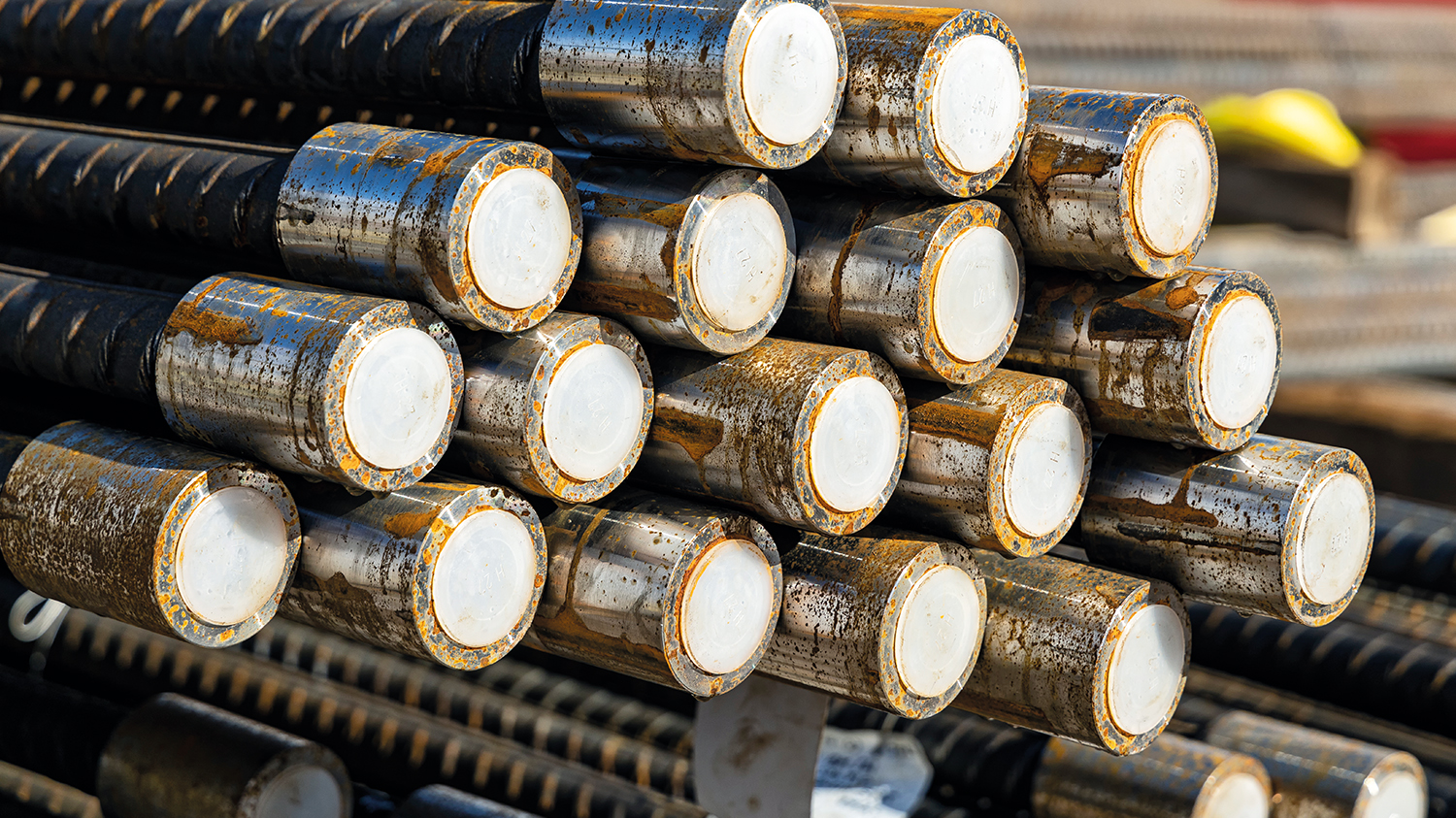
On the Euston HS2 project, the Mace Dragados JV has used cloud technology to track rebar compliance – and deliver higher quality and safety standards. CM reports.
Dame Judith Hackitt’s CIOB lecture before Christmas delivered a sobering message on construction product safety, warning that progress on independent assurance testing
post-Grenfell remains far too slow.
At HS2’s Euston Station project, the Mace Dragados JV has run a trial using a cloud-based system to prove the chain of custody for steel reinforcement bar.
“Ensuring the authenticity and safety of construction materials, particularly reinforcing steel, is now more crucial than ever,” says Andrew Kinsey, sustainability operations director, Mace. “And reinforcing steel is one of the most safety-critical elements in any project.”
As well as build safety, contractors face increasing pressure to account for the environmental impact of their designs and the carbon footprint of materials, Kinsey adds. Historically, obtaining accurate data on embodied greenhouse gas emissions of materials like steel reinforcement bar has posed a challenge.
“On HS2, there are stringent standards for material procurement and supply, which include product conformity, responsible sourcing certification and BREEAM criteria, necessitating a robust chain of custody,” says Kinsey. “Traditional paper-based certificates have historically been used to verify compliance but are time-consuming.”
The UK government’s procurement guidelines, such as Procurement Policy Note
PPN 11/16 and its successor PPN 04/23, further emphasise the need for transparency in the origin of steel used in publicly financed projects, he adds.
A cloud solution
The Mace JV, working with consultant Digital Construction Solutions, decided to partner with CARES Cloud and trial a digital chain of custody system for steel rebar at Euston.
The software was introduced by CARES (UK Certification Authority for Reinforcing Steels) in 2016. It tracks each batch of reinforcing steel from its point of origin at a steel mill, through offsite fabrication processes and onward delivery to the construction site.
Standardised QR codes are used on bundles of rebar provided by each CARES-certified rebar manufacturer. A mobile app available scans rebar which is received and used on the project, providing a digital record of the entire process.
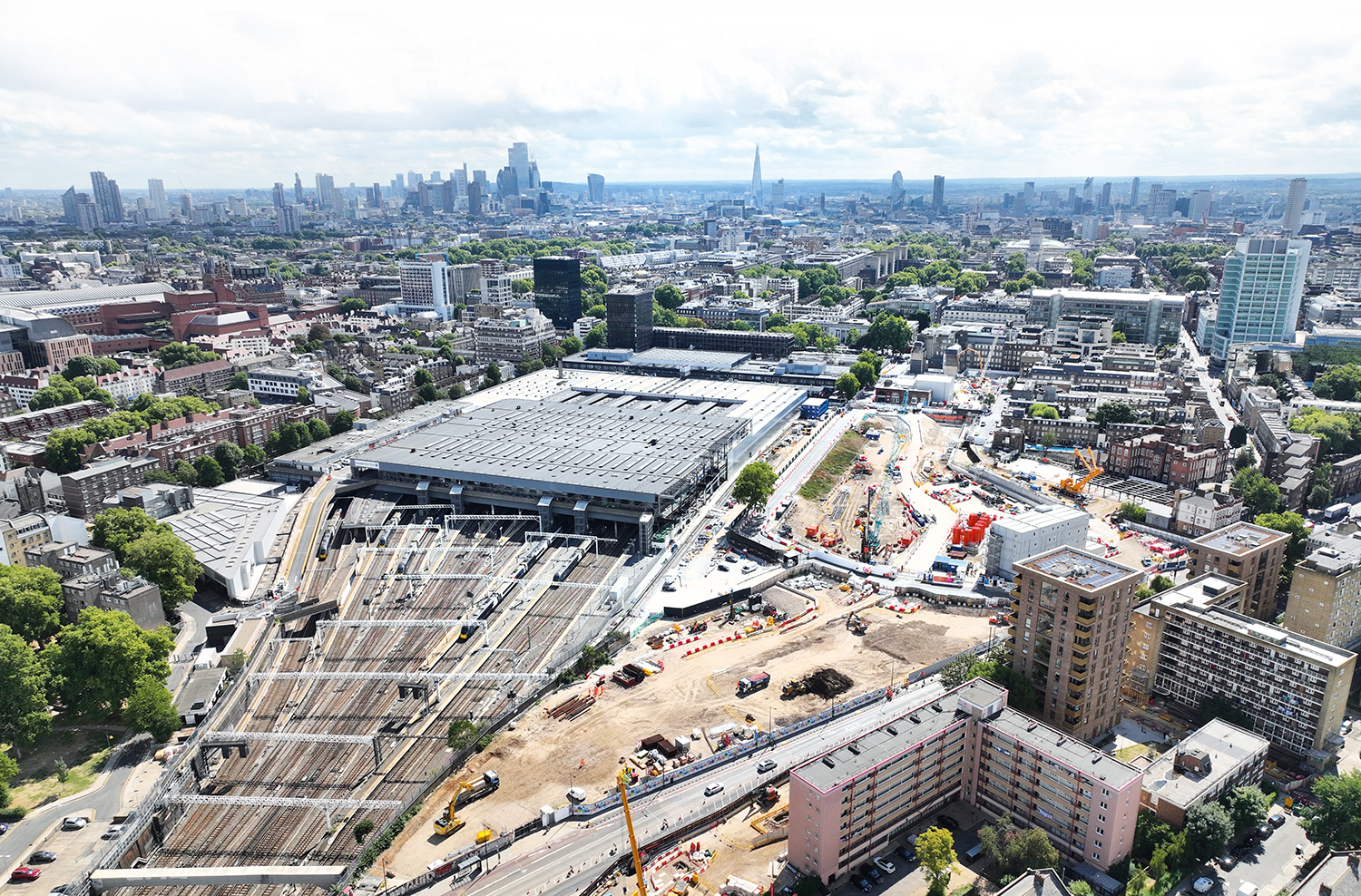
A dashboard provides an overview of the product conformity approvals status of each bundle of rebar, ensuring it is of the grade specified, plus a digital product material passport of the rebar used, together with quality and responsible sourcing certificates. Product information and evidence of assurance can be included in project BIM models.
The system also gives carbon footprint data, sustainability information to achieve credits in BREEAM assessments, and environmental product declarations (EPDs) for the actual material used.
The Euston trial
The Mace JV’s trial of CARES Cloud, supported by HS2’s innovation fund, was undertaken on two of the early works piling packages.
It had several objectives, including: operational cost savings; improving speed of data collection and quality; establishing QR codes as a standard for rebar; data exchange improvement; and accurate carbon data reporting.
Kinsey says the trial achieved all the goals set; 100% of steel reinforcement was delivered with a complete set of assurance records, including all CARES certificates of approval, and complete carbon footprint data for all reinforcement manufacturers and fabricators.
“The project dashboard recorded, analysed and summarised the data along the supply chain, in real time,” he says. “Supply chain transparency increased confidence in product integrity, production safety record and carbon accountability.
“The implementation of digital recording resulted in an 11-day saving in processing time for 712 tonnes of reinforcement.”
Carbon savings data could be accurately quantified, based on the actual manufacturer of the reinforcement, the quantities used, production methods and origin of manufacture, Kinsey continues.
Carbon footprint data
“CARES Cloud enabled the use of actual carbon footprint data during the construction phase, overcoming challenges such as a time lag in receiving data and inconsistent formats,” he explains. “It collated carbon footprint data for all reinforcement manufacturers in the UK and elsewhere and the tonnage from each manufacturer was reported and analysed via the CARES Cloud dashboard.
“The data allowed our procurement team to make informed decisions and give preference to lower emission steel sources, and accurately calculate the actual emissions associated with the reinforcing bar. This meant a (non-cash) saving of £19,000 based on the carbon price used at the time of £50 per tonne.
“The carbon savings and digital data exchange support HS2’s carbon reduction plan and commitments, and this system can contribute towards any company’s carbon emissions reductions, in line with industry pathways such as Co2nstruct Zero and SteelZero.”
The technology also provided HS2 with the toolset to comply with UK government guidelines on procuring steel in public contracts.
“CARES Cloud offers a valuable digital solution for tracking quantities, quality and characteristics of steel rebar used,” concludes Kinsey. “We have learned invaluable lessons about improving efficiency in rebar tracking and quality assurance. It could become a key part of a materials passport scheme on future projects.”