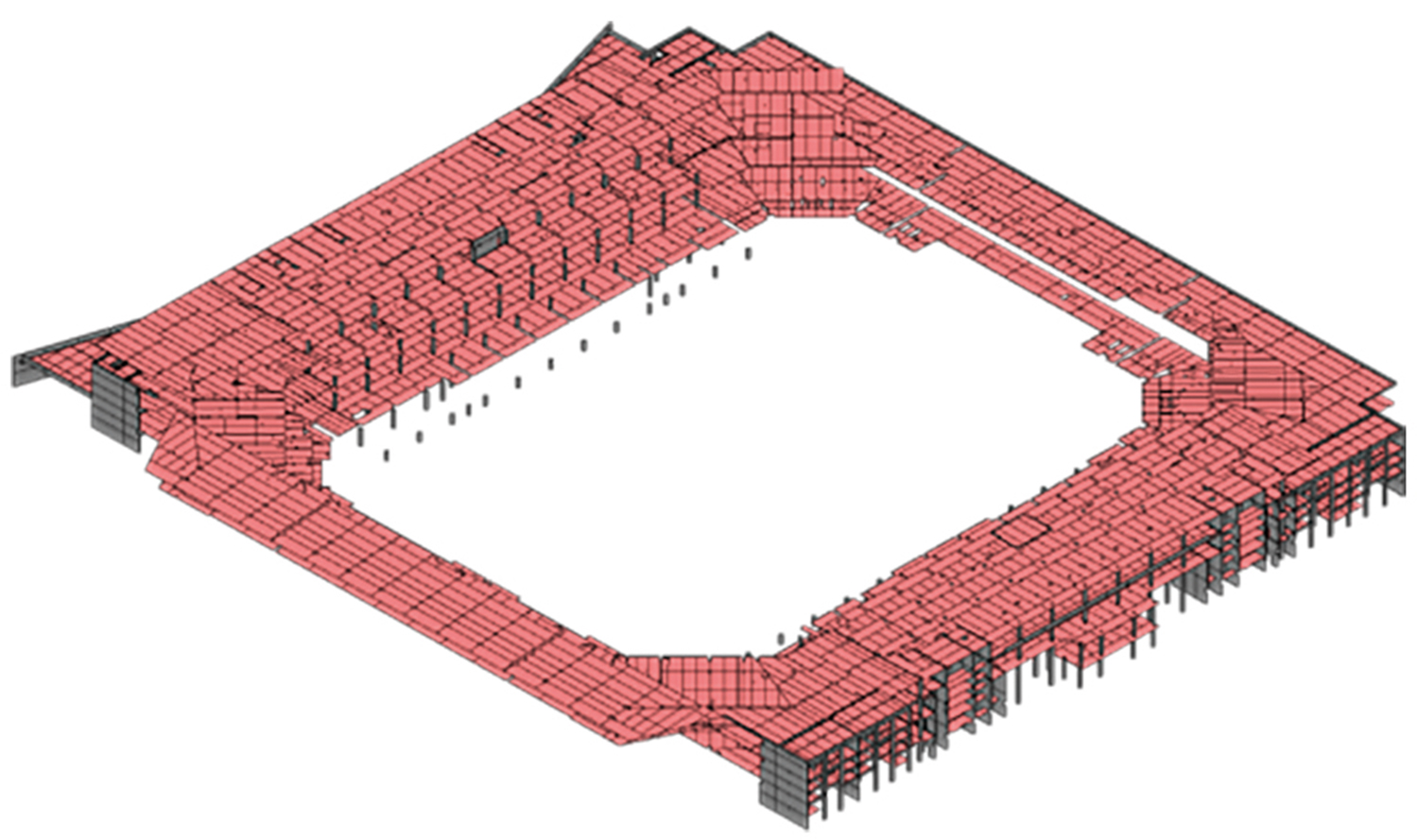
There’s use of augmented reality (AR) too. In the workshop where the brick panels are made, a worker checks the position of darker bricks which form a pattern, to make sure they are in the right place before concrete is poured. Out on site, an engineer uses AR to project MEP modules onto the ceiling to see where they will fit.
Immersive room
The Everton project is also using an immersive ‘3D room’, with three screens for interactive induction and safety training and look-aheads for work coming up.
Created with training provider Immersive Interactive, the technology is evolving as the project progresses. It is a much better way to engage with people, says Edwards, and can encourage contributions from people who might not typically contribute in a traditional meeting.
One of Edwards’ design management team, Reece Singleton, has led development of a digital process for ensuring fire-stopping products are designed and installed properly – following the ‘golden thread’ principles of the Hackitt review and Building Safety Act.
The automated process, developed with software house Solibri, interrogates the design to confirm compatibility between products and design for
over 70 situations.
“It is data-driven and ensures we have modelled the build and the MEP correctly and that we have compliant details,” says Edwards.
Doing all this on-project means dissemination and development is faster,
says Edwards.
Comments
Comments are closed.
Awesome read