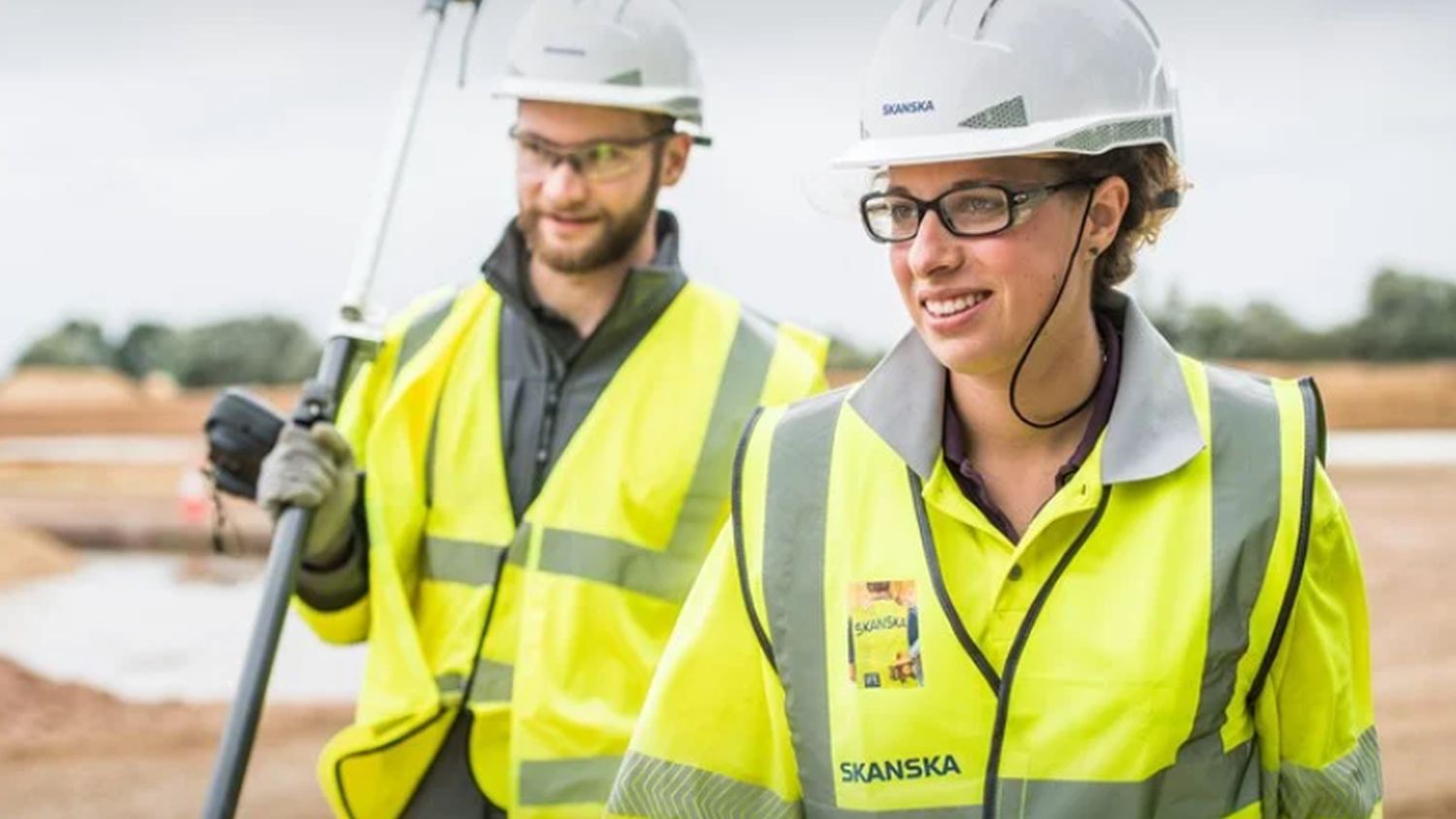
Digital construction has a “critical” role to play in achieving net zero in the built environment, according to Skanska UK’s head of environment technical.
Skanska’s David Mason was speaking at yesterday’s Digital Construction Summit 2022 session examining digital construction’s role in achieving net zero.
Skanska has set itself the target of reaching net zero by 2045, including Scope 3 emissions from its supply chain.
Mason said that three key challenges for Skanska are the carbon in concrete and cement products, steel products, and its reliance on internal combustion engines.
To achieve net zero, Skanska needs to cut in the region of 12,000t of CO2 emissions a year. The company has used digital tools to calculate that for every £1m of revenue, it is generating 180t of carbon. It needs to reduce that by 11t a year to meet its target.
It is focusing on six key areas to reduce its carbon emissions:
- Carbon capability for key roles
- Carbon data and measurement
- Digital carbon management tools
- Net zero materials
- Net zero fleet and plant
- Supply chain collaboration
Mason said: “There’s some really promising developments going on which I think will help the industry deliver this net-zero challenge. I remain fully optimistic that it can be done. Digital construction has a critical role in achieving net zero across the built environment. It will take a lot longer to do it without much better digital.”
Eco Driver initiative
Meanwhile, Steven Sutch, director of plant hire firm L Lynch, described how his company has used digital tools and machine telematics to measure how long drivers leave machines idling. By cutting idling time, L Lynch has also managed to reduce CO2 emissions.
It launched a pilot of its Eco Driver exercise with Skanska, Costain and Strabag on HS2 in London.
With a focus on heavy machinery such as dumpers and rollers, the Eco Driver programme focused on educating and upskilling drivers with a view to reducing idling and therefore fuel consumption, as well as improving worker wellbeing by cutting exhaust fumes on site.
At the start of the programme, machine idling was at 41% for the 16 machines. Over 12 weeks, that reduced to 24%. L Lynch measured a 46% drop in CO2 consumption and saved its clients £10,000 in fuel.
Sutch said: “The trial has allowed us and our customers to identify operator behaviour and driving techniques through better collaboration with sites, and to report on CO2 emissions. The blend of telematics data and training has empowered behavioural change. This has resulted in tangible benefits for both us and our clients.
“If our machines don’t work as many hours, we don’t have to service them as regularly. It has provided cleaner air and a more sustainable construction site. The Eco Driver programme has enabled us to automate how we provide carbon reports. We have now collaborated with NOCN and CPA and this has been accredited as an approved training course for operators of machinery.”